Surface treatment of aluminum alloy die casting parts

Posted on : Sep 21 , 2022 By GREFEE
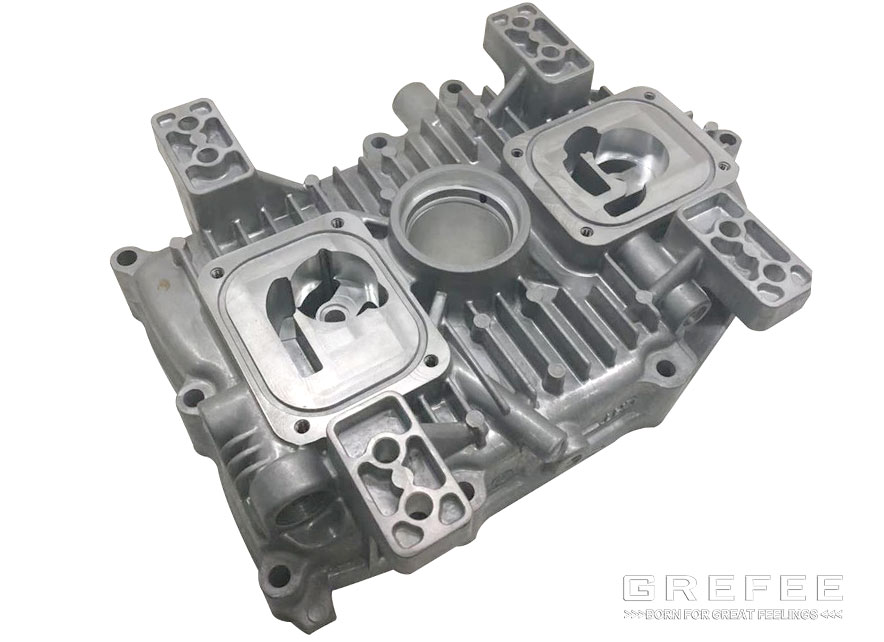
There is a series of surface treatment procedures before a aluminum alloy die casting part is considered as qualified to be used, such as de-burring, surface strengthening, etc. The following are the common surface treatment methods.
Method 1: Aluminum phosphating
Through a series of methods, including the SEM, XRD, potential time curve, film weight change and others to research on the influence of accelerator, fluoride, Mn2 +, Ni2 +, Zn2 +, PO4 and Fe2+ on the process of aluminum phosphating. The results of the research show that: guanidine nitrate has the good water solubility, low dosage and rapid film formation, which is an effective promoter for aluminum phosphating. Fluoride can promote film formation, increase film weight and refine grain; Mn2 +, Ni2 +, can obviously refine the grain, make the phosphating film uniform and dense, and improve the appearance of the phosphating film. Low concentration of Zn2 + will cause the film failed to be formed or obtain poor film formation. The Zn2 + concentration increases as the film weight increases. PO4 content impacts the weight of phosphating film, and PO4 is increased. The content increases the weight of phosphating film.
Method 2: Alkaline electrolytic polishing process of aluminum
After researching the alkaline polishing solution system and comparing the influence of corrosion inhibitor and viscosity agent on polishing effect, we obtain the alkaline polishing solution with good polishing effect and it not only decreases the operating temperature but also extends the service life. In the meantime, the polishing effect of the additives is improved as well. Based on the experiment, a certain amount of the additives in NaOH solution can generate great polishing effect.
The result of experiment also shows that after the DC constant voltage electrolytic polishing with NaOH solution containing glucose under certain conditions, the surface reflectivity of aluminum can reach 90%. However, due to the uncertainties of the experiment, it is still need to be further researched. The research adopts the DC pulse electrolytic polishing method under the polishing aluminum under alkaline condition to see its feasibility. The result shows that the pulse electrolytic polishing can achieve the flat effect that can be obtained from the DC constant voltage electrolytic polishing, but the speed is slow.
Method 3 aluminum and aluminum alloy environmentally friendly polishing
The new technology that develops the environmental friendly chemical polishing with phosphoric acid and sulfuric acid as base solution is confirmed, it will achieve zero exhaust of Nix and over the quality defects that are found in the previous similar technologies. The key of the new technology is to add some special used chemical substances to replace the nitric acid in the base solution. So, we need to analyze the three acid chemical polishing process of aluminum, especially the function of the nitric acid. The main function of the nitric acid in the aluminum chemical polishing is to Inhibit pitting corrosion and improve polishing brightness. Combined with the chemical polishing test in pure phosphoric acid and sulfuric acid, adding special substances into the phosphoric acid monosulfuric acid will inhibit the corrosion, ease the corrosion overall and obtain great flat and brightening effect.
Method 4: Electrochemical surface strengthening treatment of aluminum and aluminum alloys
The process, properties, morphology, composition and structure of ceramic like amorphous composite conversion film formed by anodic oxidation and deposition of aluminum and aluminum alloys in neutral system are discussed.
Based on the research result, the concentration of film-forming promoter should be controlled to be 2.5 ~ 3.0g/l in the Na_ 2WO_ mixing system.
The concentration of complexing agent is 1.5 ~ 3.0g/l_ 2WO_ 4 concentration is 0.5 ~ 0.8g/l and the peak current density is 6 ~ 12a / DM2. Slightly stiring the fluid can obtain the complete and even gray series inorganic nonmetallic film layer of which the film thickness is 5-10 μ m and the microhardness is 300 ~ 540hv with great corrosion resistance. This neutral system has good adaptability to aluminum alloys, and can form films on different types of aluminum alloys, such as rust proof aluminum and forged aluminum.
Method 5: surface treatment technology of YL112 aluminum alloy
YL 112 aluminum alloy is widely used int eh structural properties of automotive and motorcycle. The metal surface will be oxidized under various heat treatment, mechanics operation, transportation, and maintenance, then generating a oxide layer with uneven thickness. At the same time, it will also be affected by different grease and adhere to other impurities.
The grease and some adhere impurities on the oxide layer can be cleaned by the solution, or cleaning with chemical treatment and mechanical treatment or only medical treatment. For metal surface with server oxidization with thick oxide layer, the surface cannot be cleaned or treated with chemical solution, it is better to fix with mechanical treatment.
Metal surface after the treatments will have higher flexibility, and is more likely to be contaminated by the dust or mist. For this, the metal surface should be fed quickly after the treatment in case the pollution.
The storage period of metals after different treatments is as follows:
(1). Wet sandblasting aluminum alloy, 72h
(2). Chromic acid sulfuric acid treated aluminum alloy, 6h
(3). Anodized aluminum alloy, 30 days
(4). Sulfuric acid treated stainless steel, 20 days
(5). Sandblasting steel, 4H
(6). Brass with wet sand blasting treatment, 8h
Degreasing treatment: wipe with degreasing cotton dampened with solvent, remove the oil stain, and then wipe with clean cotton cloth for several times. Common solvents are trichloroethylene, ethyl acetate, acetone, butanone and gasoline.
After degreasing, it should be chemically treated in the following solution: concentrated sulfuric acid 27.3 potassium dichromate 7.5 water 65.2 immerse in 60-65 ° C for 10-30min, then take out and rinse with water, air dry or dry under 80 ° C.
It could also be fired in the following solutions: Acid 10 n-butanol 3 water 20 this method is applicable to phenolic nylon glue, and others with good effect. After degreasing, it is chemically treated in the following solution: ammonium hydrogen fluoride 3-3.5 chromium oxide 20-26 sodium phosphate 2-2.5 concentrated sulfuric acid 50-60 boric acid 0.4-0.6 water 1000 is immersed at 25-40 ° C for 4.5-6min, i.e. water washing and drying.since this method has a high bonding strength and the bonding is within 4h after treatment, which can reapplied for epoxy adhesive and epoxy butyric acid adhesive bonding.
After degreasing, chemically treated the metal in the following solution: phosphoric acid 7.5 chromium oxide 7.5 alcohol 5.0 formaldehyde (36-38%) 80 is immersed at 15-30 ° C for 10-15min, and then washed and dried at 60-80 ° C.
After degreasing, perform the anodizing treatment in the following solution: immersing the metals in the 22G / L concentrated sulfuric acid 10-15min under the DC strength of 1-1.5a/dm2, and then immersed in saturated potassium dichromate solution at 95-100 ° C for 5-20min, then washed with water and dried.
MORE BOLG
Insert mold in injection mold service
What are advantages and disadvantages of Zinc alloy and Aluminum alloy?
Inspection standards for injection molded partappearance
How to judge the quality of your plastic products?
Inspection standards for CNC machining
To ensure that your products are 100% qualified
Categories
Try GREFEE now,for free
We keep your uploaded files confidential and secure.