Zinc Alloy Electroplating Processing

Posted on : July 22 , 2022 By GREFEE
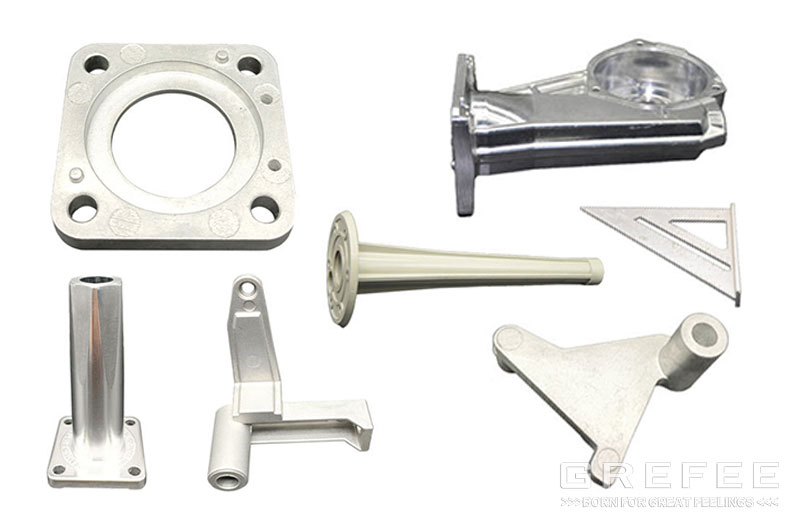
Electroplating is a common treatment method for metal surface. Metal plating also needs professional processing process to make the surface beautiful and qualified. Common parts that are used for plating on zinc alloy, plating on aluminum alloy, plating on magnesium alloy, plating on copper alloy, etc., have gold plating, silver plating, zinc plating, nickel plating, chrome plating, etc.
Electroplating process
Ultrasonic wax removal – hot water washing (75 ℃) – chemical oil removal – hot water washing – three-stage countercurrent cleaning – cathodic electricity free oil – hot water washing – three-stage countercurrent cleaning – acid etching (volume fraction of 2% sulfuric acid + volume fraction of 2% hydrofluoric acid, room temperature, 2S after separating bubbles) – three-stage countercurrent cleaning – pre leaching (sodium cyanide 50g/l, room temperature, 10s) – cyanide copper plating (cuprous cyanide 30g/l, sodium cyanide 45g/l, potassium sodium tartrate 20g/l, 50 ℃, 3min, jk=1.0a/dm2) – recovery – tertiary countercurrent cleaning – acid activation (volume fraction of 10% sulfuric acid, room temperature, 0.5min; the same below) – tertiary countercurrent cleaning – pyrophosphate copper plating (copper pyrophosphate 65g/ L, potassium pyrophosphate 300g/l, ammonia 3ml/l, appropriate amount of brightener, 56 ℃, 15min, jk=2a/dm2, ph=8.8) – recovery – tertiary countercurrent cleaning – acid activation – tertiary countercurrent cleaning – sulfate copper plating (copper sulfate 200g/l, sulfuric acid 60g/l, chloride ion 60mg/l, appropriate amount of brightener, 23 ℃, 15min, jk=3.5a/dm2) – recovery – tertiary countercurrent cleaning – acid activation – tertiary countercurrent cleaning – sulfate nickel plating (nickel sulfate 200g/l, nickel chloride 60g/l, boric acid 50g/l, appropriate amount of brightener, 50 ℃, 10min, ph=4.6, jk=4a/dm2) – recovery – tertiary countercurrent cleaning – acid activation – tertiary countercurrent cleaning – white chromium plating (chromic anhydride 230g/l, sulfuric acid 2.3g/l, trivalent chromium 3g/l, extender 2.3g/l, 45 ℃, 1min, jk=20a/dm2) – recovery – tertiary countercurrent cleaning – hexavalent chromium recovery (sodium bisulfite 30g/l, room temperature, 1min) – tertiary countercurrent cleaning – Ultrasonic Cleaning – tertiary countercurrent cleaning – acid neutralization (5% sulfuric acid, room temperature, 0.2min) – three stage counter current cleaning – hot pure water washing (70 ℃, 1min) – drying (100 ℃, 25min) – off the shelf – Inspection – Packaging – warehousing.
Characteristics of zinc ally electroplating
1. Excellent wear resistance. With same thickness, The corrosion resistance of Zn-Ni alloy coating is 4 ~ 8 times that of pure zinc coating. The coating itself is an anodic coating on steel substrate, which can provide effective cathodic protection.
2. The thickness is 5 ~ 15 μm within thread tolerance range, can obtain long-term wear resistance, which demonstrates that the coating itself is very close to the extreme low corrosion rate.
3. The coating and the base have sufficient bonding force to ensure it can maximum the value of the wear resistance of the coating.
4. Great thermal fatigue resistance. The corrosion resistance of the coating remains the same after chilling and heat treatment at -60 ~ 250 ℃.
5. The process ability is almost equal to the electroplating pure zinc layer. The coating still has a high corrosion resistance that is higher than that of the pure zinc coating after deformations process.
6. Low hydrogen brittleness. The hydrogen embrittlement rate of Zn-Ni alloy coating is only 1.5%, whereas the embrittlement rate of pure zinc plating is more than 40%, and that of bright cadmium plating is about 18%.
7. The hardness of Zn-Ni alloy coating is higher than that of pure zinc and hence with better wear resistance.
8. Simple operation process.
The technological process and equipment of electroplated nickel alloy are the same as those of electroplated pure zinc, and no special equipment is required. Process flow: acceptance before plating → oil removal → water washing → acid pickling and rust removal → cleaning → activation → water washing → electro galvanized nickel alloy → water washing → passivation → water washing → drying → classified packaging.
Common issues summary in electroplating
The primary problem factors of electroplated nickel plating are: poor pretreatment, with metal impurities and quite less boric acid content, as well as extreme low bath temperature, all of these factors will lead to pinholes in the nickel plating layer. Moreover, the bath maintenance and strict control process are essential as well. The electroplating quality can be obtained as long as these issues are addressed.
1.Pockmarks (pinhole)
The pockmark (pinhole) is the result of organic pollution. Large pockmarks indicate there is grease and needs to be cleaned by decomposing the oily carbon for treatment. If the mixing is not good, bubbles cannot be expelled, and pockmarks(pinholes) will be formed. Wetting agent can be used to reduce its impact.
2. Rough (Burrs)
Rough indicates the dirty solution can be corrected after full filtration. If the value is too high, it is easy to form hydroxide precipitation, which should be controlled. If the current density is too high, the anode mud and make-up water are mixed with impurities, which leads to roughness (burrs) in serious rough surface (burrs)
3. Low binding force
If the oxide layer copper and titanium of unactivated copper coating are removed without being unactivited, the adherence is poor, which may lead to the coating peeling. If the current is interrupted, it may also lead to the coating peeling, and the low temperature does, too.
4. Brittle coating and poor weldability
When the coating is bent or being worn to a certain extent, the brittle of the layer will be exposed, which indicates that the organic substance or heavy metal impurities pollution. Too much additives make the organic substance or decomposed substance content increase, which is also the major source of the organic substance pollution. This can be addressed by adding the activated carbon. The heavy metal impurities can be addressed by the electrolysis or other methods.
5. The color of coating is gloomy and uneven
The gloomy and uneven color coating indicates there is metal pollution. Since the steps is the copper plating and then titanium plating, the mixed copper solution is the major source for pollution. What’s more, to minimize the copper solution on the hanger to eliminate the metal pollution in the nickel plating bath, the corrugated steel plate is required as the cathode for electrolytic treatment under the current density of 02-0.5a/dm2. There are many factors that affect the color and gloss of the coating, such as the poor pre-treatment and bottom coating, low current density and main salt concentration, as well as poor electric conductivity.
6. Burned coating
Many factors could be the reason for coating burning, like the insufficient boric acid, low concentration of metal salt, too low operating temperature, too high current density, too high pH value or insufficient stirring.
7. Low deposition rate or low current density leads to low deposition rate.
8. Blistering or peeling of coating
Blistering or peeling may result from factors, like poor pre-plating treatment, too long intermediate power-off time, organic impurity pollution, too high current density, too low temperature, too high or low pH value, and serious influence of impurities.
9. Anode passivation
Insufficient anode activator (nickel chloride), too small anode area and too high current density will lead to anode passivation.
Even though the development of the electroplating industry and manufacturing industry, it is also an industry with high pollution, energy consumption and waste. However, it plays an indispensable role in many products that is made of metal material. Thus, how to effectively and appropriately guide and manage the electroplating industry is a topic that we need to pay attention to.
To solve the pollution from the electroplating radically is to adopt the green electroplating technique and high efficient cleaning production process to eliminate or remove the pollution before or during the production. By doing so, the pollution can be eliminated radically and can achieve the sustainable development of electroplating industry. In the current scientific technology development, the alloy catalyst fluid effectively solve the pollution which brought by the electroplating with simple operation and low cost.
Try GREFEE now,for free
We keep your uploaded files confidential and secure.