Gravity Die Casting

Posted on : Nov 7 , 2022 By GREFEE
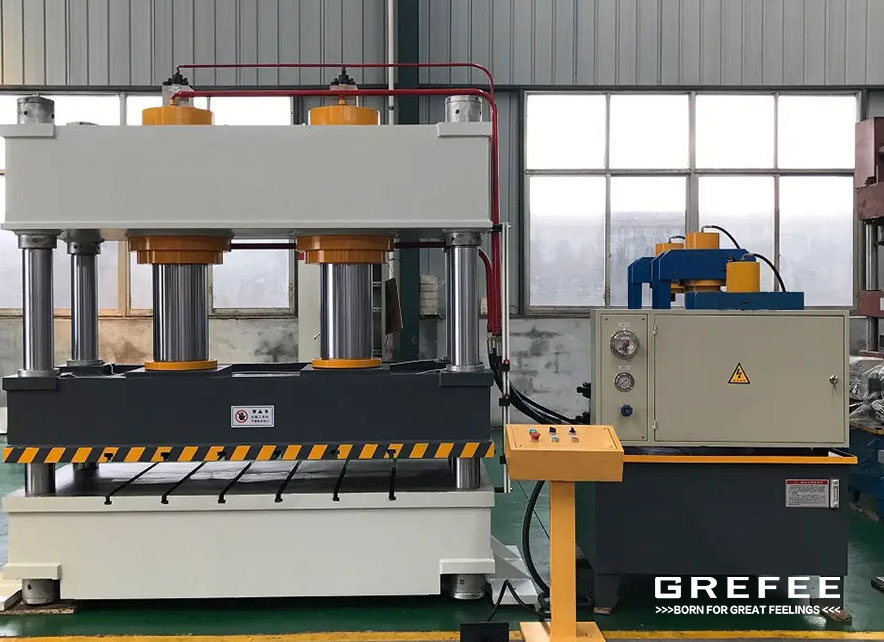
Definition of gravity casting process
The gravity die casting process refers to the process that the metal liquid is injected into the casting mold by gravity, also named as casting. Gravity casting process include sand casting, metal casting, investment casting, lost foam casting, mud film casting, etc. The metal casting is modern technique of heat resistant alloy steel manufacturing die. During the gravity die casting process, the liquid metal is often poured into the casting gate manually, and then filling the whole cavity by the weight of liquid metal itself. After a series steps, venting, cooling, molding opening, the product is obtained. The process steps are: molten aluminum smelting, casting material filling, exhaust, cooling, mold opening, production clearing, heat treatment and processing.
Characteristics of gravity casting
1. There are not too many pores inside the castings, and can carry out thermal treatment. The strength of products after thermal treatment will obtain a high achievement, or even exceed the die casting products.
2.The density property is lower than that of die casting products, which depends on the weight of product it self to form. Besides, the strength is poor, too. The elongation rate is high.
3.The surface finishes of products is low. The surface of the cast product is easy to form a pit similar to shot blasting after cooling and shrinkage. The molding filling is slow and production rate of gravity casting is low, only one fourth of high pressure casting, resulting in high costs, but the service life of molds is long and the cost is low.
Not suitable for producing thin-walled parts
What are the similarities and differences between gravity casting and low pressure casting?
Mold selection: metal and non-metal (like sand casting)
The purchasing cost of metal molds is high, whereas that for wood molds is low. While, it may produce a large cost on maintenance for the gravity die casting suppliers if the molds are not used for a long term or requires large volume production.
Production rate: metal low pressure casting easy to achieve automatic beat production with high efficiency. The appearance of resin made molds and the inner mold core can only use once, of which the production rate is low.
Material utility rate: low pressure casting is suitable for thin walled castings. The riser occupies very little material. The gravity casting is not suitable for producing thin-walled castings, which requires the riser (risers is the supplementary part attached to the top or side of the casting to avoid defects in the casting. The gate is the head of the part, and the riser is the tail of the part. It is used to observe whether the cavity is filled with saturation. Both of them need to be removed).
Casting material: black metals and nonferrous metals. Low pressure casting mainly applied into nonferrous metals casing. The alloy material is expensive and low pressure casting can reduce the loss of raiser.
Working environment: mainly is mechanized operation, and the working environment is good. While the environment is poor while gravity casting is poor, especially for pouring operation
Process procedures of gravity casting
Take the most used sand casting as an example, what need to prepare include molding material preparation and molding core making. Different materials used to make for the mold cores in the sand casting include casting sand, molding sand binder and other auxiliary materials, as well as molding sand, core sand and coating prepared from them, which are all called modeling materials. The preparation duty is according to the requirements of castings and properties of metals to select appropriate raw sand, binder and auxiliary materials, and then they are mixed into molding sand and core sand with certain properties in a certain proportion. The commonly used sand mixing equipment includes roller type sand mixer, counter flow type sand mixer and blade groove type sand mixer. The latter is specially designed for mixing chemical self hardening sand, with continuous mixing and high speed.
Molding and core making are based on casting process requirements, and casting methods, good preparation of casting material. The accuracy of casting and economic effect of the whole production process are mainly determined by this procedure. Many modernized casting workshops, the core making and casting all achieved the mechanization or automation. Common used sand casting equipments include the high, medium and low pressure molding machines, sanding machines, non box injection molding machines, core injection machines, cold and hot core box machines, etc.
The castings come out of the pouring cooled mold with many defects, like gates, risers, metal burrs, burrs and clamping lines. The sand is also adhered to the sand casting, so the castings must be cleaned with equipments include polishing machine, shot blasting machine, pouring and riser cutting machine, etc. The peeling of the sand castings is a step with poor working conditions, so when selecting modeling method, we should fully consider the create convenient conditions for sand falling cleaning. Some castings have to undergo post-treatment due to special requirements, such as heat treatment, reshaping, rust prevention treatment, rough machining, etc.
Matters needing attention during gravity casting:
1. Before casting, the dummy head should be positioned well, and ensure that the machine is repaired and checked carefully. Repairing or replacement is required if necessary.
2. If the the graphite ring is damaged too much or cracks appear, repairing the graphite immediately.
3. Before processing, the aluminum alloy gravity die casting manufacturers, should check whether the equipment process normally, whether the lubrication is in place, whether the wire rope is damaged and whether the switch is flexible, etc.
4. Pre-heat the flow grooves and the related casting tools. During the preheating, positioning the filter screen properly.
5. Replacing the plug immediately after opening the water running holes, and close it to achieve the effect of controlling flow.
6. During the aluminum alloy gravity die casting process, start working after the related crystallizer has been filled with molten aluminum. Controlling the speed and temperature properly during casting.
7. Stop the casting machine and then stop the water near the end, which ensures the aluminum water void completely.
Common defects of aluminum alloy gravity casting parts:
1. Shrinkage cavity
This kind of defect often occurs in the thick part of the casting or at the junction of thickness and thickness. Sometimes the surface of the casting is white, which is actually shrinkage.
Causes:
(1). Insufficient feeding of castings during crystallization
(2). Wrong position to introduce alloy liquid
(3). Improper temperature of each part of the metal mold and does not comply with the principle of sequential solidification;
(4). Improper coating or coating falling off;
(5). High pouring temperature
(6). Fast pouring speed
(7). Casting cooling is too slow;
(8). The rough edge of the casting is too large.
Solutions:
Setting the risers on the thick area of castings. The size and height of risers should be appropriate until it solidified, which can improve the feeding effect of riser.
Evenly arranging the inner runners along the castings or setting the supplement runners at the root of the risers to improve the feeding.
Adjusting the temperature standards of each area of metal casting, for the sake of sequential solidification of castings.
Selecting different coating and thickness of coating according the requirements of different areas of risers and working parts of castings, and ensure feeding evenly.
Lowering the pouring temperature appropriately.
Reducing the pouring speed.
Copper cold iron or vent plug can be embedded in the parts prone to shrinkage and looseness to accelerate cooling.
2. Cold shuts
Cold shuts usually appear on the large surface of the thin walled castings and the last confluence of the alloy. The castings after molding need to clean the sand for the appearance inspection to check whether if there are any cold shuts.
Cause:
(1). Mold temperature is too low
(2). The temperature of aluminum liquid is too low
(3). Venting of mold is poor
(4). Poor injection system designing. The number of inner gates is not enough and the cross section is too small.
(5). The pouring speed is too slow or the pouring is interrupted.
(6). The wall of castings is too thin or there is a lack of appropriate fillets.
Solutions:
(1). Raising the mold temperature appropriately
(2). Raising the pouring temperature of aluminum liquid
(3). The area that gas cannot be voided easily should be with venting grooves or venting plugs to maintain good venting effect.
(4). Raising the number of inner gates appropriately and the cross section area of inner gates.
(5). Raising the pouring speed to avoid the interruption of molten aluminum pouring.
(6). The designing of the reasonable minimum wall thickness and casting fillet is according to the technological requirements of casting design.
3. Pores
Pores are often detected on the emboss areas on the surface of castings. The inside of the castings often have pores, which must be detected through the X-ray fluoroscopy and when the casting is processed.
Cause:
(1). Fast pouring speed and gas tracking.
(2). Poor venting
(3). liquid aluminum flows fast
(4). Melting temperature is high
(5). Poor degassing of alloy
(6). Pouring temperature is high
(7). The sand core is not dry, the exhaust is poor or the gas generation is too large.
Solutions:
(1). Pouring smoothly
(2). Adding vent slot or vent plug on the parts where metal type gas is not easily excluded, and cleaning regularly.
(3). The ladle should be as close to the gate cup as possible when pouring
(4). Strictly control the temperature of aluminum liquid to prevent the temperature exceeds the range.
(5). Degassing of molten aluminum correctly.
(6). The mud core should be dried, and the exhaust hole should be unblocked. After the mud core returns to moisture, it should be dried. The middle of the extra large mud core should be hollowed out.
(7). After the coating, waiting for the coating dried to pour
4. Cracks
Cracks often appear on the internal included angle of the casting and the transition part of the thick and thin section. The area that liquid alloy enters into the castings and the part with the largest casting stress can be inspected by the coloring test, air tightness test and X-ray inspection. Any cold cracks on the aluminum castings can be detected in the appearance check after cleaning the sand.
Cause:
(1). There are sharp corners on the casting, and the thickness varies greatly
(2). Local area overheating or the temperature of pouring is high
(3). Incorrect placement of cold iron;
(4). poor feeding
Solutions:
(1). Improve the designing and cleaning the shape corners. Try to make the wall thickness of the casting evenly transition and fillet;
(2). Selecting the position of gate and runner properly, controlling the pouring temperature and coating thickness, placing the cold iron properly, and increase the feeding capacity of the riser;
(3). Apply asbestos insulation coating on the mold riser.
5. Segregation
Segregation is often found in the center and upper part of the thick part of the casting, which can be detected by macro analysis.
Cause:
(1). The composition of molten aluminum is not stirred evenly before pouring;
(2). Pouring temperature is too high.
(3). The temperature of metals is too high. The coating is not even and thick.
Solutions:
(1). Stir the liquid alloy evenly before pouring
(2). Appropriately lowering the pouring temperature and the preheating temperate of metal molds.
(3). Cold iron and vent plug are required at parts with slow cooling, or air cooling and water cooling should be adopted.
(4). Adding the element that prevents segregation of the alloys.
(5). Reducing the wall thickness of castings appropriately to accelerate solidification.
MORE BOLG
Insert mold in injection mold service
What are advantages and disadvantages of Zinc alloy and Aluminum alloy?
Inspection standards for injection molded partappearance
How to judge the quality of your plastic products?
Inspection standards for CNC machining
To ensure that your products are 100% qualified
Categories
Try GREFEE now,for free
We keep your uploaded files confidential and secure.