10 major processes to achieve product color

Posted on : Oct 6 , 2022 By GREFEE
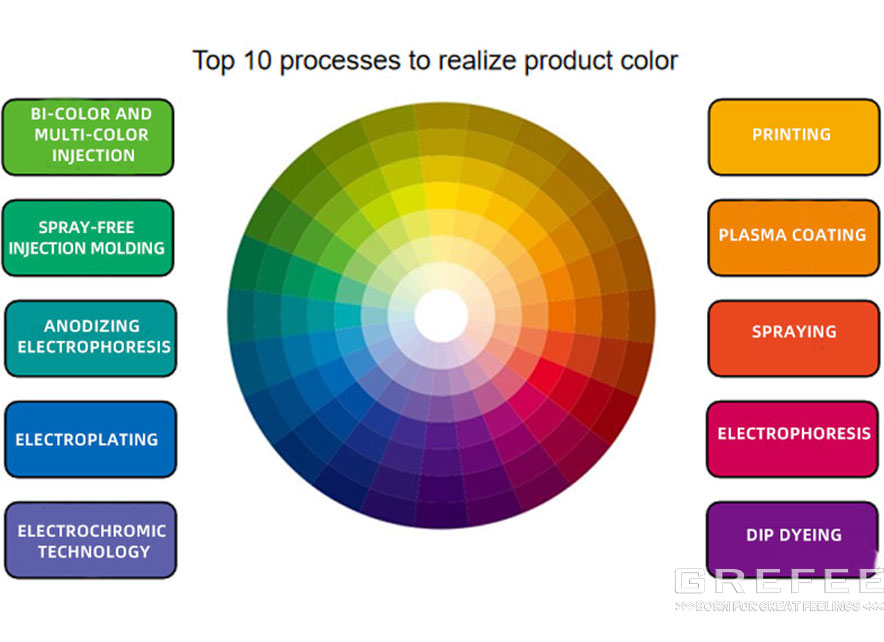
1. Bi-color and multi-color injection
Bi-color injection molding is a classical forming technology, which uses two kinds of material to obtain the injection products and can achieve different appearance effect with various glossy and sensation. In addition, it is currently widely used as it improves efficiency, lowers the cost and provides higher degrees of design freedom.
With the continual developement of products design and technolgy, bi-color injectoin molding no longer can meet the requirements. How to combine the different features, like soft touch, various color effects, LOGO, electronic devices and beautiful design together? Traditional injection molding parts assembly is too complicated, resulting in the creature of three-color and multi-color injection molding technology. This should be paid higher attention and is necessary for CMF designers and product developers to know.
It is a technology that is applied into multi-material injection molding process with multiple combine methods, such as plastic + plastic; plastic + silicone; plastic + cloth, etc. It not only makes the various combinations of colors available, but also can achieve versatility integrated through internal components, such as corresponding hardware and electronic chips can be implanted, which significantly reduces the assembly steps and saves costs. It truly realizes the miniaturization, intelligence, multi-function and personalization, and also has unique advantages in the field of precision injection molding products with small area functions.
At present, many suppliers are endeavour to research and develop multi-shot injection technique. The author learned from the communication with Hyundai Precision that their multi-shot implantation technology is now highly mature, and all kinds of injection molding equipment are independently developed, which not only can achieve bi-color and three-colors, and can also be combined with more materials to complete processing and production, which is determined by designing.
2、 Spray free injection molding
The spray free injection molding went viral since 2016 because it cuts off the post-treatments and can achieve one-time injection molding through plastic particle injection molding with special metal color effect. The products made by this has color and texture can achieve different appearance effects, such
as imitating metal, ceramics and even fabrics. As the continuous tightening of national environmental protection policies and the upgrading of products’ beautiful and colorful designs. As A choice that takes both advantages into consideration, the spray free injection materials have been applied into Mass production applications in household appliances, beauty and other industries and the future of it will be prosperous.
High gloss, traceless and spray free has high requirements in material selection and mold design, such as fluidity, stability, glossiness and some mechanical properties of the material. Factors that need to considered for molds include temperature resistance, water channel, strength performance of mold material itself, etc.
3、 Anodic oxidation
The anodic oxidation is a common color film process used for metal products, especially for aluminum alloy products. It is a kind of electric chemical reaction. Metals in the specific electrolytes, plus the process of forming an oxide film on the anode by current. The technique has been quite mature, so we won’t introduce traditional crafts too much. Below will display the gradient anode and image texture anode effect.
As the gradient color goes viral, the gradient anodizing process is gradually adopted in many areas and has been largely produced. The principle is quite simple. After the anodizing, controlling the coloring time in the dye pool to achieve the effect of gradient color. The longer the dying time, the more dye enters, the deeper the color. Through the operation of computer, time for the areas that need to be dying is accurately controlled, such as gradually remove the dye from the workpiece to achieve even coloring effect. After sealing the holes, it is the so-called gradient anode process.
Not only color, it also can produce patterns. Below, the appearance effect is the pure anode oxidation, of which the texture is achieved by secondary anode oxidation without using etching process.
The following pics are also provided by the GREFEE, focusing on the image anodizing is manufactured by patented technology. For more information of suppliers, reaching out our staff for surface treatment services.
The two pictures are the micro arc-oxidation process is developed from the anodic oxidation technology, and the coating formed is better than the anodic oxidation.
4、 PVD coating (electroplating)
PVD is currently the most used coloring technique for the back cover of phone. In addition to the color, it also improves the metallic luster and texture.
PVD is physical vapor deposition, so the whole process is a physical principle. Simply speaking, it separates and transfers the target material to the substrate surface by some means to improve the hardness, wear resistance, and chemical stability of surface. In the meantime, it also can be used for decoration. Things used on the mobile are generally magnetron sputtering plating.
Flow of PVD coating:
As the gradient color appears, the gradient vacuum plating (gradient PVD) process is gradually adapted in a large number of products. The gradient effect can be achieved by accurately changing and controlling the film thickness or superimposing coating pigments. The more precise the effect, the better. Generally, it is in the nanometer level.
The application of electrochromic technology in mobile phones started in 2020, and is commonly used in mobile phone casings. This is a more creative design to realize color change, which can realize multi color in one machine.
The color changing mobile phone can realize the gradual change between silver gray and dark blue within 10 seconds. It is currently the first electrochromic mass production model in the mobile phone industry.
The principle of electrochromism is simply to realize the reversible change of color under the action of an external electric field. The EC (electrochromic layer) thin film material in the film structure undergoes redox reaction under the action of electric field, resulting in changes in the transmissivity and reflectivity of light, thus realizing changes in the appearance color and transparency of the product.
6、 Printing
The concept of printing is relatively broad. Silk screen printing, UV transfer printing, thermal transfer printing, water transfer printing, hot stamping, concave convex printing, pad printing, embossing, etc. commonly seen belong to the category of printing. Some are mainly used for color, and some are used to achieve texture patterns. They are a very traditional surface treatment process, which will not be mentioned here. With the popularity of gradient color, gradient printing has been applied more and more. The following mobile phone cover plate is a color effect achieved through gradual offset printing.
7、 Plasma coating
Plasma coating works by the plasma coating of the surface of products to achieve the metal texture that is usually obtained by electroplating (Specular highlight, matte, semi matte, etc). The color can be adjusted. The technique and used material don’t contain heavy metals, which are environmentally friendly. It is a high-tech developed and applied across borders in recent years with wide application range. The materials include resin rubber, ceramic, metal, glass, wood, gypsum, etc. The application fields include mobile phone accessories, automobiles, electronic appliances, home decoration, daily necessities, handicrafts, etc.
Flow:
During the whole manufacturing process, the coating materials and equipment are the keys, deciding the appearance effect and quality of products.
Process characteristics:
Wide applications, multi-materials and products can be adopted.
Environmentally friendly, technique and materials do not contain heavy metals and toxic chemical substances, which are harmless to humans.
Low investment. No need of large slots and complicated and multiple equipments with low energy consumption. Generally the electroplating is about 50%.
Good adhesive of coating.
Simple to operate.
Excellent properties of surface coating with great impact resistance, hardness, corrosion resistance, temperature resistance, aging resistance, etc.
8、 Spraying
Spraying is the most used surface treatment technique, which is generally through spray gun or atomizer, coating paint (paint, etc.) on the product surface to form a decorative or functional film. It is mainly used into in many fields, such as mobiles, automotive home appliances and household appliances. Now, the technology has been extremely mature. The range of spraying is wide, which includes the plasma coating.
As the gradient color goes viral, gradient spraying is gradually applied in various product fields, which is generally utilizes the spraying equipments that contain two and more color coating materials. Though the modification of the structure of equipment, one color will be slowly transited to another color to form a new decorative effect.
In addition, color technology and electrophoresis: generally, the primer is painted in a single color, mainly is the black gray. Immersion: traditional color technology is not widely used in the mobile products filed. As the development of industry and technology, the public gradually has a higher needs for the aesthetic values. In designing CMF products, we should also pay attention to the combination of other technology and materials to further achieve better appearance effect, which is essential.
MORE BOLG
Insert mold in injection mold service
What are advantages and disadvantages of Zinc alloy and Aluminum alloy?
Inspection standards for injection molded partappearance
How to judge the quality of your plastic products?
Inspection standards for CNC machining
To ensure that your products are 100% qualified
Categories
Try GREFEE now,for free
We keep your uploaded files confidential and secure.