Before you initiating your new project, you need to know the types of injection molding.
Posted on : March 24, 2022 By GREFEE
There are many ways to classify the injection molding, in which it is classified into few types according to the difference.
(1) classified by the material, there are thermoplastic injection mold and thermosetting plastic injection mold.
a. Generally, injection molding technology suits for both thermoplastic and multiple thermosetting plastic.
b. In the injection molding process of thermoplastic molds, the material is melting in the barrel, and the bar or piston pushes the material into the cavity, passing by the nozzles, runners, and gates. It ultimately is cooled in the cavity and being shaped as the requirement. However, for the thermosetting plastic molds, the premix will be heated under a circumstance under which the curing reaction will not happen. The bar and piston push the material into the heated mold. When the material passes through the nozzle, the temperature rises further, which leads to the curing reaction. This process makes the material into specific shapes.
c. Overall, the difference between thermoplastic injection molds and thermosetting plastic injection molds is that the former is a low-temperature mold in which material is cooled and shaped. While the latter is high-temperature mold in which the premix, cured, and shaped in the mold.
d. Injection molding technology does not apply to all types of plastic. In thermoplastic injection molding, the melting temperature of materials, like polytetrafluoroethylene, ultra-high molecular weight polyethylene, pure polyphenylene ether, polyphenylene sulfide, and PEEK are close to or even higher than the decomposition temperature, so we usually only use the die casting method ( with the possibility of taking injection molding after modification). The curing temperature of some thermosetting plastic materials almost equals the melting temperature of the premix, so it must be processed by compression molding.
(2) it can be classified by the number of cavities, single cavity injection mold and multi-cavity injection mold.
Pros and cons: the reliability and flexibility of the multi-cavity mold are lower than those of the single cavity mold. However, for the equipment investment, space utilization, energy consumption, cost, and other aspects, the multi-cavity molds surpass the single cavity molds. When the multi-cavity mold has one more cavity, the size accuracy of the product will decrease by 4%, so for injection molding parts with high accuracy requirements and complex structures, it is better to reduce the number of the cavity or use the single cavity mold. Besides, some plastic materials are not compatible with the gate type, and the number of the mold cavity cannot be confirmed till the gate type has already been checked. The one mold multi-cavity method suits different kinds of gates, except for the direct gate and disk gate.
(3) classified by the types of injection molding machine: horizontal injection mold machine, vertical injection mold machine, vertical angle injection mold machine.
The vertical injection mold machine is classified into two types: single sliding injection molding machines, and double sliding injection molding machines. The machine is specifically used for industrial plastic, which has rigorous requirements for accuracy. Injection molding with accurate or micro inserts is also one of the optimal insert injection molding plans. This machine is featured by the function of fixing by core plug and the former block sliding out. The double sliding plate has one core plug and double former blocks, which work alternately, suit the insertion and removal of high precision hardware. Some double-shot injection molds can be obtained by the double-sliding injection molding method. Most molding products need two people to operate, which increase the cost, such as electronic precision connector, mobile connector, integrated circuit package, etc
The horizontal injection mold machine: It is the most common type of injection mold machine. The mold opens horizontally as its clamping part and injection part is placed at the same horizontal centerline. This machine is characterized by a short body, convenient operation, and repair. It has a stable assembly due to its low gravity. The product will fall automatically with the action of gravity after being ejected, so it suits automation operations. While the disadvantages of it include the complex assembly process, the possibility of falling or deflecting, and a large coverage area. Currently, these types of machines have been widely used in the market.
The axis of the injection device and clamping device of vertical angle injection machine is in a vertical arrangement. It is mainly characterized by placing its principal runners on the horizontal parting surface, and no gate marks are allowed at the production center area. Its coverage area is between horizontal injection mold machines’ and vertical injection mold machines’. So far, the production volume of domestic injection mold machines is small but indispensable.
(4)classified by the size of plastic parts: injection mold, precise injection mold
The main difference is the accuracy of casting parts. The higher the accuracy is, the higher the manufacturing cost will be. Click to learn the tolerance of injection molding parts in GREFEE.
Classified as pouring system: cold runner mold, adiabatic runner mold, hot runner mold, warm runner mold.
Advantages: hot runner molds have been widely used in developed industrial areas worldwide. The hot runner mold has many characteristics, which are:
1. Shortens the molding cycle
With the limitations of cooling time due to the absence of a sprue system, the part can be released after molding directly. The molding time for many thin wall parts made of hot runner mold could be lower than 5 secs.
2. plastic material saving
As no cold sprue sits in hot runner mold, so no production waste. This feature is of great significance for projects that use expensive plastic materials. As a matter of fact, the international hot runner makers all developed when petroleum and plastic are pricy, so reducing the hot runners is an effective method for lowering the cost of the material.
3. Minimize the waste production & increase the product quality
In the hot runner molding process, the plastic melting temperature is controlled accurately in the runner system, so the quality of all parts is qualified, for the plastic can flow into each cavity more equally. The hot runner molding parting has a good quality gate, low residual stress after mold releasing, and minimization of deformation of the part. Many products from the famous international brands use the hot runner mold, like MOTOROLA, HP printers, DELL laptops, of which many plastic parts come from the hot runner mold.
4. Elimination of Post-Treatment beneficial for production automation.
we can obtain parts merely after the hot runner molding process without trimming the gate, recycling and machining the cold runner, and other procedures, which is beneficial for production automation. Many international makers combined the hot runner and automation to achieve greater production efficiency.
5. expand the range of injection molding technology
Much advanced plastic molding technology developed on hot runner technology, such as PET preforming, multi-shot and multi-material co-injection technology, STACK MOLD, etc.
Disadvantages: although hot runner has many remarkable advantages compared to cold runners. however, the mold user still need to have some knowledge about the disadvantages of hot runners mold,
Below are a few points of disadvantages:
1. Mold making cost increases.
2. The expensive hot runner parts cause the cost of the hot runner mold to increase significantly. Economically, low production volume cannot promise cost-effectiveness due to the high mold-making cost. For many mold users in developing countries, the price of the hot runner system is one of the primary issues which affects the popularization of hot runner molds.
3. hot runner mold manufacturing has high requirements for equipments
4. The precise machining mechanics assure the hot runner quality as the mold will cause many server issues without rigorous assembly requirements for hot runner system and molds, such as the plastic is not being sealed appropriately will lead the plastic overflow and interrupt the production by damaging the hot runner components. The incorrect connecting position of the spray nozzle and gate will significantly affect the quality.
5. complex operation and repair
6. Compared to cold runner molds, hot runner molds are hard to operate and repair. Improper operation is likely to cause hot runner components to damage and suspend production, causing a massive economic loss. For new users of the hot runner mold, it needs a long period for the experience accumulation. Contact GREFEE to start your new project!
Classified by the overall structure feature of injection mold, which are:
A. Single parting surface injection mold (two-plate injection mold) is the simplest one in injection molds. Part of the cavity is on the moving die, and the rest is on the fixed die. The horizontal and vertical injection mold machines use single parting surface injection mold with locating the principal runner at one side of the fixed-die, and sub-runners stay at the parting surface. The aggregate in runners and components will be at the side of the moving die and be pushed away by the push-off device, which is on the moving die.
B. Double parting surface injection mold has two parting surfaces. The single parting surface injection mold has one middle plate (is also called moveable gate plate with gate, runner, and other components and parts that fixed dies need), so it is also named three-plate injection mold (moving-die plate, middle plate, fixed die plate) which is often used for the single cavity injection mold or multi-cavity injection mold of pinpoint gate feeding. When the mold opens, the middle plate on the guide pin of the fixed die is away from the fixed die plate with a fixed distance in between, which allows the pouring system aggregate to release. Double parting surface injection mold has a complex structure and is expensive to make. The components are hard to process, so it often does not apply to large-scale or ultra-large-scale plastic products molding.
C. the injection mold with movable molding components – due to the specific requirements of plastic parts, can add movable molding components inside the mold for the convince to release the part, like the moving force plug, movable former block, moveable molding rod, moveable molding insert, etc.
D. The injection mold with side parting and core pulling – when the part has side holes or side grooves, adds side parting and core-pulling systems, like angle pin or angle block, etc. when opening the mold, uses the mold opening force to move transversally with the side core to make it separate with the components. There are also situations like adding a hydraulic cylinder or air cylinder to do the transversal parting core-pulling action.
E. Automatic un-screw threads injection mold – for plastic parts with internal threads or external threads require the rotatable threaded core or ring on the mold in the automatic de-molding process. Settings can help with the mold releasing, like the rotation of lathe moving back and forth, or design a specific original engine part (like electronic engine, hydraulic engine, etc) and transmission device to make the threaded core or ring rotate.
F. After opening the mold, the injection mold with a push-off device in fixed die, the component will stay at the side of the fixed die and the same as the push-out device. Due to the specific requirement or limitations of shape for parts, the part will stay on the fixed die (or possibly on the fixed die). When the mold opens, the pull plate or chain pushes the part off.
G. Injection mold without runners – injection mold without runners include hot runner mold or insulation runner injection mold. They heat or insulate the runners (the condensed plastic layer separates the molten plastic of the runner center) to maintain the plastic injected from the spray nozzle into the cavity gate being molten state. After each injection, what only needs to do is to release the part with no recovery material of the pouring system. It effectively enhances the production rate and assures the pressure transmits in the runners. By doing so, the mold is effortlessly achieving fully automatic operation.
H. The vertical angle injection mold – What makes it different from other molds is that its feeding direction is perpendicular to the direction of mold opening and closing. The principal runners of this mold are on both sides of the parting surface of the fixed die and moving die. Besides, its cross area remains unchangeable. It is different from the molds that other injection molding machines use. The top of the principal runners can have a replaceable flow insert to prevent the spray nozzle of the injection molding machine and gate of the principal-runners from being worn and deformed.
With 20 years of experience, GREFEE can provide a professional injection molding plan for you according to the characteristics of parts and your requirements with the lowest cost. Try GREFEE for the new project. Our staff will contact you with rapid real-time pricing (12hrs) and free DFM analysis.CONTACT US
MORE BOLG
Categories
Latest blog
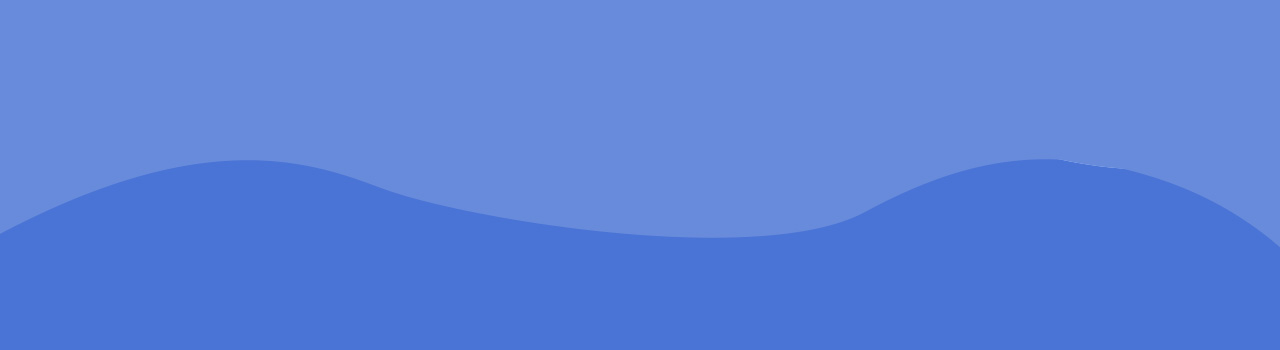
Try GREFEE now,for free
We keep your uploaded files confidential and secure.