Purpose of mold testingprior to mold manufacturing and delivery

Posted on : July 9 , 2022 By GREFEE
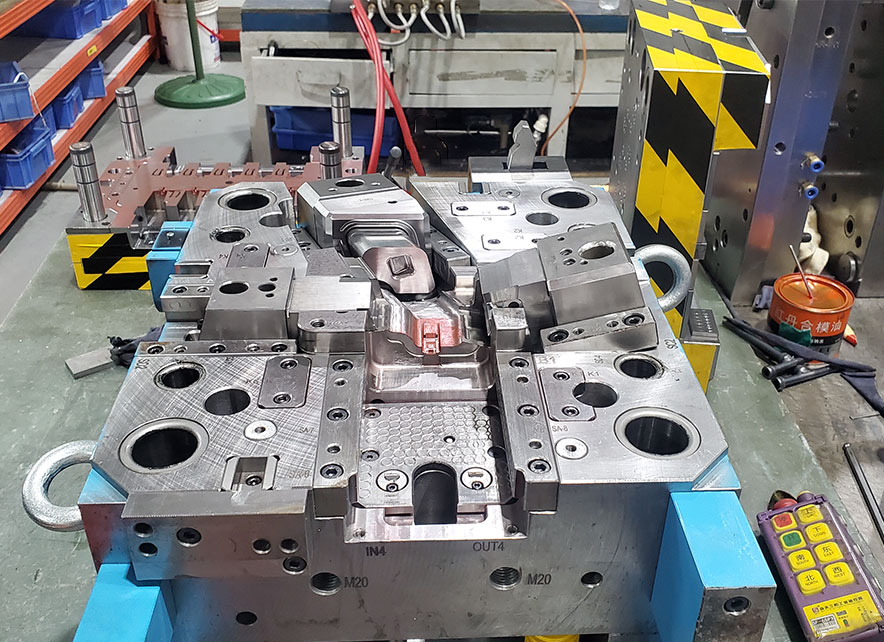
Purpose of mold testing prior to mold manufacturing and delivery
Checking whether the injection mold, product structure, plastic raw materials and color masterbatch (toner) meet the requirements of development and design to ensure the mass production processing effectively. This article mainly focuses on the injection mold.
Range
Applicable to injection molding production and manufacturing, injection molding technician, and injection molding rack technician for mold trial operation.
Responsibilities
Organize and coordinate the relevant agendas of mold trial according to the requirements, including the upper and lower mold, process commissioning as required, mold problems detection, product structure, plastic raw materials, color masterbatch (toner), and strive to fix the issues from the perspective of technology, and feedback the existing problems to the relevant departments (development department or purchasing department).
Instruction
Dos and Don’ts before the trail mold.
1. Understand the relevant data
Before the mold trial, the mold design manufacturers should obtain the mold design drawings, mold instructions and other relevant data. Processing the analyzation and assigned the duty to the specified repair team to participate in the mold test.
2. Inspect the mechanical cooperation action first on the worktop:
Defects like scratches, missing parts, looseness and other phenomena, whether the action of the die to the sliding plate is correct, whether there are leaks at the water and gas pipe joints should be recorded and report in time. Restrictions on the mold opening stroke should also be marked on the mold. Completing the above actions before hanging the mold can help avoid the waste of labor time caused by disassembling the mold after the problem is found after hanging the mold.
3. After the action of each part of the mold is appropriately set, we can start to select a proper injection molding machine for mold trail, and pay attention to the following aspects:
① Injection capacity ② width of guide rod ③ maximum opening distance ④ whether accessories are complete.
After everything is assured, the next step is to hang the mold. During hanging, be aware that not to remove the hook before locking all clamping templates and opening the mold. The reason for this is to avoid loosening or fracture of clamping templates and falling of the mold. After the mold is installed, double check the mechanical actions of each part of the mold carefully, like the sliding plate, thimble, tooth retraction structure and limit switch. Pay attention to whether the injection nozzle is aligned with the feed inlet.
The next step is the mold closing action observation. At this time, the mold closing pressure should be reduced. During the manual and low-speed mold closing action, pay attention to whether there is any unsmooth action and abnormal sound.
4. In the mold trial, pay attention to the mold temperature. However, it is the hardest to control the mold temperature during short-term mold trail and the future mass production. However, the incorrect mold temperature also impacts the sample size, brightness, shrinkage, flow lines and material shortage. If work without using the mold temperature machine, it is hard in the future mass production.
5. Increase mold temperature appropriately:
Selecting the correct mold temperature machine to increase the mold temperature to the level for the mold manufacturing according to the property of the raw material and size of the mold, like the plastic mold manufacturing. The processing temperature varies according to the material properties. After the mold temperature is ready, double check the action of each part to avoid the stuck issue due to the thermal inflation. Therefore, pay attention to the slide action of each part to in case the strain and trembling.
6. Only one condition can be adjusted at a time when adjusting the mold test conditions to distinguish the impact of a single condition change on the finished product.
7. The raw materials used should be properly baked according to different raw materials.
8.Try to use the same raw materials for the trial mold and mass production in the future.
9. Do not try the mold completely with secondary materials. If there is a color demand, you can arrange the color test together.
Major steps for mold trail
To avoid the waste of time and other matters, it is necessary to cost a lot of energy to adjust and control each processing conditions to find the optimal woking temperature and pressure conditions.
1. Check whether the plastic in the barrel is correct, and whether it is baked according to the regulations (different results may be obtained if different raw materials are used for mold trial and production).
2.The material pipe should be thoroughly cleaned to prevent the degraded rubber or impurities from entering the mold, for the degraded rubber and impurities may block the mold. Start test the temperature of the material pipe and the temperature of the mold to see if they are suitable for the processed raw materials.
3. After the mold is closed slowly, the mold closing pressure should be adjusted and operated for several times to check whether there is uneven mold closing pressure to avoid burrs and mold deformation.
4. After the above steps are checked, the safety buckle and jacking stroke should be decided.
5. If the limit switch of the maximum stroke is involved, the mold opening stroke should be adjusted to be a little shorter, and the high-speed mold opening action should be cut off before the maximum stroke since the high-speed action travel is longer than the low-speed action travel in the whole mold opening stroke during mold installation.
6. Thinks need to inspected before the first mold injection
① Whether the feeding stroke is too long or insufficient;
② Whether the pressure is too high or too low;
③ Whether the mold filling speed is too fast or too slow;
④ Whether the processing cycle is too long or too short.
⑤ Know clearly about the cavity structure features, deep cavity structure or the mold sticking possibilities in the mold with complex structures. Spraying an appropriate amount of mold release agent before the test to avoid the mold sticking or other production issues, like crack, deformation, burrs or short injection. If the production cycle is short, the ejector pin would push through the finished product or strip the ring to crush the products. If it is a long production cycle, the thin and weak parts of the mold core may be broken due to the shrinkage of the rubber. These situations might cost you two to three hours to fix. Comprehensive consideration and timely measurements should be taken before the operation to avoid the cost loss and server issues.
7. Adjust the pressure and injection volume for products with high quality and great appearance. However, do not trim the burrs, especially when some mold cavity have not yet fully solidified. Take a comprehensive consideration before adjusting the control conditions as a small change in mold filling rate would lead to a big mold filling change.
8. Wait patiently until the conditions of the machine and mold are ready, which is generally more than 10 minutes. This period of time can be used to check the possible problems of the finished product.
9. The time of the screw forge ahead should not be shorter than the solidification time of the gate plastic, otherwise the weight of the end product will be reduced and the performance of the end product will be shrunk. When the mold is heated, the forge ahead time of the screw should also be extend to fully compress the end products.
10. Adjust and reduce the overall processing cycle appropriately
11. Wait about 10 mins till the new conditions operated smoothly and then produce a full mold product at least. After that, mark the date, quantity on the mold, and displace them according to the mold cavity to test its operation stability and obtain an appropriate control tolerance, especially for multi cavity mold.
12. Record the continual product measurement and the important dimension (start measuring till the samples cooling to the room temperature)
13. Make a comparison of each sample, be aware that.
①Whether the dimension is stable
② Whether there is an increasing or decreasing trend in some dimensions, which indicates that the machining conditions are still changing, such as poor temperature control or oil pressure control.
③Whether the dimension change is within the tolerance range
14. The If there is no change in the size of the end product and the processing conditions are normal, it is necessary to ensure the quality of the end product from each cavity is qualified, and its size is within the allowable tolerance. Recording the mold hole number measured continuously, or those that are higher or lower than the average value to check the correctness of the mold dimension.
15. Record and analyze the data for the mold modification and production conditions, which would be taken as the reference for the future mass production.
16. Adjust the machine conditions according to the size of the end product. Increasing the size of the gate when there is a too large shrinkage or sufficient injection material
17. The size of each cavity should be modified if they are too large or small. If the cavity and gate are in the correct size, we should try to change the machine conditions, such as the mold filling rates, mold temperature, and the stress on each part. What’s more, the cavity filling speed can also be regarded as a factor to evaluate.
18. Perform modification according to the matching condition of each mold cavity of the end product or mold core displacement, or to re-adjust the mold filling rate and mold temperature to improve its uniformity.
19. Check and modify the problematic ejector, such as the oil pump and valve, temperature controller (barrel temperature, drying temperature, mold temperature) and other parts, which might lead to changes in processing conditions. Even the most perfect mold can not promise a great work efficiency under the poor maintenance of the machine.
20. After all the values are recorded, keep a set of samples for checking and comparing whether if there are any improvement.
21. When the mold or raw materials and color masterbatch (toner) are unqualified, the unqualified sample must be retained. Last but not the least, the sample must can effectively reflect the problem of the mold or raw materials and color masterbatch (toner).
22. Requirements for filling the mold test report form:
① Weigh the unit weight of product and gate weight, weigh at least 10 pieces of small products to take the average value, and fill the form;
② Fill in the data in the injection molding process, such as raw material drying, barrel temperature, hot runner temperature, mold temperature adjustment process, mold unlocking, neutron, glue injection, pressure maintaining, glue melting, loosening, mold supporting, operation mode, cooling and cycle time. What’s more, fill the operation instruction separately to record the injection molding process in more detail if needed, which means to save all the data that is necessary for successfully establishing a same processing conditions to further obtain products that are in align with the quality standards.
③ Record problems that are detected in the mold, raw materials and color masterbatch (toner);
④ Keep the test mold samples and quantity as required with labels on. Put them in a separate packing box and place them in the designated area.
⑤ The mold tester must sign the report, keeping the mold test report form and filing it
23. Clean the grease and other dirts on the product during the mold test, and mark them for the pulverizer and material management.
MORE BOLG
Insert mold in injection mold service
What are advantages and disadvantages of Zinc alloy and Aluminum alloy?
Inspection standards for injection molded partappearance
How to judge the quality of your plastic products?
Inspection standards for CNC machining
To ensure that your products are 100% qualified
Categories
Try GREFEE now,for free
We keep your uploaded files confidential and secure.