3D Printing Services
Improve productivity, quickly complete your project and reduce your budget by about 30%.


Deliverable in the fastest day

Multiple material selection and finishing options

Maximum size: 880*800*390mm
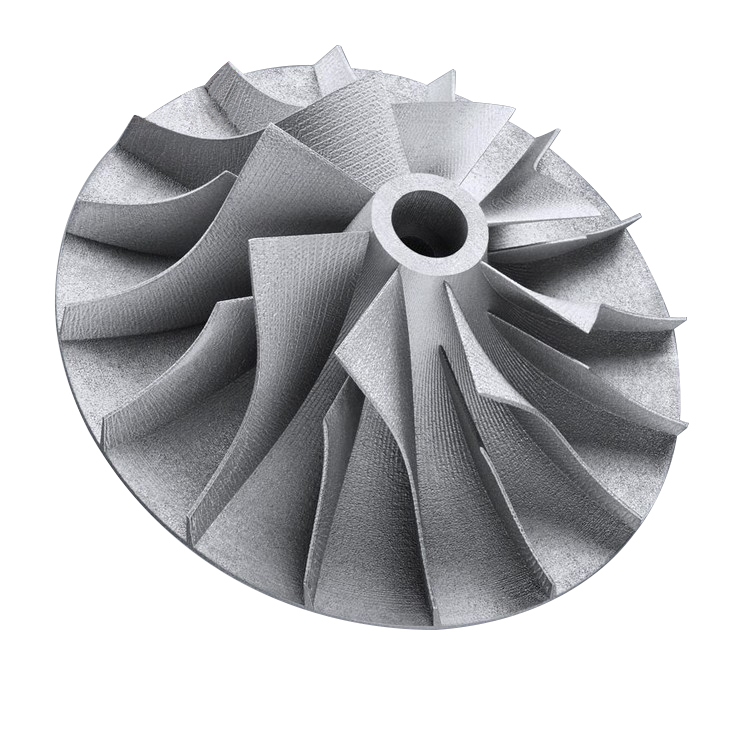
3D printing (3DP), also named additive manufacturing, which is one of the rapid prototyping technologies used for powder cohesive metal printing. It can print plastic material ring upon ring based on digital model files.
3D printing technology usually works with the help of digital technique material printer, which can make prototypes of mold manufacturing and designing in industry fields for the direct product production. 3D printing has been successfully applied in industry and has been worked perfectly. It has been applied in a wide range of purposes not only for medical, education, architecture but also engineering and aerospace etc. it has penetrated into all walks of life gradually.
3D Printing Technology
We’re equipped with more than 40 3D printers, used for printing plastic, metal and elastic parts. At GREFEE, your 3D printed parts can be made within one day. Besides variety options of materials, we also provide many kinds of finish to improve appearance or enhance mechanical property.
SLA:
SLA is the abbreviations of Stereo lithography Appearance.
Ultraviolet laser with specific wavelength and strength focus on the surface of photocureable materials, which makes material solidified from point to line, and line to surface, until complete one layer of printing, then the lifting platform in the vertical direction moves a layer of height to solidify another layer. In this way, these layers are stacked up to form a three-dimensional model.
SLA can be used to make precision components or parts with complicated structures, work in fast speed, and the precision error can be controlled within ±0.05mm.
Maximum size: 880*800*390mm
Advantages of SLA
- Stereo lithography Appearance is the earliest technology of rapid prototype manufacturing, high maturity, and stand the test of time.
- CAD digital model can produce prototype straightaway without tedious procedures, unlike some other similar technologies, it doesn’t need cutting tools and molds fo it processes quickly and saves lots of time for manufacturers.
- Pertains to manufacturing sophisticated prototypes and molds that cannot performed by conventional practice.
- Turning CAD digital model visualized and reducing problems fixing cost
- Experiments samples available and effective computer simulated calculation results verifications and inspections.
- Can be operated online and controlled remotely, and is beneficial to achieve automated production.
Disadvantages of SLA
- SLA system costs high in operating and maintaining.
- SLA system requires strict operating environment as it is the precision device working on liquid.
- SLA printed parts are mostly resin, with limited intensity, rigidity and heat resistance, which is not good for long-term preservation.
- Large calculation of the pre-processing software and driving software, and high correlation with the processing effect.
- It’s difficult to operate the complicated software system, so it’s hard to get started. Most designers are not familiar to the file format.
- Stereo Lithography Appearance technology is monopolized by certain company.
Development tendency and prospect of SLA
The developments tendency of SLA is high speed, energy conservation and environment protection, and microminiaturization.
Its continuous improvement of processing accuracy makes it most possible to have a brilliant future in biology, medicine, microelectronics and other fields.
Forming schematic diagram of SLA
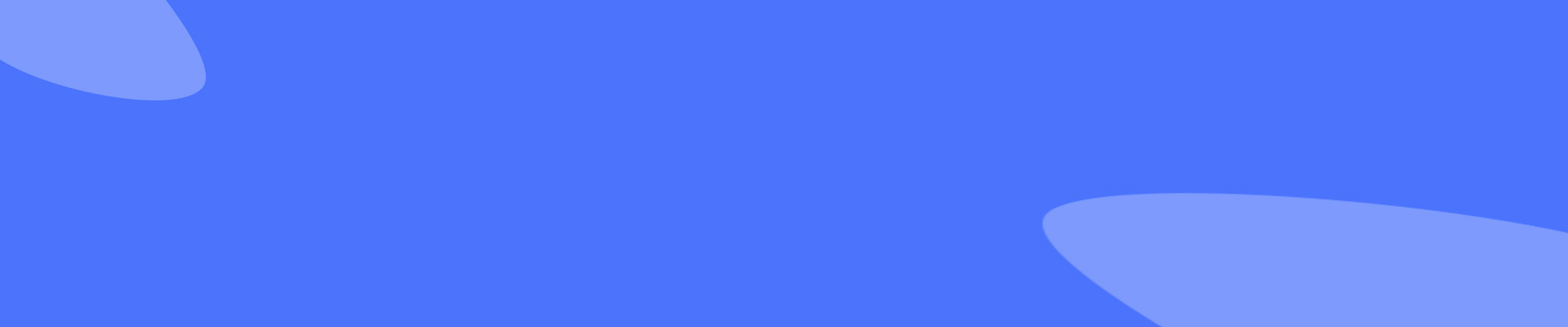
Selective Laser Sintering( SLS laser molding )
SLS is one of the 3D printing technologies, most use powder materials and adopt energy of infrared laser.
In processing, firstly pre-warm the powder material to the temperature next to its melting point, then pave the powder with scraping stick. Laser beam sinter selectively under control of computer according to the sectional information of layers, with layer by layer. An integral sintered part can be obtained before the needless powder taking off after sintering. At present, the maturely used processing materials are wax powder and plastic powder, while the technology of sintering metal powder or ceramic powder is still to be studied.
Technical principles of SLS
The forming principle of Selective Laser Sintering as below picture shows:
1) Powder particles are stored in the feed bin left side. In printing, the lift platform in feed bin rises up push the powder above the print plane to the printing plate in printing bin by spread powder roller, to form a thin and flat powder layer.
2) At this moment, the laser beam scanning system selectively scans the powder layer according to the 2D CAD path. The scanned powder particles will be sintered together under the high temperature of the laser, then form a sheet with a certain thickness, while areas not scanned still remains powder in loose status.
3) After one layer is sintered, the printing platform drops according to the height of the slice, and the horizontal roller paves the powders again, and then starts to sinter a new layer, meanwhile, the layers are sintered together.
4) In this way, repeat sintering until all layers are sintered, then remove and recycle the powder not sintered, and finally get the printed solid model.
Materials: Plastic powder, mixing powder of ceramics and binder, mixing powder of metal and binder, etc.
At GREFEE’s factory, we use Nylon(FS3300PA), Nylon + Glass(FS3400GF) in SLS technology.

Advantages of SLS
SLS technology is a technological method of integrating discrete points layer by layer to a three-dimensional model. It uses carbon dioxide laser to selectively sinter powder materials (plastic powder, mixing powder of ceramics and binder, mixing powder of metal and binder, etc.)
Materials and finished products
As a new manufacturing technology, SLS is different from commonly used technologies(like CNC, SLA) in traditional prototype manufacturing. SLS can make metal, plastic, or the mixture of these two. Nowadays, domestic commonly used material in SLS is PA12. SLS directly form three-dimensional parts by solid powder materials, not limited by complicated structure and curved face of parts, no need any assembling, directly make CAD model become real parts. SLS is a technology known as maximum complexity coefficient of prototype, widest application range and lowest operation cost. SLS can greatly shorten the lead time of product development, save cost of product development, speed up the update of product, and respond quickly to market demands, thereby greatly improve the core competitiveness of company.

SLM(Selective Laser Melting)
SLM(Selective Laser Melting) is the most common technology in 3D printing, adopting fine focusing spot to quickly melt metal powder on-premise, then get parts with any shape and fully metallurgical bounded, and the density of parts can meet 99% at least.

Main advantages of metal 3D printing
Most people thought CNC machining can make all parts. But sometimes need make a new device before make a part with high complicated structures. This is the main advantage of metal 3D printing—it can manufacture complicated shaped parts without limit.
Advantages of metal 3D printing
- Compare to traditional manufacturing methods, 3D printer can achieve complicated details more quickly.
- Cost less than traditional manufacturing methods.
- Based on selected technology, can make subtle parts with tiny structures.
- For products with complicated structures, 3D printed parts have lighter weight without sacrifice intensity. That’s why 3D printed parts are such highly demand in aviation industry.
- Metal 3D printing hardly waste material.
- In short, if other technologies cannot make complicated and subtle parts easily and efficiently, 3D printing is the first choice.
Disadvantages of metal 3D printing
- 3D printing is not perfect. Firstly, it is not so fast and cheap in manufacturing ordinary components. So, it’s not feasible for massive production.
- Other disadvantages of metal 3D printing:3D metal powder is much expensive than that of “ordinary” metals.
- Speed is relative slower in manufacturing traditional parts.
- Metal 3D printer is expensive.
- Sometimes need surface treatment and finish.
- Accuracy is lower than CNC machining relatively, and a bit larger error range.
- Sometimes need extra heat treatment to decrease inner press in printing.
- Cannot manufacture parts with large size.

Materials
For now, GREFEE provides metal 3D printing service of titanium alloy, stainless steel, and aluminum alloy. Each metal has its own unique advantages on performance, weight and corrosion resistance. Our engineers are glad to recommend the most suitable material to achieve cost-benefit.
Finish services
Metal 3D printing requires certain finish sometimes, to make up its limitation. At GREFEE, we provide comprehensive services of finish post processing. Our CNC machines can remove excessive material by milling, turning, drilling and grinding. We also provide a series of finish services to make sure you get parts with idea appearance.