
Need real custom over Molding parts?
GREFEE is the most professional company making over-mould parts, our merits:
- Advanced injection molding machines including Vertical three-position injection molding machine.
- Over-molded parts are high quality and cost-economical.
- Help customers improve designing of over-mould parts(create dust proof or transparent plastic window).
- Cost benefit: short run and massive production by automated machines or by robots are valid.
- Various materials are valid in over-mould injection molding, let you get right property parts.
- Rich experience in over-mould injection molding.
Looking for plastic, rubber, or TPE over-molding? We provide free product assessment and DFM analysis, contact us now!
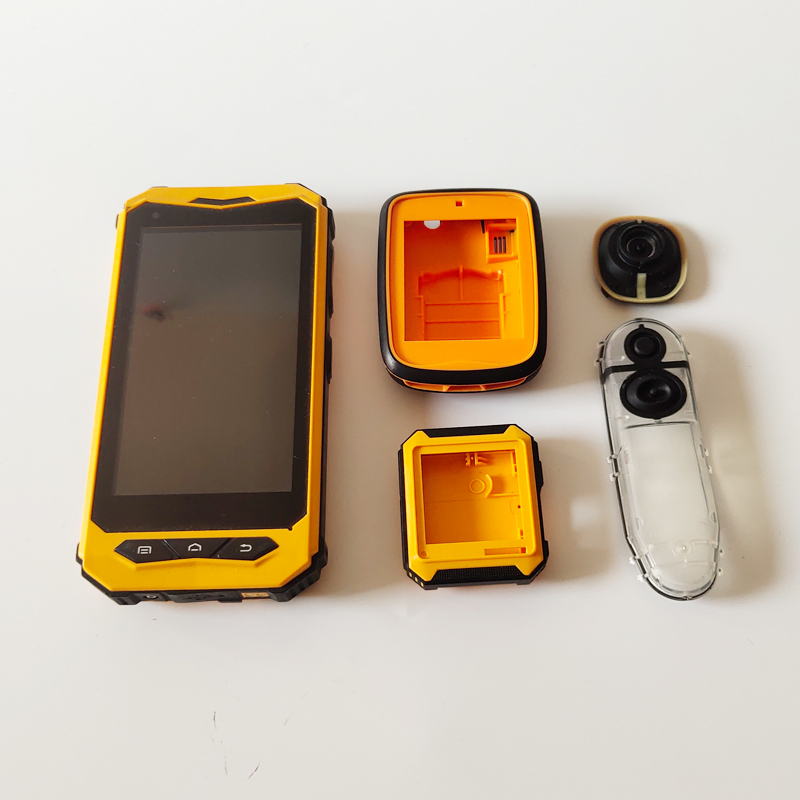
GREFEE provide high quality injection molding for prototypes and production components as required.
In short, over-mold injection molding let you make a unit part from various plastics.
Adopting over-mold injection molding, designers could add soft-touch appearance on parts to enhance grasping feeling and beauty, or made from 2 or more materials to achieve function.
Over Molding parts are more attractive to customers. There’re plastic over-molding, rubber over-molding, TPE over-molding…etc. Below let’s know more about the advantages of over-molding:
- Achieve function of over Molding parts
Take washing machine cover for an example, it consists of 2 parts, the first part is hard plastic(usually are PC/ABS), the second part is transparent window made from PC, these 2 parts become a unitary component by plastic over-molding, then we can get a plastic cover, which is not only has clear window but also has high intensity.
- Improve product performance
Rubber(usually are TPE/TPU) over-molding used on grip can reduce shock and vibration, help electrical insulating, lower sound, improve chemical resistance and anti-ultraviolet property, and greatly improve the product performance of TPE/TPU after over molding.
- Add beauty
The part can made from 2 or more colors and materials by over molding, which help products stand out from others and attract customers to purchase.
- Cost-benefit production way
Over molding injection molding technology is getting more and more mature in industry, suiting for sm18all-batch production. It costs less on mould than that of 2K(2-SHOT) MOLD.
Over molding plastic materials
Choosing a right over molding material plays a crucial role in product application and performance. Need pay attention that there should be molding temperature gap(melting point) between hard and soft plastics, and it should be at least 30℃ or above. The molding temperature of base material should be higher than that of cover material. We provide follow materials for over molding:
- The firstly injected material called base or base material, usually they’re hard plastics, can be ABS, PP, PA6/PA66-GF, PC, PC+ABS….etc.
- The secondly injected material called cover material, usually they’re elastic resin, can be artificial rubber, TPU, TPR, TPE, soft PVC…etc.
1.In the case of determining the base material, here’re preferred sequences of cover materials(front is preferred)
Base materials(body/skeleton) | Cover materials | Notes |
PA6-GF | General all elastic resins, but TPE is the first priority | TPE is wear-resisting |
PA66-GF | General all elastic resins, but TPE is the first priority | TPE is wear-resisting |
ABS | General all elastic resins, but TPE is the first priority | TPE is wear-resisting |
PC+ABS/PC | General all elastic resins, but TPE is the first priority | TPE is wear-resisting |
PP | TPR/TPE/PVC | |
Die-casted metal parts | TPE/PVC /TPU/PPS/PA6-GF | Need consider design/function/working condition |
PA6-GF/ PA66-GF/PC | ABS(suggest not used in large-acreage part) | 1.Small-acreage logo area(100mm*20mm) is feasible 2.large-acreage over molding area should consider comprehensively including structure and curvature(fall) |
2.In the case of determining the cover material, here’re preferred sequences of base materials(front is preferred)
Cover materials | Base materials(body/skeleton) | Notes |
TPE | General all engineering plastics/ die-casted metal parts | |
TPU | General all engineering plastics/ die-casted metal parts | |
PVC | General all engineering plastics/ die-casted metal parts | |
TPR | General all engineering plastics/ die-casted metal parts | |
PPS | die-casted metal parts | |
PA6/PA66-GF | die-casted metal parts | |
ABS(suggest not used in large-acreage part) | PA6-GF/ PA66-GF/PC | 1: Small-acreage logo area(100mm20mm) is feasible 2:large-acreage over molding area should consider comprehensively including structure and curvature(fall) |
Before choose a specific material, we need consider the compatibility of materials. If the over molding materials are incompatible, the covered plastic is easy to peel off, or even not stick to the second material, which directly causes the functional problems of components. At GREFEE, we built solid partner relationship with resin suppliers, so we’re able to get resins for special purposes at competitive prices to suit your needs for over molding. We’re glad to provide best solutions for your projects, regardless of rubber over molding, plastic over molding or TPE over molding on metal parts. Contact us and get more information now!
Design tips for over-molding products
- Need add material pressing groove on skeleton, width is 1.2mm(standardized).Suggest make groove 1.8mm on complicated surface. Groove as below picture shows:
- This around material pressing groove plays a sealing role in rubber injection molding, therefore the whole around groove on skeleton needs fitting closely with the over mold, and on the reverse side, should avoid ribs or holes as material is easy to spill around the groove face to ribs and holes.
- Soft material surface should be a bit higher than that of hard material, and add appropriate chamfer or fillet to avoid sharp edges, in this way, users will not feel the sharp edges when hold it.
- Base: when do over molding on a slant surface, this slant surface cannot beyond 45°.The cover surface width should be at least 1.2mm, and parallel or perpendicular to the parting surface as much as possible. If on a slant surface, the inclination should be small as much as possible, to low down the difficulty of fitting moulds. The most inclination is better not over 45°.
Should make dovetail buckles on over molding parting surface, making cover material buckle on skeleton and not easy to peel off. Distance between dovetail buckles usually is around 20mm, while undercut size depends on over molding wall thickness. GREFEE’s products refer to design standard guidance(standardization). At the two ends of over molding parting surface, should make left-hand screws, buckle these two ends. Details refer to design standard guidance.
Molten soft material has excellent liquidity, it’s bleeding easily with light press, therefore the thickness of over molding should keep the same as much as possible, and choose gate point in the middle of the part, which helps material injected evenly.
In the corners or spindly areas of over molding areas, need make material pulling holes with steps. Around over molding area, make material pulling grooves or spacing material pulling grooves, with depth 1.0mm and width 1.0mm.Make rivet holes as much as possible(20-30mm space),and close to edges or corners. The edge distance between rivet holes and rib plates on skeleton should be at least 1mm, in order to avoid cover material spilling over the gap of rib plates causing material leaking or flash.
Design Tips for mould in Over molding
Click here to get more details of design tips for over molding
In over molding, only one section of the material is required injection, therefore no need to cover the whole skeleton inside the mould, as picture shows, only need cover that section of the part, but must make sure that no waggle or crushed after put the part inside the over mould when mold clamp, and make sure it is balanced for mould opening and clamping.
In over molding, to avoid the gate point on the part surface, usually the cavity and core are reverse to that of the mould for skeleton, that’s to say, cavity for skeleton faces to the core of over mold, while core for skeleton faces to the cavity of over mold.
In over molding production, part is placed into the mould cavity by operator or mechanical arm(really high demand on mechanical arm, so commonly place part mainly by operator), make part parting surface and mould parting surface fit closely, then gather the cavity and core for injection.
Common problems in over molding
- Difference between over molding and 2K injection molding Over mold(Secondary Tooling): two kinds of plastic materials are not always injected in the same injection molding machine, and molded twice. A part demolded from one mould, then is placed into another mould for secondary injection molding. So, usually this kind of injection molding technology is completed by 2 sets of moulds, just need ordinary injection molding machines.
- Double Injection, sometimes known as 2 material 2 shot molding or 2K moldin。 Bicolor injection mould(Double-shot mould): sometimes known as 2 materials 2 shots molding or 2K injection molding. In other words, 2 kinds of plastics are injected in same injection molding machine, injected in twice but demould once for a product. Bicolor injection mould is usually completed by a set of mould, and need special bicolor injection molding machines. Quality of products made from bicolor injection molding are generally higher than that of over molding, but mould and production costs are much higher than that of over molding.
- There’re many reasons for flash happening in over molded parts’ soft covering material area, but the main reason is that the mould core doesn’t press the hard plastic causing the soft material flow out from cracks in injection molding. Suggest do mould fitting again and make the sealing surface on soft material mould 0.03-0.05mm higher.
- Another common reason is that the supporting strength of hard material is not enough, then the hard material is impacted into deformed in injecting soft material, in this case, need protect the hard material from deformation in injecting soft material by thickening the hard material or adding steel support at the back of hard material.
- Material issue: molecules of soft material and hard material have poor adhesion property, cannot merge enough.
- Product issue: avoid sharp corners as much as possible, to assure the contact area as large as possible between soft material and hard material, improve adhesive result.
- Mould issue: unreasonable venting system in mould, air exists in mould cavities, too small demolding draft, or part damaged in demolding.
- Injection issue: improper mould temperature in injection molding