Summary of properties of common plastic materials

Posted on : Sep 23 , 2022 By GREFEE
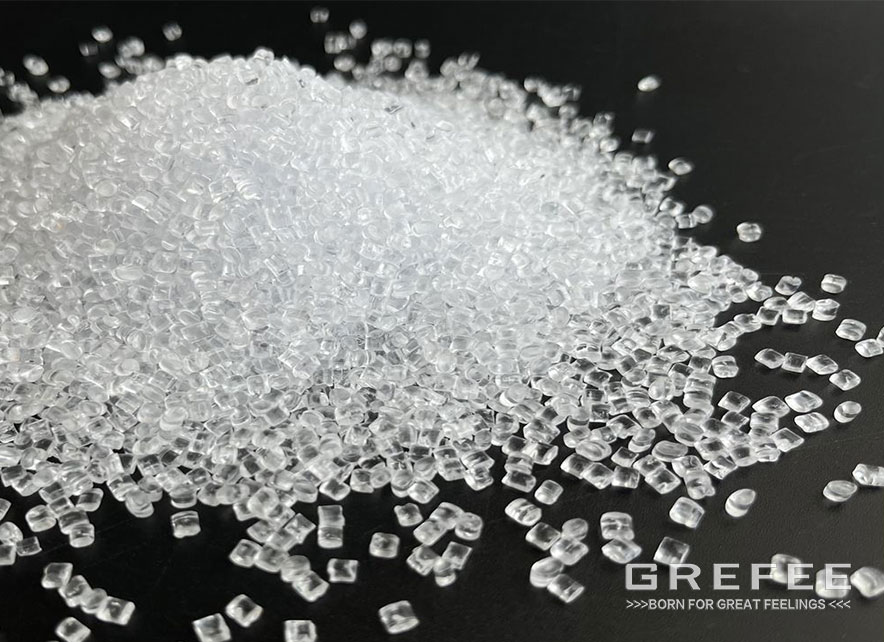
P S (polystyrene)
Function of PS
PS is a kind of amorphous polymer with good flowability and low water absorption (less than 00.2%), which is simple to form into clear plastic, of which the light transmittance is 88-92%. Its tinting strength and hardness are great. However, PS products are brittle and are easy to crack due to the internal stress. The thermal resistance is poor (60-80℃), non-toxic, with a specific gravity of about 1.04gcm3 (slightly larger than water).
Molding shrinkage (generally 0.004-0.007in / in), transparent PS —- which only refers the transparency of resin rather than the crystallinity (chemical and physical properties : most of the commercial PS are transparent and amorphous material.
PS is welcome due to its multiple advantages , which induce good geometric stability, thermal stability, optical transmission characteristics, electrical insulation characteristics, low moisture absorption, waterproof, and diluted inorganic acids. While the disadvantage of it is that easy to corroded by strong oxidizing acids, such as concentrated sulfuric acid, and can expand and deform in some organic solvents.)
Processing characteristics of PS
The processing indexes of PS are melting point (166℃), processing temperature (185-215℃), melting temperature (180~280℃). In terms of the flame retardant material, the temperature upper limit is 250℃, and decomposition temperature is about 290℃, so the processing temperature range of PS is wide.
Mold temperatuer is 40 ~ 50 ℃, injection pressure: 200 ~ 600bar. It is recommended that injection speed should be fast. The suggestion for runners and gates is that all general types of gates can be used.
Before processing, PS does not need drying treated unless it is improperly stored. If it needs, the conditions for drying would be 2-3 hours at 80 ℃. Due to the low specific heat of PS, after the heat dissipation, some molds can be condensed and solidified quickly, of which the cooling speed is faster than that of ordinary raw materials, and the mold opening time can be earlier. Its plasticity and cooling period are short, so its molding cycle could be reduced. The gloss of PS products will be better as the increase of temperature.
Typical application range:
Packaging products (containers, covers, bottles), disposable medical supplies, toys, cups, knives, tape reels, windproof windows and many foam products – egg boxes. Meat and poultry packaging plates, bottle labels and foamed PS cushioning materials, product packaging, household products (tableware, trays, etc.), electrical (transparent containers, light scattering devices, insulating films, etc.).
HIPS (modified polystyrene)
Performance of hips:
HIPS is the modified material of PS. The molecule of it contains 5-15% rubber composition, of which the rigidity is 4 times enhanced than that of PS. In addition, its impact strength has been increased significantly (High impact polystyrene). There are flame retardant grade, stress cracking resistance grade, high gloss grade, extremely high impact strength grade, glass fiber reinforced grade and low residual volatilization grade.
Other important properties of standard HIPS: bending strength 13.8 ~ 55.1mpa; tensile strength: 13.8-41.4mpa; elongation at break is 15-75%; Density 1.035-1.04 g / ml; It supports PS molding and has strong tinting power. HIPS products are opaque with low water absorption, and can be processed without pre drying.
Process characteristics of hips:
As there is 5-15% rubber in the molecules of HIPS, which affects the flowability, injection pressure, and molding temperature to some extent. Its cooling speed is slower than PS, so it requires sufficient pressure and time for holding pressure, and cooling time.
Its molding cycle would be longer than PS, of which the processing temperate is usually at 190-240℃. The water absorption rate of HIPS resin is slow, so it does not need to be dried. Sometimes, the outer appearance quality of products may be affected as the water on the surface of material would be absorbed.
The excess water can be removed by drying at 160 ° f for 2-3H. There is a special white edge issue among the HIPS products. Through increasing mold temperature and mold clapping force, reducing pressure of holding pressure and time to improve it, which causes the water mark in the product be more obvious.
Typical application range:
The main application fields of it include packaging and disposable products, instruments and meters, household appliances, toys and entertainment supplies, and construction industry. Flame retardant (UL V-0 and UL 5-V), impact resistant polystyrene has been produced and widely used in TV casings, commercial machines and electrical products.
SA (San — styrene acrylonitrile copolymer / Dali rubber)
Performance of SA
Chemical and physical performance: SA is a kind of hard and clear material, which is not easy to crack due to the internal stress. Its transparency is high and the soft temperate and impact strength is higher than PS. Styrene makes SA hard, transparent and easy to process; The acrylonitrile component makes SA have chemical stability and thermal stability.
SA has strong load bearing capacity, chemical reaction resistance, thermal deformation resistance and geometric stability. The strength and thermal deformation resistance of SA after adding the fiber glass can be strengthened, and its thermal expansion coefficient is reduced. The Vicat softening temperature of SA is about 110 ℃. The flexural deformation temperature under load is about 100C, and the shrinkage rate of SA is about 0.3 ~ 0.7%.
Processing characteristics of SA
The processing temperature of SA is generally 200-250 ℃. SA needs to be dried for more than one hour before processing as it is easy to absorb moisture. Its fluidity is slightly lower than that of PS, so its injection pressure is slightly higher (injection pressure: 350 ~ 1300bar). Injection speed: high-speed injection is recommended. the ideal mold temperature is at 45-75 ℃. Drying treatment: SA has some hygroscopic properties if stored improperly. The recommended drying conditions are 80 ℃ for 2-4 hours.
Melting temperature: 200~270℃. Thick-walled products can use the melting temperature lower than the lower limit. For the strengthen material, the mold temperature should not exceed 60℃. The design of cooling system must be paid attention to because mold temperature directly affects the outer appearance, shrinkage, and bending of products. Runners and gates: applicable to all the ordinary gates and the size of the gates should be proper to avoid the generation of stripes, spots and gaps.
Typical application range:
Electrical (sockets, shells, etc.), daily commodities (kitchen appliances, refrigerator devices, TV bases, cassette boxes, etc.), automobile industry (headlight boxes, reflective environments, instrument panels, etc.), household goods (tableware, food knives, etc.), cosmetic packaging safety glass, water filter shell and faucet knob. Medical products (syringes, blood suction tubes, renal dialysis devices and reactors).
Packaging materials (cosmetic box, lipstick sleeve, eye black cap bottle, cover, cap spray and nozzle, etc.), special products (disposable lighter shell, brush base material and hard hair, fishing gear, false teeth, toothbrush handle, pen holder, instrument nozzle and directional monofilament), etc.
ABS
Properties of ABS
ABS is synthesized from acrylonitrile, butadiene and styrene. (Each monomer has different characteristics: acrylonitrile has high strength, thermal stability and chemical stability. Butadiene has toughness and impact resistance. Styrene has easy processing, high finish and high strength.
The polymerization of the three monomers produces a terpolymer with two phases, which is continuous phase of styrene acrylonitrile and a dispersed phase of polybutadiene rubber respectively. In terms of morphology, ABS is an amorphous material with high mechanical strength and good comprehensive properties of “hardness, toughness and steel”.
As an amorphous polymer, ABS is a general-purpose engineering plastic with various varieties and wide applications. It is also called “general-purpose plastic” (MBS is called transparent ABS). ABS is easy to absorb moisture, with a specific gravity of 1.05g/cm3 (slightly heavier than water), and a low shrinkage rate (0.60%?). with the stable size, ABS is easy to form and process. The ratio of three monomers and the molecular structure in the two phases affect the properties of ABS, which allows great flexibility in product design, and thus hundreds of products made of ABS materials of different quality come out in the market.
Various materials provide different properties, such as from the medium impact resistance to advanced impact resistance, from low to high finish and high temperature distortion characteristics, etc. ABS has excellent process ability, appearance characteristics, low creep, excellent dimensional stability and high impact strength.
ABS is a kind of material with light yellow granular or bead opaque resin, non-toxic, tasteless, low water absorption, good comprehensive physical and mechanical properties, such as great electrical properties, wear resistance, dimensional stability, chemical resistance and surface gloss. In addition, it is simple to process and form. While, the disadvantages of it include poor weather resistance, heat resistance and flammability.
Process characteristics of ABS
(1). ABS has high moisture absorption and humidity sensitivity, so it must be fully dried and preheated (at least 2 hours at 80-90c) to keep the moisture content below 0.03% before the molding.
(2). The melt viscosity of ABS resin is less sensitive to temperature (different from other amorphous resins). Although the injection temperature of ABS is slightly higher than that of PS, it can not have a loose temperature rise range like that of PS. Only increasing the temperature cannot effectively reduce the viscosity. Instead, the fluidity can be enhanced by increasing the screw speed or injection pressure. Its general processing temperature is 190-235 ℃.
(3). The melting viscosity of ABS is medium, which is higher than PS, hips and as. Therefore, it is necessary to use high injection pressure (500 ~ 1000bar) beer.
(4). medium and high injection speed for ABS material can obtain a great effect (unless the shape is complex and the thin-walled parts require a high injection speed). Air lines are easy to found on the product nozzle.
(5). the molding temperature of ABS is high, which generally at 25-70 ℃. When producing large-sized products, the temperature of the fixed mold (front mold) is generally around 5 ℃ higher than that of the movable mold (rear mold). The mold temperature affects the finish of plastic parts, and lower temperature will lead to lower surface finish.
(6). staying in the high-temperature barrel for a long period of time (less than 30 minutes) will lead to the decomposition of ABS and cause the color of it turning yellow.
Typical application range:
Automobile (instrument panel, tool compartment door, wheel cover, reflector box, etc.), refrigerator, high-strength tools (hair dryer, mixer, food processing machine, lawn mower, etc.), telephone shell, typewriter keyboard, entertainment vehicles such as golf cart and jet sled, etc.
BS (K material)
Performance of BS
BS is a butadiene styrene copolymer with certain toughness and elasticity. The hardness (soft) ion BS is low. BS has good transparency. The specific gravity of it is 1.01fcm3 (similar to water), which is easy to color, good fluidity and easy to form.
Process characteristics of BS
The suggested processing temperature range for BS is generally 190-225 ℃, and the mold temperature is 30-50 ℃. Ensure that it is dried before processing. Due to the good fluidity, the injection pressure and injection speed can be lower.
PMMA (sub afterburner)
performance of PMMA
PMMA is an amorphous polymer, commonly known as organic glass. PMMA has great transparency, good heat resistance (thermal deformation temperature: 98 ℃), good impact resistance, medium mechanical strength, and low surface hardness. Moreover, traces may be left as it is easy to be scratched by hard objects. It is less brittle than PS, with a specific gravity of 1.18g/cm3. PMMA has excellent optical properties and weather resistance.
The penetration of white light of PMMA is up to 92%. PMMA products have ultra low birefringence and is a great material for making video discs. PMMA has room temperature creep property. As the increase of load and time, stress cracking can be caused.
Process characteristics of PMMA
The manufacturing requirements of PMMA are strict. As PMMA is sensitive to moisture and temperature, so it should be fully dried before processing (normally the drying conditions are at 90 ° C for 2-4 hours. PMMA has high melt viscosity and it needs to be formed under high pressure (225-245 ° C). The recommended mold temperature is at 65-80 ° C.
The stability of PMMA is poor, and it is prone to decompose under high temperature or stay for long under the high temperature. The rotating speed of screw should not be high (normally 60%). The processing methods of “big gates, low material temperature, high mold temperature, slow injection” is often adopted as cavities are easily appear in thick PMMA parts.
MORE BOLG
Insert mold in injection mold service
What are advantages and disadvantages of Zinc alloy and Aluminum alloy?
Inspection standards for injection molded partappearance
How to judge the quality of your plastic products?
Inspection standards for CNC machining
To ensure that your products are 100% qualified
Categories
Try GREFEE now,for free
We keep your uploaded files confidential and secure.