Processing tips for CNC Deep Hole Drilling

Posted on : May 6, 2022 By GREFEE
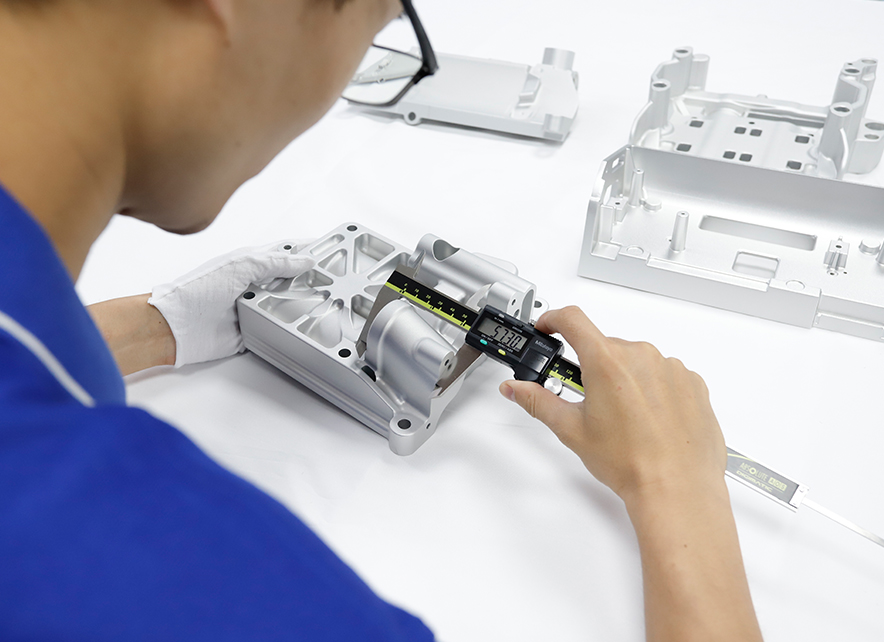
Deep hole machining is inevitable in CNC machining. While in this process, the parts are often plagued by some common issues which need to be solved urgently, like size accuracy, surface quality, the service life of tools, etc. GREFEE has rich experience in this domain, of which the products have been involved in industries, such as automotive, medical, mechanical, UAV, etc. For more detailed answers, contact our engineers. Below are some common problems and solutions to the deep hole machining.
1. Augmented aperture, large errors
cause:
- high out-diameter design value of the reamer
- burrs on the blade of the reaming cutting edge
- high machining speed
- improper feeding amount
- large cutting edge angle of the machining tools
- adhered built-up edge on the reaming cutting edge
- adhered built-up edge on the reaming cutting edge
- the bigger run-out tolerance of the reaming cutting edge when machining
- uncleaned grease or collisions on the taper shank surface when installing the reamers
- Morse taper of the taper shank is obliquely placed into the lathes.
- Primary axis bending or the spindle bearing loose or damaged.
- Reamer floating is not flexible
- Different axle -load from the parts,Reamer shakes left and right
solution:
- minimize the outer diameter of the reamer according to the situations
- decrease the machining speed
- adjust the feeding amount or reduce the working approach angle
- straighten or scrap the invalid and bend reamer.
- trim it with oilstone until it is qualified.
- clean the greasy dirt on the reamer taper shank or the primary axis or the inside of the taper holes of machine tool spindle thoroughly before placing the reamer.
- grind and repair the morse taper of the reamer.
- adjust or replace the spindle bearing.
- alter the floating dopp and the axiality.
2. aperture shrunk
cause:
- small outer diameter of the reamer
- low cutting speed
- high feeding amount
- cutting edge angle of the reamer is small
- The worn part of the reamer is not removed when cutting and grinding. Elastic recovery makes the aperture smaller.
- When reaming steel parts, the aperture minimized, out of round inner hole, unqualified aperture appear due to the high allowance or unsharpened reamer.
solution:
- change the outer diameter size of the reamer
- increase the cutting speed appropriately
- decrease the feeding amount appropriately
- enlarge the cutting edge angle appropriately
- select oily cutting fluid
- replace reamers regularly and grind the cutting parts of the reamers properly.
- the size of the reamer should be based on the considerations of above situations when designing.
- Take an appropriate allowance to sharpen the reamer in the experimental cutting.
3.the reamed inner hole is out of round
cause:
- reamer is too long. Insufficient rigidity. Vibration generated when reaming.
- the cutting edge angle of the reamer is too small.
- Narrow cutting edge band
- Notch and fork holes on the reaming surface
- sand holes and air holes
- the bearing spindle loose, without guide sleeves.
solution:
Reamers without sufficient rigidity can adopt different types of split pitch reamers. The installation of it should be rigid coupling. Increases the primary reamer and controls the position allowance of holes in the pre-processing procedures. Select split pitch reamer and long and precise guide base. Reaming holes with equal pitch reamer needs to adjust the primacy axis gap of the lathe. Combined with the coordination of the guide sleeve and proper clamping methods, to reduce the clamping force.
4. Evident faceted surfaces on the internal surface of the holes
cause:
- allowance of the reaming holes is high
- relief angle after cutting is large
- cutting reaming edge is too wide
- air holes on the part’s surface
solution:
- reduce the reaming allowance
- reduce the relief angle after cutting
- grind and repair the width of the blade
- select qualified blank
- adjust lathes
5. High roughness value of the inner-hole surface
cause:
- high cutting speed
- inappropriate cutting fluid
- large cutting angle, reamer blade is not in the same circumference.
- imbalanced reaming allowance or allowance is too small, so the local surface is not reamed.
- in-accurate run-out tolerance, blunt blade, wide cutting edge belt.
- Poor chip removal when reaming
- reamer is over worn
- collisions, balde retention, burrs, or tipping
- The angle the cutting edge is related to the material. This material is applicable for zero or negative rake angle reamer.
solution:
- decrease the cutting speed
- select proper cutting fluid according to material
- decrease the cutting edge angle appropriately, grinding the reaming cutting edge and the hole’s allowance.
- increases the positions accuracy of the front bottom hole and quality, or increase the allowance of the reaming.
- selects appropriate reamers
- reduce the number of the reamer teeth according to the conditions of blades. Augment the chip holding slot space or use the reamers with cutting edge inclination.
- replaces the cutting edge regularly. Grinding and remove burrs.
- In the process of reaming, using, and transportation, we should use protective measures to avoid the collisions.
- For the already damaged cutting edge,it is better to use fine oilstone to repair the reamer, or to replace the reamer.
- Modifying with the oilstone until it’s qualified.
6. Short service life
causes:
- Improper material of reamers.
- reamer burned during the grinding
- improper selection of cutting fluid. A smooth flow cannot be guaranteed.
- Roughness value is too high after grinding the reamer cutting edge.
solutions:
- Select the proper reamer material according to the machining material. Suitable choices include hardening alloy reamers or coating reamers.
- Strictly control the cutting edge damages.
- select proper cutting liquid according to the machining material.
- Clean the scissel in the grooves regularly. Use enough pressure to cut and grind to meet the requirement.
7. accuracy of the reaming position is out of tolerance.
causes:
- guide sleeve
- the bottom of the guide sleeve is far from the parts
- the guide sleeve is short and accuracy is poor. The primary axis is loose.
solutions:
- Replaces the guide sleeve: elongate the guide sleeve to enhance the coordinate accuracy between the guide sleeve and reamer.
- repair the bearing gap of the machine in time
8. Broken edge of reamer teeth
causes:
- The allowance of the reamer is large
- material hardness is high
- run-out tolerance of the cutting edge is large. Imbalanced cutting load.
- the main cutting width of reamer increases
- Reaming deep holes or blind holes, there are too much scissel which is not cleaned in time and the teeth is already broken when grinding.
solution:
- modifying the aperture size of the pre-processing
- lower the material hardness or replace by negative rake reamer or hardening alloy reamer.
- increase the cutting edge angle.
- clean the scissel in time or process with the reamer with angle blade.
- be aware of the edge-grinding quality
9. Broken reamer shank
cause:
- big reaming allowance
- When reaming, the allowance allocation of the rough and fine reaming, as well as the cutting amount is inappropriate.
- reamer teeth is blocked by scissel.
solution:
- alter the aperture size of the pre-processing.
- alters the allowance allocation and select the cutting amount properly.
- reduce the number of the reamer teeth. Grind one teeth out between the gaps.
- inclined center line of the reaming posterior holes
cause:
- Inclined drilling holes, especially when the aperture is small. Due to poor rigidity, the bending angle is big and cannot be recovered. Poor guidance makes the reamer is easy to go off the track in reaming.
- The inverted cone of the cutting part is too large.
- reamer go off the track due to the intermittent holes.
- when reaming manually, place too much pressure on one direction will force the reamer inclined on one side, which will break the reaming verticality.
solutions:
- Increase the reaming and the correction holes of the boring procedures.
- Reduce the cutting edge angle and select proper reamers.
- Switch to the side that has the guide or replace it with guide reamer.
- Deep hole machining in CNC parts requires experience to some extent, or it will lead to high scrapped rates, which affect the lead time and the quality. GREFEE has many years of experience in this aspect. You can trust us!
MORE BOLG
Insert mold in injection mold service
What are advantages and disadvantages of Zinc alloy and Aluminum alloy?
Inspection standards for injection molded partappearance
How to judge the quality of your plastic products?
Inspection standards for CNC machining
To ensure that your products are 100% qualified
Categories
Try GREFEE now,for free
We keep your uploaded files confidential and secure.