Common Riveting Applications of Plastic Parts

Posted on : Dec 3 , 2022 By GREFEE
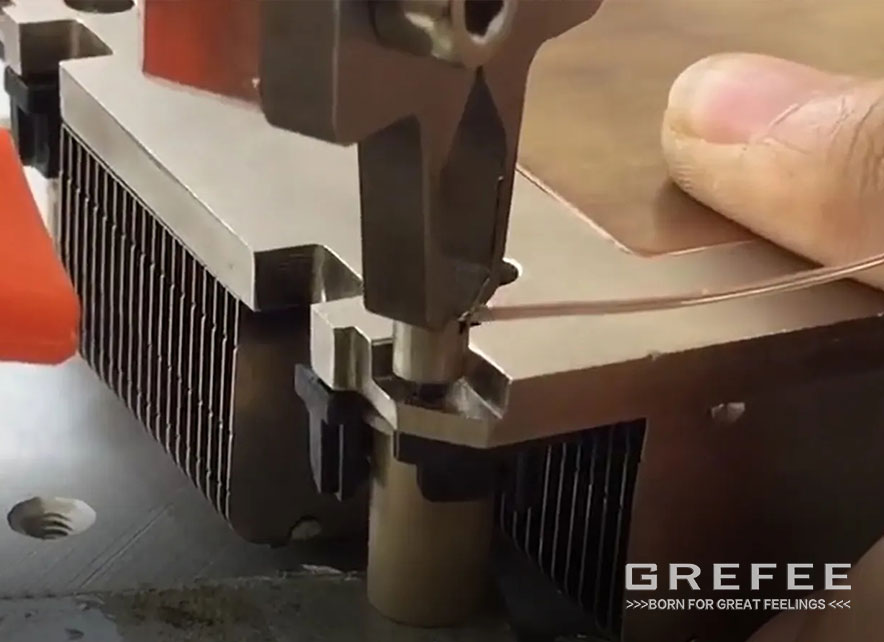
For the riveting of plastic parts, the main body is plastic parts, and the connected parts include plastic parts, metal parts (such as metal sheets), electrical components (such as PCB boards), fabrics (such as mesh cloth), etc. The riveting does not require additional rivets or riveting posts and other accessories like metal riveting, but directly grows plastic structures on the plastic body, such as columns and rebar positions. These make them pass through the connected parts, Then, heat and soften the protruding column or reinforcement position, shape it under the compression of rivet head, and complete the riveting after cooling.
According to the heating and softening methods, it includes three riveting processes
Hot press riveting
Hot press riveting is contact riveting. Part of the technology is to set the heating pipes at the front of the rivet head, then heat the metal rivet head by the heating pipes. Thus, the size of the whole metal rivet head is larger, but the heating efficiency is low. At present, the common technology is to make the metal hot rivet head can generate heat by itself without conducting heat through a heating block or a heating tube by high frequency pulse heating principle. The advantage of this method is high heating efficiency because the metal rivet head is small and can be applied into multiple applications.
time 00:11
Hot air riveting is also called the hot air riveting or hot air cold riveting, which is non-contact riveting.
Hot air cold riveting mainly works by utilizing the heating source to heat the rivet column and shape. The whole process include two processes. First is to heat the rivet column evenly with hot air until it is molded state. During this process, the stable temperature and uniform air volume is essential for the heating of rivet column.
In the second process, the cold rivet head compresses the soften rivet column into the firmed rivet head. Since the rivet column have been heated and softened, the shaped rivet head can firmly and firmly fix the parts to be riveted. In the process of hot air cold riveting, the gap between the rivet column and the opening on the workpiece to be riveted should not be too large. If the gap is large, the soften plastic will run into the gap during the riveting process and cause unstable size of rivet head.
Ultrasonic riveting, also is a kind of contact riveting. The process is as follows:
How to select correct riveting process and what are the advantages and disadvantages?
Common advantages :
1. Simple structure without complex designs and low cost.
2. Simple assembly without extra accessories or fasteners, high reliability
3. Multiple welding points can be riveted at one time, assembly efficiency increased
4. Not suitable for the connection between plastic parts, but also metal parts and other non-mental parts, especially for some occasions where space is limited and other connection methods are difficult to adapt.
5. The parts after riveting is applicable to long term mechanical vibration, environment temperature, and human changing, occasions where the natural environment is extremely harsh.
6. Simple operation, energy saving, high speed. Nil special technical skills required for operators, and the quality inspection can be done visually.
Common disadvantages:
1. Extra riveting tools and tooling fixture.
2. Not applicable to occasions with high requirements in strength or under long-term load.
3. The riveting process is permanent connection and fixation, not applicable to occasions where disassembly and repair required.
4. Once was invalid, it will be permanently invalid and is difficult to make up with repairing. Thus, if necessary, some remedial measures shall be taken in the structural design stage).
Comparison of advantages and disadvantages
Comparison program | Hot press riveting | Hot air riveting | Ultrasonic riveting |
Riveting strength | The metal hot melting head directly works on the rivet column, directly melting and compressing. High stress, unreliable strength after riveting and sensitive to vibration. | Heating the whole rivet column and reduce the stress. The strength is high after riveting and is not sensitive to the vibration. | The ultrasonic welding head directly acts on the rivet column and vibrates with high frequency, causing high stress and unreliable strength after riveting |
Fixed effect | The pressure head acts on the upper part of the riveting column to soften while pressing down. The root of the riveting column cannot be completely softened. The product assembly gap is not filled, and the fixing effect is defective. | great. After the rivet column is softened as a whole, it can be rapidly formed under the effect of pressure, which can completely fill the product assembly room. | The welding head acts on the upper part of the welding column and softens while pressing down. The root of the rivet column cannot be completely softened. The product assembly gap is not filled, and the fixing effect is defective. |
Riveting speed | Small riveting points 6-10g, big riveting points 50-60g. | 6-10s heating, 2s cold riveting | Less than 5s |
Equipment flexibility | Heating and welding are integrated, customized according to the product, and the type change is complex. | The heating and cold riveting can be adjusted independently. The air nozzle can be customized according to the rivet column, and the riveting point temperature can be adjusted independently. | the depth or amplitude of riveting and spot welding cannot be controlled separately if it is integrated welding head. |
appearance of riveting point | bright and perfect surface, easy to wire drawing. | Bright, matt surface in most cases, no wire drawing | The surface is bright and beautiful. |
Material adaptability | Glass fiber may precipitate, affecting the appearance. | It can be riveted to almost all common thermoplastic and fiberglass materials. | Non rivetable or difficult to rivet glass fiber materials. |
Impact on products | For contact heating riveting, the heat of the hot melt head will affect the surface of components or products near the rivet column. | Non-contact heating riveting without damaging the appearance of components or products. | Using vibration heating riveting, and the vibration will damage the components to a certain extent |
Specifications:
Hot press riveting
The advantages of hot press riveting are obvious, the rivet head heats the rivets column and formed rivet head at the same time so that the equipment can be designed compactly, especially for rivet plastic rivet posts with close spacing on smaller workpieces.
The disadvantages are also evident. Due to the insufficient cooling of hot rivet head, there are still some heat left so that the rivet column plastic will stick on the rivet head and cause wire drawing. Thus, hot rivet head needs to be replaced regularly. The hot press riveting is not applicable to the large size rivet column as the heated surface is more and more difficult to transmit surface heat to the center and bottom of the rivet column, so cold core may exist in the center of the rivet column. The gap between rivet column and connectors cannot be filled. In addition, the stress of hot press riveting products is large, but the drawing strength is slightly low. So, the hot press riveting is also not recommended in the products with high requirements for riveting, positioning and fixing.
2. Hot air riveting Since the plastic riveting columns are heated evenly under the hot air environment of several hundred degrees and thus the plastic rivet columns is softened completely, which effectively reduces the internal stress after forming. In the second step, the cold rivet head stamping, the complete softened plastic material can be filled quickly into the 90% gaps between connectors and rivet columns. Thus, it can achieve great fixing effect.
3. Ultrasonic riveting The riveting strength and fixing effect of ultrasonic riveting is similar to the hot press riveting. However, due to the friction generates heat, after the riveting points are formed, the ultrasonic wave machine also stops working, the welding head does not required to be completely cooled as the hot rivet head for hot press riveting. In another word, the ultrasonic welding head has no heat, so low possibility of wire drawing. Meanwhile, there is also the shortest time for ultrasonic riveting.
If uses the ultrasonic riveting, the rivet column cannot be designed on the plane with large height difference, because the height difference will lead to the amplitude difference of different riveting points, the column will be heated at different rates, causing one of the columns may loosen or material degradation due to high temperature when another column has riveted and formed. If use one welding head to rivet, the distributor distance of columns may be limited. While in the hot press or hot air riveting process, the review column can be designed on different planes with a quite far distance, but it can still achieve multipoint riveting at one time.
Adaptability of materials
The plastic rubber material can be divided into thermoplastic and thermosetting plastics, and riveting are only suitable for thermoplastics as they can be melted in the certain temperature range. While the thermosetting plastic will be cursed when the temperature reaches a specific level and is hard to carry out riveting thorough the above three methods. Therefore, riveting is normally for thermoplastics, and thermoplastics are often selected in terms of product structure.
Thermoplastic plastic is also divided into amorphous plastic and crystalline plastic.
For non crystalline plastics, the molecular arrangement is disordered and the temperature (Tg glass transition temperature) can soften, melt the material gradually until it flows. The above three riveting processes is applicable to this kind of plastic.
For crystalline plastics, not only the molecules are orderly arranged, but also has obvious melting point (Tm melting temperature) and re freezing point. Before the temperature reaching the melting point, the semi crystalline plastics remain solid all the time. When the temperature reaches the melting point, the whole molecular chain will start moving, and plastic will start melting. If the heat is reduced at this moment, the plastic will be cursed soon. Fig 3-106 presents the difference between the melting processes of amorphous plastics and semi crystalline plastics.
Thus, as the rivet head of hot press riveting plays the role of heating the rivet column and forming the rivet point at the same time, the crystalline plastic is more suitable for hot press riveting.
The crystalline plastic has a regularly distributed molecular structure similar to a spring, which is helpful in absorbing the high frequency ultrasonic vibration energy. Thus, it is difficult to produce heat on the jointing plane of rivet column by high frequent vibration and the crystalline plastic often has high melting point, which only can be melt with sufficient ultrasonic energy. Thus, comparing to non-crystalline plastic, the crystalline plastic is more difficult to rivet. To obtain sufficient higher riveting quality of crystalline plastics, many factors need to be taken into account. For instance, higher vibration, appropriate joint surface design, welding head contact, welding distance, welding fixture, etc. Moreover, in order to concentrate the ultrasonic energy, the top of the rivet column should be designed to minimize the initial contact with the welding head.
3) for plastics with additive material (eg. Glass fiber), due to the big difference in melting point between the plastics and glass fiber. If it is hot press riveting, the temperature should be controlled within ±10°. The glass fiber will be separated from the plastic if the temperature is too high and cause the material sticking and rough surface. If the temperature is low, then it may cause cracks and cold forming. In case of ultrasonic riveting, more vibration energy is required to melt the plastic. High content of glass fiber is too high will cause the waste residue will appear at the riveting part and fall off after ultrasonic riveting. Therefore, the riveting strength will be reduced, and the riveting is not reliable.
There is no big difference to the properties of material when feeding is lower than 10%. Moreover, these materials (eg. Glass fiber) is greatly helpful in riveting soft material. For example, PP, PE and PPS, etc. When the feeding is within 10%~30%, the strength of riveting will be decreased. When it is higher than 30%, the riveting effect may be affected.
Geometric shapes and structural dimensions of common rivet columns and rivet heads
1. Half round rivet head (large profile)
1) applicable to columns of which the D1 < 3mm and is better than 1mm, to prevent the break.
2) the height of column projection area, H1, is generally (1.5-1.75)*D1;
3) the diameter of rivet head, D2 is normally around 2*D1, the height, H2 is about 0.75*D1. The specific number should be based on: Volume conversion S head=(85% – 95%) * S column;4)
This type is the most common, generally is used to the occasions that do not require high strength, for instance PCB plate, plastic trim, etc.
2. Half round rivet head (small profile)
1) applicable to the rivet column of which the D is lower than 3mm, and is better than 1mm to prevent the breakage.
2) the height of the projection area of rivet column, H1 is normally 1.0*D1;
3) the diameter of rivet head D2 is about 1.5*D1, height H2 is about 0.5*D1, the specific number should be based on volume conversion S head=(85% – 95%) * S column;
4) the riveting time of this is shorter than that of the large profile semicircle rivet head riveting, which is normally applied into occasions that do not require high strength, such as FPC flexible cable, metal spring, etc.
3. Double semicircle rivet head
1) applicable to the riveting column, the diameter D1 = (2-5)
2) the height of the projection area of review column H1 is normally 1.5*D1.
3) the diameter of riveting head D2 is normally about 2*D1, height H2 is about 0.5*D1. The specie number should be according to the volume conversion S head=(85% – 95%) * S column;
4) the rivet columns of this type is slightly larger than that of the half round head type. To shorten the time of riveting and to obtain better riveting effect, double half round head type can be adopted, which is normally used into occasions that require higher fixing strength.
5) the center of the riveting head and hot rivet head of mold should be aligned so that qualified rivet heads can be obtained.
4. Annular rivet head
1) applicable to riveting head of which D1 is higher than 5mm.
2) the height of projection area of riveting columns, H1 is normally (0.5-1.5)*D1. The larger the diameter, the smaller the value, inner D is 0.5*D1 (The principle is to avoid shrinkage at the back of the column);
3) the diameter of riveting head D2 is normally about 1.5*D1, height H2 is about 0.5*D1. The specific number should be according to the volume conversion S head=(85% – 95%) * S column;
4)when the diameter of rivet column is gradually increasing, hollow rivet columns will be adopted to shorten the time of riveting and to obtain better riveting effect. In the meantime, it can prevent the shrinkage on the back of the columns, which is normally applied into occasions that require fixing strength.
5) the inside and outside of hollow rivet columns are being heated evenly, which is helpful in obtaining qualified riveting heads.
5. Flat head rivet head
1) the diameter of rivet columns D1 is less than 3mm
2) height of the projection area of riveting columns, H1 is normally 0.5*D1
3) the diameter of riveting head D2 and height H2, the specific number should be according to the volume conversion S head=(85% – 95%) * S column;
4) the connected piece require sufficient thickness design counterbore, otherwise the connection will not be stable and fixing strength may be insufficient
5) the flat rivet heads are suitable for rivet head after forming without projection areas.
Rivet reinforced vertical head
1) the diameter of column bottom, D1 is less than 3mm, the diameter of top D3=(0.4-0.7)*D1;
2) height of the projection area of riveting columns H1 is generally 1.5-2)*D1, H1 is less than the height L of the riveting columns.
3) the diameter of riveting head D2 is about 2*D1,height, H2 is about 1.0*D1. The specific data should be according to the Volume conversion S head=(85% – 95%) * S column;
4) rivet reinforced vertical heads are applicable to the designed riveting force area is relatively large and no enough space for hollow rivet columns.
Flanging rivet head
1) diameter of column bottom,D1 is less than 3mm, diameter of top D3=(0.3-0.5)*D1
2) height of the projection area of rivet column H1 is about (1.5-2)*D1,H1 should be less than the length of rivet column.
3) diameter of rivet column D2 is normally 2*D1, height H2 is about 1.0*D1, the specific data should be according to volume conversion S head=(85% – 95%) * S column;
4) the reinforced vertical rivet heads are suitable for connectors that require crimping or wrapping.
Notes:
1. If the rivet column is on the inclined plane or the rivet column is far from the bottom surface, it should be designed into the following modes
2. Since once the riveting is filed, then it will be permanently damaged and is difficult to make up with the repairing. Thus, it is necessary to have redundancy design in structure. In the Fig below, double the rivet column and hole. The rivet column at the yellow position is used for the first time can be used with the columns at white position if repaired, so it has a chance to repair.
MORE BOLG
Insert mold in injection mold service
What are advantages and disadvantages of Zinc alloy and Aluminum alloy?
Inspection standards for injection molded partappearance
How to judge the quality of your plastic products?
Inspection standards for CNC machining
To ensure that your products are 100% qualified
Categories
Try GREFEE now,for free
We keep your uploaded files confidential and secure.