The application of 3D printing in the laryngoscope mold
Posted on : March 31, 2022 By GREFEE
Medical care used tools have rigorous requirements on accuracy. Thus, it has higher requirements for the accessories production of medical used machines. In the production of the accessories of medical devices, there is no tolerance for the surface quality, accuracy, and hygiene, from the hyperbaric oxygen chambers to hearing aids, anesthesia laryngoscopes, medically used buttons, and other injection molding products.
If it is required, it has to be changed. The qualified rates of injection molding products are related to many factors, such as injection molding machine, mold, raw material, and the temperature controlling system.
How to make sure the fundamental things – the modification of mold makes sure the quality improvement of medial or high-end products and accelerating the production efficiency, which is also the focus of many medical devices mold makers.
GREFEE takes the laryngoscope as an example. We will discuss the specific advantages and provide the analysis of 3D printing in the medical health care field and other high-grade projects.Contact US
The disposable anesthesia laryngoscope is complicated in many medical injection molding products and is also the typical one. Show as pic one.
1. It has a complex structure with a narrow top space.
2. The top tip is directly in contact with the human body, so the requirements for hygiene are strict.
3. Rigorous requirements for sizes and quality, no defects are allowed on the surface.
4.The laryngoscope is a disposable product, so the volume is large, and the cost should be controlled within the range.
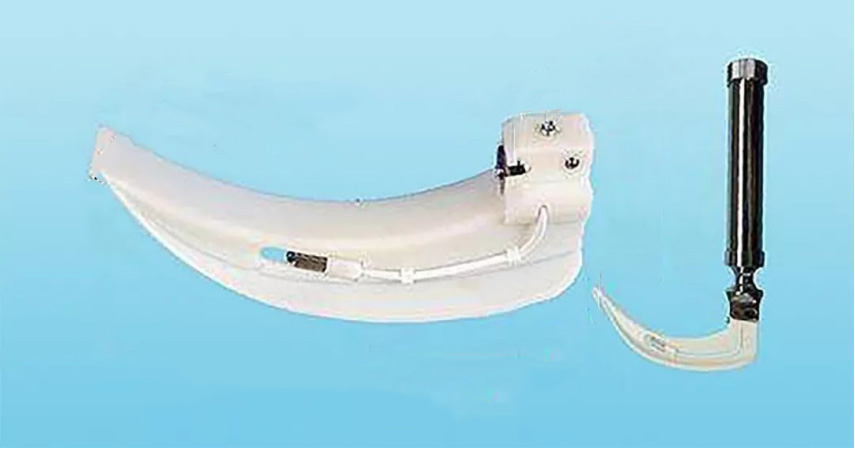
1.The top tip contact the body, so it is strict with the hygiene of materials.
2.Complex structures, narrow top space.
Diagram of the laryngoscope,Therefore, for mold makers, how to balance the quality, efficiency, hygiene and other aspects is the key.
It is well-known that one of the important methods to assure the quality of the mold is the waterway system. A well-designed waterway system can shorten the forming cycle and increase the qualified rates.
However, the waterway is generally made by the milling machine or other machining technologies so far. The cured waterways are still not available and cannot cover the mold cavity.
Advantages of the 3D printing laryngoscope
Defects of conventional waterways
Waterways are not available due to the deep holes and the cycle is long
Medical used beryllium copper is expensive and long order time with poor effect
Shown as pic 4, for the difficulties faced by the ordinary plan, the additive manufacturing conformal waterways design can help with.
1. Forming cycle
For conventional waterways, a 3D printing-designed waterway system covers the mold cavity so that it can accelerate the cooling, shorten the forming cycle, and raise the production efficiency.
Ordinary waterway cooling time: 32s conformal waterway cooling time: 23s
Show as pics above: the conventional waterway cooling time is 32s, whereas the conformal waterway cooling time is 23s. 3D printing reduces the time for reaching the ejection temperature by 23%.
2. Surface quality
The forming quality of injection molding products is related to the mold temperature to a great extent. Unbalanced mold temperature, the temperature difference between the highest temperature and the lowest temperature is big so that the high-temperature area is easy generates many defects, such as scaled or deformation.
This largely affects the qualified rates. The 3D printing conformal waterways are distributed evenly in the mold cavity, which can minimize the temperature difference, balance the mold temperature, and increase the qualified rate.
Temperature difference for ordinary waterways: 32.5℃
Temperature difference for conformal waterways: 4.98℃
The mold flow analysis result shows that the temperature difference between the highest and the lowest temperature of ordinary waterways is 32.5℃. While, the temperature difference for the conformal waterways reduces to 4.98℃, which is almost no difference.
Besides, in terms of the 3D printing material, GREFEE uses the self-developed EM191 metal powder. It has many properties, such as anti-rust, corrosion resistance, anti- scratches, and durability, which assure the work life. In our self-developed powder system, there are also EM181, EM201, and other materials which are 3D printing used. Choose different materials according to the needs.
With the development and updating of technology, 3D printing will be applied to more fields, and mold manufacturing must update and improve itself with new technologies. GREFEE has been seeking innovation and takes it as our mission to inject new blood and new ideas into this industry,CONTACT US
Try GREFEE now,for free
We keep your uploaded files confidential and secure.