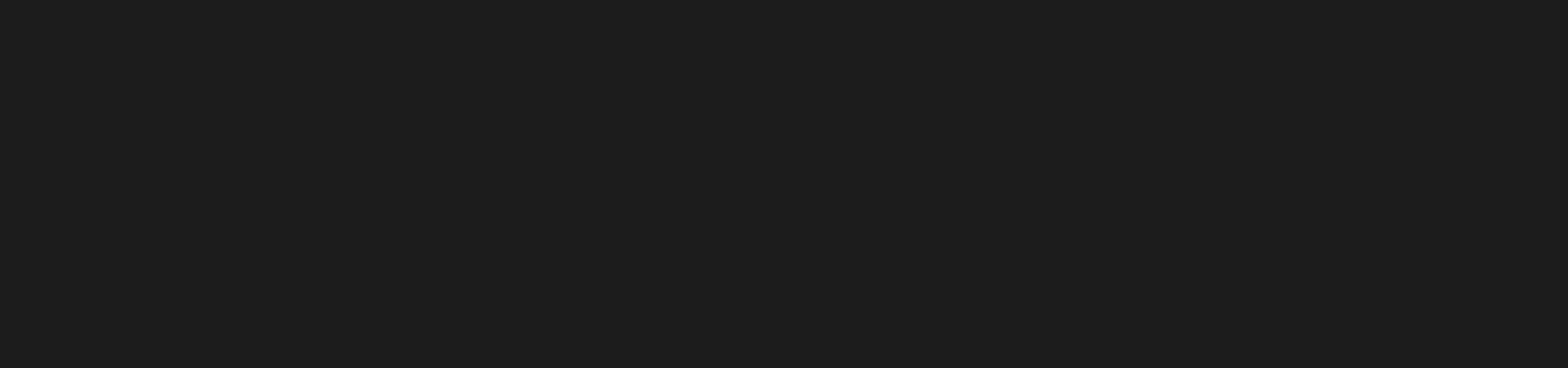
Common Surface finishes
Surface treatment of parts? Now consult us.

- You can choose more than thirty ways.
- Professionals have more than 10 years of processing experience.
- Provide processing effect photos in the fastest three days.

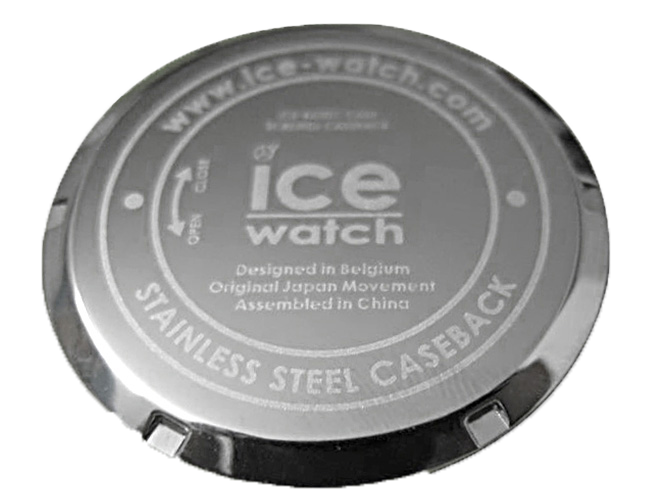
- A good product is not just machined, various surface finishes shall be applied to ensure the corrosion resistance, wear resistance, aesthetic and longer service life.
- GREFEE has years of prototyping experience, CNC, 3D Printing, etc. We provide a series of one-stop services ranges from machining, surface treatment as well as assembly.
- Therefore, in addition to CNC technology we are also experienced in surface treatment including painting, baking, powder coating, sand blasting, shot blasting, anodizing, hard anodizing, micro arc oxidation, electroplating, electrophoresis, laser engraving, silk screen, brushing, mirror polishing, dyeing, black oxide, CD pattern, etching, high glossing, etching pattern, glue dropping, etc. The products will be like icing on the cake with a good finish.
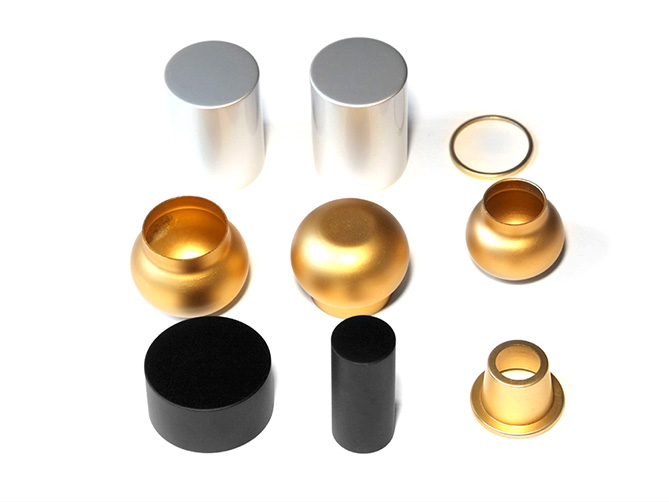
Anodizing
Anodizing is an electrolytic process which converts the surface of metal parts into a protective film.
The natural oxide layer increases resistance to corrosion and wear, and provides better adhesion for paint primers and glues than bare metal does. With anodizing finishing you can get a product with a longer service life and more color options. There are different types of anodizing that can be divided into: ordinary anodic oxidation, brushing oxidation, hard oxidation, thick film oxidation, micro arc oxidation, etc. Materials that can be oxidized are aluminum alloy, magnesium alloy, titanium alloy and so on.
Electroplating
Basically, the electroplating refers to immersing the parts in the metal salt solution as the cathode whereas the metal plate works as anode, to generate a metal coating on a solid substrate to achieve the reductions of cations of that metal by the direct electric current. Electroplating can benefit your products in many ways. it can make your products more aesthetically pleasing and brings more market potential. There are many different types of electroplating so far, which have been widely applied into different products manufacturing.
Electrophoresis
Electrophoresis (EP) is the short name of electrophoretic phenomenon, which refers to the phenomenon that charged particles move towards to the opposite electrode under the action of electric field. The separation technology of using different moving speeds of charged particles in the electric field is called electrophoresis technology. As its industrial demands increasing, electrophoresis treatment has been a popular method for keeping metal luster no matter colors you’ve selected and improving corrosion resistance of the products surface. Electrophoresis treatment has little effect on the accuracy of products. The electrophoresis film thickness in one side is about 10-25um. Actually the thickness can also be customized if you prefer a thicker film.
Passivation
Passivation is also known as chromate treatment which is a kind of acid pickling technology. the passivation process uses acid or ultrasonic cleaning to remove free oil scale, rust stain and oxide on the surface. After that a protective outer layer of shield material will be created by the chemical reaction of passivation solution. This oxide layer that is less likely to chemically react with air and cause corrosion which helps to prevent corrosion and resists rust. The color of passivation films altering depends on the material types. Passivation won’t affect the tolerance of the product as it doesn’t has an impact on the thickness of the product.
Black Oxide(Blackening)
Blackening, also known as bluing, which is a process used for improving the corrosion resistance by generating an integral protective oxide film on the metal surface. Products are soaked in intense oxidizing chemical solution to cut off the air contact to stop the occurrence of rust. This technique is applicable to ferrous materials like iron and steel.
QPQ
QPQ is the abbreviation of Quench Polish Quench,it is sometimes known by the brand name of Tufftride, Tenifer or Melonite. The process is to put ferrous metal parts into two different kinds of salt solutions, during which multiple elements been penetrated into the metal surface and forms a composite infiltration layer, so as to achieve the purpose of improved cosmetic surface. QPQ finish helps to have good coefficient of friction, fatigue resistance, corrosion resistance and small deformation. QPQ process is suitable for all kinds of iron and steel materials.
(Note: Black Oxide is not work for stainless steel products, QPQ can help SS products get a black surface)
Laser Engraving
Radium carving is commonly applied to engrave logo or pattern on products through optical principles, is also named Laser engraving or loser marking.Radium carving effect is permanent and has high surface quality. It is suitable for all kinds of metal and plastic products.
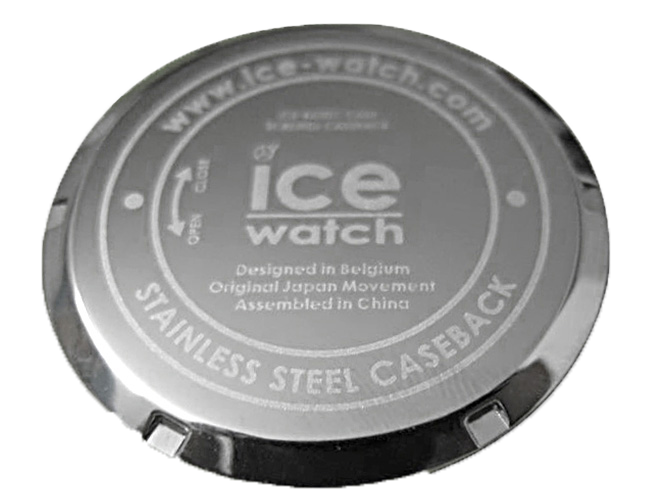
Polishing
Polishing is a kind of surface finishing process for smoothing a workpiece’s surface, which leads to a brighter and aesthetic surface. Thus, transparent polishing shall be a good choice for you if you are looking for a beautiful surface. Metal polishing has two types: mechanical polishing and electrolytic polishing. Electropolishing can be used to replace heavy mechanical polishing, especially for parts with complex structure and parts that are difficult to be polished by hand or mechanical methods. Electropolishing is often applied for steel, aluminum, copper and other metal parts.
Silk screen printing
Screen printing transfers ink pattern onto a substrate surface by a mesh.er ink pattern onto a substrate surface.
Normally, it is single color printing mode each time. However, It can apply several screens as it can produce a multi-colored image or design as you wish GREFEE has many successful projects that to print 6 colors on one product surface (including black, red, blue, yellow, white and green). If you prefer to have a more lasting screen printing, the UV layer could be added after the screen printing to prolong its service life. The screen printing is suitable for all kinds of metal and plastic materials, and can also be applied together with surface treatments such as oxidation, painting, powder spraying, electroplating, electrophoresis and so on.
Brushing finish
Brushing is a type of surface treatment that forms lines on the surface of the metal products through flat pressing abrasive belt and non-woven roller brush which provide a durable, high-traction surface. A good brush finish is something of an art.
Brushing finish is becoming more and more popular in modern life. It is widely used in smart phones, computers, displays, furniture, electrical appliances and so on.
Powder Coating and Painting
Powder coating and painting are two normal surface finishes in metal parts. It’s also been commonly applied in precision parts and small batch customized products. It is usually used to form a hard finish that is tougher than conventional paint which can protect the surface from corrosion and rust, and can also provide a beautiful surface. In GREFEE you can choose different textures (fine grain, coarse grain, leather grain, etc.), different colors as well as different glossiness (matte, flat, high gloss).
Sandblasting
Sand blasting is an effective method for surface treatment of metal products. As the sand particles strike the surface, it creates a smoother and more even texture which can improve the cleanliness and roughness of the products. The adherence and durability will also be improved at the same time between products and coatings. It has been the choice of pretreatment in many surface treatments, for instance, sand blasting + oxidation, sand blasting + electroplating, sand blasting + electrophoresis, sand blasting + powder spraying, sand blasting + paint baking, sand blasting + passivation, etc.
Teflon Coating
Also known as Teflon spraying, it is a very special surface treatment. It has the characteristics of superior viscosity resistance, non-viscosity, high temperature resistance, low friction, high hardness, non-humidity and high chemical resistance, etc. Therefore, it is widely used in food industry, tableware, kitchenware, paper industry, medical devices, electronic products, automotive parts, chemical equipment and so on. In the meanwhile, Teflon coating can protect the material from chemical corrosion, which lengthens the useful lifespan of the parts.
In addition to the above surface finishes, GREFEE also provides shot blasting, dyeing, CD pattern, etching, high glossy, etching pattern, glue dropping, etc. for more details, please feel free to contact us.
Electroplating coat thickness chart
Category | Electroplating Type | Thickness | Features |
Barrel plating | Nickel | 8um/min | Glossy and good corrosion resistant |
Barrel plating | Nickel | 8um/min | Smooth and average anti-corrosion |
Barrel plating | Nickel | 8um/min | Smooth and good corrosion resistant |
Barrel plating | Blue zinc | 6um/min | Good corrosion resistant, soft blue |
Barrel plating | Color zinc | 8um/min | Average corrosion resistant,colorful |
Barrel plating | Green zinc | 6um/min | Good corrosion resistant, army green |
Barrel plating | White zinc | 4um/min | Poor corrosion resistant, zinc white |
Barrel plating | Black zinc | 6um/min | Good corrosion resistant, pure black |
Hanging plating | Steel chrome plating | Ni 8um/min | Cass experiment, continuous spray for 16 hours, 7 level. |
Hanging plating | Steel chrome plating | Cr 0.2~0.3um/min | Cass experiment, continuous spray for 16 hours, 7 level. |
Hanging plating | Zinc alloy chrome plating | Cu 10~25um/min | Neutral salt spray test for more than 96 hours |
Hanging plating | Zinc alloy chrome plating | Ni 5~10um/min | Neutral salt spray test for more than 96 hours |
Hanging plating | Zinc alloy chrome plating | Cr 0.2~0.3um/min | Neutral salt spray test for more than 96 hours |
Hanging plating | Copper chrome plating | Cu 10~25um/min | Neutral salt spray test for more than 96 hours |
Hanging plating | Copper chrome plating | Ni 5~10um/min | Neutral salt spray test for more than 96 hours |
Hanging plating | Copper chrome plating | Cr 0.2~0.3um/min | Neutral salt spray test for more than 96 hours |
Any other questions?