Reduce CNC Cost, Start from the Design.

Posted on : May 23, 2022 By GREFEE
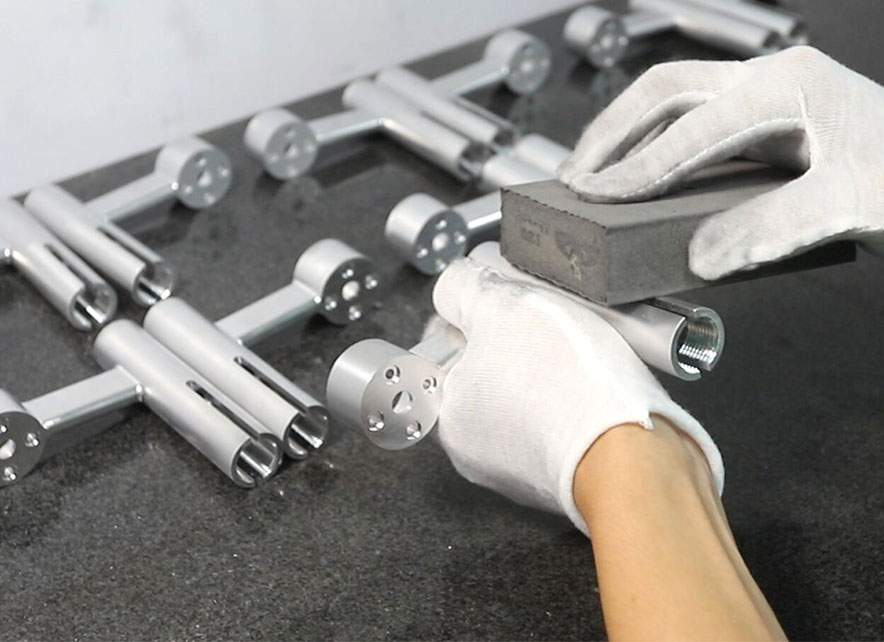
Concerning CNC machining, whether it is a single prototype or mass volume production, lowering the manufacturing cost is the priority. The designer has a huge influence on the final price. By following the feasible machining skills mentioned in the article, you can obtain parts that see your design requirements with the lowest cost and have been optimized. GREFEE has many years of experience in CNC parts design and machining. Try our CNC service to start your new project.
What affect the cost of CNC parts?
The cost of CNC machining parts are determined by these:
Machining time: the longer the machining process, the higher the price.In CNC, machining time is the major cost.
Start-up costs: These are related to the preparations of CAD files and processing plan, which has a great significance for small batch production. This is a fixed cost, but it has the opportunity to lower it through the “Economies of scale”.
Material cost: how difficult the material cost and processing are has a great impact on the overall cost. Optimize the design when considering some factors about the material to reduce the cost effectively.
Other manufacturing costs: when you design parts with special requirements (such as defining the strict tolerance or designing a thin wall), you might need special tools, more strict quality control, and more machining steps to slow down the machining speed. Indeed, it will affect the overall manufacturing time and price.
Now, you are clear about the source of the CNC cost. Let’s take a look how to optimize the design to minimize the cost.
Tip 1: add the radium on the internal vertical edges
All the CNC milling tools have cylindrical shape and will generate a radius when milling the mold cavity edges.
Using tools with a small radius can reduce the corner radius. This means we need to carry out multi-time feed at a low speed —— small tools cannot remove the material in one feed quicker than big tools —— add the machining time and cost
Minimize costs:
- Add a radius of at least 1/3 of the cavity depth (the larger the better).
- It is better to use the same radius at all the internal edges.
- At the bottom of the mold cavity, spicy a small radius (0.5 or 1mm) or no radius at all.
- Ideally, the corner radius should be slightly larger than the tool radius used to process the cavity. This will reduce the load on the tools and further lower the cost. For instance, if your design has a 12mm deep cavity, add a radius of 5mm (or larger) at the corner, which will allow ø8 mm tools (R=4mm) to cut them faster.
Tip 2: limit the depth of cavity
If needs internal edges with sharp corners (such as when putting the rectangular part into the cavity), use shapes with the undercuts rather than reduce the radius of the inner edges. Shown as below:
The processing of deep cavity will affect the cost of CNC parts significantly because it will consume a large amount of time due to a quantity of material removal.
It is necessary to remember that the cutting length of the CNC tools is limited: generally, when the cutting depth reaches 2-3 times that of its diameter, its working efficiency is the best. For instance: a ø12 milling tool can cut a 25mm deep cavity safely.
It can cut deep cavities (as high as four times that tool diameter or more). However, it will increase the cots due to the need for specific tools or a multi-axis CNC system.
Besides, when cutting the mold cavity, the tools must be drafted to a correct cutting depth. A smooth entrance must need enough space.
minimize cost:
Set the depth of all the empty cavities as the 4 times of the length.
Tip 3: enhance the wall thickness
Unless the weight is a major factor, the solid section is more stable (lower machining cost), which should be the first choice.
To avoid the deformation or cracks in processing thin walls, it needs to carry out multi-feed at a low cutting depth. The thin wall is also easy to vibrate. Thus, accurate machining is more challenging and will extend the machining time.
Minimize cost
- For metal parts, the designed wall thickness exceeds 0.8mm (the thicker, the better)
- For plastic parts, the thinnest wall thickness should be maintained over 1.5mm.
- The metal can be as thin as 0.5mm. Plastic is 1.0mm. However, the machinability of these characteristics should be based on specific situations.
Tip 4: limit the length of thread
- Due to the need for specific tools, specifying the threads that are longer than the necessary length might increase the cost of CNC machining.
- Please remember that thread length that exceeds 0.5 that of diameter will not facilitate the connection strength.
Minimize cost
Design a thread with the maximum length of 3 times the hole diameter.
For threads in blind holes, it is better to add an unthreaded length of at least 1/2 diameter.
Tip 5: design a standard size holes
- In CNC, using standard drills can process holes quickly and accurately. For non-standard sizes, it is necessary to use a machining hole with an end milling cutter, which will increase the cost.
- Besides, limiting all the hole’s depth to 4 times its diameter can make deeper holes (up to 10 times the diameter). It will raise the cost because it is hard to process.
Minimize cost:
For holes of which diameter is less than or equal to 10mm or over 0.5mm, design the diameter increment at 0.1mm.
When designing in inches, please use the traditional inch fraction or make a referral to this fraction inch dimension table of the drill tip.
A hole with a design length up to 4 times its diameter.
Tip 6: strict tolerance is required when necessary
- Strict tolerance will increase the cost of CNC because it enhances the processing time and needs to be checked manually. Only when necessary will it carry out strict tolerance.
- If there is no specific tolerance on the technical drawing, the part will use standard tolerance (+ 0.125mm or more) to process, which is adequate for most non-specific features.
The rigorous tolerance of the internal feature is hard to achieve. For example, when processing the cross holes and empty cavities, due to the deformation of the material, there might be some little defects on the edges (is called burrs). Parts with such features will need to inspect to remove burrs. These two signs of progress are all manually practiced (with low time efficiency), which raises the cost.
Minimize cost:
Specify more strict tolerance when necessary.
Specify single datum (such as the cross section of two lines) as the reference with tolerances dimensions.
On the technical drawing (such as flatness, straightness, roundness, and true position), using geometric dimensioning and tolerance dimensioning (GD &T) can reduce the cost of CNC machining. Since they are generally defined as a wide tolerance, they can be used effectively with advanced knowledge.
Tip 7: keep the number of machine settings to a minimum
Rotating or re-position parts will raise the cost because it is completed manually. Moreover, for complex geometrical shapes, it might need customized jigs, which further increases the costs. Especially for complex geometrical shapes, a multi-axis CNC system is needed, leading to cost increment.
Consider splitting the part in a geometrical shape that can be carried out by setting only once, connecting or welding them together by bolts, which is also applicable to deep cavity parts.
Minimize cost:
Design parts that can only be machined in one setting.
If this is impossible, please split the geometrical shapes into many parts for the following assembly.
Tip 8: avoid small features with high aspect ratio
- Small features with an aspect ratio of length, width, and height are easy to vibrate, so it is hard to machine accurately.
- To enhance their rigidity, we should connect it with the thicker wall or strengthen it with the support ribs (the number of ribs should be four: one on each side).
Minimize cost:
Design features with aspect ratio less than 4.
Add support structure or design the features on the wall of parts to enhance its strength.
Tip 9: delete all the texts and lettering
- Adding the texts on the surface of CNC machined parts will raise the cost because it needs extra time-consuming processing procedures to complete.
- Surface fine machining method. For example, silk printing or spray painting is cost-effective for adding texts on the CNC parts’ surface.
Minimize cost:
Delete all the texts and letters on the CNC machining parts.
If needs texts, letterings are much better than the embossed texts because the latter needs to remove more material.
Tip 10: consider the machinability of material
The machinability refers to how difficult it is to cut the material. The higher the machinability, the faster the CNC material machining speed, then the cost decreases.
The machinability of each type of material is determined by its physical properties. Typically, the softer a metal alloy is (with better elasticity), the easier it is to process.
Minimize cost:
If you can select between different materials, choose the one with better mechanical performance (especially the mass production)
Tip 11: consider the cost of bulk material
The cost of material is another factor that largely affects the cost of CNC machining parts.
Aluminum 6061 is the most economical material to manufacture metal prototypes because it combines low casting with excellent machinability.
Minimize cost:
Select material with low batch cost (especially small batch orders)
Tip 12: avoid (many) surface treatment
The surface treatment enhances the capability of CNC machining parts against poor conditions and improves their appearance. This also increases the cost.
The cost rose due to extra steps since it is required to carry out different surface treatments on the same part.
Minimize cost:
Select surface finishes after machining
Multi-surface treatment required only when necessary.
Tip 13: consider blank size
The size of the bank strip might affect the overall cost. For good accuracy, some material must be removed from all the edges of parts, which has a great impact on the material cost (especially for mass production orders). Based on the experience, the blank must be 3mm la
Minimize cost:
Design the parts of which the dimension is 3mm smaller than the standard blank.
Refer to the blank size table or large-scale material supplier catalog for reference.
MORE BOLG
Insert mold in injection mold service
What are advantages and disadvantages of Zinc alloy and Aluminum alloy?
Inspection standards for injection molded partappearance
How to judge the quality of your plastic products?
Inspection standards for CNC machining
To ensure that your products are 100% qualified
Categories
Try GREFEE now,for free
We keep your uploaded files confidential and secure.