Precision injection molding solutions

Posted on : Aug 15 , 2022 By GREFEE
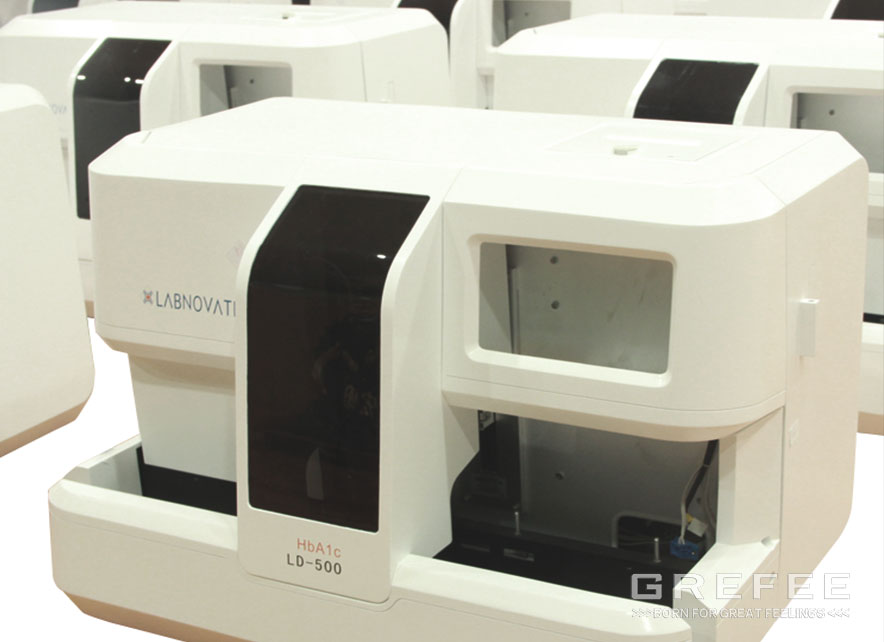
What is precision injection molding?
The high precision injection molding refers to an injection molding method of which the dimensional repetition accuracy of the injection molding parts is very high, resulting in hard to achieve the requirements with general injection molding machine and ordinary injection molding processing. What distinguishes the high precision injection molding from the ordinary injection molding is that the technology of using precision plastic parts to replace high-precision metal parts in the field of instruments and electronics.
Currently, there are two standards in terms of the high precision injection molding products, which are the repetition accuracy of dimension and repetition accuracy of the products’ quality respectively. However, due to the difference of the property and processing techniques of each kind of material, the accuracy of the plastic parts and metal parts are not the same thing. The precision injection molding is a technique that involves comprehensive technology of raw material performance, formula, molding process and equipment.
For products like digital camera parts, computer connectors, light guide plates, aspheric lenses and other precision products, of which the remarkable characteristics is not only the high dimension accuracy, but also the inner quality of products and the yield requirements. The injection molding molds of the molding products determine whether the products meet the dimension errors of design requirements or not, whereas the precision injection machines promise the products are formed accurately within the dimension molding range and higher yield rates.
The highest accuracy level of plastic products is level 3.
1. Characteristics of precision injection
(1). There is a high-precision dimensional limit. The dimensional accuracy of the workpiece is high and the tolerance is small.
(2) .The weight repetition accuracy of products is high, requiring the dimensional stability of day, month and year.
(3) .Good material of the injection mold, which is rigid enough, and the dimensional accuracy, smoothness of the cavity and the positioning accuracy between the templates are high.
(4) .Replace conventional injection machine with precision injection machine.
(5) .Adopt precision injection molding process;
(6). Select materials suits the precision injection molding.
The most crucial technical index for evaluating products is the accuracy of injection molded parts (dimensional tolerance, geometric tolerance, and product surface finish). Precision plastic products should be strictly controlled by four factors: which are material selection, the mold design of injection parts, the molding process of injection parts, and the technical level of operators. The dimensional accuracy of products is generally within 0.01 ~ 0.001mm to meet the requirements of the precision injection molding machines.
Other than those this, it also requires high injection pressure and high injection speed, as well as the clamping system for enough rigidity and high clamping precision. The so-called clamping precision means the uniformity, adjustability, stability, repeatability of clamping force, and the precision of opening and closing position with the need of pressure, flow, temperature, measurement, and other factors so that it can be accurately controlled to the corresponding accuracy. The multi-stage or non-stage injection required is to ensure the reproduction conditions of the molding process and the repetition accuracy of the product size.
2. Factors affecting the dimensional accuracy of products
(1) .Precision of injection mold.
(2) .Molding shrinkage.
(3). The temperature, humidity and fluctuation range of the environment in which the product requires.
The selection principle of precision molding materials for injection molded parts is to choose materials with high mechanical strength, good dimensional stability, good creep resistance, and wide environmental adaptability. Four commonly used materials here include:
(1).POM and carbon fiber reinforced (CF) or glass reinforced (GF), which is characterized by good creep resistance, fatigue resistance, weather resistance, good dielectric properties, fire resistance, and easy to de-mold with lubricant.
(2).PA and glass fiber reinforced PA66 are characterized by strong impact and wear resistance, good flowability, and can produce products with a wall thickness of 0.4mm. Glass fiber reinforced PA66 has good heat resistance (melting point 250 ℃), but the disadvantage is that it has hygroscopicity. Generally, humidity regulation is required after molding.
The molding time of PBT reinforced polyester is short. The comparison of forming time is as follows: PBT ≤ POM ≈ PA66 ≤ PA6. (4) PC and GFPC features include good wear resistance, increased rigidity after reinforcement, good dimensional stability, good weather resistance, fire resistance, and molding processability.
Four factors affecting shrinkage: in precision injection molding include thermal shrinkage, phase change shrinkage, orientation shrinkage, and compression shrinkage.
(1). Thermal shrinkage is the inherent thermophysical property of molding materials and injection mold materials. The mold temperature of injection molded parts and products is high, so the actual shrinkage will increase. Therefore, the mold temperature of injection molded parts for precision injection should not be too high.
(2). Phase change shrinkage is caused by the reduction of specific volume due to the crystallization of polymer during the orientation of crystalline resin. The injection molding parts have high temperature, high crystallinity, and high shrinkage. On the other hand, the increase in crystallinity will increase the density of products, and reduce the coefficient of linear expansion and the shrinkage rate, which are two key elements of the actual shrinkage.
(3). Orientation contraction: since the molecular chain is forced stretched in the flow direction, the macromolecules will have a tendency to re-curl and recover when cooled, and shrinkage will occur in the orientation direction. The degree of molecular orientation is related to injection pressure, injection speed, resin temperature, and injection mold temperature. The injection speed is the primary element.
(4). Compression shrinkage and elastic reset, most plastics have compressibility, which indicates that their specific volume changes significantly under high pressure. if it is under the normal temperature, the specific volume of pressure molded products will reduce, the density will increase, the expansion coefficient will decrease, and the shrinkage will decrease significantly. In terms of the compressibility, the molding material has the function of elastic reset, which reduces the shrinkage of the product. The factors affecting the molding shrinkage of products are related to the molding conditions and operating conditions.
Precision injection mold
(1). The accuracy of injection mold mainly determines by whether the mold cavity size accuracy of injection mold is high, the cavity positioning accuracy or the parting surface accuracy meets the requirements. Typically, the dimensional tolerance of the injection mold of precision injection molding parts should be controlled lower than 1/3 of the dimensional tolerance of the product.
(2). Process performance and rigidity
In the mold structure design of the injection molding parts, the number of the mold cavity should not be too much. However, the bottom plate, supporting plate, mold cavity should be thicker to avoid server elastic deformation under high temperature and high pressure.
(3). The mold release performance of products
The number of the mold cavity and runners of the injection molding parts should be as less as possible, and should be with higher glossy for ordinary injection molding molds, which is advantageous for mold releasing.
(4). Alloy steel with high mechanical strength is the optimal choice for the precision injection mold. The materials used to make the cavity and sprue should be subject to strict heat treatment, and the materials with high hardness (the molding parts should be about hrc52), good wear resistance and strong corrosion resistance are suggested.
Characteristics and selection of precision injection machine
1. The characteristics of technical parameters are divided from the injection pressure, which are ordinary machine: 147 ~ 177mpa, precision machine: 216 ~ 243mpa, ultra high pressure machine: 243 ~ 392 MPa.
Why the precision injection molding machine should be under high pressure:
(1) .The increase of the accuracy, quality and the injection pressure of the precision products impacts the shrinkage of products significantly.
(2) .It reduces the wall thickness of precision products and improves the molding length. Taking PC as an example, ordinary machine can produce products with a wall thickness of 0.2 ~ 0.8mm with an injection pressure of 177 Mpa, while precision machine can produce products with a thickness of 0.15 ~ 0.6mm with an injection pressure of 392 Mpa, the ultra high pressure injection machine can get products with larger flow length ratio.
(4).The increase of the injection pressure can fully stimulate the effect of the injection rate. There are only two ways to achieve the rated injection rate which are to increase the maximum injection pressure of the system, and to reform the screw parameters and improve the length diameter ratio. Precision injection machine has a high injection rate. Taking DEMAG precision injection molding machine (60 ~ 420 tons) made in Germany as an example, of which the injection speed can reach 1000mm/s, and the screw can obtain an acceleration of 12m/s2.
2. Characteristics of precision injection machine in control
(1). It has a requirement in the repetition accuracy (reproducibility) of molding parameters of injection molded parts, so the multi-level injection feedback control is suitable.
a. Multi level position control.
b. Multistage speed control.
c. Multistage pressure maintaining control.
d. Multi stage back pressure control.
e. Control of multi-stage screw speed. The accuracy of the displacement sensor should be 0.1mm, for strictly controlling the metering stroke, injection stroke and the thickness of the residual pad (injection monitoring point) to ensure the accuracy of each injection volume and improve the molding accuracy. An accurate temperature control of the barrel and nozzle is required. In addition, the overshoot and the temperature fluctuation should be small when heating up. PID control is suitable for precision injection molded parts to make the temperature accuracy within ± 0.5 ℃.
(2). Plasticization quality requirements.
The uniformity of plastic not only affects the molding quality of the injection molding parts, but also affects the resistance of molten plastic when it passes through the gates. The design of specific screw bar and the use of plasticization technology are necessary to obtain uniform plasticization. Besides, the control of the temperature of barrel should be paid attention to. Most of the screw and barrel temperature are controlled by PID (proportion, differentiation and integration), and the accuracy can be controlled within ±l℃, which can basically meet the requirements of precision injection molding parts. Compared to the PID, the control method, FUZZY is more suitable for precision injection molding parts.
(3) .The temperature control of working oil
It shows that the change of high oil temperature leads to the fluctuation of injection pressure, so the closed-loop device of heating and cooling must be used for working oil to maintain the oil temperature at 50 ~ 55 ℃.
(4) .Influence of holding pressure
The holding pressure impacts hugely to the precision injection molding parts. Accurately speaking, holding pressure can effectively feed, reduce the deformation of plastic parts, control the accuracy of plastic parts. The stability of holding pressure determines the molding accuracy of plastic parts, and the constant end position of screw is the main factor for the effect of the hold pressure.
(5) .For the temperature control of injection mold
If the cooling time is the same, the thickness of products with low mold cavity temperature is larger than that of products with high temperature. For instance, when the mold temperature is 50 ℃ μ M, the thickness of the POM and PA materials is 50 ~ 100, and then reduced to 20 ~ 40 at 80 ℃ μ m. when it is reduced to only 10 at 100 ℃ μ M, the room temperature also affects the dimensional tolerance of precision products.
3. Hydraulic system of precision injection molding machine
(1) The oil circuit system should adopt the proportional system of proportional pressure valve, proportional flow valve or servo variable pump.
(2) In the direct pressure clamping mechanism, separate the oil circuit of the clamping part and the injection part.
(3)Due to the high speed of precision injection molding machine, the reaction speed of the hydraulic system needs to be stressed.
(4)The hydraulic system of precision injection molding parts should fully demonstrate the mechanical —electric—hydraulic — instrument, integration project.
4 .Structural characteristics of precision injection molding machine
(1). Due to the high injection pressure of the precision injection molding machine, the rigidity of the clamping system should be paid attention to. The parallelism control of the moving and fixing mold should be within 0.05~0.08mm.
(2) .Protection of molds of low pressure injection molded parts and control of the mold claiming accuracy are required since the clamping force affects the degree of the mold deformation, which further affects the dimension tolerance of the parts.
(3).The mold opening and closing speed should be fast, usually at 60mm/s.
(4). Plasticizing parts: screw, screw head, check ring, barrel, and other plasticizing parts. should be designed into a structural form with strong plasticizing ability, good homogenization degree and high injection efficiency. The driving torque of the screw should be large and non-stage speed change can be achieved. Conclusion: no matter what kind of precision injection molding machine, stably control the dimensional repetition accuracy and quality repetition accuracy of products is essential.
6. The main representative models of precision injection machines.
The injection molding parts processors that can represent the world’s advanced level of production of the development of precision injection molding machines are mainly Klaus mafi, Demag, Yabao, aberg in Germany, and injection molding parts processing plants such as Nissei, Nippon Steel, Toshiba machinery and Sumitomo heavy machinery in Japan. The clamping mechanism of the precision injection machine introduced by Germany’s ABERG adopts the box design to improve accuracy of mold clamping. Since the front and rear plates of the three-plate injection machine are fixed on the frame, the extension of the four drawbars is limited by the frame when applies the clamping force, so that the drawbars tend to “arch bridge shape” and affect the clamping accuracy. The result of the box sample design improves the clamping accuracy from limiting the deformation.
The adoption of bidirectional pressure servo control to accurately position the screw position of the injection cylinder doubles the injection volume control accuracy. Optimizing the control of main pump motor with the frequency converter not only improves the control accuracy of hydraulic system, but also saves energy significantly. In addition, the modular design allows that the motion systems of the injection molding machine can adopt the combination of hydraulic and electric according to the actual needs of users. The injection system can also have a variety of configurations if utilize the space relative positions of the mold locking system.
The precision injection molding inc, like the Nissei Eco. Co adopts the new control system TACT to increase the responding speed and stability of operations. In addition, a multi language control interface is displayed by LCD. New injection mechanism includes the increase the length diameter ratio of the screw to enhance the plasticizing effect. They also optimized the plasticizing temperature control in five temperature zones, and developed new hydraulic FN series precision injection molding machine, as well as the hydraulic small precision plastic injection molding machine NP7RealMini, au3e, as15 and other models.
The main processing materials of this precision plastic injection molding machine are the liquid crystal polymer (LCP), polyamide (PA), polyphenylene sulfide (PPS) and other engineering plastics, and other engineering plastics. The Nissei NEX 150 precision injection molding machines combine the ultimate micro injection molding technology, which can be used for molding and processing of small precision plastic parts with large quantities of injection molded parts. It is equipped with the design of precise metering, rapid response injection system, high precision and high rigidity that is optimized, which can process precision micro plastic parts weighing 0.1 ~ 0.3g are used for digital cameras, mobile phones, hard disks, fine pinhole connectors, etc.
The ultra-high speed precision injection molding machine J-ELII-UPS was developed by the Japan Steel Institute. Under the standard conditions of holding pressure, the change of the weight of products is about 0.022 gram. After adopting the new pressure holding control means, the change of the weight of products will reduce to 0.006 gram.
MORE BOLG
Insert mold in injection mold service
What are advantages and disadvantages of Zinc alloy and Aluminum alloy?
Inspection standards for injection molded partappearance
How to judge the quality of your plastic products?
Inspection standards for CNC machining
To ensure that your products are 100% qualified
Categories
Try GREFEE now,for free
We keep your uploaded files confidential and secure.