Difference between shot blasting and sand blasting, which one?

Posted on : June 9, 2022 By GREFEE
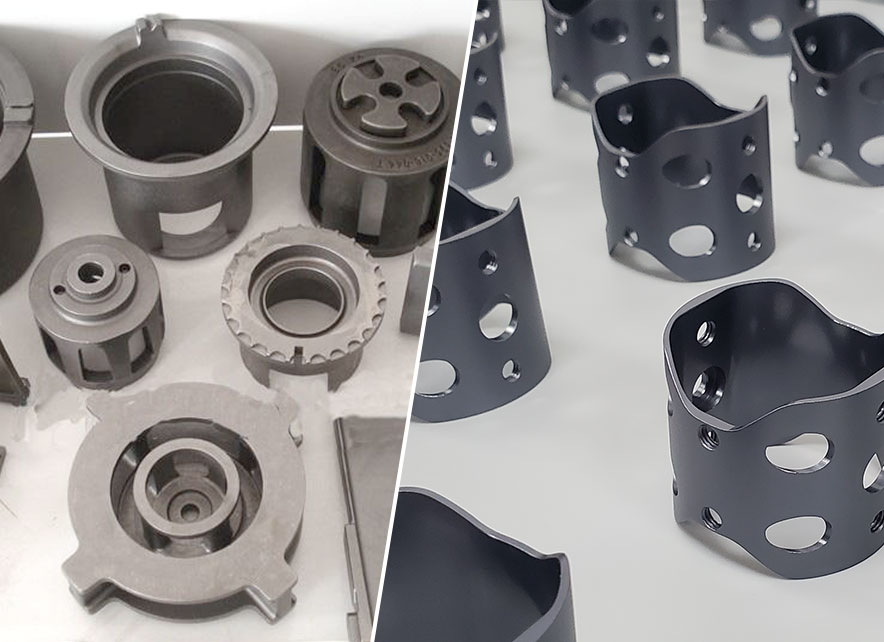
Shot blasting uses the high-speed rotating impeller to throw the small steel shot or small iron shot to knock the part surface quickly to remove the oxide layer of the parts. Meanwhile, the lattice of the surface will distort when the steel shot or iron shot, which increases the stiffness. Shot blasting is often used for casting surface cleaning and part surface strengthening.
Generally, shot blasting is used for regular shapes. Several ramming heads work together, up and down, right and left, which is high efficiency and less pollution. In the mechanical and shipbuilding industry, shot blasting and sand blazing are widely used, too. No matter whether it is sandblasting or shot blasting, we can use the compressed air mode. Of course, it is not necessary to adopt high rotating impellers in shot blasting. In the shipbuilding industry, shot blasting is mostly used in the pre-treatment of steel plates (remove rust before assembly and coating). Sandblasting usually can be seen in the formed parts or segments. Its function is to remove the old paint or rust on the blank and repaint. In the mechanical processing industry, shot blasting and sandblasting increase the adhesion of material coating paint and its appearance.
The cleaning of castings not only relies on shot blasting. For the large-scale part, we should clean the sand first with the roller, which is to place the part in the roller for rolling after the riser of the casting is cut off. Due to the collision in the roller, the sand on the surface will be cleaned before the shot blasting.
The shot size used for shot blasting is 1.5mm. Researches show that it is easier than compressive stress when there is tensile stress on the surface in terms of damages. When the surface is under compressive stress, the fatigue life of the material increases significantly. Thus, shot blasting is a good choice for shafts or parts that are likely to have fatigue broken as it can form a surface compressive press and increase the service life. Besides, the metal material is also very sensitive to stretching, resulting in the tensile strength of the material being much lower than the compressive strength. This is also why metal materials use tensile strength (yielding, tensile) to stand for the material property.
The working surface of the steel plate in the automotive that we take everyday is strengthened by the shot blasting, which can rise the fatigue resistance strength remarkably.
Shot blasting works by the motor drives the impeller body to rotate. Due to the centrifugal force, balls with a diameter of 0.2~3.0 (cast shot, cut shot, stainless steel shot, etc) are thrown on the workpiece surface, which renders it reach a certain roughness level to improve the appearance to change the welding tensile stress into the compressive stress, which extends the service life effectively. It is almost used in most fields in the mechanical industry, shipbuilding/automotive components/steel structure/mechanical components/steel plate/pipes, etc. Sandblasting uses compressed air to spray the sand with a diameter of 40~120 or balls at 0.1~2.0 with the same effect. Different sizes of the balls bring various treatment effects. Key point: sandblasting can also be used for strengthening.
What is sandblasting? Sandblasting uses compressed air to blow out the quartz sand at a great lick, which is one of the surface cleaning treatment methods. In factories, this is also called sand blowing. It can remove the rust and the oil in the meantime. For painting, it is highly useful and is commonly used for surface rust removal. Besides, it is also adopted for the part surface finish (the small-scale liquid sandblaster in the market is used for this. The sand is usually corundum with a medium like water.). For the steel structure, we should use the high-strength bolt to connect due to its advance. Since the high strength connection utilizes the friction between the bonding surface to transmit the force, the requirement for the quality of the bonding surface is high. In this situation, we must use sandblasting to process the binding surface.
Sand blasting used for complex shapes are easy for manual rust removing but is not efficient. The poor site environment and uneven rust removing outcome will lead to many quality issues.
Sandblasting used for complex shapes is easy for manual rust removal but low efficiency. The poor site environment and uneven rust removal outcome will lead to many quality issues.
Shot blasting and sandblasting services can all clean the dirt for the workpiece, aiming for the preparation for the follow-up procedure. It needs to ensure the roughness requirements of the next step and the consistency of the surface. Shot blasting has a remarkable strengthening effect on the workpiece, whereas sandblasting is not that obvious. Generally, shot blasting is the small iron ball, and sandblasting is quartz sand. According to the requirements, there is a mesh number of crudeness or fineness.
Advantage and application ranges of the sand blasting
1. No hydrogen embrittlement
The rust composition of the steel part surface is mainly Fe2O3. The oxide skin of steel after heat treatment is mainly Fe3O4. Methods that are often used for removing the rust and oxide skin include sandblasting and acid wash. The latter allows the hydrogen to penetrate the inside of the steel easier. Moreover, it increases internal stress and lowers plasticity. However, sandblasting does not generate hydrogen embrittlement. No matter it is high carbon steel, high strength steel, or the elastic copper components, stainless steel and aluminum sandblasting all can enhance the bonding force of the coating and oxide layer, which is remarkable in the aluminum oxide sandblasting
2. Casting coating enhancement
To reduce the mechanical processing and lower the cost, it uses a large quantity of zinc alloy castings and aluminum alloy castings to replace the iron and nonferrous metals in the treatments, like electroplating, sandblasting, and powder coating. As there might be flow marks, mottles, cold patterns, air holes, and welding lines, the painting will be affected significantly if they are not solved.
After an array of treatments, like chemical grease removal, surface sandblasting, galvanization, cyanide copper plating, neutral nickel plating, and zinc alloy castings have bright nickel plating or chrome plating with a 90% above electroplating pass rate.
Aluminum alloy castings can obtain good binding force and smooth coating after sandblasting and anodic oxidation.
3. Improve the surface roughness of workpiece
Sandblasting roughens the workpiece surface, so the workpiece surface roughness changes and generates pastel-colored satin. Steel and brass parts, after the fine sandblasting and oxidizing, will form a chemical black mottle layer. Steel and brass parts receive chromium plating, or nickel plating followed by chromium plating after sandblasting will form satin chromium. Glass after sandblasting can form the opaque frosting glass.
4. Repaired parts
In parts that are washed with acid, the eroded base metal results in an increase in brittleness due to the acid wash. One method that can adopt is to remove the unqualified coating by sandblasting, then carry out electroplating, oxidizing, and painting.
In addition to the chrome plating, all the single coatings can be removed by sandblasting. Parts in products are composed of brass-oxidized parts and aluminum alloy castings. The aluminum alloy coating needs to be removed but retain the oxidized black of brass without using the paint remover (since paint remover impacts the copper oxidation). Therefore, adopting local sandblasting to remove the paint is quite effective for the aluminum alloy castings’ repainting.
Advantage and application range of shot blasting treatment
1. Surface cleaning of casting
In die casting, shot blasting is effective for workpiece cleaning and surface defects cleaning. If there are air holes, slag holes, sand sticking, cold shut, peeling, and other problems, shot blasting plays an indispensable role in dealing with them. Crawler-type shot blasting machine works by high strength wear-resistant rubber track and manganese steel track loading-workpiece. It utilizes high-speed rotating impellers, stamping parts, gears, springs, and other components to clean the sand and remove the rust. Besides, it cleans the oxidized skin with surface strengthening. It is well particularly applicable to the cleaning and strengthening of parts that are collisions tolerable.
2. Surface cleaning of the colored metal castings
The surface cleaning of the colored metal castings must be processed by shot blasting with a sound effect, such as aluminum alloy surface cleaning and brass alloy surface cleaning. These two alloys need shot blasting to remove the oxide skin on parts. It also cleans the defects detection on the workplace surface. Shot blasting aims to remove the burrs on castings to enable the castings to surface quality of decoration with an ideal outcome. Crawler-type shot blasting machine works by high strength wear-resistant rubber track and manganese steel track loading-workpiece. It utilizes high-speed rotating impellers, stamping parts, gears, springs, and other components to clean the sand and remove the rust. Besides, it cleans the oxidized skin with surface strengthening. It is well particularly applicable to the cleaning and strengthening of parts that are collisions tolerable. With the shot blasting machine, shots at a diameter of 0.2~0.8 will be thrown to the workpiece surface to reach a certain level of roughness to optimize the appearance of parts or extends the service life by changing its compressive stress.
Try GREFEE now,for free
We keep your uploaded files confidential and secure.