Injection molding process of TPR material

Posted on : Aug 23 , 2022 By GREFEE
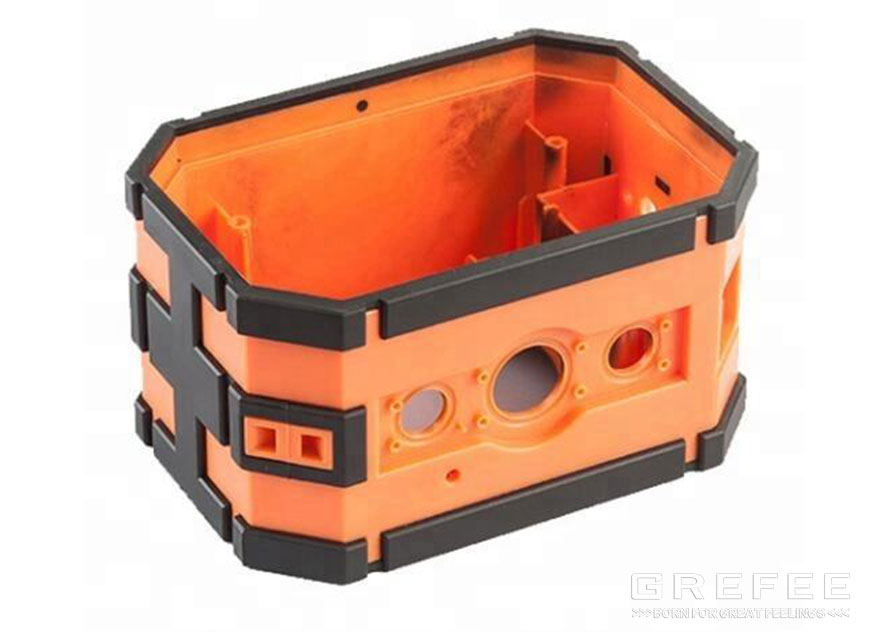
Typical, according to the condition of the properties of material and material supplement, the inspection should be carried out to check the appearance and process properties of materials before molding. The supplied particle have varying degrees of water, solutions, and other volatile low molecular substances, especially the TPR of which the water content is always exceeding the allowed limit. Thus, TPR should be fully dried and check the water content before processing. The water content in TPR is under 5% under a high temperature, or even 2%~3%, and thus dry the TPR with the vacuum box at 75℃~90℃ for 2 hours. The already dried material should be sealed and managed properly to in case the material absorbing water from the air.
In terms of this, the drying chamber hopper can supply the dry and hot material for the injection molding machine consistently, which is beneficial to simplify work, keep clean, improve quality, increase injection rate. The loading amount of the drying chamber hopper is 2.5 times that of hourly consumption of the injection molding machine. The TPE that is based on SBC has an advantage in color than other most TRP materials. Therefore, they can achieve a certain color effect with a small amount of masterbatch. Moreover, the color produced are more pure than other TRP. Typically, the viscosity of the masterbatch is lower than that of TRP, which is the reason why the melt Index of TRP is higher than that of masterbatch. This is beneficial to the dispersion process for more uniform color distribution.
For SBS-based TPEs, polystyrene-based vehicles are recommended.
For TPRs based on harder SEBS, polypropylene (PP) vehicles are recommended.
For softer SEBS based TPRs, low density polyethylene or ethylene vinyl acetate copolymers is recommended.
For softer varieties, PP vehicles are not recommended because the hardness of the composite will be affected.
For some overmolding applications, the use of polyethylene (PE) vehicles may exert a negative effect on the adhesion to the substrate.
Before the new injection molding machine is used or it is required to change products , raw material, color or find the decomposition phenomenon of the plastic during the production, the barrel of the injection molding machine should be disassembled and washed.
Heating barrel cleaning method is often used and the cleaning agent is often the plastic raw material (or plastic recycled material). For TRP, the transition cleaning material can be replaced with the new material processed.
During the injection molding process, whether the set of temperature is correct will affect the appearance and properties of the products. The following are some advice for the temperature setting in TRP injection molding process.
The temperature of the feeding area should be extreme low to avoid the blockage of the feeding port and exhaust the air. When using the masterbatch to improve the mixing status, the temperature of the transition area should be higher than that of the color masterbatch. The temperature in the area closest to the injection nozzle should be set close to the required melt temperature. So, the temperature setting range for TRP products in each area after testing generally are 160 — 210 degrees for barrel, 180 — 230 degrees for nozzles.
The mold temperature should be higher than the condensation temperature of the injection molding area, which will avoid the contamination of the mold by moisture and the appearance of fringes on the surface. The longer the mold temperature, the longer the circulation cycle. However, it can improve the appearance of the welding lines and products. Therefore, the range of the mold temperature should be between 30-40.
During the product forming and cavity filling process, if the filling properties of products are poor, there will be a series of quality problems, such as large pressure drop, filling time is too long, short shots. We can try to improve the filling properties and quality of products in forming process from the following aspects.
(1). Change to another series of products
(2). Change the gate position
(3). Change the injection pressure
(4). Change the geometry of the part
The control of the injection pressure is usually divided into the primary injection pressure, the secondary injection pressure (holding pressure), or the injection pressure of three or more times. Whether the pressure switching timing is appropriate is important to prevent the pressure in the mold from being too high, to prevent overflow or lack of material, etc. The specific volume of the molded product depends on the melt pressure and temperature when the gate is closed during the holding pressure stage. If the pressure and temperature are consistent when it is switched from pressure holding to products cooling stage, the specific volume will not change. Under a consistent mold forming temperature, the important index that decides the dimension of products is the holding pressure. The variable affecting the dimension errors include the holding pressure and temperature. For instance: after the mold filling, the holding pressure will decrease immediately. Raise the holding pressure when the margin reaches a certain thickness, the large products can be formed with low clamping force to eliminate the depressions and galling.
The holing pressure and speed are usually 50%~65% of the highest pressure and speed when the plastic filling the cavity, which is the holding pressure is lower than the injection pressure by 0.6~0.8MPa. Since the holding pressure is lower than the injection pressure, the load of the oil pump is low, the service life of the solid oil pump is extended, and the power consumption of the oil pump motor is also reduced within a considerable pressure holding time. Adjust the amount of metering in advance, so that there is still a small amount of melt (buffer volume) at the end of the screw near the end of the injection stroke. According to the filling condition in the mold, the injection pressure (secondary or tertiary injection pressure) is further applied to supplement a little melt. By doing so, the product can be prevented from being depressed or the shrinkage of the product can be adjusted.
The cooling time is mainly determined by the temperature of melt, thickness of products, and the cooling efficiency. In addition, the hardness of material is one factor. Compared to softer types, the hard variety solidified quickly in the mold. If it is cooled from the sides, then the cooling time for every 0.100 ‘wall thickness will usually be about 10 to 15 seconds. Products by encapsulation will need longer cooling time because it can be cooled effectively through a smaller area. The cooling time for every 0.100 ‘wall thickness will usually be about 15 to 25 seconds.
1. Incomplete plastic forming
(1). Improper feeding adjustment, lack of material or more material.
(2). Extreme low injection pressure, short injection time, and the plunger or screw retracts too early.
(3).Slow injection speed
(4).Low material temperature
2. Overflow (flash)
(1) Extreme high injection pressure or the injection speed is too fast.
(2) Excessive feeding causes flash.
(3) If the temperature of barrel and nozzle or mold are too high will reduce the viscosity and increase the fluidity of the plastic, resulting in flash in the case of smooth mold entry.
3. Silver fringes, bubbles and porosity
(1) .Material temperature is high, resulting in decomposition.
(2) .Low injection pressure and short pressure holding time, so that the molten material is not closely attached to the surface of the cavity.
(3). Fast injection speed making the molten plastic decompose due to the large cutting effect, and product the decomposition gas. Low injection speed cannot fill the cavity in time and cause silver fringes due to the insufficient surface density.
(4).Insufficient material, too large feeding buffer, too low material temperature or too low mold temperature will affect the flow and forming pressure of molten material and produce bubbles.
(5). If the back pressure is too low when the screw is pre-plasticizing, high rotating speed will make the screw bar retract too fast. The air will be pushed to the front of the barrel with the material.
4 .Burning & dark lines
(1) .The temperature of barrel and nozzle is too high.
(2) .The injection pressure or pre-plasticizing back pressure is too high.
(3) .The injection speed is too fast or the injection cycle is too long.
MORE BOLG
Insert mold in injection mold service
What are advantages and disadvantages of Zinc alloy and Aluminum alloy?
Inspection standards for injection molded partappearance
How to judge the quality of your plastic products?
Inspection standards for CNC machining
To ensure that your products are 100% qualified
Categories
Try GREFEE now,for free
We keep your uploaded files confidential and secure.