Factors affecting CNC machining: The CNC machining tips you must know?
Posted on : January 15, 2022 By GREFEE

The working performance and service life of mechanical products are always directly related to the machining quality of components and the assembling accuracy of products. The machining quality of components is the foundation of the whole product quality.
Studying on machining quality aims to discover the regularity of machining errors.Then study and analyze the influence of various factors on machining error. This article will illustrate all kinds of factors which affecting the machining quality of components one by one.We provide CNC online machining services。
The factors affecting the machining quality are very complicated in machining process. To meet the requirements on machined surface, The processing technology and cutting parameters must be carefully and appropriately controlled, which will increase the cost accordingly as well for meeting the high standards of quality control, however, which will increase product cost accordingly, so for general parts, try to adopt common technologies to ensure the quality instead of blindly pursuing high processing requirements.
While need control the machining quality of important component surface which may directly influent product performance, service life and safe operating, to achieve relatively high machining quality.
Machining precision and machining error
Machining precision refers to the coincidence degree between part actual geometric parameters (size, shape and mutual positions) and the specified geometric parameters of the ideal part in drawing designing.
Machining error refers to the deviation degree between the actual geometrical parameters of a part after machining and the ideal geometrical parameters specified in drawing designing. If the actual value is more close the ideal value, that means the machining precision is higher and less errors. “Machining precision” and “machining error” are only the two aspects evaluating the precision of geometric parameters of the parts. In actual production, the condition of machining error determines the machining precision level.
In actual production, any kind of machining technology is not possible, and not necessary to make parts absolutely accurate, as long as the machining error is controlled within the allowed range of performance requirements. Therefore, in setting technical requirements, should take it as criterion that achieve the highest performance with lowest precision and relatively large surface roughness.
Machining precision
Machining precision includes dimensional precision, shape precision and location precision.
Ⅰ.Dimensional precision: the coincidence degree between the actual dimensions of part itself or its surface after machining and the ideal dimensions of part. And the ideal dimensions refer to the mid-value of the part marked dimensions.
Ⅱ.Shape precision: the coincidence degree between the actual shape of part and the ideal shapes of part. The ideal shapes of part refer to the absolutely accurate surface geometry shape.
Ⅲ.location precision: the coincidence degree between the actual surface locations of part and the ideal locations of part. The ideal locations of part refer to the absolutely accurate locations between surfaces, without error.
Factors affecting machining precision
In mechanical processing, machine tools, jigs, cutters and parts form a complete system, which is called technological processing system. The machining precision problem of parts is an essential the problem of the whole technology processing system. Various errors in technology processing system reflect the part errors under different conditions in different degrees. Errors in processing system are the root of part errors, therefore, the processing system errors are called the original errors. Errors caused in machining process are called dynamic errors in processing system . Errors exist in machine tools, cutters and jigs and errors caused from part assembling are called static errors in processing system.We are a CNC companies produced in China
Various errors in technology processing system will cause different machining errors of part under different machining conditions. Process system errors can be classified in four aspects including the geometrical error, errors caused from deformation by force, errors caused from thermal deformation and errors caused from part internal stress changing.
Surface quality
Surface quality refers to the situation of part surface after machining, including surface roughness, and surface physical properties.
surface roughness: part surface presents convex peaks and concave valleys in different shapes and sizes since the cutting marks left on part surface after machining.
The influence of surface quality on the working precision of parts.
If the machining precision is too rough, the surface roughness will make the fitting clearance increase rapidly in the initial stage of abrasion for clearance fitting thus damaging the fitting precision, especially has a greater influence for clearance fitting requiring tiny size and high precision.
For interference fitting, the convex peaks of the fitting surface is extruded in the assembly process, so the actual effective interference is reduced and the fitting strength is decreased.
For parts, the surface roughness makes the actual contact areas between parts only occupy a small part of the nominal contact areas, and the areas really in contacting situation are only the several convex peaks of this small part.
The influence of residual stress on part precision
Although the surface residual stress is balanced inside the part, due to the creep deformation of metal materials, the residual stress is getting weaken and even disappear after a period of time, meanwhile the part also changes, which causes part errors in size and shape. For high precision parts, such as precision machine bed, precision measuring devices and so on, if there’s large residual stress on surface, it will influence the stability of their precision.
The influence of surface quality on fatigue strength of parts
The concave valley areas of the surface roughness cause stress concentration and fatigue cracks under the action of alternating loads.
The influence of physical and mechanical properties on fatigue strength
Generally adopt rolling, sandblasting, shot blasting and other methods to treat on part surface of important shaft journal and corner, and all kinds of important spring, which aims to cause the plastic deformation partly and expansion all around, and then cause strong residual stress since material expansion, delay the expansion of fatigue crack, so as to improve the fatigue strength of parts. The fatigue life for parts with different residual stress surfaces can differ from several times to tens of times.
Cold hardening on the surface layer can improve the fatigue strength of parts, since the cold hardening layer can not only prevent the expansion of existing cracks, but also prevent the fatigue cracks.
The influence of surface quality on corrosion resistance of parts
Corrosive medium condenses on the surface of metal and corrodes the surface layer of metal. The degree and speed of corrosion have a great connection with the surface roughness of parts. Part surface has concave valley or slight cracks after machining, so the corrosive matters accumulated in the concave valley and cracks. The metal corrosion gradually as it penetrates inside the metal, causing the metal fracture peeling down and forming a new surface with concave and convex. After that, the corrosion repeatedly expending to the new concave valley on the surface. repeatedly. The smaller the surface roughness is, the shallower the concave is and the less possible of corrosion.
The compressive residual stress and a certain degree of strengthening on the part surface will help to improve the wear-resisting performance of the parts.
According to their function role and their working environment, some parts require a relatively higher corrosion resistance instead of fine surface roughness, in this situation, the part surface must be polished.
Summary
Machining quality is the foundation of the whole part machining and the purpose of analyzing the machining quality is to discover the regularity of machining errors as well as the influence of various factors on machining errors. This article comprehensively analyzes the factors influencing the CNC machining quality, which helps us realize and avoid the possible affecting factors in future CNC machining work, and make qualified products. GREFEE’s CNC machining team has many years of experience, we’re glad to challenge those difficult projects.
MORE BOLG
Insert mold in injection mold service
What are advantages and disadvantages of Zinc alloy and Aluminum alloy?
Inspection standards for injection molded partappearance
How to judge the quality of your plastic products?
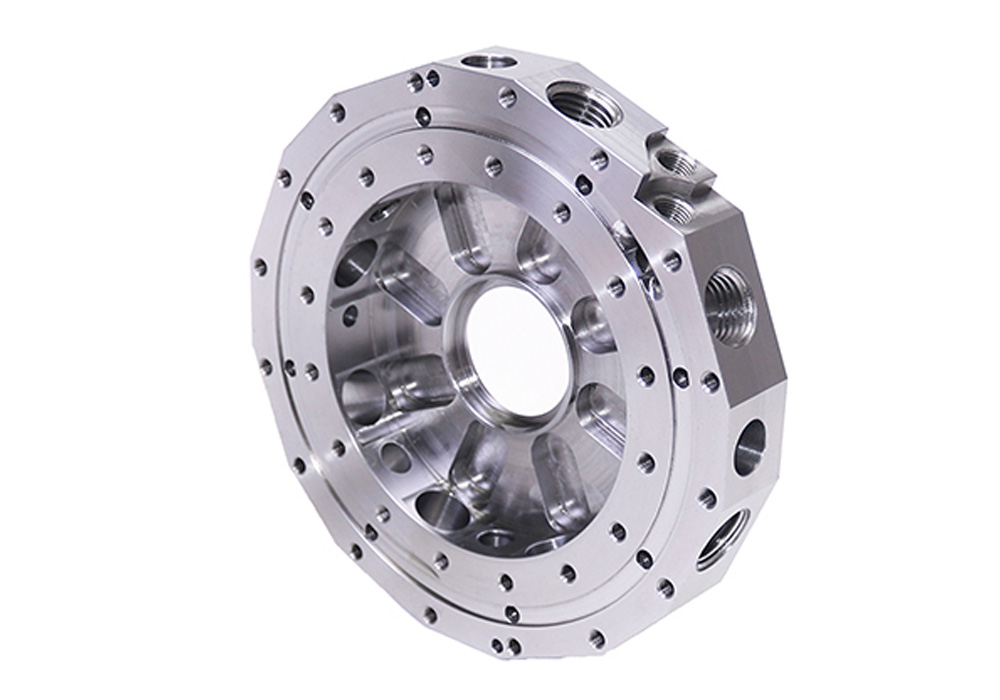
introduction of stainless steels commonly used in cnc machining
Stainless steel is a material that brightness closes to mirror, and touch feeling hard and cold.
Categories
Try GREFEE now,for free
We keep your uploaded files confidential and secure.