How to select tools for CNC threads

Posted on : June 14, 2022 By GREFEE
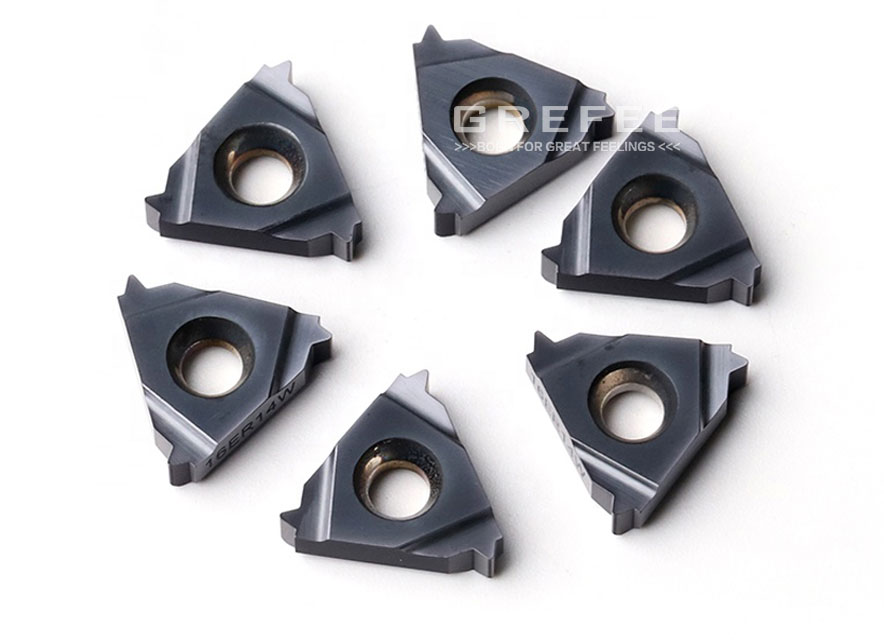
Threads are the most common methods to connect the mechanical parts, whereas the threads holes processing is machining often at the end of the whole production. Once the processing is unqualified, the part might be scrapped or re-processed. Thus, it has a high requirement for the safety of processing. Processing thread holes requires various tools. Commonly used tools include the thread turning tool, tap, extrusion tap, thread milling cutter, etc. How to select the correct processing tools? Tool selection is the processing selection. The tools used in each processing method are different. Typical processing methods for the thread holes include tapping, turning, extrusion forming, and thread milling. Now, let’s start with the pros and cons of each processing method and the use limitation. In the actual production, these processing method helps us to adopt which type of tools technologically and economically.
tapping
Tapping is a processing method with extensive applications in thread hole processing. It confirms the forming of threads by the geometrical shape of tools so it can work on ordinary lathes and special machines in production lines and processing centers without necessarily using a specific machine tool. Tapping starts with the tap rotating forward first for cutting and then reverse at the bottom of threads. When it leaves the parts, it is cut in a very narrow space, and then the scissel chip is voided. So, different processing conditions and materials lead to different tap types. Generally, tapping is often used in small diameter and mass production.
TurningTurning
Turning processed threads works by using the indexable blade to process the turning. Triangle thread which is seen often in daily life, the shape of the cutting part of the thread tool should in align with the axial section of threads. When turning, to obtain a correct thread, the turning tool will move one lead longitudinally per revolution of the workpiece (single head thread, lead = pitch). Three commonly used methods of turning triangle thread:
A .Straight thread cutting
When processing the turning thread, inspect the workpiece during the trial cutting. Once the thread distance meets the requirement, feeding radially perpendicular to the workpiece axis, repeat many times until the thread is turned. The thread form produced by this method is qualified.Two blades of the turning tools are cutting in the meantime, and the chip is hard to remove. Since the high force, the turning tools are worn. The scissel chip will scratch the thread surface.
B. oblique feed threading.
Pitch of the workpiece that is over 3mm often being processed with oblique feed threading. Oblique feed threading is the turning tools feed radially along the side of the thread profile and do axial feed simultaneously. After several times of feeding, the thread processing is completed. Finally, using the straight cutting method to ensure the accuracy of the thread form.
C .stagger cutting method.
On the ordinary lathes, this method uses the horizontal carriage scale to control the threading tool to make it feed perpendicularly and then uses the small carriage scale to control the feeding right and left. When the threads are almost finished, use the bolts or the thread gauge to check whether the thread size and processing accuracy are qualified or not. This method is widely used due to its convenience.
The turning processing threads generally adopts large diameter holes and the workpiece can be clamped on the lathe firmly to rotate and process.
extrusion processing
Extrusion processing is chip-free processing. The processing is as same as tapping. Screw the extrusion tapping into the pre-drilled holes to push the material out radially and axially and form a unique thread form profile. The thread extrusion forming suits material with good plasticity forming. The material range is small, so its fracture elongation rate is often over 7%. However, the highest tensile strength is less than 1300N/MM, usually used in aluminum alloy processing.
Thread milling
Thread milling progress is shown as pics below. The thread milling cutter first goes down to the bottom of the thread holes, then gets close to the part by the helical interpolation. After rotating 360 degrees along the thread holes, it will increase by a pitch at the Z-axis direction before leaving the workpiece. The torque is small when the thread milling cutters are processing, which improves the safety level. Besides, it also has an extensive application property that can process different kinds of material. So, when the pitch is equal, one tool can produce different thread diameters or threads within the tolerance range. The disadvantage is that the lathe must be 3-coordinate CNC machine tools. Compared to tapping, its efficiency is lower, and the cost of tools is high. Therefore, it is often used for processing the large-diameter thread holes of low volume production
We just mentioned that tap is the tool used most so far to process the small diameter threaded holes. What’s more, tapping is a complex process, and it will come across many issues during production. Common problems of tapping include cracking, tipping, wear, etc. It breaks along the whole cross-section of tapping, and tipping is the cutting edge chipping, whereas the wear of tappings refers to the tapping, and the die has not been used for long. The cutting edge has already been worn off and causes the tooth size to become smaller and cannot be used. The life for these three invalid taps is all less than the normal service life. After finding out these issues, we can analyze them from the below aspects:
1.Lathe
Check whether the lathe operation is normal or not, whether the primary axis beating is too large, whether the primary axis of the lathe and the axis of bottom holes are the same, whether the processing procedures are correct or not, etc.
2.Workpiece material
Check whether the material strength of workpiece is too high or not, whether the material quality is stable or not, whether there are air holes, residues, etc.
3.Diameter and depth of the thread bottom holes
Inspect the diameter of the threaded bottom holes. If the diameter is small, its bottom can touch the workpiece when the tap cutting and cause the tap to break. The diameter of thread bottom holes is marked in the samples of tap or can calculate as the diameter of bottom holes with this formula (bottom hole diameter = thread diameter — pitch). For the extrusion tapping, the diameter of the thread bottom hole is different from the cutting taps, but still can be obtained from the formula: bottom hole diameter = thread diameter — pitch/2).
For blind holes, we also need to consider the depth of the holes. Since the front end of the tap has several cutting tooth and their diameters are small, they cannot be regarded as qualified threads. Thus, the depth of the bottom hole also should be based on the depth of the cutting tooth and the size of the corner at the front end of the tap. In the production, there is also the case that the bottom hole is not deep enough, so the front of the tap broke when touching the bottom.
4.Type of tap
As we mentioned before, for different processing conditions and materials, the type of tap you select will be changed, too. So, for the through holes and blind holes, the cutting tap will be selected accordingly. Material of long chip, like steel, should choose straight groove tap in the through-holes. The chip will be voided downward. For blind holes, a spiral flute tap is a good choice. The chip goes upward. Material of short chip, such as cast iron, the iron scurf is the flake that can be contained in the slag slot. Thus, the straight groove tap applies to blind holes and through holes. Another condition is that the chip generated by the Tap LH is separated. This tap is suitable for situations when there is insufficient space for chip removal because the workpiece is close to the frock.
We also can often see the spiral flute tap in the processing of though holes, which is an incorrect method for three reasons: first, the spiral flute tap is the upward chip removal structure. To obtain this, it has a complex structure. Moreover, the rigidity is poor, and the chip transmission stroke is long, so it is easy to be stuck during the transmission process or lead to tipping or cracking. Second, the number of cutting teeth of the two types of the tap is different, which is 2-3 for the spiral flute tap and 3-5 for the straight groove tap. The service life of the tapping extends with the increase in the number of cutting tooth. Third, the spiral flute tap is more expensive than the straight groove tapping and is not cost-effective.
On the other hand, in the cutting taps, different materials should select ones with different groove types. There are also different angles for taps, such as front angle, rear angle, guide angle, blade angle, etc. The design of these angels is based on the properties of various materials. For instance, the steel part and casting part. Due to the long chip, the front angle of the tap will be bigger, whereas the front angle of casting iron is small, even zero, because the iron scurf is flakes. The tool company will recommend different taps according to the material, too. The tap of processing steel parts, aluminum alloy, cast iron, stainless steel, and other common materials will also be separated by different color rings on the handle.
5. cutting parameters
Cutting parameters are essential. Different types of taps, processing conditions and materials determine the parameters you choose, such as the linear velocity of the high-speed steel wiretaps and hard alloy taps under the same condition varies significantly. The rotating velocity has a specific range. Normally, the linear velocity of a high-speed steel wire tap is within 20M/MIN (tap feeding is fixed, which is pitch). Too fast or slow will lead to an invalid tap. Appropriate cutting parameters guarantee a high production rate and long service life.
6. cooling and lubricate
As mentioned before, the tap works in a very narrow space and removes the chip. During this process, it will generate a large quantity of heat. Thus, cooling and lubricating are both essential. For materials with high toughness, we can increase the concentration of cooling agents or utilize oil cooling agents.
MORE BOLG
Insert mold in injection mold service
What are advantages and disadvantages of Zinc alloy and Aluminum alloy?
Inspection standards for injection molded partappearance
How to judge the quality of your plastic products?
Inspection standards for CNC machining
To ensure that your products are 100% qualified
Categories
Try GREFEE now,for free
We keep your uploaded files confidential and secure.