Differences between water cutting, laser cutting, plasma cutting and wire cutting in parts processing

Posted on : July 19 , 2022 By GREFEE
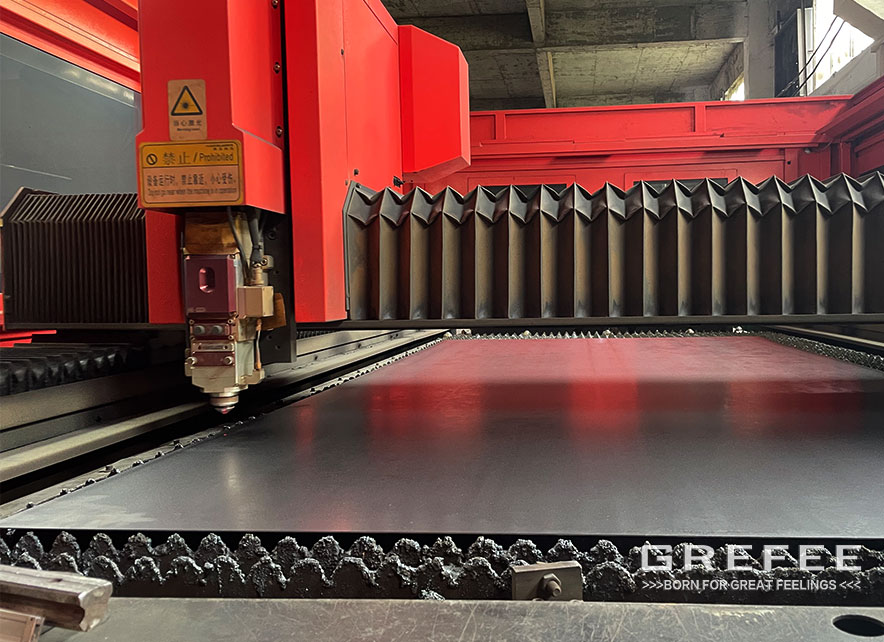
When we processing the parts, we often need to cut the plates first according to the drawings. There are some common methods include water cutting, laser cutting, plasma cutting and wire cutting. What is the difference between these methods?
Laser cutting
Laser cutting service is not limited to large part laser cutting, even could process small-scale parts. It utilizes focused high power density laser beam irradiates workpiece to melt, vaporize, ablate the material immediately to reach to the melting point. Meanwhile, the molten material will be removed with the high-speed airflow coaxial with the beam, and the workpiece is cut. So far, the machine that is often used is the CO2 pulse laser. Laser cutting is one of the thermal cutting methods.
Laser cutting is used widely worldwide, even in some countries, like China, having CNC laser cutting. This works with the help of the CNC laser cutting machine. Common metal processing with this includes sheet metal laser cutting, laser cutting steel, aluminum laser cutting, stainless steel cutting. With the development of this, many stainless steel laser cutting machine manufacturers have realized the importance to involve CNC into the production, which saves time and cost effectively.
Water cutting
Water cutting, also named water jet, which is high pressure water jet cutting technology, a machine that utilizes high pressure water flow cutting machine. This machine works under the control of the computer and can be engraved. It is less affected by the material. Water cutting has two types, sandless cutting and sanding cutting.
Plasma cutting
Plasma cutting relies on the heat of the high temperature plasma arc to melt and evaporate the metal at the cut of the workpiece, and to form a cut with the momentum of high-speed plasma to remove the molten metal.
Linear cutting
Wire Electrical Discharge Machining, simply known as WEDM, blogs to the electrical processing category. WEDM can be divided into fast WEDM, medium WEDM, slow WEDM. The wire-feeding speed of the fast WEDM is 6~12m/s. As the electrode wire moves back and forth at high speed, so the cutting precision is poor. Medium WEDM is further developed based on the fast WEDM. It makes the frequency conversion multiple cutting function available, which is the latest technique in recent years. The wire-feeding speed of the the slow WEDM is 0.2m/s, and the electrode wire moves in one direct at low speed. Its cutting accuracy is high.
Comparison of application scope
The laser cutting machine has an extensive application range. No matter it is metal, non-metal, cloth, or leather, all can be processed with the CO2 laser cutting machine. Fiber laser cutting machine can be used to cut metal due to small plate deformation.
Water cutting is cooling cutting without deformation, so the cutting surface has high quality without second processing. It is still easy to perform the second processing if needed. Water cutting is applicable to the drilling and cutting any type of material with fast cutting speed and flexible processing dimension.
Plasma cutting machine is applicable to the cutting of metal, like the stainless steel, aluminum, copper, casted iron, and carbon steel, etc. the plasma cutting has an evident thermal effect. However, the processing surface has low accuracy and is hard to perform second processing directly.
Linear cutting can be only use for cut the electric conductive substance. The cooling agent is needed during the cutting process, so items like paper and leather which is non electric conductive but cannot tolerate water are not suitable for linear cutting due to the cooling agent.
Cut thickness comparison
Laser cutting carbon steel is often below 20mm in the industrial use. The cutting capacity is below 40mm. The industrial use of the stainless steel is below 16mm, of which the cutting capacity is below 25mm. With the thickness of the workpiece increases, the cutting speed decreases significantly.
The thickness of the water cutting can be very thick, 0.8-100mm, or even thicker material.
The plasma cutting thickness is 0-120mm. The best cutting thickness range is about 20mm. The cost performance of the plasma system reaches its peak.
The linear cutting thickness is 40-60mm, and the thickest could be as high as 600mm.
Cutting speed comparison
Cutting the 2mm thick low carbon steel plate with the 1200w power laser cutting with a 600cm/min cutting speed. The cutting speed is 1200cm/min when cutting 5mm thick polypropylene resin board. The cutting efficiency of the WEDM is 20-60mm2/min and the highest can be 300mm3/min. Obviously, the laser cutting is faster, suiting for large volume production.
Water cutting speed is slow, but does not suit for large volume production.
The cutting speed of the plasma cutting is slow but with low accuracy, suiting for thick plate. However, the end face is draft.
For the processing of metal, laser cutting are required to have higher cutting accuracy but the speed is low. Sometimes, it needs to utilize other methods to carry out the perforation and threading to start the linear cutting, and it is quite limited.
Cutting accuracy comparison
The cut of the laser cutting is thin and narrow. The two sides of the slit is paralleled and perpendicular to the ground. The size accuracy of the cutting parts can be ±0.2mm.
The cutting accuracy of the plasma cutting can be within 1mm.
Water cutting is friendly due to no heat deformation, of which the accuracy is ±0.1mm. the dynamic water cutting can increase the cutting accuracy, which is ±0.02mm, eliminating the cutting obliquity.
The linear cutting accuracy is generally ±0.01~±0.02mm,the highest can be ±0.004mm。
Cutting seam width comparison:
Laser cutting is more accurate than the plasma cutting with narrower seam, which is about 0.5mm.
The seam of the plasma cutting is wider than laser cutting, which is around 1-2mm.
The seam of the water cutting is 10% larger than the diameter of the knife tube, about 0.8mm-1.2mm. as the increase of the diameter of the sand knife tube, the cut is larger, too.
The seam of the linear cutting is the smallest, about 0.1-0.2mm.
Comparison of cutting surface quality
The surface roughness of laser cutting is poorer than that of water cutting. The thicker the material, the more obvious it is.
Water cutting will not change the texture of the material around the cutting seam (laser cutting belongs to thermal cutting, which will change the texture around the cutting area.
Production cost comparison:
The price of the laser cutting machines are different according to different purposes. For example, the cheap CO2 laser cutting machine is only $4000-$5000, and the 1000W fiber laser cutting machine is now more than $350,000, which are more expensive. The laser cutting does not have a large volume material consumption, but its equipment investment cost is the highest among all cutting methods, which is much higher, and the use and maintenance cost is also high, too.
The plasma cutting machine is much cheaper than the laser cutting machine. The price varies according to the power and brand of the plasma cutting machine. However, the use cost is high. Basically, it can cut any electric conductive material.
The cost of water cutting equipment is just below the laser cutting, with high energy consumption, high use and maintenance costs, and the cutting speed is slower compared to plasma cutting. Since all abrasives are disposable, they are discharged into the nature after being used once, leading to serve environmental pollution.
Wire cutting often costs about thousands of dollars. However, the wire cutting consumed large amount of material, such as molybdenum wire, cutting coolant, etc. There are two types of wires commonly used in WEDM. One is molybdenum wire (molybdenum is valuable), which is used for fast wire walking equipment. Its advantage is that molybdenum wire can be reused many times. The other is to use copper wire (which is much cheaper than molybdenum wire anyway) for slow wire walking equipment, of which the disadvantage is that copper wire can only be used once. In addition, the fast wire walking machine is much cheaper than the slow wire walking machine. The price of a slow wire walking machine is about 5-6 times that of the fast wire walking machine.
As mentioned above, laser cutting is mainly used in sheet metal laser cutting workshops, such as aluminum alloy laser cutting, stainless steel laser cutting and other metal plates, and wire cutting is used for processing high-precision parts. GREFEE is a manufacturer with laser cutting machines and liner cutting machines. Contact us for more cutting services!
MORE BOLG
Insert mold in injection mold service
What are advantages and disadvantages of Zinc alloy and Aluminum alloy?
Inspection standards for injection molded partappearance
How to judge the quality of your plastic products?
Inspection standards for CNC machining
To ensure that your products are 100% qualified
Categories
Try GREFEE now,for free
We keep your uploaded files confidential and secure.