Secondary Processing After CNC Machining: Heat Treatment

Posted on : April 27, 2022 By GREFEE
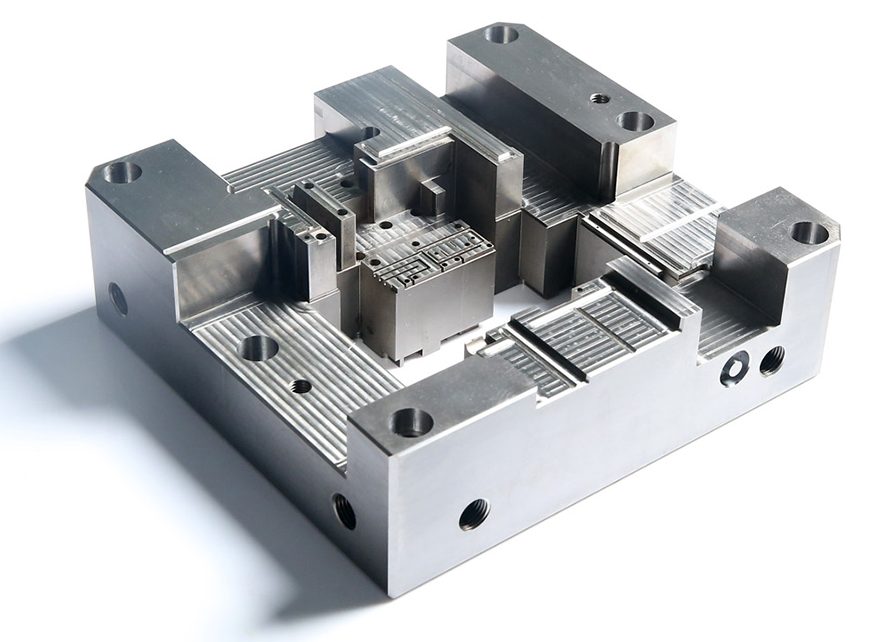
Secondary Processing After CNC Machining: Heat Treatment
When you finish the CNC parts, your job has not been done actually. These components might come with rough surfaces and insufficient strength, affecting the service life. Or they might be a part of a component and have to be connected with other accessories to obtain a complete product, even though the possibilities of using the CNC components and other components are higher.
The important thing is that secondary processing is important in the performance of the components. Here, I would like to talk about some things you should pay attention to. This will help you select the correct heat treatment method for your projects.
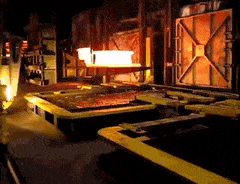
Heat treatment before processing or after processing?
(1)The first thing you need to consider after processing is the heat treatment or the material of the heat treatment. Why does this method not others? The processing order of heat treatment and machining of the metals might affect the material property, machining process, and tolerance.
(2)If you use the already heated material, it will affect your processing —— Hard materials need longer machining time. What’s more, the tool wears quickly, which increases the cost. According to the heat treatment type or the depth below the surface of the materials being affected, we can cut off the hardening layer. This will lose the meaning of using the hardening metal.
(3)There might have enough heat generated to enhance the stiffness of the components. Some materials, like stainless steel, are more easily hardened during the mechanical machining process, so we should be aware of it.
(4)However, metals that receive heat treatment have some advantages. For hardening metal, your components can maintain rigorous tolerance and the metal can be used at any time. Thus, it is easier to purchase materials. Moreover, if we wait until the treatment is done, heat treatment will add another time-consuming step in the production process.
(5)On the flip side, the heat treatment after the machining process will make you better control the machining process. There are many types of heat treatment. You can select which types to obtain the required material properties. The heat treatment after the mechanical processing ensures the consistency of the heat-treatment effect. For the materials which have been pre-heated, heat treatment might only affect the material. Thus, mechanical processing might remove the hardened materials in some places rather than other places.
As said above, heat treatment increases the cost and lead time because it needs extra outsourcing steps. It might also affect the tolerance due to the warpage or deformation
What is quenching?
The quenching of steel is to heat the steel over the critical temperature AC3 (hypoeutectoid steel) or AC1 (hypereutectoid steel). To preserve the heat for a moment, make the whole part of it austenitic and then cool the steel to lower than Ms (or close Ms) with a cooling speed higher than the critical cooling speed. Next is to start the heat treatment of transmitting the Martensite (or bainite). Usually, the solution treatment of aluminum alloys, copper alloys, titanium alloys, tempered glass and other materials or heat treatment combined with rapid cooling is called quenching.
Aim of quenching:
(1) increases the mechanical property of the metal materials or components, such as: increasing the stiffness and wear resistance of the tools and bearing, the elastic limit of spring, the comprehensive mechanical property of the shaft parts, etc.
(2) improves the material property or chemical property of some special steels, such as increasing the corrosion resistance of stainless steel, permanent magnetism of magnetic steel, etc.
(3) In quench cooling, except for selecting the quenching mediums, the correct quenching method is also necessary. The common quenching methods include single liquid quenching, double liquid quenching, step quenching, isothermal quenching, and local quenching, etc.
Characteristics of steel parts after quenching:
- Unbalanced (i.e. unstable) structures such as martensite, bainite and retained austenite.
- Large internal stress.
- Insufficient mechanical property. Thus, the steel must need tempering after quenching.
What is tempering?
Tempering is a heat treatment used to heat the metal or materials to a temperature after quenching and then preserve the heat for a while. Tempering is an operation after the quenching. It is usually the last step of the heat treatment. Thus, we call quenching and annealing the final processing procedures.
Main aim of quenching and annealing
(1) reduces internal stress and brittleness. The quenching parts have big stress and are brittle. Deformation and cracking might occur without quenching in time.
(2) adjusts the mechanical property of components. After quenching, the stiffness level and brittleness of parts are high. To meet the requirements in the property of diverse comments, we can adjust the stiffness, strength, plasticity, and toughness through annealing.
(3) stabilizes the dimension of parts. A stable metallographic structure can be achieved by tempering to prevent deformation in the future.
(4) machinability improvement of some alloy steels
functions of tempering
(1). Increases the stability of structure to prevent the parts from structure transmission in using so that its geometrical dimension and properties are ensured.
(2). Eliminates internal stress to improve the using properties and stabilizes the geometrical dimensions of parts.
(3). Adjusts the mechanical properties of iron steel to meet more needs
The reason why tempering is functional is that its atomic activity increases when the temperature goes up so that the iron, carbon, and the atomic of other alloys would spread quickly and achieve the rearrangement of atomic to turn the unbalanced structure into a stable and balanced structure. The elimination of internal stress is also related to the stiffness of metals when the temperature increases. Generally, when the iron is tempering, its stiffness and strength decrease but plasticity increases. The high the tempering temperature, the bigger the mechanical property changes. Some alloy steel with a large extent of alloy elements will precipitate some metal compounds when tempering at a specific temperature, which increases its strength and stiffness. This is called secondary hardening.
Tempering requirements:
components for different uses should be tempering under different temperatures to meet the requirements in using.
(1).Tools, bearing, carburized and quenched parts, Surface quenched parts usually being tempered under 250 degrees. The stiffness difference is little after being tempered under low temperature. Its internal stress reduces, but toughness increases a bit.
(2). The spring should be tempering under 350-500 degrees to obtain higher elasticity and required rigidity.
(3). The components made of medium carbon structural steel usually being tempered at 500-600 degrees to obtain good coordination of strength and toughness.
When the steel is tempering at 300 degrees, its brittleness increases and is called Type I temper brittleness, which normally does not temper in this temperature range. Some carbon alloy structure steels will turn brittle after high temperature tempering, then air cooling. This is called Type II temper brittleness. Adds the molybdenum into the steel or cools it in oil or water when tempering can prevent the Type II temper brittleness. Reheats the steel of the Type II temper brittleness to the original tempering temperature to eliminate the brittleness.
In production, we often divide the tempering into low temperature tempering, medium temperature tempering, and high temperature tempering according to the properties requirements and heating temperature. Conditioning is the quenching and tempering combined heat treatment technique. It has high strength and good plasticity and toughness.
(1) low temperature tempering: 150-250 degrees, M-loop to reduce the internal stress and brittleness, increase the plasticity and toughness, increase the high stiffness and wear resistance, for making the antifriction bearing, tools, measuring tools, etc.
(2) medium temperature tempering: 350-500 degrees, T-loop, has high elasticity, and a good plasticity and stiffness, for making spring, forging mold, etc.
(3) high temperature tempering: 500-650 degrees, S-loop, has great comprehensive mechanical property, for making gear, crankshaft, etc.
What is normalizing
Normalizing is a type of heat treatment for improving the toughness of the steel. Heats the steel parts to 30-50 degrees higher than Ac3 and preserves the temperature for a while before air cooling out of the furnace. The primary characteristic is its cooling speed is faster than that of the annealing but slower than quenching. In the normalizing process, we can refine the steel’s crystal grain in the rapid cooling process. This not only brings satisfied strength but also increases the toughness (AKV value) and minimizes the cracking tendency. The comprehensive mechanical property and machinability of some dilute alloy hot rolled steel plates, dilute alloy steel forgings, and castings improved significantly after normalizing.
Functions of normalizing
(1).For Hypoeutectoid steels, the normalizing method is used to eliminate the superheated coarse grain structure and widmanstatten structure of the castings, forging pieces, and welding pieces. It also helps with the banded structure in rolled products, and refined grains, and also can be used as the pre-heated treatment of the quenching.
(2).For Hypereutectoid steels, normalizing can eliminate the netting secondary cementite and refine the pearlite. It not only improves the mechanical property but also helps the spheroidizing annealing.
(3).For low carbon deep drawing steel sheets, normalizing eliminates the free cementite at grain boundary to improve the deep drawing property.
(4).For low carbon steel and low carbon low alloy steel, normalizing has more sliver pearlite structures to raise the stiffness level to HB140-190 to avoid the sticking issue in machining, which improves the machinability. Medium carbon steels not only suit for normalizing but also for annealing. While normalizing is cheaper and more convenient.
(5).For ordinary medium carbon structure steels, with different requirements of mechanical properties, we can replace the quenching by normalizing plus high temperature tempering. It is not only simple but also ensures a stable structure and dimension of steel.
(6).High temperature normalizing (Ac3 above150~200℃). Due to the high spreading speed under high temperatures, the composition segregation of castings and forging pieces is improved. The rough grains after annealing can be refined after the second lower temperature annealing process.
(7).For some low and medium carbon alloy steel for boiler and steam turbines, annealing is often used to obtain the Bainite structures. After a high temperature normalizing, it has great creep resistance under 400~550 degrees.
(8).Except for steel and iron parts, normalizing is also widely used for heat treatment of nodular cast iron to make it obtain pearlite matrix to enhance the strength of the nodular cast iron.
Normalizing is air cooling. Thus, the environmental temperature, stacking method, airflow, and dimension of pieces will affect the structure and property after Normalizing. The annealing structure can also be a classification method of alloy steels. Usually, the air-cooled structure can classify the alloy steels into pearlitic steel, bainitic steel, martensitic steel, and austenitic steel after the samples whose diameter of 25 mm is heated to 900 degrees.
What is annealing?
Annealing is a metal heat treatment technology used to slowly heat the metal to a specific level temperature, keep it for a while, then cool it at a proper speed. The annealing treatment is classified into complete annealing, incomplete annealing, and stress relief annealing. The mechanical property of the materials of annealing can be used for the tensile test, as well as the stiffness test. Many steel materials have received the annealing heat treatment for delivery. The stiffness test relies on the Rockwell hardness tester to obtain the HRB stiffness. Rockwell hardness tester also helps with the HRT stiffness test of thin steel plates, steel strips, and thin wall steel pipes.
Functions of annealing:
(1).To improve or eliminate any structural defects and residual stress of steel during the cast, forging, rolling, and welding processes to prevent the deformation and cracks of the workpieces.
(2).Soft the work pieces for machining process.
(3).Refine the grains and improves the structures to raise the mechanical property of work pieces.
(4).Prepare for the final heat treatment (quenching & tempering)
Common annealing techniques
(1).Complete annealing. Used for refining the large and overheated structure with poor mechanical properties of low and medium carbon steels after casting, forging, and welding.
(2).spheroidizing annealing. Used for lowering the high stiffness of the tool steel and bearing steel after forging. Heat the parts to a temperature that is 20-40 degrees higher than the start temperature of austenite. The parts cool slowly after heat preservation. The lamellar cementite of the pearlite turns into spherality in the cooling process, which lowers the stiffness.
(3).Isothermal annealing. Used to lower the high stiffness of some alloy structure steels with high nickel and chromium content to process machining process. It starts with cooling to the most unstable temperature of austenite at a faster speed and keeps it for a while till the transformation of austenite to troostite or sorbite, the stiffness will be lower.
(4).Recrystallization annealing. To eliminate the stiffness phenomenon in cold drawing and cold rolling of metal wire and sheet (stiffness raises, plasticity decreases). The heating temperature starts at 50 ~ 150 ℃ below the temperature at which the steel begins to form austenite. We can make the metal soft and eliminate the stiffness issues only through this method.
(5).Graphitization annealing. Used for turning cast iron with high cementite content into malleable iron with good plasticity. The first is to heat the castings to about 950 degrees and maintain the temperature for a while before they cool so as to degrade the cementite into the flocculent graphite.
(6).Diffusion annealing. Used to homogenize the chemical composition of alloy castings and improve their service performance. The way to do it is to heat the casting to a temperature as high as possible without melting, then keep the high temperature and cool till all the metal elements are distributed.
(7).Stress relief annealing. Used to eliminate the internal stress of the steel castings and welding pieces. For iron and steel products, the temperature at which austenite begins to form after heating is 100 ~ 200 ℃, cooled in the air after heat preservation.
For different requirements of CNC parts, proper heat treatments are essential. In order to obtain a better result, it also needs years of experience. GREFEE has almost 20 years of experience in CNC machining with 3-axis, 4-axis, and 5-axis machining equipment at 0.005mm machining accuracy. Try GREFEE for your new CNC projects.
Try GREFEE now,for free
We keep your uploaded files confidential and secure.