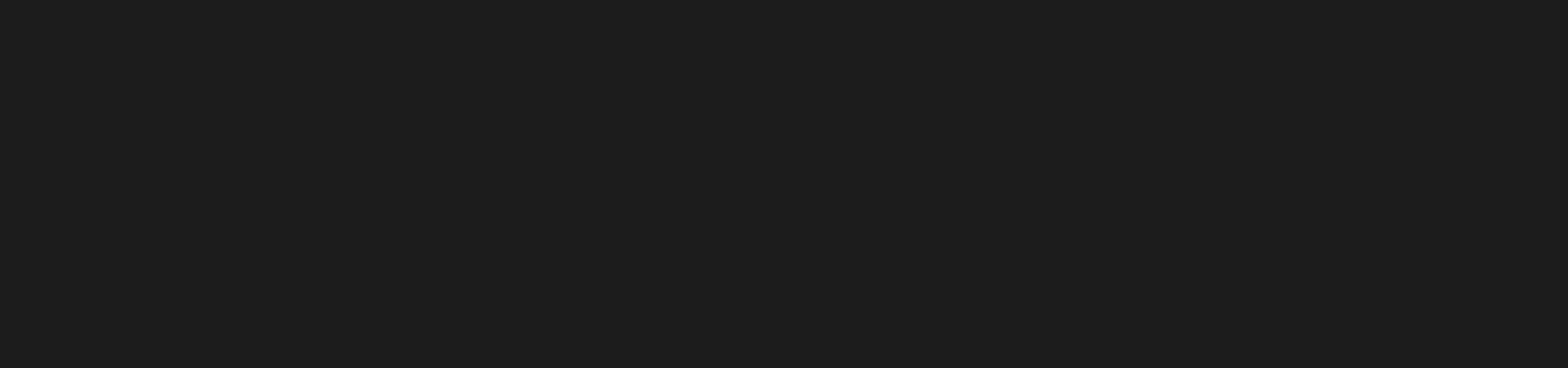
Zinc die casting
From materials to mass finished products, GREFEE can create higher value for your project
- Provide services for customers from more than 40 countries all over the world
- Provide products weight from 0.05KG to 16KG.
- GREFEE holds 7 Zinc die casting machines, with 7*24 working.
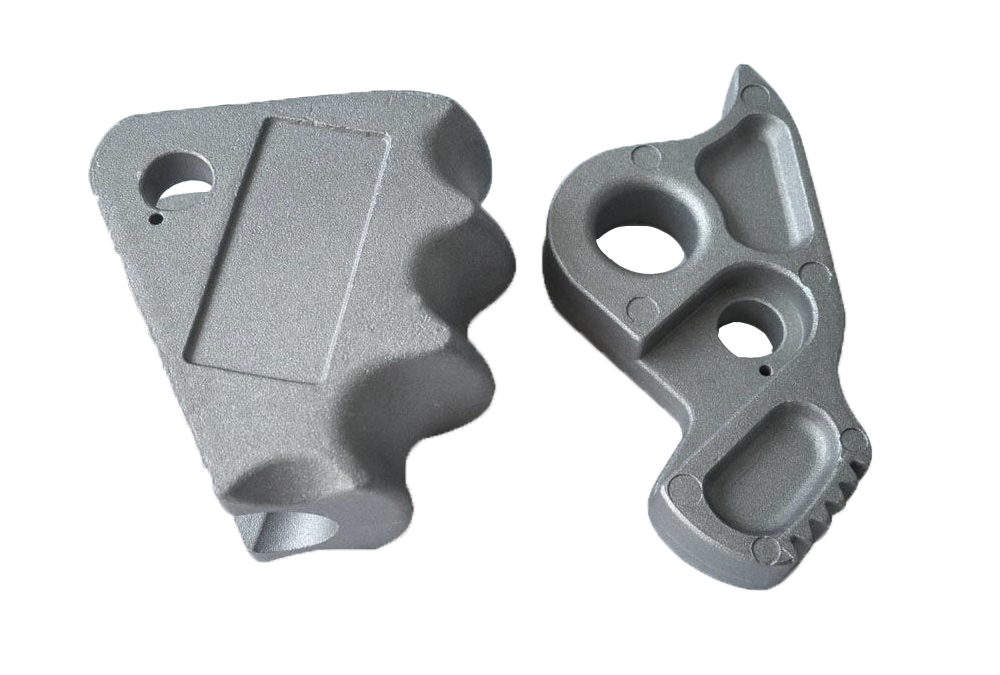
Die cast zinc alloy industry
GREFEE is a world-leading company of zinc alloy die casting parts manufacturers. We’ve produced tens of millions of die casted Zinc products,Without outsourcing, we produce in house. The fast lead time can meet 2 days. We have strict quality control from mould manufacturing to part finish, and are equipped with corresponding finish and inspection devices. Our professional technical experts are glad to solve all kinds of difficulties in customers’ products for free. Contact us now!Zinc alloy is widely used in many industries, such as: automobile, household appliances, mobile phone, electronics, beauty equipment, kitchen electrical products…etc.
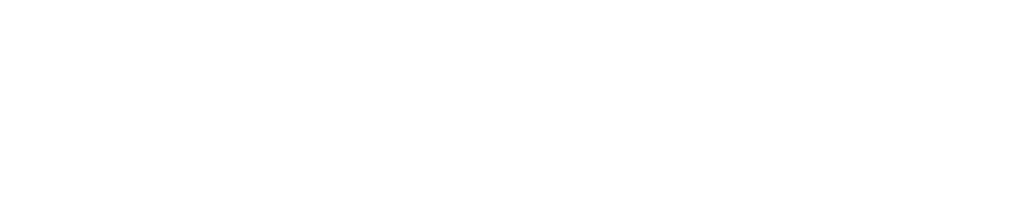
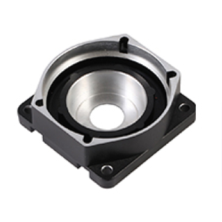
Motor Housing
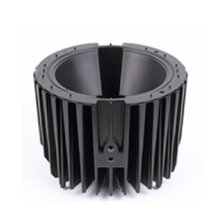
LED Housing
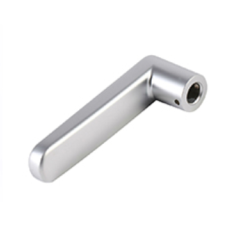
Handle
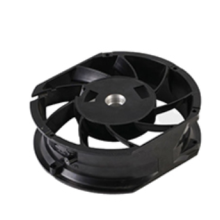
Exhaust Fan
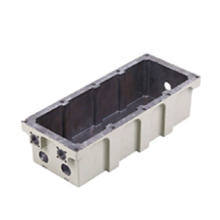
Enclosure
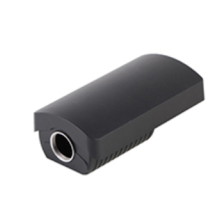
Camera Housing
Zinc alloy has low melting point, and it melts when temperature meets 400℃. Zinc alloy is easy to mold in die casting. Zinc alloy doesn’t adsorb iron in the process of melting. Zinc alloy has good properties of casting, electrical conductivity, thermal conductivity, dimensional accuracy, stability, thin-walled ability, corrosion resistance, recyclable, high intensity and great hardness, besides, Zinc alloy costs low of raw materials, which makes Zinc alloy become the idea choice of replacing machining, pressing, stamping and assembling components. In the process of die casting, can make many intricately shaped precise components get smooth surface after die casting. Long term used Zinc alloy are: ZA-27, Zamak-2, Zamak-3, Zamak-5, Zamak-7, ZA-8, ACuZinc-5 .
ZA 27
Compare to Zamak alloy series, ZA-27(Alloy of Zinc and Aluminum) contains obvious more composition of aluminum. 27 means approximate percentage of aluminum.
Zamak 2
#2 Zinc alloy(Kirksite or Zamak 2 (ASTM AC43A)) has the highest intensity and hardness among Zamak series.
Zamak 3
Zamak 3 (ASTM AG40A) is the most widely used Zinc alloy in North America, and it usually is the priority option in Zinc die casting for many reasons.
Zamak 5
Zamak 5 (ASTM AC41A) is the most widely used Zinc alloy in Europe.
Zamak 7
Zamak 7 (ASTM AG40B) is improved based on Zamak 3. It’s a high purity alloy, with low magnesium content and less impurities, which makes the liquidity, ductility and surface smoothness improved.
ZA 8
Compare to Zamak series alloy, ZA-8(alloy of Zinc and Aluminum) contains obvious more aluminum at 8.4%. It’s the only one ZA alloy for hot chamber die casting, which is the important factor should be taken into consideration in choosing materials for making components.
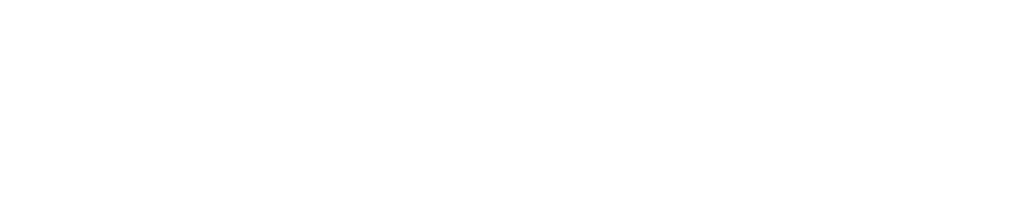
Mould for Zinc alloy die casting
Provide single cavity mould, multi-cavity mould, series mould, and also MUD mould base for small batch production of Zinc die casting.
Surface treatment
Strong coating, electronic coating, chrome plate, glossy and matte finish. Read more
Zinc alloy die casting
Make Zinc alloy die casted parts from small clips to giant electronic devices with complex geometry(like thin-walled geometry.)
Post Machining
GREFEE is equipped with advanced CNC machining center, so we can do post CNC machining for dimensions require strict tolerance, to make specific components.
Die casting
GREFEE is the most professional company in Zinc die casting
As one of the best manufacturer of Zinc die casting in China, GREFEE provides one-stop service for custom Zinc die casted parts from engineering, mould making , Zinc die casting production, post finishing machining and surface treatment. We can provide our customers prototypes for Zinc die casting production, small batch production of Zinc die casting, and massive production of Zinc die casting. We’re really good at it!
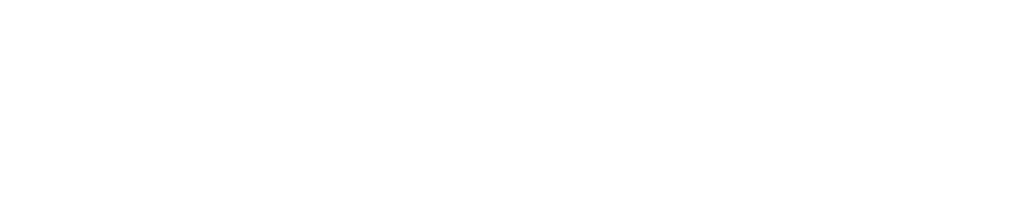
Small batch production of prototype zinc die casting
GREFEE provides our customers services for small batch Zinc die casting and Zinc die casted products. We help you get high quality Zinc die casted products and low down the mould cost mainly by 3 methods, and they are:
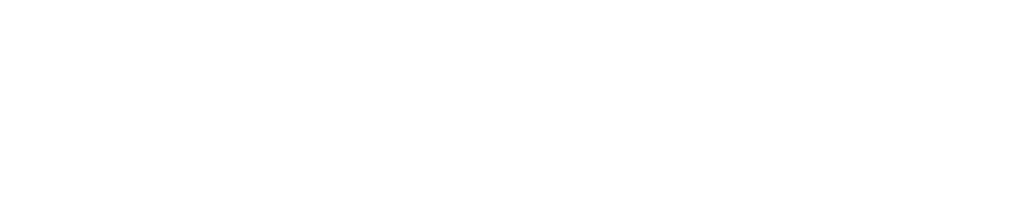
Zinc alloy die casting mold
MUD mould base, we called female die. Female due suits for the low-volume production as it is based on modularization and can convert efficiently during process. It also saves time and cost because one mud mold base can operate two or two molds.MUD mould base belongs to GREFEE. We create a series of MUD mould base storage and prepare for coming projects. MUD mould bases are free of charge.
Family mould
Our multi cavity mold can produce parts share similarities in material and size, suiting for low-volume production. Our capacity can allow us to produce sophisticated zinc die cased parts in only one cycle. Family mould is a good choice for injection molding and die casting because it cost-effective in not only mold production but also die casting production.
Interchangeable cutter
We receive a 100-unit order from a customer who requested a small size 3-version zinc die casted parts with same outline and diverse knots for him. We suggest him to try the interchangeable insert, that is a mold consists with 3 different inserts which are geometrically different but quick and easy to assemble. After cast one version, we then replaced the inserts for another version.
GREFEE provides OEM service. If you have die casting projects from small to large batch of zinc die casted parts, please send your inquiry to info@grefeemold.com today, and our sales engineers will get quotation back to you as soon as possible.
Common problem
- Property
- Characteristic
- Differences in technology
- Differences in mechanical properties
- Difference in material composition
- Advantages and disadvantages of Zinc alloy:
- Advantages and disadvantages of Aluminum alloy:
- Electroplating is good for improving the beauty, density and corrosion resistance for die casted Zinc parts. Materials are commonly used for electroplating are: Nickel, Tin, Copper, Silver, and Gold. Before electroplate. Must check carefully to confirm whether the part surface is fine for electroplating. Parts are not suitable for electroplating if have defects such as loose, racks, air bubbles, cold lines, pinholes…etc.Other finish for parts such as polish and smooth need completed before electroplating, so it’s better to design even product structure and avoid great sags and crests, large planes and sharp edges in product designing and mould designing, which is easy for polishing parts.
- Painting can be used for decorations, protection, and signs. It can partially hide some defects on surface of die casted Zinc parts, to help products achieve better performance. In painting, the concentration, quantity should strictly follow operation standards to avoid defects such as orange grains, pinholes, matte, paint gathering, paint throwing…etc.
- Chemical film forming treatment,Chrome-plating can improve the corrosion resistance of die casted Zinc parts and add beauty on part surface. Chrome-plating forms a protection layer on part surface, which makes die casted Zinc parts more easier to be painted and colored.
- Electrostatic painting also can form a protection layer for die casted Zinc parts, and make parts more smooth, beautiful and better performance. It can also improve the property of corrosion resistance. Electrostatic painting process needs strictly follow the operating standards, must check devices carefully as required before painting, and need choose the best appropriate hanging locations, adjust the moving speed of die casted parts, strictly control the temperature, paint viscosity and amount, to make sure that each part is painted evenly.
- Dimensional accuracy. Whether the mould can die cast Zinc parts within required tolerances.
- Die casting production efficiency. It means the time for one part die casted, the shorter time takes, the better quality and higher efficiency mould is.
- Mould stability. Whether the Zinc die casting mould can keep casting ok parts, and keep stable and high efficient for long term, besides, not easy to damage.
- Long lifetime die casting mould is surely the best financial return to customers.
- Runners design of die casting mould. Die casted parts don’t have defects of flow marks or cracks.
- Whether it is reasonable for die casting mould designing. It covers reasonable mould structures, reasonable gate locations, and die casting mould intensity as required. It also means reasonable arrangement of cooling runners of die casting mould, which is good for Zinc parts demold from die casting mould, and parts not stick to the mould. All of these requires years of experience in mould designing. GREFEE has several skilled mould designers who can design die casting mould with fast speed, lead time of mould making 10-15 days, seldom problems and quick processing.