Introduction to mold polishing

Posted on : February 17, 2022 By GREFEE
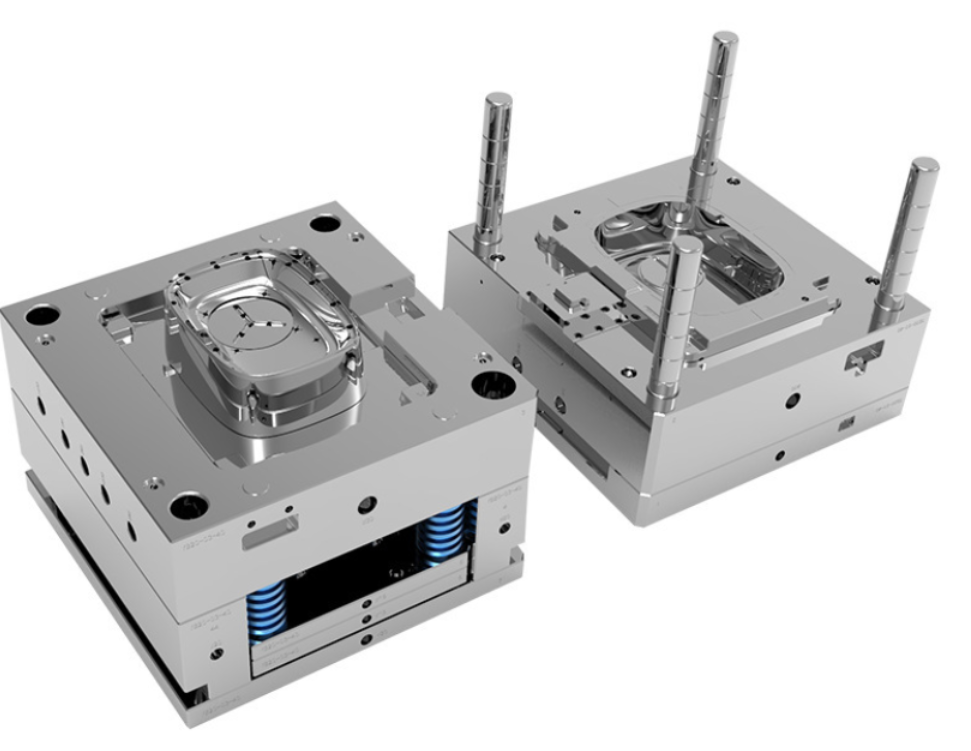
List
Ⅰ.Objectives of mold polishing.
Ⅱ.Issues caused by poor mold polishing.
Ⅲ.Mold polishing classification.
Ⅳ.Tools & machines in mold polishing.
Ⅴ.Common used polishing tools.
Ⅵ.Dos and don’ts of mold polishin.
Ⅶ.Factors affect the quality of mold polishing.
Ⅰ.Objectives of mold polishing.
With plastic material has been utilized in different industries, the requirements of mold polishing can reach up to the degree of mirror finishing. The guidelines of mold polishing include:
1.Polishing can improve the aesthetic quality of parts for the needs of optical skills and appearance.
2.Polishing improves corrosion resistance and wear resistance on the surface of the material.
3.Polishing reduces resin flow resistance.
4.Polishing improves the accuracy of clamping surfaces, avoiding burrs.
5.Polishing makes plastic material de-mold easily, shortening lead and injection time.
Ⅱ.Issues caused by poor mold polishing.
1.Poor polishing will lead to texture marks, foreign body, polishing marks, and concave-convex.
2.Lead to scratches and resin chips in demolding.
3.Due to the static electricity, resin dander will stick on the female and male die PL surface. Under this condition, the PL surface will puff up.
4.There are burrs as the puffy scratch surface can not be closed together.
5.Although it can fix burrs(real-time solution) but is not 100% effective; besides, it wastes time due to poor polishing, which is the key.
6.Repairing mold many times in volume production will cause the rate of movement to decrease and material wasted, too.
Ⅲ.Mold polishing classification.
Code | Designation | Processing method | Roughness | Polishing code |
—- | 30 | Oilstone | 0.16-0.17 | C1 |
—- | 37 | Oilstone | 0.23-0.27 | C2 |
—- | 45 | Oilstone | 0.34-0.39 | C3 |
—- | 11# | Texture | 0.92-0.99 | D1 |
—- | 240# | Texture | 1.77-1.89 | D2 |
—- | 24# | Texture | 3.15-3.58 | D3 |
—- | = | Texture | 1.83-1.99 | SP15 |
—- | 3A | EDM | 3.62-4.31 | 3A |
—- | 2A | EDM | 2.33-2.41 | 2A |
—- | 1.5A | EDM | 2.07-2.14 | 1.5A |
—- | 1A | EDM | 1.31-1.53 | 1A |
140# | —- | Grinding | 3-4 | —- |
230# | —- | Grinding | 2-3 | —- |
400# | —- | Grinding | 1-2 | —- |
Ⅳ.Common used polishing tools & machining
Common polishing tools:
Abrasive paper, oilstone, felt roller, diamond paste, diamond file, flint, diamond grinding needle, Cooper slices, bamboo slices, fiber oilstone, emery cloth boots.
Front and rear puller, rotary grinder, pneumatic front and rear puller.
V.Steps and methods of polishing
To excellent polishing effects, it is vital to undertake assisted with auxiliary and polishing tools like high-quality oilstones, abrasive paper, diamond paste, etc. The surface condition in the early stage determines the polishing procedures, such as mechanical processing, electrical discharge machining (EDM), grinding, etc.
Mechanical polishing procedures:
1.Rough polishing:After the process of milling, electrical discharge machining ( EDM), and grinding, we can use a rotary surface polishing machine or ultrasonic grinder with a rotating speed of 35000-40000 rpm for polishing.
Common methods include tyre (dia.3mm, WA # 400) to remove the white electrical spark layer and then is the manual oilstone grinding, striped oilstone add kerosene working as lubricant or cooler.
Some common methods for this process include a tire (dia.3mm, WA # 400) to remove the white electrical spark layer and then is the manual oilstone grinding, striped oilstone adds kerosene working as a lubricant or cooler.
The common using procedure is #180 ~ #240 ~ #320 ~ #400 ~ #600 ~ #800 ~ #1000.
Many mold makers choose to start from #400 to flat the electric discharge texturing.
2.Semi-Finishing Polishing
Mainly use abrasive paper and kerosene
The code of abrasive paper: #400 ~ #600 ~ #800 ~ #1000 ~ #1200~#1500
3.Fine Polishing:Mainly use diamond grinding paste,9μm(#1800)~ 6μm(#3000)~3μm(#8000)。
Provided that applies polishing cloth roller mixing diamond grinding powder or grinding paste, the grinding order would be 9μm(#1800)~ 6μm(#3000)~3μm(#8000). The 9μm diamond grinding paste and polishing cloth roller can remove the hair scratches caused by #1200和#1500 abrasive paper. After that, polishing with adhesive felt and diamond grinding paste, the order is 1μm(#14000)~ 1/2μm(#60000)~1/4μm(#100000).
The polishing accuracy requirement is more than 1μm and must carry out in a space with absolute cleanliness. Dust, smoke, dandruff, or saliva droplets, all of them can possibly ruin the fine polishing surface achieved in a few working hours.
Ⅵ.Dos and Don’ts in mold polishing
Dos and Don’ts in abrasive paper polishing:
1.When it comes to abrasive paper polishing, we need to utilize a soft stick or bamboo stick. When polishing a round surface or sphere, we can use a soft stick to better fit the radian of the round or sphere surface. Some hard wooden strips like cherry wood fit flat surface polishing better.
Adjust the end of the wood strips to make them fit the surface shape of steel parts to avoid the deep scratches caused by the contact between the acute angle of the wood strips (or bamboo strips) and the surface of steel parts.
2.When using different types of abrasive paper, the direction of polishing should change from 45°~ 90°.In this way, the textures caused by the polishing of the previous type of abrasive paper can be distinguished. Before changing another category of abrasive paper, we must carefully wipe the polishing surface with 100% cotton dipping in detergents like alcohol.
Even only one small sand will ruin the following polishing work, for the abrasive paper polishing mode changing into diamond grinding paste polishing mode, cleaning is vital, too. Before continuing polishing, clean the molecules or kerosene thoroughly.
3.To avoid scratching or burning the surface of parts, we should be careful when polishing with #1200 & #1500 abrasive paper. It is necessary to add one light load and polish the surface in 2-step Polishing Process. We should double polish in two different directions when applying each type of abrasive paper. Rotating 45°~ 90°each time between two directions.
Polishing in only one direction can cause polishing textures easily and scratches on the surface.
The polishing direction of the current polish degree should cross with the polishing direction of the previous degree before the front polishing textures can be polished flat. The longer the slide work distance is, the more convenient it is to operate (especially narrow surface polishing)
4. flat electric discharge textures:
flat #360 polishing textures,flat #600 polishing textures.
in a similar way,diamond paste #200 remove all the reverse buckles.
Dos & Don’ts in Diamond Grinding Polishing
1.However, it is hard to maintain the accuracy of this it. To make it easier, we can make a thin and narrow handle on the wood strip, like adding a copper slice on the wood strip or cutting part of it to make it softer. It can assist with controlling the polishing pressure so that the surface pressure would not be too high.
2.For diamond grinding polishing, not only the surface should be cleaned carefully but also our both hands, too.
3.The polishing time should be short. The shorter it is, the better effect it brings. If the process is too long, there might have “orange peel” or “pitting corrosion”
4.To achieve a fantastic polishing effect, we should avoid methods and tools that are easy to be getting heat. Such as polishing the wheel, the heat quality it generated caused orange peel easily.
5.When polishing stops, it is vital to ensure the surface is clean and remove all the grinding agents and lubricants, too. Finally, coat the parts with an antirust coating.
Ⅶ.Factors affect the quality of mold polishing.
1.As mechanical polishing operates manually, the polishing technique is still the primary factor for the quality.
2.It is associated with material, pre-polishing surface conditions, heating, etc. The fine polishing quality can not be achieved without good quality steel. It would be hard to polish with inconsistent steel surface hardness and characteristics. Diverse inclusions and air holes will affect the polishing process.
MORE BOLG
Insert mold in injection mold service
What are advantages and disadvantages of Zinc alloy and Aluminum alloy?
Inspection standards for injection molded partappearance
How to judge the quality of your plastic products?
Inspection standards for CNC machining
To ensure that your products are 100% qualified
Categories
Try GREFEE now,for free
We keep your uploaded files confidential and secure.