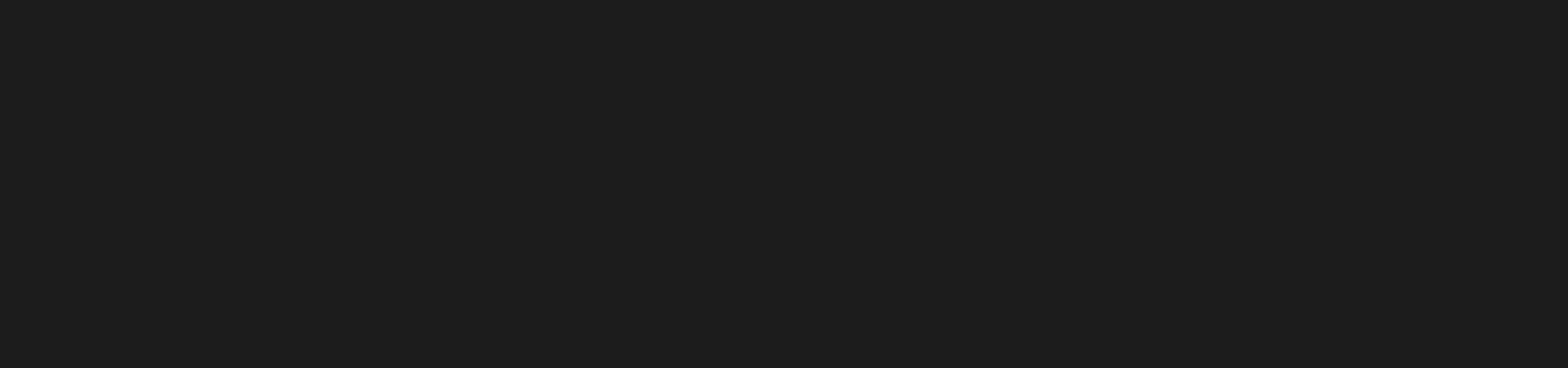
Aluminum die casting
I will quote the best price for your aluminum alloy die casting project now
- Providing free design analysis and product quote
- High quality material supplier or material provided by customer
- Consulting our die casting expertise team
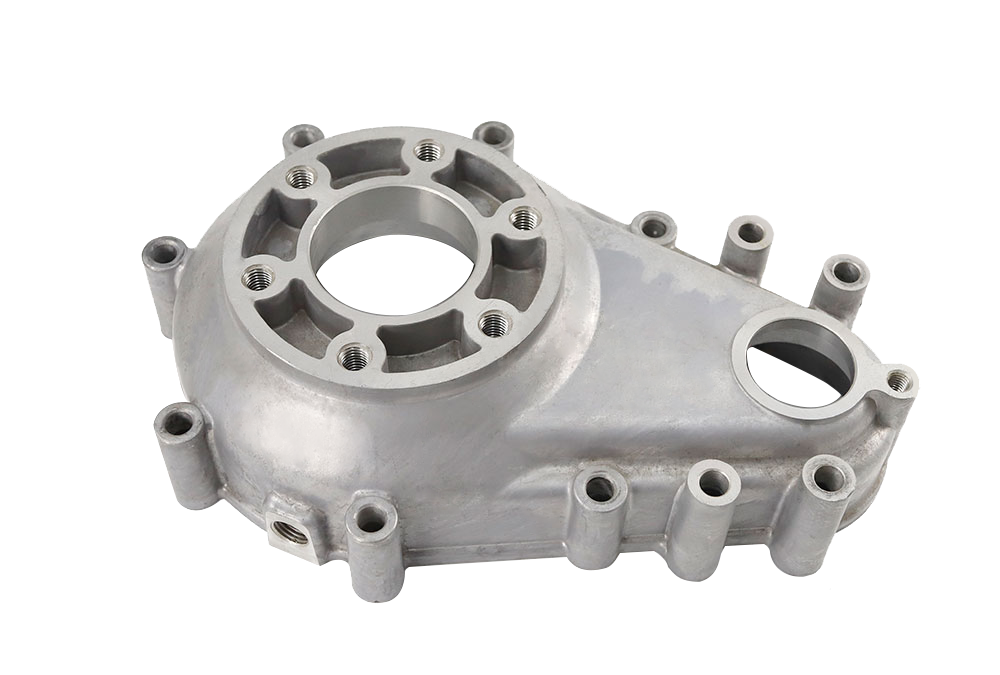
Advantages of aluminum die casting
GREFEE provides high pressure die cast aluminum, aluminum die casting means that pour the melted aluminum into die casting machine, then the melted aluminum is pressed into cavities by die casting machine and get the required part finally.In die casting, inject melted metal under high pressure and speed, to get precision structures and high intensity products. It suits for intricately shaped components. Die casting is high productivity, so it’s widely used in manufacturing industries including automobile, computer, communication filter, medical devices…etc. Die casted products are commonly seen in central control dashboard, electrical machinery box, steering system, computer shell, two-cavity filter…etc.
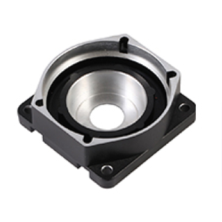
Motor Housing
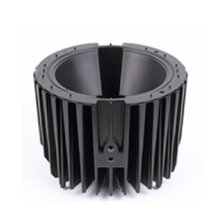
LED Housing
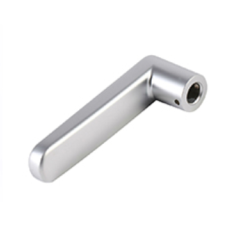
Handle
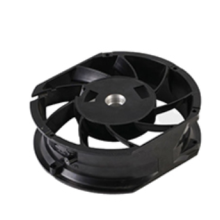
Exhaust Fan
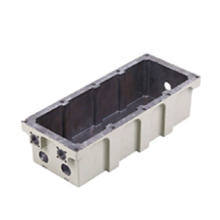
Enclosure
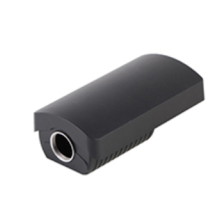
Camera Housing
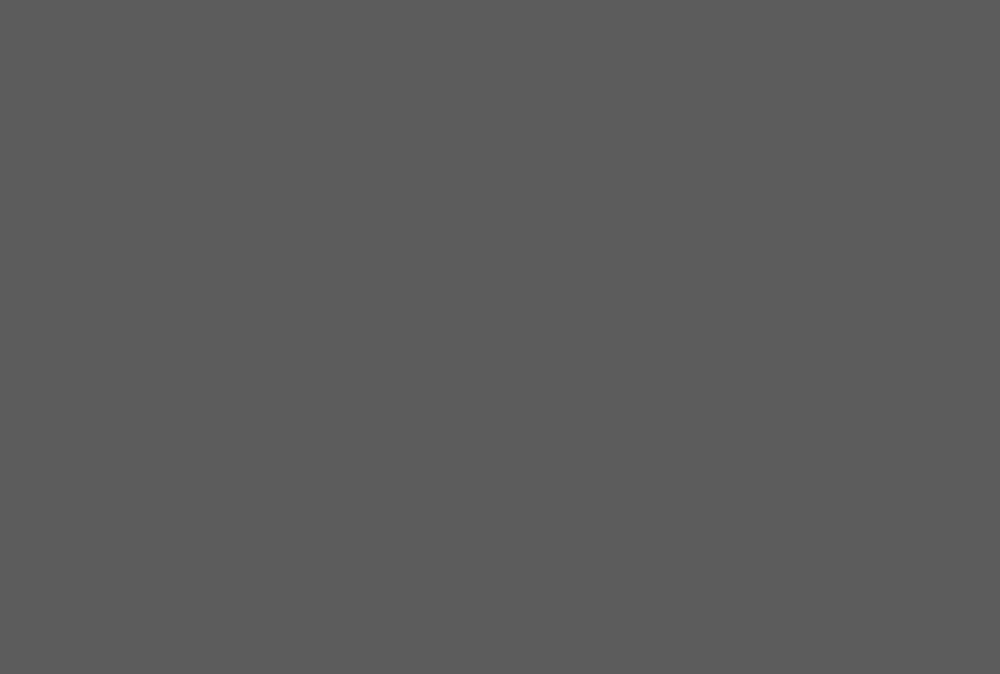
Properties of aluminum alloy
- Excellent corrosion resistance
- Excellent intensity and hardness
- Excellent thermal conductivity and conductivity
- Good stiffness and high weight ratio
- Excellent shielding performance of EMI & RFI
- Light weight
Aluminum die casting products are gradually accounting up the market. Why they are so competitive? One of the reasons is its high intensity. Besides, its good corrosion resistance and great heat dispersion also make it a better choice.Apart from that, we widen its application range again with our patents in aluminum die casting technology. Contact us now and get project assessment for free!
The aluminum alloy die casted components have advantages that other alloys don’t, which are light weigh and diverse finishing options.Besides, it also has good performance in resisting high temperature and corrosion, which further widen its application range. It appears in almost every industry. Apart from that, even with thin wall thickness, it still maintains a great dimensional stability.
Electronic instruments
Aluminum can stand high temperate environment, for its great electricity and shielding properties. Electronic connectors and shells components all can be produced through die casting.
Handheld device
Die casted aluminum parts are able to shield EMI/RFI for handheld devices. Its good stiffness, durability and light weight making it more and more popular. It’s also very light in weight.
Communication equipments
The aluminum die casting parts mostly used industries involve network construction, telecommunication infrastructure, and computer industry as aluminum has a good performance in heat dissipation of radio-frequency filter shells.
Automobile
Die casted aluminum parts can improve the fuel efficiency of cars by lighten weight.
Die casting
Application fields of aluminum die casting
The processing industry often maximizes the performance of materials and applies the value of materials to your project at a low price.
Application fields of aluminum die casting
Die casted aluminum parts can improve the fuel efficiency of cars by lighten weight.
Network construction, infrastructure of telecommunication and computer industry also involve die casted aluminum parts. As shells of radio-frequency filters generate lots of heat in working, so the aluminum can facilitate with heat dissipation.
For handheld devices, die casted aluminum parts can shield EMI/RFI, and it has good stiffness and durability. It’s also very light in weight.
Aluminum is often applied into high temperature working environment because its great electricity and shielding properties. Electronic connectors and shells usually are die casting components.
Recycling of die casted aluminum components
The function of primary aluminum ( pure aluminum or purification aluminum) and recycled aluminum( recycling aluminum) is slightly different. The latter is transferred from molten or pure aluminum mixed with metals, like magnesium, iron, and copper.Pure aluminum is very rarely to see in die casting as the high cost of aluminum purification, while aluminum alloy is almost the first choice for designers from any industry because its properties of light weight, durability and easy to use.
With a very small amount of energy manufacturing consumption (5%), the recycled aluminum is more cost-effective than primary aluminum. This small percentage of energy largely distributes to the heating and metal remelting. GREFEE can save more time, energy and cost by controlling inner re-melting according to product usage requirements.
Common aluminum die casting materials
Materials we frequently used for die casting are ADC12, A380, A383…etc.
ADC12(AL-Si-Cu base cast aluminum alloy) has good properties of castability and mechanical, so it’s usually used for automotive components with complicated shapes, such as gearbox, cylinder blocks and converter shells. It is also one of an alloy widely used in international production of press mould shells.
Mechanical properties
Chemical composition
A380 aluminum die cast
A380 is one of the commonly used material. Since its good properties of pressure resistance, heat resistance and liquidity, it’s the most optimal combination of mechanical, castability and thermal properties. A380 is widely used in many industries.A380 is widely used to make products such as engine brackets, electronic chassis, household furniture, gearbox shells, hand tools…etc.
A380 is one of the most widely used aluminum alloy, and has many obvious advantages:
- It’s the perfect combination of mechanical, castability and thermal properties
- It has excellent properties of liquidity, air tightness and heat resistance
- A380 is used to make many kinds of products, such as: electronic chassis, engine brackets, gearbox shells, household furniture, electric and hand tools….etc.
Advantages of aluminum A380 die casting
Compared with other alloys, aluminum alloys has multiple advantages, including light parts production, more finishing options and higher performance in bearing high processing temperature. Apart from that, die casted aluminum parts resist corrosion and remain a high dimensional stability even for low wall thickness, so it has wider range of uses.
Learn more about thin-walled aluminum die casting.
Select appropriate alloy for die casting
Aluminum A380 is one of the commonly used material in die casting, but it is one of the alloys in GREFEE. To achieve perfect parts, first need to select appropriate material. In GREFEE, we don’t think your options in materials are limited.
Mechanical properties
Physical properties
Chemical composition of A380
Aluminum die casting — A383
A383 suits for more complicated components, can replace A380.A383 has better corrosion resistance and lighter weight, fine liquidity, easy to die cast, and excellent properties of mechanical and dimensional stability.
Application advantages of aluminum die casting
Easy to add inserts. It’s easy to design locations in die casting mould, which is easy to add inserts.
ONE
Can make metal components with complex shape, clear outline, thin-walled and deep cavity. Since molten metal keeps high liquidity under high pressure and speed, can make metal components which cannot be made from other technologies.
THREE
High material utilization. Since the high precision of die casted parts, they can be assembled and used after only slightly machining, some even can be assembled and used directly. The material utilization is around 60%-80%, and blank utilization can meet 90%.
TWO
Die casted parts are high precision, which can meet grade IT11—13, or even grade IT9 sometimes. Surface roughness can meet Ra0.8—3.2um. It has good interchangeability.
FOUR
High productivity. Since high speed filling, short filling time, and the metal also freezes fast, die casting works in a fast cycling way. Among all kinds of casting technologies, die casting is the most high productivity one, which suits for massive production.
Aluminum die casting manufacturer
GREFEE is a first-class company providing aluminum die casting service to suits your project development. We provide customers best die casting solutions from hundreds of prototypes to tens of thousands production components. We have experience in die casting area for decades, and provide services for customers in different industries from all over the world. 99% customers are satisfied with our quality and service, also our price.
Low volume assortment items supply in die cast aluminum.
- GREFEE provides our customers integrated solutions of prototype designing, mould, die casting, machining work, finish and assemble, so it is in aluminum die casting.
- GREFEE provides a variety of aluminum materials to suit your needs for small batch manufacturing.
- GREFEE strictly controls the quality even though for your small batch components.
- GREFEE provides a series of reworks to suit your product needs.
- GREFEE closes to Hong Kong. Your aluminum die casted parts can be exported from HK port conveniently and efficiently.
Common defects on die casted parts and solutions:
Many abnormal problems will be encountered during the production of die casting project. The following are some common problems and solutions. You can also consult our engineers. CONTACT US >
- Liquidity shortage of molten aluminum, molten aluminum contains high air content, has more oxide skin.
- Poor gating system, too small gate section.
- Poor venting, too much coating, or too high mould temperature making air hard to vent.
- Increase the liquidity of molten aluminum, appropriately increase gating temperature, mould temperature and gating speed.
- Increase gating section acreage.
- Improve venting conditions, add material chute and venting plug etc.
- Unreasonable structure of die casting part, causing thermal centre in thick areas.
- Large shrinkage of alloy, or too high mould temperature.
- Too small gating section acreage
- Improve die casting part structure, make wall thickness even as much as possible.
- Choose alloy with relatively small shrinkage, low down temperature appropriately, adopt temperature control devices.
- Increase gating section acreage appropriately.
- Too high temperature of die casting mould or molten aluminum.
- Too quick speed of filling, or molten metal with air.
- No good venting, or opening mould too early.
- Cooling mould to working temperature, improve melting technology.
- Low down filling speed, avoid vortex with air.
- Clear and add venting grooves, adjust mould opening time.
- Material may have problems.
- Mould problems, main because unbalance ejecting press, unreasonable cooling design causing unbalance mould temperature, and unreasonable material filling.
- Choosing technological parameters inappropriately, technological parameter problems mainly result from wrong time control on mould retention and eject delay.
- For die casting materials, try not to use too much scrap materials or recycled materials, especially for thin-walled parts.
- Modify mould to achieve appropriate situation of ejecting, cooling and filling.
- Mould retention time cannot be too long, usually 3 seconds for each millimeter wall thickness. Eject time cannot be too long, usually 0.5-2 seconds.
- Raw materials may have impurities.
- use too much mould release agent or the release agent contains high organics. These organics are reduced to carbon or organic macromolecular polymers in high temperature molten aluminum. Carbons and polymers became black spots on die casted parts’ surfaces.
- The main thing is to check whether the raw material contains impurities or foreign substance.
- Increase the demould draft of die casted parts to reduce the useage of release agent. Decrease the concentration of coating paint, choose alternative painting or lengthen the ventilation time after painting.
- Not tight assembling between cavity and core, there’re relatively large gaps.
- not enough mould clamping force causing metal material splash, or unparallel fixeing plates in cavity and core on die casting machine.
- Too large injection force causes deformation of mould or fixing plates on die casting machine, thus cause material spraying.
- Check mould and do mould fitting again, control the gaps within reasonable range.
- Increase mould clamping force, make it parallel for mounting plates in cavity and core.
- Change into larger die casting machines, add support pillars, or strengthen the intensity of fixing plates.
- The main reason is that the uneven spread of release agent or injection oil, they’re gathered partly causing composition abnormal on aluminum alloy surface or piebaldness, which causes textures after anodize. Basically the textures of anodizing is consistent with that of die casting.
- High speed injection causes insufficient filling, unclear outline , and marginal incomplete, which then causes textures after parts anodized.
- Anodizing tank contains too much Copper ions, may cause textures, but this rarely happens.
- Seldom or even not to use release agent, assure even painting and not gathered.
- Assure qualification of part filling, enhance part testing.
- Decrease the content of copper oxide.
- Firstly, check the mould temperature to see whether it’s normal. Appropriately decrease the temperature of mould and molten material gating.
- Check the ratio of release agent to see whether it’s normal. Try to change different release agents, and adjust painting locations or polishing.
- For nitrided moulds, for caution’s sake, not to polish. If do need polish, pay attention to damage the surface nitration layer(if the nitration layer damaged, will get into trouble of the more polish, the more sticky)
- Improve the structure of gating system, to avoid molten metal material continuously impacting cavities and cores.
- Improve mould cooling system, to assure enough cooling in sticky areas.
- Adjust die casting technology parameters, low down the gating speed appropriately, and short injection distance.