How Design Plays an Effect Role in Improving the Quality of Zinc Alloy Casting

Posted on : July 11 , 2022 By GREFEE
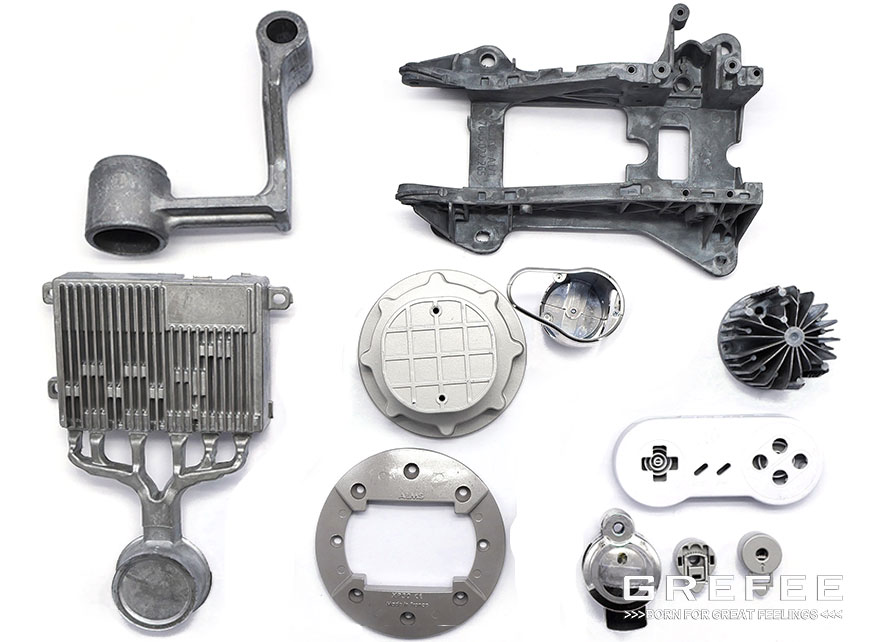
Zinc alloy die casting molds are important process equipments in the zinc alloy die casting production. During the production, the liquid metal solidified in the die casting molds and finally being formed into the zinc alloy die casting parts. Its shapes, dimensions, quality and efficiency are all related to the die casting molds. Thus, a proper design is essential.
Basic structure of the zinc alloy die casting mold
The commonly used die casting molds are composed of two half mold, which are fixed mold and moving mold respectively. Indeed, there are more complex die casting molds other than this two half molds.
The function of zinc alloy die casting mold composition:
1.The sprue connects the pressure chamber or the transverse sprue, including the sprue sleeve and the diversion cone.
2.the channel for the alloy liquid of the gating system to enter the mold cavity, including the inner sprue, transverse sprue and direct sprue.
3. the cavity is formed on the insert block, generating the geometrical shapes of the castings.
4. The core pulling system completes the pulling and insert of the moving core, including the slideway, slide block, oil cylinder, slash, etc.
5.Venting gas from the overflow system and store cold metal residues, etc.
6. The temperature controlling system controls the temperature of the die casting mold, including the cooling and heating pipes, etc.
7.The ejection system ejects the castings from the cavity, including the ejector bar, etc.
8.The moving mold connects and fixes the components of the moving mold, including the sleeve plate, support plate, etc.
Design of the zinc alloy die casting mold
Dos and Don’ts in designing the die casting mold:
1. Try to select simple structure to ensure the action is reliable and stable, as well as the maintenance.
2.The modifiability of the gating system should be considered, and necessary modifications can be made during commissioning.
3. Properly choosing the tolerance, scale and allowance to ensure the fitting of components and the accuracy requirements of zinc alloy castings.
4. Reliable mold material and thermal treatment process is the insurance of the service life of the die casting molds.
5.Sufficient rigidity and strength that can bear the clamping force and swelling force, and doesn’t cause the deformation during the die casting process.
6.Try to use the standardized die casting mold parts to improve the economical and interchangeability performance.
Zinc alloy die casting process system design
It comes to the design of the gating system after the mold frame part. In the production of zinc alloy die casting, the position and direction of the inner runner are adjusted according to the internal quality of the product. In recent ten years, since the development of numerical simulation technology of casting filling and solidification process, as well as the market demand of casting industry, the commercialized software of casting process simulation are increasingly popular. The die-casting simulation process is even important for many main engine manufacturers before designing the mold. Therefore, MAGMAsoft or AnyCasting are the two simulation softwares that they often use . At the beginning of the design, the designed three-dimensional is imported into this program. As soon as the die-casting process parameters are set, the simulation software will get the simulation animation close to the real production effect after certain calculation.
The simulation results of die casting process requirements are as follows:
1.The alloy liquid should reach the inner runner more or less in the meantime.
2.The alloy liquid should be filled smoothly during the filling process.
3.No entrainment or turbulence occur during filling.
4. Before completing the filling , the liquid alloy cannot seal the slag collecting ladle passage.
5. The cold metal produced in the filling process should not be stored in the zinc alloy die castings, but should be pushed into the slag collection bag.
According to the requirements of filling simulation and particle tracking simulation and die-casting process, the position and size of the sprue and slag collector of the mold should be optimized accordingly. According to solidification simulation and wall thickness of zinc alloy die castings, the cooling water and heating oil pipes in the mold, as well as the location of point cooling can be determined. According to the mold erosion simulation, we can detect which parts of the mold need to be sprayed. Through simulation analysis, the process of manual optimization of gate and slag collector is addressed in the design, which can omit the mold modification process due to the deviation caused by experience in mold manufacturing.
To further improve the quality of the zinc alloy casting parts, some zinc alloy die casting manufacturers utilize the vacuum technology to lower the scraping rate and create higher value. The vacuum pumping technology is very mature in Japan. Some manufacturers in China even learn a lot from their experience. The vacuum technology requires that the area of the mold exhaust duct is 1:100 of the punch area. Start the vacuum pump 0.4s before the start of rapid injection. The number of vacuum exhaust wave plates or vacuum valves should be based on the complexity of the product and the size of the mold in zinc alloy die casting mold designing.
Properly using the vacuum technology will lower the scrap rate of zinc alloy die castings to at least 20% of the previous figure. However, due to the expensive of vacuum pumping equipment, some zinc alloy die-casting manufacturers only adopts it in produce molds with high scrap rate.
MORE BOLG
Insert mold in injection mold service
What are advantages and disadvantages of Zinc alloy and Aluminum alloy?
Inspection standards for injection molded partappearance
How to judge the quality of your plastic products?
Inspection standards for CNC machining
To ensure that your products are 100% qualified
Categories
Try GREFEE now,for free
We keep your uploaded files confidential and secure.