11 kinds of Surface Defects and Solutions of TPE Injection Molding Parts

Posted on : Aug 17 , 2022 By GREFEE
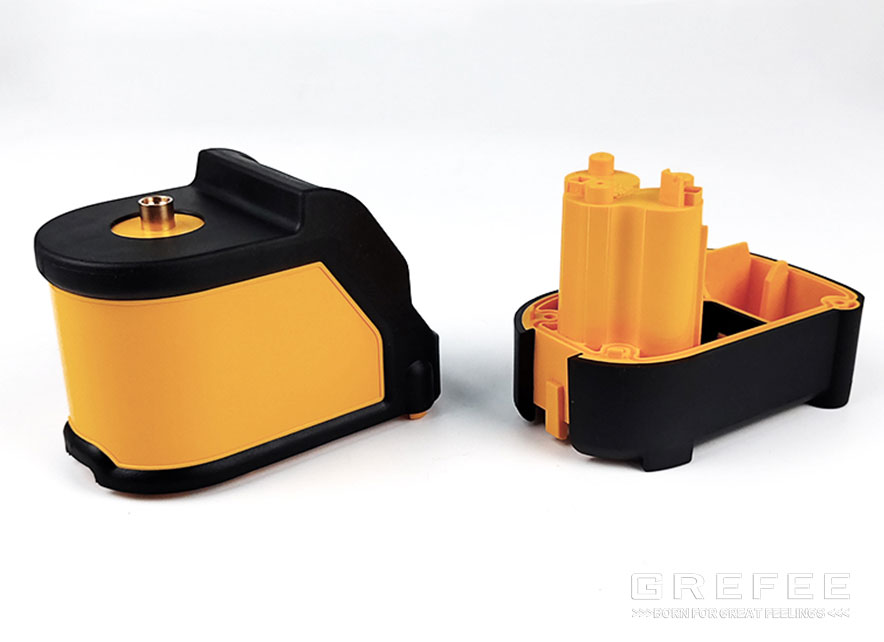
TPE injection molding parts are commonly used in toy dolls, toy tires, sucker dolls, fitness equipment, sporting goods, auto parts, etc. TPE injection molding products often have surface defects. GREFEE, the TPE injection molding manufacturers in China has collected and concluded 11 common surface defects and the solutions for the TPE injection molding manufacturers.
Whitening
It refers to that the stabilizer and other additives migrate to the surface of the molded product, and its surface presents a white phenomenon after spraying powder.
Cause: it is mainly caused by the excess amount of stabilizer or the incompatibility of polymers. The incompatibility can be solved by adding the related compatibilizer. The stabilizer with good compatibility with polymer should be selected or the dosage of stabilizer should be controlled in the best range.
In addition, it is effective if replace the stabilizer into the one with a high relative molecular weight. Other than that, there are also stabilizers that function by migrating to the surface of molded products, such as antistatic agent, lubricant, etc. In terms of this kind of stabilizer, it is necessary to select stabilizers that are difficult to whiten even if they migrate.
The whitening phenomenon is rarely seen in the TPE, but to increase the durability, it is necessary to add the thermal stabilizers and weather resistant stabilizer in situations, like high temperature, humid, or outdoor environment, especially under high temperature, it is very easy to migrate. Thus, the selection of stabilizer is essential.
Sticky phenomenon:
Compared to resin, the sticking phenomenon is more likely to be found in the surface of the soft thermoplastic elastomer.
Cause: It is mainly caused by the migration of low molecular weight polymers, plasticizers and stabilizers to the surface due to aging. No matter which situation, though using analysis method, such as IR, can easily identify the related substances.
The reason for sticking phenomenon is mainly due to the high molding temperature, and polymers form low molecular weight substances due to thermal decomposition. Although the set temperature of the molding machine hasn’t reached to the thermal decomposition temperature. However, Sometimes, the shear heat generation in the molding process will make it temporarily reach high temperature.
Solution: lowering the temperature and shear, or using the nitrogen purification molding machine to compress the bottom the cylinder with hydraulic pressure. In addition, when the forming machine stops, the material will stick to the cavity of the forming machine in a melt status due to aging after a long period of time. Other than that, the products used under high temperature will have sticking issues. Therefore, the selection and use amount of the stabilizer and softening agent is of great significance.
Aging phenomenon:
The mechanical properties of products decrease significantly, and the appearance quality is poor.
cause: compared to inorganic and metallic materials, poor heat resistance and UV resistance linearity of polymer materials causes the aging of products. The mechanical properties, appearance quality of the most products decrease due to the aging.
Solution: the aging phenomenon can be eased to some extent thorough the combining heat resistance, weather resistance and other stabilizers, and by adding ultraviolet absorbent and light stabilizer.
Porosity:
The porosity in the molded product is mainly caused by the shrinkage of during the cooling process in the mold. In addition to requiring that the material must fill the mold cavity, rapid cooling is also very necessary. Specifically, it is to increase the holding pressure (secondary pressure) and reduce the set temperature of resin and mold.
In addition, it also depends on the shapes of the end products. Since the porosity is easily to appear in the thick area, the prototype design with the injection port or flow channel around it should be adopted for this kind of products.
Burrs:
This is because the resin overflowed from the mold cavity. For the injection molding of rubber, it is common to have burrs, but not to resin or TPE.
Compared to plastic rubber material, the flowability of the molten resin or TPE is high, but injection pressure is low.What should do first is to reduce the filling about to decrease the holding pressure and shorten the time of pressure holding. Besides, for molds with dimension and accuracy errors or parting surface with gaps, it is necessary to repair it. Burrs could also be found when the projection area of molded products is large and the clamping force is relatively lower than the injection pressure, and thus it is necessary to utilizer larger molding machines.
Flow marks:
Stripes with different gloss appear on the surface of molded products.
Typically, the injection molding of resin includes:
Recording stripes if it has narrow intervals
There are relatively wide spacing stripes in the same phase above and below the surface of the molded product.
There are three types of relatively narrow interval stripes with ectopic fringes on the surface of the molded product.
Methods that can be adopted to address this issues include adding pure monomer resin, increasing the injection speed and mold temperature, increasing the glue injection port, increasing the resin temperature and injection rate, increasing the molding temperature, mold temperature or reduce the injection speed. Overall, the increase of the injection speed or mold temperature are both effective means.
Poor mold releasing
Poor mold releasing refers to the it is hard to take the molding products out from the mold or the products deform when it is taking out, which is especially common when using material with high sticky properties. However, adding mold release agent or apply the mold release agent on the mold can improve this situation.
Insufficient cooling (poor solidification) will also cause this issue, and thus it is necessary to let the product cool completely. In addition, improper mold design is another reason, especially for the injection inlet, feeding inlet and areas at which the mold are likely to stick. Enlarge the draft angel of gate or widen the inlet are all effective.
Silve fringes
Radial stripes appear with the injection port as the center is caused by the water in the material or the vaporization of volatile components, among which gas trapping during the plasticizing process or hidden in the mold will also lead to silver fringes. Therefore, It is necessary to ensure the hygroscopic materials are completely dry before forming and reduce the forming temperature of the materials that are prone to produce decomposition gases.
Underfeeding :
The phenomenon that the end of the mold cavity is not sufficiently filled is called underfeeding, which is mainly caused by insufficient feeding or inappropriate molding conditions. Moreover, incomplete venting or imbalance distribution of the runners (multi-cav mold) will also lead to underfeeding.
Burning:
Burnning refers to the aging phenomenion of the parts not filled to the end and not filled with the mold cavity, like burning, which is mainly due to insufficient venting, or the thermal insulation compression caused by air or the gas generated, resulting in the temperature raise significantly immediately. In another word, it is the thermal aging occurs on the surface of molded products.
The best way to address this is to improve the venting system or lower the injection speed when it is at a lower degree.
Non-uniform color and lustre
When coloring the masterbatch of pigment with TPE particles and dry mixture material, it is easy to generate non-uniform, uneven color and lustre or poor binding effect. The way to improve the color and lustre include utilizing the appropriate coupling agent and compatibilizer, increasing the back pressure of screw bar, or mixing when strengthening the filler are all helpful.
MORE BOLG
Insert mold in injection mold service
What are advantages and disadvantages of Zinc alloy and Aluminum alloy?
Inspection standards for injection molded partappearance
How to judge the quality of your plastic products?
Inspection standards for CNC machining
To ensure that your products are 100% qualified
Categories
Try GREFEE now,for free
We keep your uploaded files confidential and secure.