Coloring Method of Plastic Raw Materials: Toner, Color Masterbatch, Pelleting

Posted on : Jan 9, 2023 By GREFEE
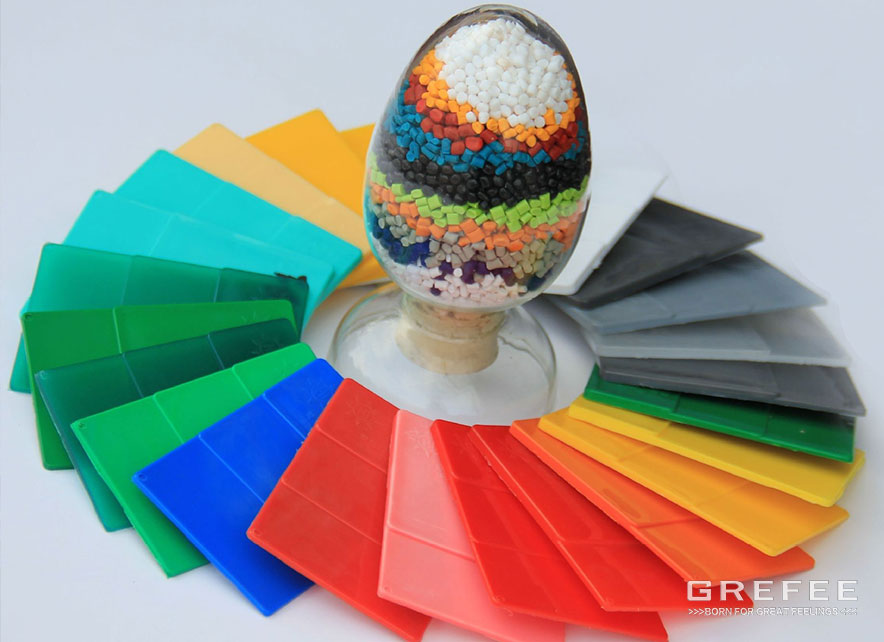
Three-primary colors: our eyes have three different types of color sensors, so the colors that we see are usually based on these three colors, which are called “three primary colors”. Generally speaking, the superimposed three primary colors are red, green and blue, also known as the three primary colors, which are used for TV sets, projectors and other display devices. The subtractive three primary colors are cyan, magenta and yellow used for printing books, magazines, etc.
In the actual production, due to the limited supply of variety of plastic colorant in the market, it is impossible to achieve and meet people’s needs for various plastic colors by adding a single variety of toner in plastic color matching, which only can be addressed by color blocking. Making use of the reasonable allocation among different toners to mix the required specific colors.
As we know, as the three primary colors, the red, green, blue cannot be mixed blended with the other colored lights, but they can form almost all colors. However, in the practicing, every color mixing and painting material mixing are all based on red, yellow, and blue.
Color matching is one of the important links of coloring. Color matching is based on the three basic colors of red, yellow and blue to produce a favorite color that meets the color difference requirements of the color card, is cost-effective, and does not change color in processing and use.
The plastic coloring is to utilize the dyes, pigments to reduce the color of sunlight and make products colored, which is to change the absorption and reflection of lights to obtain different colors, like absorbing all the lights, black. If only absorbs part of the lights (which only absorbs the light of a certain wavelength) and the number of the diffused light is low, so the plastic can become the colored transparent. If it is fully reflected, it will be white. If the unabsorbed light is completely scattered, the plastic will become “colored and opaque”.
Natural color of plastic: directly formed according to the background color of the natural color of raw materials, without adding any color materials, like transparent parts and internal parts of the natural color.
Three common coloring methods used for plastics: toner, color masterbatch and particle extraction
The first thing that we need for the plastic coloring is the colorant.
Colorant: can change the color of subjects or change the colorless into colorful substances, are called by a joint name, colorant.
Common colorant can be divided into two types: pigments and dyes
Dyes are soluble into many solvents and organic compound of solvent and dye medium, characterized by good transparency, high coloring power and low density.
Pigments are insoluble in water, oil, resin and other media, as opposed to dyes, pigments have no affinity with the coloring materials they need. If the material is colored by dispersing its particles in the colored material, the pigment is insoluble. So, in order to obtain good coloring performance, it is necessary to evenly disperse the pigment in the plastic by mechanical method.
Before using, the pigment should be soluble into water. If your plastic parts require bright and transparent color, but not temperature and weather resistance, then dyes can be used. Dyes dissolved in advance are called colorings.
The pigment needs to be grinned before using. If your plastic parts require bright and transparent color, but not temperature and weather resistance, then dyes can be used. Pigment pre-dispersed is called color paste!
Toner
Toner: raw materials set according to plastic. The manufacturer mixes various pigments according to the color sample given by the customer, and the dosage is calculated by each piece (unit: KGS)
Toner is a broadly speaking, it can be either dye or pigment, which is different from color essence, color paste and color masterbatch. Generally it refers to pigment.
Advantage:
1. Simple processing, cheap price
2. Simple transportation and is the cheapest
3. Suitable for a small number of diversified products.
Disadvantage
1.Toner is generally powder, which is likely to fly, causing great pollution and affecting the health of operators.
2. Stir the toner, and clean the mixing barrel and machine hopper when changing the color.
3.The dispersion of toner is poor, requiring the technicians have good technical knowledge on toner dispersion.
Application range: widely applied into coloring process of plastic products.
Instructions: Add the toner into the plastic in proportion and mix it. After heating by the molding equipment, the production finished.
Notice: adopting the relative color powder and raw materials in corresponding proportion according to the requirements of plastic products. Before using, cleaning the mixer and mechanics thoroughly to avoid the color mixing. In addition, during the production process, the parameters of the machine should be adjusted according to the requirement of each kind of products.
There are two factors mainly affecting the coloring effect: decentralization and homogenization.
Color Masterbatch
The color master batch is also called the color seed and color masterbatch are composed of three basic elements: colorant (pigment or dye), carrier and dispersant. It refers to the aggregate obtained by uniformly attaching super constant pigment or dye to the resin, which can be called pigment concentrate, so its coloring power is higher than the pigment itself.
It simply can be understood that the color masterbatch is a cylindrical granular pigment concentrate made by mixing and stirring the pre dispersed color powder+resin and then extruding it.
Basic component of masterbatch
1. Colorant
Refers to the pigment or dye
2. Carrier
Carrier is the matrix of color masterbatch. The carrier of the general matrix of master batch is a kind of resin with low melting point. The special color masterbatch generally selects the same resin as the product resin as the carrier, which has the best compatibility, but also needs to consider the mobility of the carrier.
3. dispersion
Dispersant is used to make the pigment to be dispersed evenly. The melting point of dispersant should be lower than that of resin. It has great good compatibility with resin and good affinity with pigment. The most commonly used dispersant are polyethylene low molecular wax and stearate.
4. Additive
Flame retardant, brightening, anti-bacterial, anti-static, anti-oxidation and other varieties, unless required by customers, Generally, the color masterbatch does not contain the above additives.
Advantage
1. Enable the pigment better dispersion
Color masterbatch is an aggregate made by uniformly loading super large amount of pigment into the resin.
The pigment must be refined during the production process to improve the dispersion and tinting power of pigments. The specifically used carrier of materibatch is similar to the variety of the plastic of products having good matchability. The pigment particles after heating and melting can be well dispersed in the plastic products.
2. Benefit the chemical stability of pigment
If use the pigment directly, it will contact with the air directly during the storage and using process, then the pigment will absorb the water and oxidize. After made into masterbatch, the resin carrier will separate the pigment with the air and water, which will maintain a good quality of pigment.
3. Maintain the stability of the product color
The particles of materbatch is similar to the resin particles, which is easier to measure and not easily to stick on the container when mixing. It is also mixed evenly with the resin, so it also ensures a stale adding amount, which further ensures the color stability.
4. Operating safety
The pigment normally are powder, so it is likely to fly when adding and mixing. It will also affect the wellbeing of
operators after inhaling.
5. Keep a clean environment and do not stain utensils.
6. Simple process, and is easy to change color, saving time and material.
Disadvantage
1. Must have a certain production amount, at least 100kg per batch, slow delivery response.
2. Must be mixed uniformly in case the static electricity and color difference.
3. Expensive than toner but cheaper than granulation.
Application range: applicable to the plastic products with higher requirements in color, using frequency, and products requiring a clean and tidy working environment.
Instruction:adding the masterbatch into the plastic and mixing them according to the proportion. After molding and heating, the plastic products obtained.
Notice: the adding amount of masterbatch is about 2%-4%. If it is the special technique, then the trial version shall be deployed as appropriate.
Graduation
Granulated material refers to the plastic raw materials are mixed with the color powder, and then the granulated plastic small particles of various colors are extracted by the granulator.
Simply, it means to transport the plastic raw materials for molding back to the color matching factory, then adding the color powder to make this batch of raw materials into cooled particles before sending them back to the molding factory.
Advantage
1. Color is unchanged.
2. Simple operating and automatic processing without stirring the raw materials.
3. Clean and environmentally friendly.
Disadvantage
1. The cost of the same color is higher than the toner and masterbatch, slow delivery response.
2. During the Granulation process, the properties of raw material maybe decreased.
3. The storage is large and the delivery fee is the highest.
Application range: applicable to the plastic products with higher requirements in colors or using frequently or large sizes.
Instruction: ready to use without adding the toner according to the proportion.
Notice: Any plastic in the plasticizing process will cause a break and decompose of high molecular. The longer the residence time, the more serious the fracture and decomposition. Thus, the performance after granulation will be lower.
Comparison of Several Coloring Methods
shading type | coloring method | dispersibility | color uniformity | flying | operability | automatic metrology | application range |
granulation | direct extrusion or injection molding | excellent | best | nothing | easy | easy | general industrial products and products with high requirements for color uniformity and dispersion |
color masterbatch | dilute 10-50 times when using | excellent | good | nothing | easy | easy | general industrial products and products with high requirements for dispersion, like thin film, fiber, etc. |
powder coloring | Dry pigment+dispersant | good | good | have | Slightly difficult | Slightly difficult | General products |
pasty coloring | pigment is dispersed in plasticizer or non-foaming organic solvent | excellent | excellent | nothing | easy | easy | PVC film,sheet metal and construction products |
liquid coloring | high concentration pigment is turned into organic solvent | excellent | excellent | nothing | easy | easy | PP, PE, PS, ABS and other film and plate products |
MORE BOLG
Insert mold in injection mold service
What are advantages and disadvantages of Zinc alloy and Aluminum alloy?
Inspection standards for injection molded partappearance
How to judge the quality of your plastic products?
Inspection standards for CNC machining
To ensure that your products are 100% qualified
Categories
Try GREFEE now,for free
We keep your uploaded files confidential and secure.