Tips for the appearance of injection molded part inspecting
The quality evaluation of you plastic products.
Posted on : January 11, 2022 By GREFEE
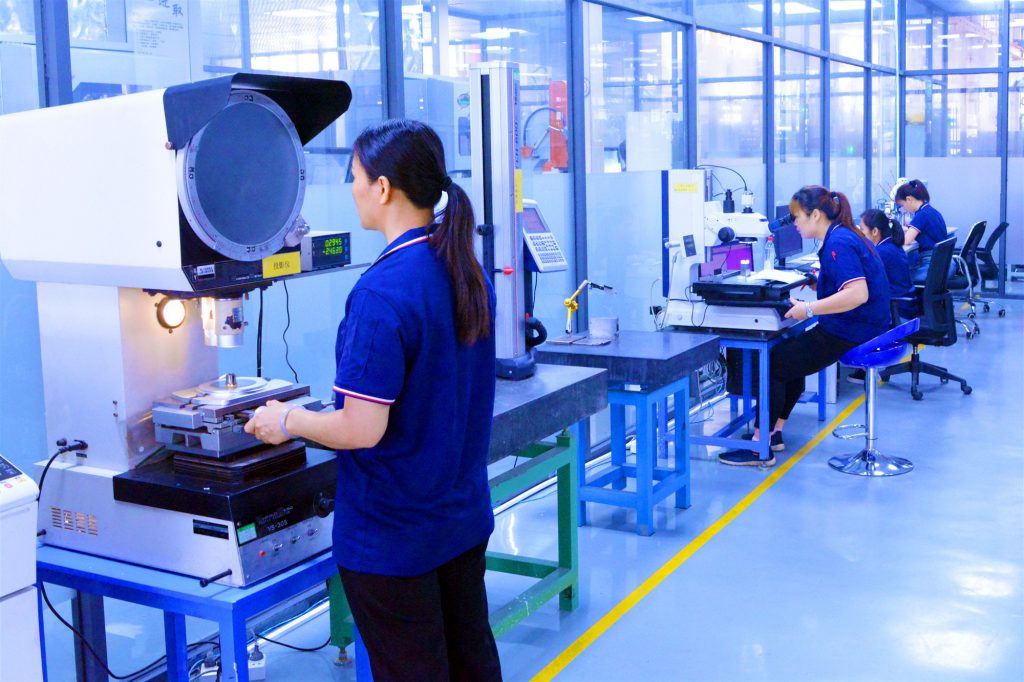
Injection molding is the most common manufacturing technology in industrial fields. Injected products not only have high requirements of dimensions, but also even have higher requirements on its appearance. Common defects of injection molding products such as: shrinkage on product surface, welding marks, flash, eject marks, etc. Those are important factors affecting the use of products.
GREFEE has many years experience in injection molding industry, we provide high quality injection molded products for industries of household appliances, automobiles, medical devices, communication electronics and so on for a long time. We keep improving from raw material purchasing, injection molding technology controlling, to product quality inspection. In 2021, the acceptance rate of our injection molding products is 99.2% in the first production, and the quality pass rate is 99.8% through the feedbacks of customers after use. Have a check of your injection molded parts to see whether they have defects.
Classification of defects
not all defective products are unqualified products, but we need to confirm whether these defective products affect our usage. So we need classify the defects.
Critical defect(CR)
Defects that are dangerous to personal safety or harmful to human health. Such as electricity leakage, water leakage, toxic plastic, sharp edge, etc.
Main defects(MA)
Products loss main function, defects affect mold life, assembling speed, or serious poor appearance so as to directly affect product sales, such as scratch, heterochromatic problem and so on.
Minor defects(MI)
Products with slight defects on appearance, but not affect sales. That’s to say, defects besides CR and MA, such as minor oil contaminations, scratches, water lines, shrinkage, etc.
Classification of surface grades
A surface: the outside surface can be seen in normal using, such as the surface for the screen printing position or the nameplate position, which are called A surface.
B surface: the outside surface cannot be seen in normal using, such as the side or back surface, which are called B surface.
C surface: the internal surface can be seen without tools or the surface can be seen after open.
Definition of defects on plastic part surface
Color stain point: result from visible different colors of impurities or burnt chips on the part surface.
Scratch: concave lines or linear marks without depth on part surface acted by external stresses. Fingernails can feel the layer sense.
Flash: bulgy material around plastic part edges or joint line areas, or irregular shapes (usually caused by poor molding)around part edges by handwork trimming.
Color aberration: toners mixed unevenly in plastic material tinting, improper use of gating material, or injection temperature changing, which cause the aberration between part and color palette.( refers to: the comparison between the color of parts and confirmed sample or color number exceeds the acceptable value).
Shrinkage: effected by all kinds of factors, shrinkage happens inside part in cooling after injection molding, which causes sink marks on the part surface.
Short shot: insufficient injection and mold damage cause deficient shape or material lack of product.
Distortion: too high injection temperature, inadequate cooling time, shrinkage after demolding, or residual internal stress cause bending, not smooth demolding, or distortion from forced ejecting.
Oil contamination: the oil liquid attaches on the part surface.
Gas mark: poor venting in mold or improper mold fitting. When the melted material fills the mold cavities, the material flows too slowly, making it difficult to vent, so the air can only vented by water exhausting location and present circle color-changing or light reflection around water gating surface.
Water pattern: in injection molding, when the melted material fills the mold cavities, it cannot flow smoothly after meet inserts, holes, pillars or grids, and then joint from multiple strands. Linear welding lines caused from incomplete joint.
Wrinkle: poor venting in mold or improper mold fitting, melted material flows too fast in filling the cavities, the air between part surface and mould cavity cannot be exhausted in time, forming white dots, which can scraped by finger nails.
Bubble: empty caves inside part and the round promontory on the part surface.
Eject mark: high pressure and temperature in injection, inadequate cooling time, when the part is demolded from the mold, some areas make it difficult to demold, need the ejectors to eject the part by force, then cause whitish problem or embossing around ejector location.
Assembling clearance: clearance caused by assembling of two parts except the specified tolerance in design.
Inspection standards
This standard is based on SOP(standard operation procedure)of GB/T2828.1-2003 for primary sampling plan, Ⅱ sampling level, random sample inspection and AQL. If there are no specific requirements, the decision shall be made according to the following AQL.
Critical defect(CR): C=0
Main defects(MA): MA=0.65 defects main are defective performance, defective function or components missing assembling, and this kind of defect will cause customer complaints or high reworking cost.
Minor defects(MI): MI=2.5 defects main are defective appearance or mechanical properties, but not affect function performance.
Inspection conditions
Ⅰ.Observe the part from front for a week under 40W fluorescent lamp, with 100cm of vertical distance, 30cm of visual distance, and sight 45 degrees above level.
Ⅱ.Cannot use unidirectional light source to highlight the flaws on parts surface, and there should be no direct light source during visual inspection.
Ⅲ.Inspection time: inspection time for each location as below chart shows, if find visible defects exist in any above inspection location, this visible defective area follows the specified standards for that area.
No. | A | B | C |
Visual distance | 300mm | 300mm | 600mm |
间Visual time | 10 s | 5 s | 3 s |
Appearance criterions
FAQ:
How to avoid defects on injection molded product surface?
There’re many reasons for defects on part surface, main in five aspects: product design, mold processing, injection molding technology, raw plastic material and product package. The first two reasons have the greatest influence. Such as shrinkage caused from uneven material thickness, reason is that too thin or thick thickness. Eject marks, inject marks or welding marks on products caused from improper designing of mold ejectors, gate point, or cooling method. Details please click here to view tips for injection molding design.
Are there any improve method for plastic product with defective appearance?
Since injection molding is a technology of one-off molding, most defective appearance cannot be improved. At GREFEE, if defects are found, we will scrap the defective products and re-make qualified products.
Is there much relevance between defective injection surface and injection molding machine?
Normally there’s a certain relevance. However, GREFEE adopt scientific injection molding method, we design the parameters of injection molding machine to a reasonable range, and if the injected parts are not qualified within this range, we’ll turn to modify the mold instead of only changing the parameters, in this way, we can achieve stable product quality and high-efficiency production.
In product designing, how do we know whether the defects happen on the product appearance?
GREFEE will assist our customers to conduct feasibility analysis on products for free, if there’s any possible issue, we’ll provide customers with modification, in this way, try to eliminate problems before mold manufacturing.
Summary: defects on product appearance is the most common problem in injection molding production. We must conduct product feasibility analysis in the early stage of product design, then design appropriate mold to get perfect product appearance. Besides, it’s very important to have high-quality injection mold suppliers, as professional partners can provide customers professional suggestion on products to avoid loss on new products.
MORE BOLG
Insert mold in injection mold service
What are advantages and disadvantages of Zinc alloy and Aluminum alloy?
Test mold injection molding
This guide aims to better helping technological team members grasp knowledge of test mold injection knowledge and skills to quickly learn the guidelines of machining setting,
Die casting case for automobile gearbox of Ford
This article will introduce the case in detail for Ford automobile gearboxes made in GREFEE.
Categories
Try GREFEE now,for free
We keep your uploaded files confidential and secure.