Analysis and Solution of Internal Stress of Injection Molded Parts

Posted on : Oct 13 , 2022 By GREFEE
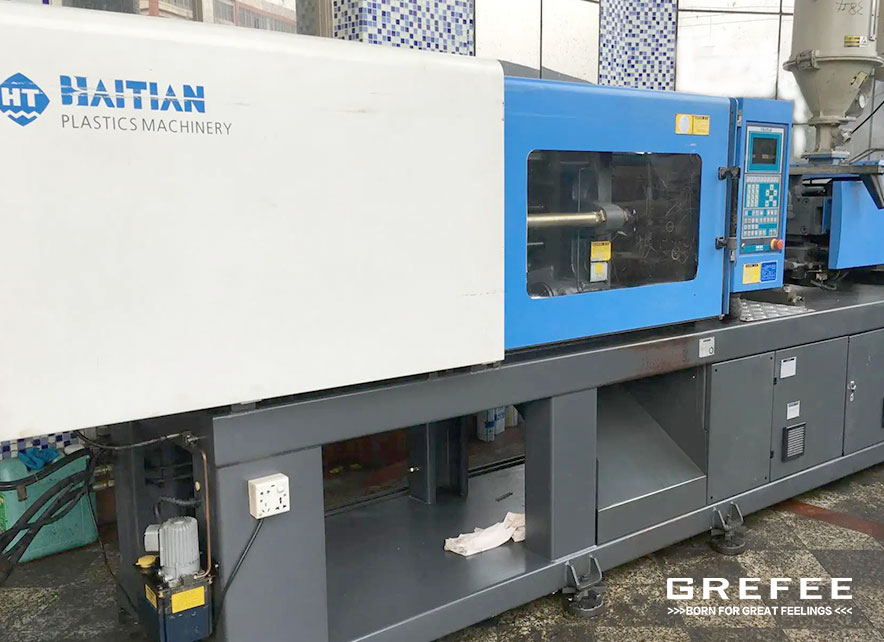
Stress refers to the force acting on the object per unit area, which emphasizes the stress condition inside the objects. Generally, under the action of external stress, the inside of object will produce stress to agents the external force. When the object is not subject to external force, the stress exist inside is called the internal stress, which is caused by the uneven plastic deformation occurs in various parts of the object.
According to the scope of internal stress action, it can be divided into three categories:
Internal stress (macro internal stress)
The macro internal stress is caused by the uneven deformation of each part of the material.
2. Internal stress (micro internal stress)
The micro internal stress is caused by the uneven deformation between each grain or sub grain of the object (most of the solid matter are grains in the natural environment).
3. Internal stress (lattice distortion stress)
The lattice distortion stress is caused by some atoms from grains deviate from their equilibrium position due to the lattice distortion, which is the main internal stress in the deformed object (damaged objects).
The plastic internal stress refers to the plastic is affected by the cooling shrinkage and orientation of macromolecular chain during the melting process.
The essence of internal stress is a kind of unbalanced phenomenon generated during the melting process of macromolecular chain. This unbalanced phenomenon cannot get back to normal and balanced phenomenon which is matchable to the environment conditions during the cooling and curing. The essence of this is a kind of reversible hyperelastic deformation, while frozen hyperelastic deformation can be stored into the plastic products in the form of energy. Under suitable conditions, this forced and unstable conformation will be transformed into a free and stable conformation, and the potential energy will be transformed into kinetic energy and released.
When the force and intertwining force between macromolecular chain cannot bear this kinetic energy, the balance between the internal stress will be broken, then the plastic products will generate internal stress and cause break, warpage, and deformation, etc.
Almost all plastic products will have internal stress exist to different extent, especially evident among the plastic injection products. The existent of internal stress not only leads to the warpage, break and deformation during the storage and using process, but also affect the mechanical performance, optical performance, electrical performance and appearance quality of products. Thus, the cause for internal stress and solution of reducing internal stress must be found to large reduces the internal stress, and makes it to be distributed evenly on the products to avoid the stress being concentrated. So, the mechanical and thermal properties can be improved.
Cause
There are many things could lead to the generation of internal stress, like the plastic melt is subjected to strong shearing during processing, orientation and crystallization in processing. The cooling speed of each area cannot achieve consistent. Inhomogeneous melt plasticization and difficult demoulding of products and other factors, all could cause internal stress. According to the causes of internal stress, the internal stress can be divided into the following categories
(1) Orientation internal stress
The orientation internal stress refers to an internal stress generated when the macromolecular chains are arranged along the flow direction and the directional conformation is frozen when the plastic melts in the process of flow filling and pressure maintaining and feeding. The detailed process of the generation of the orientation internal stress is that the melt near the flow passage wall has a high cooling rate, which causes the viscosity of the outer layer melt to increase, so that the laminar flow rate of the melt in the center of the cavity is much higher than the surface flow rate, resulting in the orientation along the flow direction caused by the internal layers of the melt are subject to shear stress.
The oriented macromolecular chains are frozen in plastic products means the existence of unrelaxed reversible high elastic deformation. Thus, the orientation stress is the transient process of macromolecular chain from the orientation conformation tries to transition to the internal force of the non orientation conformation. The orientation stress can be eliminated or reduced with the thermal treatment.
The distribution of orientation internal stress of plastic parts is getting smaller from the surface of products to the internal layer, and changes in parabola.
(2) Cooling internal stress
Cooling internal stress is the caused due to the uneven shrinkage during the cooling formation when the plastic products are in the melting process, especially for the thick wall plastic products. The cooling, solidification shrinkage of outer layer of products happen first, but the internal slyer is still hot melt, so the core layer will limit the shrinkage of the surface layer, resulting in the core layer under the compressive stress state, while the surface layer is in tensile stress state.
The distribution of cooling internal stress of plastic products is getting higher from the surface of products to the inner layer, and changes in the parabola.
In addition, the plastic products with metal inserts will produce internal stress with uneven shrinkage because of the big difference of coefficient of thermal expansion of metal and plastic.
Besides, there are also the following internal stress. For crystalline plastic products, the difference of crystal structure and crystallinity of each part will also produce internal stress. Other than that, there are also the internal stress of the configuration, the internal stress of the demoulding etc, but the proportion of the internal stress is small.
Factors affecting the internal stress of plastics:
The higher the stiffness of molecular chains, the higher the viscosity of melts, the poorer the polymer molecular chain activity. Thus, the internal stress is easily to be produced when the recovery of reversible high elastic deformation is poor. For instance, some molecular chains contain the internal stress of the corresponding products of benzene ring polymers and have high internal stress, such as PC, PPO, PPS, etc.
(2) Polarity of molecular chain
The larger the polarity of moleculr chain, the larger the force of intermolecular attraction. Thus, it is more difficult to make molecules move with each other, and the degree of reversible elastic deformation is reduced, resulting in the increase of residual stress. For instance, some molecular chains have high internal stress when they contain plastic varieties with polar groups such as carbonyl, ester and cyano.
(3) Steric effect of substituent groups
The larger the volume of substituent group of macromolecular side group, the larger the residual internal stress caused by hindering free movement of macromolecular chain is. For instance, the larger the phenyl volume of polystyrene substituent group, the larger the internal stress of polystyrene products is.
Order of internal stress of several common polymers:
PPO>PSF>PC>ABS>PA6>PP>HDPE
Reduction and dispersion of plastic internal stress:
(1) Raw material formula design
Resins with large molecular weight and narrow molecular weight distribution
Resin with low impurity content
The impurities in polymer is the concentration of stress, which lowers the original strength of the plastic. Therefore, we should minimize the impurity content is reduced to a minimum.
Blending modification
The resin is likely to crack due to the stress, and is suitable for mixing with other resin, which will lower the extent of internal stress.
For instance, mixing approximate amount of PS in the PC will make the internal stress distribute along the ball side and prevent the spread of cracks because the PC is dispersed in PC continuous phase in nearly bead shape, so the internal stress will be reduced. In addition, adding approximate amount of PE into the PC will also do because the outer edge of PE pellets can form a closed cavitation zone.
modification enhancement
Using the reinforced fiber for reinforcement modification is also a method to reduce the internal stress due to high content of macromolecular chains in the fiber entangles, thus the improvement of stress cracking ability is necessary. For example, the stress cracking resistance of 30% GFPC is 6 times higher than that of pure PC.
Nucleation modification
Adding approximate amount of nucleating agent to crystalline plastics can form many small spherulites in its products, which can reduce internal stress and disperse.
(2) Control of forming and processing conditions
In the molding process of plastic products, any molding factor that can reduce the orientation of polymer molecules can reduce the orientation stress. All process conditions that can make the polymer in the product cool uniformly can reduce the internal stress of cooling. All the processing methods that are beneficial to the demoulding of plastic products can reduce the internal stress of demoulding.
The processing conditions that have a great impact on the internal stress are mainly as follows:
1.temperature of barrel
High temperature of barrel is conducive to reduce the orientation stress because not only the melt is plasticized evenly, but also the viscosity is reduced, and the flowability is increased under high temperature of barrel. When the melt is filling the mold cavity, the orientation stress is small because the molecular orientation effect is small. While under low temperature of barrel, the viscosity is high and the molecular orientation is large during the mold filling. The residual stress is large after cooling and forming.
However, it is not always good with high temperature of barrel. High temperature will cause uneven cooling and cause deformation after mold releasing. Even with reduced orientation stress, the cooling stress and demoulding stress increase.
2.Mold temperature
The mold temperature affects the orientation stress and cooling internal stress significantly. Low mold temperature will accelerate the cooling and cause the uneven shrinkage, then to increase the cooling internal stress.
On the other hand, if the mold temperature is low, the temperature will decrease sharply once the melt entered into the mold. In the meantime, the viscosity of melt increases sharply, resulting in the mold filling with high viscosity and generate orientation stress to a large extent.
The mold temperature affects crystalize of crystal significantly. Higher the mold temperature can help the grains to be stacked tightly, reduces or eliminates the defects inside the grains to reduce the internal stress.
In addition, there are different requirements in temperature for plastic products with different thickness. Thick wall products requires high mold temperature.
3.Injection pressure
The higher the injection pressure is, the greater the shearing force is in the process of filling the melt, and the greater the chance of generating the orientation stress is. Therefore, to reduce the orientation stress and eliminate the demoulding stress, the injection pressure should be reduced.
4.holding pressure
The influence of pressure holding on the internal stress in plastic products outweighs that of injection pressure. During the stage, as the decrease of temperature of melt, the viscosity of melt will increase sharply. If high pressure applied at this moment, it will lead to the forced orientation of molecular chains to generate larger orientation stress.
5.Injection speed
The higher the injection speed, the easier the increase of the orientation degress of molecular chains. Thus, causing high orientation stress. However, if the injection speed is low, the plastic melt may layer successively to form melting trace and stress concentration line when it enters into the mold cavity and easy to cause stress cracking. Therefore, it is best to adopt variable speed injection, and the mold filling is completed when the speed gradually decreases.
6.Time of pressure holding
The longer the time of pressure holding, the greater the shearing force of plastic melt to generate larger plastic formation and freeze more orientation stress. Thus, the orientation stress will increase as the prolong of time of pressure holding and increase of replenishment amount.
7.Die opening residual pressure
Properly adjusts the injection pressure and time of holding pressure to make the residual pressure be close to the atmosphere pressure when opening the mold to avoid the generation larger mold releasing internal stress.
(3) Heat treatment of plastic products
The heat treatment of plastic products refers to the removal of internal stress by holding the molded products at a certain temperature for a period of time. It is extremely effective to eliminate the orientation stress in plastic products.
Heat treatment is necessary for injection molded parts with high rigidity of polymer molecular chain and high glass transition temperature, parts with large wall thickness and metal inserts, parts with wide temperature range and high dimensional accuracy requirements, and parts with large internal stress but not easy to self eliminate and machined parts.
Heat treatment can transform the polymer molecules from the unbalanced conformation to the balanced conformation to make the forced frozen unstable high elastic deformation to obtain energy and conduct thermal relaxation, which are useful in reducing the internal stress. The commonly used heat treatment temperature is 10-20 ℃ higher than the working temperature of the parts or 5-10 ℃ lower than the thermal deformation temperature.
The time of heat treat is determined by the plastic type, part thickness, heat treatment temperature and injection molding conditions. 1-2 hours heat treatment is enough for parts with normal thickness. As the increase of thickness, the time will be extended. Increasing the temperature of heat treatment and extend the time for heat treatment will obtain similar results. However, the effect is more obvious.
In heat treatment, putting the parts into the liquid media such as water, glycerin, mineral oil, ethylene glycol and liquid paraffin, or heat to the specified temperature in the air circulation oven, and stay at the temperature for a certain time, then let it cool naturally to the room temperature. Based on the experiment, it is helpful in reducing the internal stress, improve the performance of parts with evident effect if the parts have heat treatment immediately after demoulding. In addition, increasing the mold temperature will also extend the cooling time of parts. Thermal insulation treatment after demoulding has the same effect as heat treatment.
Even though heat treatment is one of the effective methods to reduce the internal stress, it can only reduce the internal stress to the allowable range of the working conditions of parts, and it is difficult to completely eliminate the internal stress. When the PC products are heat-treated for a long time, the PC molecular chains may be rearranged orderly, or even crystallized, thus reducing the impact toughness and notch impact strength. Therefore, heat treatment should not be taken as the only measure to reduce the internal stress of parts.
(4) Design of plastic products
1.Shape and dimensions of plastic products
When designing the plastic products, to effectively disperse the internal stress, we should follow the principles: the approach of parts should be consistent to avoid the sharp corners, right angles, gaps and sudden enlargement or contraction.
The edge of plastic products should be designed to fillet, and the radius of the inner fillet should be larger than the thickness of the thinner of two adjacent walls by more than 70%. The radius of outer fillet should be determined by the shapes of products.
For areas with large thickness difference, the cooling internal stress and orientation stress are easy to be generated due to the difference of cooling speed. Thus, even thinkness is necessary because uneven thickness will need to be transit gradually.
2.Reasonable design of metal inserts
The thermal expansion coefficients of plastic and metal differ by 5~10 times. Thus, the shrinkage for both in the plastic parts with metal inserts are different. The shrinkage in plastic is large so it can tightly hold the metal insert and bear the pressure in the inner layer of plastic around the insert, while the outer layer is influenced by the tensile stress, resulting in the concentration of stress.
When designing inserts, the following points should be paid attention to reduce or eliminate internal stress.
a. Use plastic parts as inserts as far as possible.
b. Try to use metal with small difference in thermal expansion, coefficient from plastic as the insert materials, such as aluminum, aluminum alloy and copper.
c.Apply a lyer of rubber or polyurethane elastic buffer layer on the metal insert to ensure the coating does not melt during molding, which reduces the shrinkage difference between the two.
D. Carry out surface degreasing treatment to metal inserts, can prevent the cracking due the grease.
e. Pre-heat the metal inserts appropriately.
f. The thickness of plastic around the metal inserts should be sufficient, for instance, the diameter of insert is D, the plastic thickness around inserts is h, then the plastic thickness of aluminum inserts h≥0.8D. For copper inserts, the plastic thickness h≥0.9 D.
g. The metal inserts should be designed into the round shape with delicate knurling pattern.
3.Design of upper hole of plastic products
The shape, number and position of holes on plastic products affect the concentration of internal stress significantly.
To avoid the stress cracking, the prismatic, rectangular, square, or polygonal holes on the plastic products should be avoided. Round holes are recommended. The effect of the oval hole is the best, and the long axis of it should be parralled to the direction of action of external force, such as round holes. Round holes with equal diameter can be added, and the central connecting line of the two adjacent round holes can be parallel to the direction of the external force, so that the effect similar to the elliptical hole can be achieved.
(5) Design of Plastic Mold
When designing the plastic molds, the pouring system and cooling system are essentials to the internal stress. The following points should be noted in designing.
1.Size of gate
If the size of gate is too large, it may take longer time to hold the pressure and feed. When the temperature goes down, the flow of the feeding will freeze more orientation stress, especially for the replenishment of cold materials, which will cause larger internal stress around the gates.
Reducing the gate size appropriately can shorten the time for pressure holing and feeding, reducing the pressure insider the mold when the gate is frozen to lower the orientation stress. However, if the gate is too small, it will cause the delay of mold filling and cause underfeeding of products.
2.Position of gate
The position of gate determines the flow condition, length of flow, and direction of flow of the plastic melt in the mold cavity, which can reduce the injection pressure, holing pressure and time for holding pressure, which is conducive to lower the orientation stress. When the gate is set at the thin wall area, adding the thickness of gate appropriately to lower the orientation stress around the gates.
The longer the flow distance of melt in the mold cavity, the greater the possibility of generating the orientation stress. So, for plastic parts with thick wall, long flow distance and large area, multiple gates should be distributed, so the orientation stress can be effectively reduced to prevent the happening of warpage and deformation.
In addition, since the areas around gates are likely to generte internal stress, these areas can be designed into the lug gate, which can keep the internal stress in the lug gates. After demanding, cutting off the lug gates with large internal stress can reduce the internal stress in the plastic products.
3.Design of runner
Short and thick runners are helfpul in reducing the pressure loss and temperature loss of melt. Reducing the injection pressure and cooling speed correspondingly will reduce the orientation stress and cooling stress.
4.Design of cooling system
The distribution of cooling pipes should be proper to make sure an even and slow cooling effect in the areas around the gates, far from the gates, as well as thick and thin wall areas to lower the internal stress.
5.Design of ejection system
When designing appropriate demoulding taper, the high core finish and larger ejection area are required to avoid the generation of demolding stress.
The way to check the stress of plastic parts is the solvent impregnation, which means putting the parts into the glacial acetic acid for 30s and dry it in the air, the white spot is the stress concentration spot. When the stress is too high, the plastic will crack. The more the cracks, the higher the stress. Additionally, the crack will be more obvious and deep when it is soaked into the 2rain, or the glacial acetic acid impregnation can be replaced by the 1:1 mixture of methyl ethyl ketone and acetone for 15s.
The methods to eliminate the stress include heating (annealing), which means baking the parts under 65~70℃ for 4hrs. Small parts can be soaked into the 25% acetone aqueous solution for 30mins to eliminate the stress. When the stress is too high, both methods are non-effective and the parts cannot be electroplated.
MORE BOLG
Insert mold in injection mold service
What are advantages and disadvantages of Zinc alloy and Aluminum alloy?
Inspection standards for injection molded partappearance
How to judge the quality of your plastic products?
Inspection standards for CNC machining
To ensure that your products are 100% qualified
Categories
Try GREFEE now,for free
We keep your uploaded files confidential and secure.