Manufacturing Methods of Rapid Tooling

Posted on : June 29 , 2022 By GREFEE
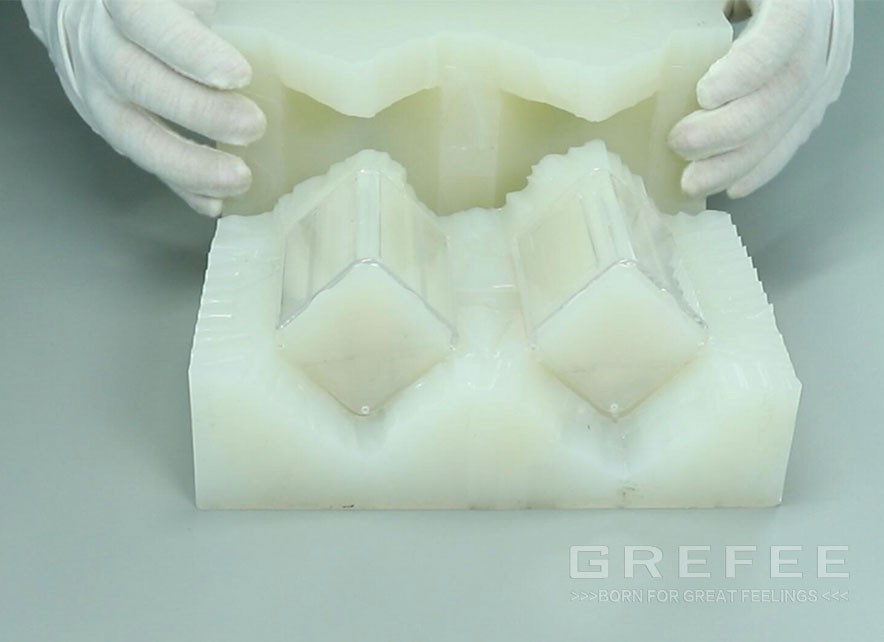
Manufacturing Methods of Rapid Tooling
Rapid tooling is a type of tool used to produce products with specific shapes, size and surface accuracy, which is mainly adopted in the large volume production. Even though the production and fabrication cost is high, the cost of each product decreases significantly due to the large volume production.
Advantages of rapid tooling processing
1. Custom moulds for personal applications are available
2. Products of rapid tooling can be put on the market earlier than it expected.
3. Compared to the products produced by large-scale injection mold, its price is cheaper.
4. Compared to the traditional molds, the mold time is shorter and its cost is lower.
5. Owns evident edges on time for rapid tooling companies in various business manufacturing. Meanwhile, it shortens the production cycle and lower the manufacturing cost and time
6. Extensive injection material till the perfect custom forming products are made.
Classification molding process
Rapid tooling is a multi-function tool that can be divided into plastic mold, cartable mold, stamping mold, forge mold, and graphite electrode grinding master mold. According to the molding material, it can also be divided into simple mold, also called soft mold, economical mold, non-steel mold and steel hard-mold root. Common rapid tooling processing methods include direct rapid tooling and indirect rapid tooling. We are familiar with plastic mold, cartable mold, stamping mold, forge mold, and graphite electrode grinding master mold, so in this article we will talk about something else, which are soft and hardened rapid tooling technology. Due to the soft material, the soft molds is well known for its difference from the traditional steel material. Proposed soft tooling manufacturing methods include the silicone rubber pouring method, metal spraying method, resin pouring method, etc. the number of the soft mold products is usually 50~5000 pcs. However, if it is tens of thousands or even hundreds of thousands of products, traditional steel molds are still needed. Actually, the hardened mold refers to steel mold. Methods that utilizes the PR prototype to produce the steel molds include the investment casting and ceramic mold finish.
Based on the rapid tooling manufacturing methods of the rapid prototypes tooling, the first thing needs to do is to make the cavity through the RP prototype and then transmit it into the mold cavity. By doing so, the product can be cast into shapes. Of course, it can be obtained by multiple conversions or through the electrode.
The rapid manufacturing method of the silicon rubber molds is soft molds, also being called the indirect molding. The silicone rubber mold manufacturing technology is a disseminated rapid tooling production method. Due to the excellent flexibility and elasticity of the silicone rubber molds, it is used to produce complex shaped parts with fine pattern effect, or parts with or without the draft angle, or parts with deep grooves. It is popular among the rapid tooling companies in China due to its advantages of short manufacturing cycle and high quality.
(1)Prototype table processing. Prototype made by PR often has step pattern or gaps between the laminated fault, which needs to be ground and strengthening and leakage prevention treatments to enhance the surface finish quality, moisture and heat resistant parts of prototypes. Only by having a sufficiently smooth prototype surface, the surface finish of the silicone rubber mold can be promised. Then, it further ensures the reproduced products with high surface quality, and is easy to be released from the silicone rubber mold.
(2) frame and fixed prototype fabrication
Designing the shape and dimension of the pouring frame according to the geometrical dimension and manufacturing requirements of silicone rubber mold. Before fixing the prototypes, it is important to decide the position of the parting surface and gate as it affects the quality of products and determines whether the mold can be released smoothly. After finishing the parting surface and the selection of gate, fix the prototype in the shape box.
(3)metering of silicone rubber, mixed with vacuum deaeration. The use amount of silicone rubber should be metered carefully according to the size of manufactured curved cabinet and specific gravity of silicone rubber. Add a certain amount of hardener into the metered silicone rubber, then stir it to get ready for the vacuum deaeration. The time of the vacuum deaeration should be determined by the required vacuum level.
(4) Silicone rubber teeming and curing. The silicone rubber mixture will be teemed into the mold frame of the fixed prototype after being vacuumed. During the teeming process, we should follow the techniques. For instance, after the teeming of the silicone rubber, a second vacuum deaeration should be performed again to ensure the cavity is filled properly. It aims to extract the gas the mixed in the silicone during the teeming process and hidden in the prototype cavity. The time for this deaeration should be longer than that before the teeming, which is determined specifically by the operation time and size of prototype of the selected silicone rubber material. After the vacuum deaeration, the silicone rubber mold will be hardened automatically or with the help of heating. The heating hardening shortens the hardening time.
(5)remove the frame, opening the mold with a knife and take out the prototype. When the silicone rubber mold has been hardened, the frame, sprue bar and other components can be removed. Opening the mold with the knife according to the marks on the parting surface of the prototype and take out the prototype before cleaning the cavity of the mold. After all, the silicone rubber mold can be used for the fabrication of the resin and plastic products.
Silicone rubber mold
Due to the high cost of the silicone rubber mold materials, people developed a processing method through the mixing with gypsum, which is way to make the economical silicone rubber mold.
Prototype placement
Placing the prototype on the platform and fixed after standard cleaning and treatments. Making the frame for each prototype and allowing an equal distance between the prototype and mold frame. Applying the mold release agent on the formwork plate surface.
Backing
Paste clay or plasticine on the surface of prototype and then pour the prepared gypsum slurry into the frame. After the gypsum slurry is solidified, remove the clay or the plasticine layer. The clay or the plasticine on the clay prototype should be cleaned for the guarantee of the mold surface quality.
Silicone rubber pouring
Calculate the volume of silicone rubber to be mixed according to the volume of clay layer, and add a certain loss to mix silicone rubber. After the silicone rubber is mixed evenly, put it into the vacuum pumping device to eliminate the bubbles in the silicone rubber. After the deaeration, carry out the pouring of the silicone rubber.
Silicone rubber solidification
Solidifying the teemed silicone rubber mold at room temperature or heat, taking out the prototype and continue to solidify the silicone rubber at room temperature or by heating till the silicone rubber does not stick.
Modification
After taking out the prototype, if there are some mild defects are found in the mold, they can be repaired with newly prepared silicone rubber and solidified. This is a resin product made by vacuum casting with economical silicone rubber mold.
Arc spray molding
The fundamental procedure is to atomize the molten the metal and spray it on the substrate at a high-speed. The shape of the workpiece should be corresponded to the substrate. It is a manufacturing method integrating material preparation and forming. The initial idea of arc spraying mold is to apply a certain thickness of metal coating on the prototype of plastic products, wood, was, gypsum and other models by spraying. After that, remove the coating from the substrate for a replicable original mold cavity. The technology is known for its simple molding process, short manufacturing cycle and low mold cost, especially for small batch and multi variety manufacturing. The process of the arc spraying can be divided into five steps:
Model preparation
Clean the model surface and apply the mold release agent, the model can be made by different materials, including wood, plastic, gypsum, rubber, etc. The important phase of the model preparation is that applying the mold release agent. The mold release agent functioned as a connecter which connects the metal grains on the substrate to prevent them from peeling. Besides, it also plays a role in the insulation and de-moulding by preventing the model being deformed, adhered on the wall, and even damaged by high temperature due to the metal coating. Applying the mold release agent evenly on the mold surface, and waiting it to dry to form a film.
Metal spraying
After the mold release agent is fully dry, starts to spray the metal on the model with taking the reference of the optimal spraying coefficient. The operator should ensure a continuous movement of spray gun to prevent the thermal deformation of the coating. The thickness of the coating can be controlled within 2-3mm.
Mold frame fabrication
If the mold bears the internal pressure in working or the mold must be installed on the forming machine, the mold must be equipped with bone structure and this structure should be with feeding material. There are two sides that need to pay attention in the fabrication of the mold frame. The first is to match the mold frame material with the thermal expansion performance of coating material and filler. The second is the specific model of the injection molding machine determines the overall dimension of the frame and the selection of the injection port.
Material filling
The mold is required to own good thermal conductivity and heat dissipation capacity in the plastic products production, so the selected filling material should be with high thermal condition rate and lower solidification shrinkage. Meanwhile, the filling material should have higher specific strength and wear resistance to allow the mold to work under a certain temperature and pressures. The typical material selections for the filling are the mixture of epoxy resin, aluminum powder, aluminum particles and other metal powders. The epoxy resin sprays the shell and the framework has a strong bonding strength. Colored metal powder can increase the thermal conduction performance of molds. Also, adding the iron powder enhances the wear resistance of molds. Cooling tubes are necessary in teeming since it can increase the thermal dissipation of molds.
De-moulding processing
The mold release process would be easy with a sufficient preparation. After releasing the mold, cleaning the residual mold release agent on the metal surface up and then start polishing and other post treatments according to the needs. Place the parting surface of the upper and lower mold on the bottom plate and brush a layer of mold release agent evenly on the mold surface. After the mold release agent is formed into a film, spraying and painting metal till meeting up the thickness requirement. Properly placing the prepared metal frame. Make sure that the frame and bottom plate must be sealed so that no leakage when filling materials. After the liquid is solidified, reverse the half mold and remove the base plate and plastic materials.
Advantages of molding technology
The arc spraying molding technology has advantages include:
(1) No matter what type of material of the mold made, metal, wood, or plastic, the obtained mold cavity must have a clear contour with no changeable outer dimension. As the surface temperature is no more than 60 degrees in painting, there is no thermal stress and deformation issue.
(2) High molding efficiency and no limitation on dimension. The size could be as small as a coin or as large as a vacuum forming die for automobile inner roof.
(3) Low equipment investment with high profit, allowing the plastic production line to replace the type of products, which meet the needs of market.
(4) Edges of cost are remarkable. Compared to other methods, the cost of this method can be saved by 2-20 times. This is an arc spraying equipment. It is composed of arc spraying gun, wire feeding mechanism, oil-water separator, cooling equipment, air compressor and spraying power supply.
Basic structure
Basic structure of the arc spraying molding includes three parts, which are metal spraying layer, backing layer, and steel structure. In terms of the zinc alloy molds, the spraying and painting of the mold are composed of the zinc alloy. In spraying, the zinc alloy lines are being melt and then atomized by compressed gas to form metal droplets. The droplets impact the surface of the transition mold, solidifies, and forms a hard and dense metal shell, which forms the surface of the mold cavity, and the thickness is 2~3mm. Even though the sprayed layer owns high strength, hardness, surface roughness and good thermal conductivity, and can accurately copy the shape of the prototype, it still cannot bear the forming pressure itself due to its thin thickness. Thus, it cannot be used as the a mold and must be backed up. The backing layer is mainly used to support and increase strength. Common backing materials include resin sand, epoxy resin, alloys with low melting point, etc. The mold release agent is versatile. First is that the film release agent can provide a reliable bonding surface between the sprayed metal droplets and the model surface, so that the sprayed metal droplets can be smoothly deposits on the model surface as it is hard for the metal particles to adhere on a smooth surface when spraying. Second is the release agent separate the coating layer and model base smoothly. Besides, the mold release agent is effective in the thermal insulation. Main requirements for mold release agent are: low surface tension and good film-forming performance. It should be easy to spread evenly on the surface of the original mold. In addition, the mold release agent must be cleaned from the original mold and coating. Common mold release agents include zinc stearate, liquid paraffin, silicone oil, polyvinyl alcohol, etc. The polyvinyl alcohol is the optimal choice for arc spraying molding process, whereas the zinc stearate, liquid paraffin, silicone oil and other mold release agents are not suggested for arc spraying process.
Epoxy molding
The rapid molding of epoxy resin is a mold manufacturing method that adopts the metal pouring method to inject the prepared raw materials (the resin is uniformly mixed with additives) into a mold cavity to solidify (complete the polymerization or polycondensation reaction). The epoxy resin rapid mold is a static pouring that is processed under the conditions of room temperature and normal pressure. After the solidification, there is no or only a small amount of cutting, and only minor external shape modification is required according to the mold conditions. Unlike the traditional metal mold making, requiring high-precision equipment for machining, the rapid mold making method of pouring special resin directly on the rapid prototype mother mold significantly saves the time and cost of mold making.
model preparation. When the prototype is used for making the mold model, one must consider some specific manufacturing issues like the material contraction in the part manufacturing. Thus, the shape and dimension of the prototype should be modified for the deformation due to the material contraction. Another issue is determined by the molding method. The rapid prototype used for making the epoxy mold should has a certain draft angle.
(2) The fabrication of the base and the practice to fix the prototype base should be in align with the model and its parting face. The base can be made of materials that are easy to carve, like wood, metal, plastic, glass, gypsum, and even the fire clay.
(3) the mold release agent should as thin as possible and should be applied by 2~3 times evenly. However, some metal frames and inserts functioned as a strengthening part should not be applied mold release agent. Moreover, to better connect the epoxy resin with the mold release agent together, sometimes we need to polish its surface or regarded it as the insert structure. Mixing the epoxy resin, hardener, filling, and adhered metal powder uniformly, then stirring it carefully to prevent the gas trapping. The vacuum mixer is useful in the prevention of air trapping.
(4) maintain an equal speed when pouring the resin and to make the epoxy resin mixture enter the mold frame from the bottom point as far as possible. Establish another mold frame and spray the mold release agent. During the same process, finish the pouring for the other half of the mold.
(5) remove the base and start the fabricate of the other half of he mold till the resin mixture is almost solidified. Reversing the mold carefully and remove the base. Establishing the frame of the other half of the mold and spray the mold release agent. Adopting the same method to process the other half of the mold.
(6)resin solidification and mold release. After the resin is completely solidified, move the frame and place the upper and lower mold into the post-treatment furnace to heat and preserve the heat. The solidification of the epoxy resin will be processed under a certain pressure. Based on the practice, solidifying under pressure will avoid the air holes occurrence, and enhancing the compactness of material, accuracy of mold, and surface finishing. Due to the low mechanical properties of UV curable resin and hollow structure made products (to increase the production rates and save resin), the pressure should not be too hight. The temperature should be lower than 60 degrees, as the glass transition temperature of UV curable resin materials is generally between 60 ℃ and 80 ℃. When the epoxy resin is fully solidified, adopts the ejector rod or special mold lifting device to take the prototype out from the resin mold.
(7)mold modification and assembly. If there are little defects on the epoxy resin mold, the defects can be modified manually and then the mold can be assembled with standard or pre-designed and processed mold frame to complete the epoxy resin mold fabrication and deliver the products for use.
Try GREFEE now,for free
We keep your uploaded files confidential and secure.