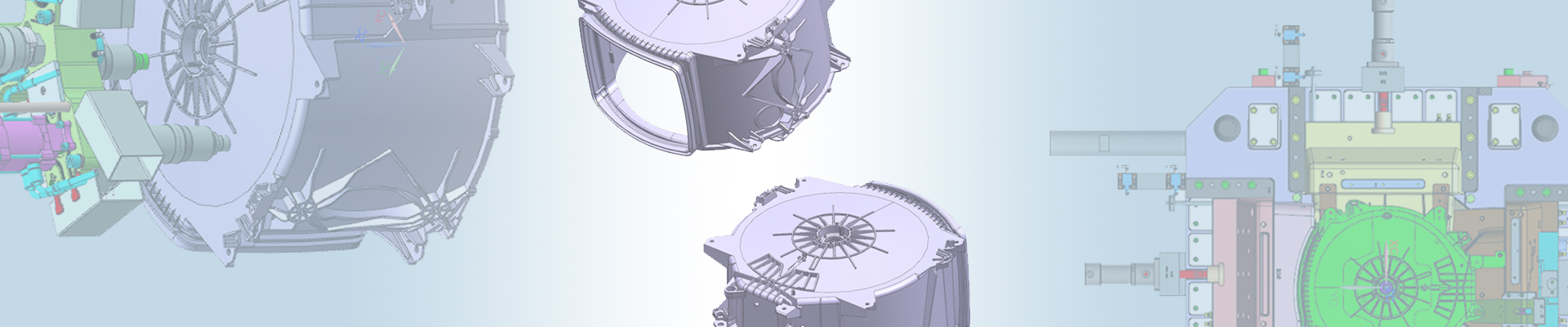
Case of Whirlpool Washing Machine Tubs
GREFEE has 20 years mold production experience, we provide practicable mold plans for customers.
“Whirlpool” belongs to Whirlpool Corporation. It is one of the fortune 500 enterprises and was founded in 1911 from Benton Harbor, Michigan’s Lou Upton. Whirlpool is one of the largest household appliances manufacturers in the world. They have been the leader of the global market in their sector this past decade.
The business of Whirlpool spans from over 170 companies globally with 47 manufacturing bases, 26 R&D centers, and 4 designing centers. For a hundred years, Whirlpool has always devoted itself to providing the highest quality household appliances for consumers worldwide. It has 9 product segments: washing machines/clothing dryers, microwaves, refrigerators, air conditioners, hot water heaters, kitchen ventilators, dishwashers, heaters, and kitchen waste processors.
GREFEE has been cooperating with Whirlpool since 2012. The first project we worked on together was a washing machine tub die. It requested challenging shapes and complex geometry. Besides, it needs extreme accuracy. Whirlpool has vigorous requirements on injection molding cycle time and automatic mold production. They have also considered other manufacturers, including our competitors. Finally, whirlpool chose GREFEE due to our expert engineering design solutions. They fully affirmed GREFEE after visiting our plant.
Introduction to summary
Product Name: Whirlpool washing machine tub
Product material: PP+T20
Product features: functional part and needs to be rotated. Therefore, it needs extremely high concentricity during rotatation, and has strict requirement on part size too. However, the part material weight varies greatly in each direction, which will cause severe deformation if not addressed.
Customer requirements:
1.Cycle time 75s (including time for molding, mold opening, product removal and mold closing, 15s faster than their previous model which had a 90s cycle time)
2.The product needs to be interchangeable, it needs to be convenient and fast for slide replacement.
Considering the requirements of the part and our client, we need to use the most reliable and stable injection molding method to get high quality products in the fastest approachable cycle time.
The difficulty of the mold is that the cycle time is short and the product has high precision requirements.
Average wall thickness is about 3mm with complex structures and many ribs, so the pros and cons of classification & cooling determines the quality of the final products.
Multiple reverse buckles inside product, lifter structure in case of product sticking to the lifter, eject system designed above the lifter.
Complex molding structure, multi-times core pulling structure needed.
Injection Solution
We applied the sequential valve gates solution: which can accelerate the flow of the material, highly shorten the cycle time, eliminate stress concentrations & welding line, reduce part distortion, improve the part quality, and ensure the final part better meets our client’s requirements.
By controlling the gate opening time, which can ensure more balanced filling, and avoid welding lines.
Enlarges the gate to speed up the flow in the cavity and shorten cycle time, it’s also good for holding pressure to reduce the molding part’s shrinkage and deformation.
Effectively reduces the internal stress of the product and improves the stability of the part.
Hot nozzle injection position is on an irregular surface. Flatten the core and cavity when designing in favor of molding.
Filling Flow
We determined a mould flow to optimize the gating.
There is no doubt about the importance of the injection system for injection molding dies. Through analysis, we carried out multiple solutions to seek for the optimal injection solution to optimize the gating.
Option 1- three valve gates open at the same time
Option 2- three sequential Valve gates
Option 3- change the gate location
Cooling
In order to get the best quality product in the shortest time, we need to maintain the temperature of the whole mold, and make sure the temperature of each position of the mold should be as consistent as possible. Then we run a flow analysis to optimize the cooling, thus the final products we get are of better quality and with the shortest cycle time possible.
3D images of mold
Cavity
Core
Cavity
Core
Front of slide
Back of slide
Front of lifter
Back of lifter
Injection molding technology:
1.Conditions for baking: 80ºC,2-4hrs。mold temp 30-50ºC, low values recommended for shortening molding period.
2.Proper injection speed and maintain pressure within a good range to reduce shrinkage cavities and gas trapping. 1800 tons clamping tonnage for mold testing. 50s cooling time. Too much pressure will lead to product sticking and breaking on the parting surface.
3. Fast injection speed lead to gas trapping.
4.Water slab is not allowed. Injection molding by at least 80% of the sample, otherwise sticking to the cavity.
5.The slide of the core facing the ground should be clamped and locked before installation into injection molding machine. Open the mold and remove after machine operation in case the pins which are inserted in the slide break.
6.Specific cooling position should be paid attention to for water transport connection.
The mould
Dos and Don’ts of mold process
Mold Fitting:
1. Shut-off surfaces without a draft angle at the slide should not be too tight, which might cause burning in mold clamping.
2. Slide pin insertion, mold touch should not be too tight. Leave a gap of 0.02 in case of deformation when mold clamping.
3. Three lifters with centered round insert: insert one lifter and then fix it by the meter before inserting the other two to ensure the assemble gap to avoid improper sealing.
4. The inclined surface by lifter and B board: assemble the lifter and intermediate insert before fitting the molds.
5. Small insert in the middle of the cavity cannot be too tight to ensure it can bounce up by slingshot on the bottom.
6. Large lifter and slide assembling smoothly, too loose will lead to material peel .
7. Sufficient vents for mold inserts of the cavity in case of shrinkage.
Die polishing:
1.Assemble the three lifters inside the B board and polish the top cavity site at 0.05 thickness of the base pad, avoiding material peeling and controlling wire clamping.
2. Four slides are assembled into the cavity and polish the bonding side together to avoid sunk angle when polishing mold and it also controls wire clamping
3. The cavity surface of the column inside the lifter should be slightly polished to ensure accuracy.
4. The large lifter should be put on the slide at the position of 0.05 thickness of the base pad, polishing cavity surface, avoid material peeling.
Conclusion
GREFEE has extensive experience in the household appliances industry. The washing machine tub is the one that requires extremely high cutting requirements among all of them. In 40 days, GREFEE can finish the mold with a 95% pass rate of T1 mold testing. All the issues are being solved completely in T2 mode testing and being delivered to customers safe and sound. The whole process takes no more than 50 days from defining molds to the shipment.
We completed the Whirlpool washing machine drum project successfully in such a short period of time. This is thanks to GREFEE’s professional technical team and strong production capabilities. We have been trusted by customers in the field of high-end mold and injection molding.
Not only did we obtain big achievements in the field of household appliances, but we also have brilliant performance in many other industries, like automotive, health care, telecommunication, and electronics.
Contact GREFEE for professional solutions for your project supported by our technical team. Choose GREFEE, choose competitive and high quality, guaranteed.