Things you should pay attention to in the plastic electroplating.

Posted on : June 27 , 2022 By GREFEE
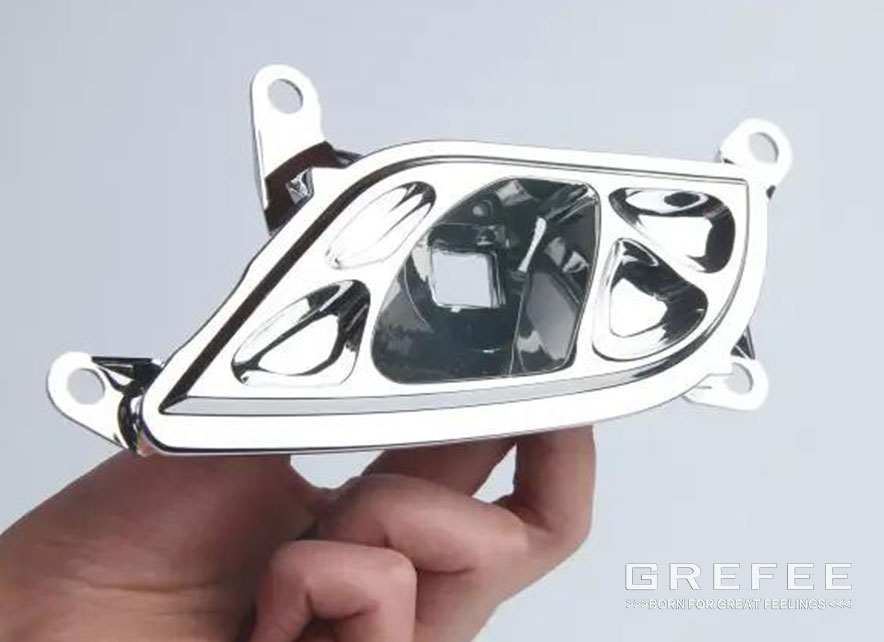
Can plastic be electroplated?
The answer is Yes!
Compared to the metal parts, the electroplating plastic parts not only can achieve a great metal texture but also reduces the weight of products. With improving appearance of plastic and meeting the need of decoration, it also enhances the properties in the electric, thermal, and corrosion resistance. However, the material selection for electroplating should be based on server factors, like the processing properties of material, mechanical properties, material cost, electroplating cost, the dimension accuracy, the difficult level of processing, and other factors. Due to its advantage in the structure, it not only has great comprehensive property but also is easy to be formed. Moreover, it is easy for the material to obtain a high coating adherence, like the chrome electroplating plastic and electroplating on abs plastic, so it is quite popular in the applications of electroplating.
Without affecting the appearance and use, the design of the plastic parts should meet those requirements.
(1) The metal glossy will deteriorate the situation of the shrinkage thus should avoid uneven wall thickness to further reduce the occurrence of the shrinkage. Even wall thickness is required. Too thin wall thickness (less than 1.5mm) will lead to poor rigidity. The part might deform in the electroplating process and cause poor plating coating binding force . The coating may fall off due to defamation in use.
(2) Avoid blind holes, otherwise it is hard to clean the treatment solution left in the blind holes, leading to pollution in the next step and affecting the quality of the electroplating quality.
(3) The sharp edges might become thicker in the electroplating processing, and they will cause the point discharge, leading to bumps on the corner coating. Therefore, it is optimal to transit with the fillet, of which the diameter should at least higher than 0.3mm. It is difficult to electroplate flat plastic parts and the coating in the central part of electroplating parts is thin and gradually getting thicker towards the edges. The whole coating is uneven, so we should change the plane shape to a slightly circular arc surface or make a matte surface with orange peel. The larger the plating area, the bigger difference in the gloss of the center of and the edge. A slight paraboloid can improve the uniformity of the gloss of the plated surface.
(4) It is optimal to reduce the grooves and emboss positions on the plastic parts because the plastic is easy to be sighted in the deep concave, whereas the protruding part is easy to be burnt. The depth of the groove should not exceed 1/3 of the groove width, and the bottom should be circular arc. The hole width shall be equal to the beam width and less than 1/2 of the thickness if with a grating.
(5) There should be enough positions for the hanging of electroplating parts, and the contact surface with the hanger shall be 2 ~ 3 times larger than the metal parts.
(6) The design of the plating parts should be based on allowing the mold to release smoothly when sinking, otherwise demoulding forcibly will lead to the surface of the plated part strained or twisted, or the generation of the internal stress of the plastic part, and the adhesion of the coating will be affected.
(7) The knurling direction should be consistent with the demoulding direction and in a straight line when the knurling is needed. The distance between knurling stripes and stripes ought to be as large as possible.
(8) No metal inserts for plastic parts as much as possible, otherwise the inserts may be corroded in the pre-plating treatment.
(9) Certain surface roughness on the surface of plastic parts.
Mold design
To obtain the flawless plastic electroplating parts, it should be without no evident directional structure and internal stress. The mold design and manufacturing should meet the following requirements.
(1) The mold material should not be beryllium bronze alloy, but should be the high-quality vacuum cast steel. Polishing the surface of the mold cavity along the direction of the mold release till obtaining the bright mirror effect with an unevenness of less than 0.2mm, and it is optimal that the surface be plated with hard chromium.
(2) The surface of the plastic part accurately reflects the surface of the mold cavity , so a smooth mold cavity of the electroplated plastic part is easy to be obtained, and the surface roughness of the mold cavity should be 1 ~ 2 levels higher than that of the workpiece surface.
(3) Parting surface, welding wire and core inlay wire shall not be designed on electroplating surface.
(4) The best place for the gate should be at the thickest part of the workpiece. To prevent the melt from cooling too fast in cavity filling, the gate should be as large as possible (about 10% larger than the ordinary injection mold). It is optimal to use the gate and runner with circular section, and the length of the runner should be shorter.
(5) Vent holes should be reserved to avoid vent holes, bubbles and other defects on the surface of the workpiece.
(6) The ejection mechanism should be selected to ensure the smooth demoulding of parts
Main points in the plastic electroplating
(1). Since the plated part is easy to float, and the place in contact with the hanger is easy to be burnt, as well as low specific gravity, it is easy to float in the solution. The outer appearance of the lampshade looks like a small disc pf which the inner surface is recessed with two small holes on the edge. At first, one copper wire is used to clamp the two small holes for electroplating. Due to the release of gas in electroplating, the lampshade may be separated from the copper wire. Besides, the copper wire is of light weight, so it is not enough to immerse the lampshade in the solution. After that, a heavy object was attached to the copper wire to deal with the issue of floating. Due to poor conductivity, the contact point between the copper wire and the lampshade is burnt and the plastic is exposed. To fix the problem of workpiece floating and conducting electricity, we have designed a special fixture. The certain weight clamp will not float after being installed on the lampshade, and then two wide conductive sheets are clamped on the hole of the lampshade to make the current uniform everywhere, so the contact points will not be burnt.
(2). Bubbles are often found in electroless copper plating on the lampshade. After the process, the bubbles become larger and can be lifted up. The process flow of plastic plating is as follows: degreasing → water washing → roughening → water washing → sensitization → tap water washing → deionized water washing → activation → water washing → electroless copper plating → water washing → electroplating → water washing → drying. From the above, we can learn that any problem in any step before electroless copper plating could lead to blistering. There are many causes for poor adhesion, and the process of degreasing and roughening are often full of problems. Insufficient degreasing may lead to peeling. The lampshade utilizes the chemical degreasing (organic solvent is not suitable for plastic parts). During the operation, raising the temperature to 65 ~ 70 ℃, and the workpiece is shaken continuously until no water drops founded after washing.Another essential part in ABS plastic electroplating is the coarsening. The adhesion decreases due to poor coarsening. Overly coarsening will enlarge and deform the hole, and further reduce the adhesion. As the divalent tin in the sensitizer is extremely unstable, the sensitizer is easy to be invalid. The activation will fail without justification. Insufficient activation will lead to incomplete deposition of chemical coating. However, over activation will reduce the active metal on the surface, and form a discontinuous film that will reduce the adhesion. Attention ought to be paid to the details. ABS particles absorbs water. According to the practice guidelines, the moisture content before injection is less than 0.1%. They must be dried in an 80 ℃ hot air drying oven for 2 ~ 4h, and the surrounding environment must also be dry.
Try GREFEE now,for free
We keep your uploaded files confidential and secure.