Die casting parts are everywhere in our daily life

Posted on : April 19, 2022 By GREFEE
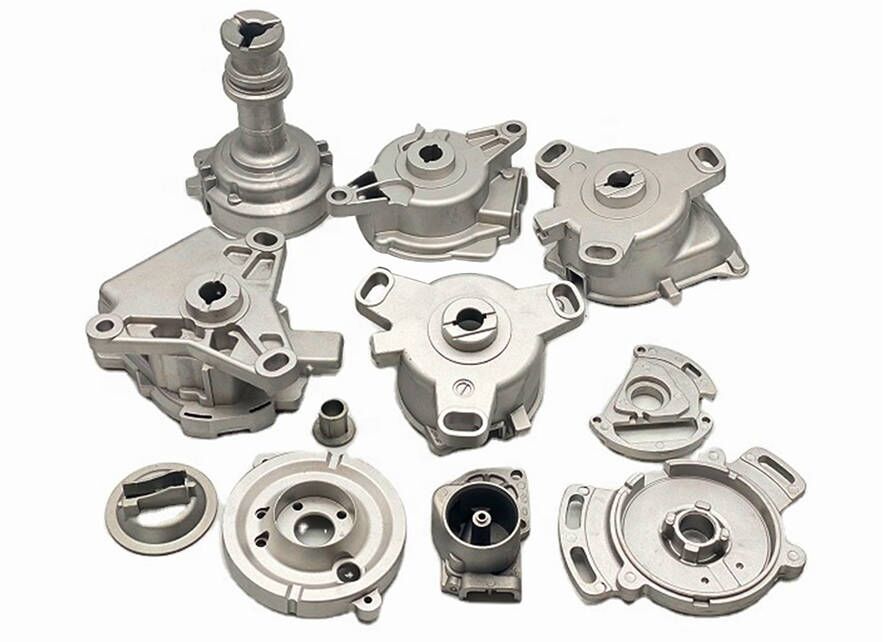
Die casting parts have always been close to us
Die casting plays an indispensable role in the automotive industry, aerospace industry, telecommuting devices, and mechanical devices due to its outstanding efficiency, stable quality, and low cost for mass production. In this article, we gonna share some knowledge about die casting. Contact us to start a new project!
1. Characteristics of die casting
- Pressure casting (die casting) is a method to obtain castings through pouring the liquid or semi-liquid metal or alloy into the cavity under a high pressure with a high speed, the molten metal forming under high pressure and then crystallised.
- Due to the liquid metal under the action of a large pressure ratio, the flow speed is quite high, and the filling time is extremely short. High pressure and high speed are the two main characteristics of the liquid metal that fill the mold in die casting. Meanwhile, it is also the fundamental difference between die casting and other casting methods.
- For example, the injection pressure is within a few MPa to tens of MPA, or even reaches 500 MPa; its filling speed is 0.5-120m/s, the filling process is extremely short, is about 0.01-0.2s, or could be as short as seconds per thousand.
2. Pros and cons of die casting
Advantages:
- High quality. As die casting has advantages of rapid thermal conductivity and cooling plus the characteristic of crystallizing under pressure, castings have a fine grain structure and strong surface due to the increase in stiffness and strength. Besides, it ensures a stable casting dimension and great interchangeability to make the thin wall and complex parts.
- high production rates, increased use times
- satisfying profit. The die casting method saves several raw materials, machining devices, and time due to the small machining allowance of castings. Generally, castings can be used only after fine machining and reaming.
cons:
- Die casting method only suits the mass production of approved products due to its complex structures, high manufacturing cost, and long provision cycle.
- High die casting speed makes the gas in the mold cavity hard to void. Apart from this, metal molds solidify quickly in molds. Actually, feeding is unavailable under this condition, which leads to small air holes and porosity. The thicker the casting wall, the server the defect is. Thus, the die casting method only suits castings whose wall thickness is less than 6mm.
- low plasticity of castings make them cannot work under the impact load and circumstances with vibrations.
- Besides, when it comes to die casted alloys with a high melting point, this type of die casting usually has the disadvantage of short service life, and this affects the application range.
- To sum up, the die casting method is suitable for nonferrous alloys and complex casting production, like the small size and thin wall. Considering the advantages of other technologies, it is only adopted when the number of workpieces is 2000 to 3000.
Application range of die casting:
Die casting method is a rapidly developed, high efficiency, less or no machining metal forming precise casting method in the modern metal processing technology.CONTACT US
There are six types of shape:
- disk — — chassis, etc.
- round cover —— – meter cover, machine cover, chassis, etc.
- round ring — — Connector, bearing retainer, steering wheel, etc
- cylinder — — flange jacket, conduit, shel shaped cover, upper cover, instrument cover, prober and control instrument cover, camera cover, carburetor, etc.
- Porous cylinder and shell — —multi-cavity shell with complex structure, like cylinder block, cylinder head, and oil pump body (this type of part has high requirement about the mechanical property and airtightness, the materiel normally is aluminum alloy). For example, the cylinder block and cylinder head of automobiles and motorcycles
- special shapes — — Impeller, horn, decorative castings, of which texts are made of the steel ribs, etc.
3. Die casting machine
Die casting machine is the base for die casing. There are two types, which are hot chamber die casting machine and cold chamber die casting machine.
- hot chamber die casting machine
- Its characteristic is that its chamber is integrated with the alloy melting furnace. Chamber socked into the molten liquid metal, of which its injection mechanism is on the heat preservation crucible. When the injection piston lifts, the liquid metal gets into the chamber through the inlet, then the piston falls, during which the liquid metal in the pipe fills the mold cavity through the nozzle. The piston lifts after solidifying, and the remaining liquid metal return to the chamber. Now, the operator can open the chamber and take the casting.
- The characteristics of a hot chamber die casting machine are its simple procedures, high production rates, and a high automation realization rate, less consumed liquid metal, stable technique, and clean metal without oxidization. It is easy to achieve high quality castings. However, the chamber and piston staying in the liquid metal for a while will affect the service life. Currently, it is mostly used for zinc alloy die casting parts and other low melting point alloy castings, sometimes for magnesium castings or aluminum castings.
(2)cold chamber die casting machine
This type of chamber is separated by the heat preservation crucible. When working, pour the liquid metal in the heat preservation crucible into the chamber and die casted. Cold chamber die casting machines are divided into two types, horizontal cold chamber die casting machines and vertical cold chamber die casting machines.CONTACT US
The centerline of the vertical cold chamber die casting machines is perpendicular. After mold clamping, the liquid metal poured into the chamber is held by the reverse piston of the nozzle holes. When the injection piston lowers down to the liquid level, the reverse piston starts falling. Opening the nozzle, then the liquid metal will be compressed into the mold cavity. After solidification, the injection piston returns, and the reverse piston lifts. Cutting off the residual and ejecting it out to the chamber. The residual falls to the original location after the residual is removed. Opening the mold and taking out the casting.
The centreline of the horizontal chamber die casting machine is horizontal. For the correct place of the castings and the chamber, as well as the die casting process, see the pic below. After mold clamping, the liquid metal is poured into the chamber, and the injection piston is pushed forward, which compresses the liquid metal into the cavity through the runners. When opening the mold, the residual is out of the chamber with the help of the injection piston. With the piston moving forward, the casting releases in the meantime.Comparing two different die casting machines, the difference between the two is the structure of the injection machine. CONTACT US
Also, The vertical die casting machines have a lower cylinder that can cut off and eject the residual. Due to its complex structure, it is hard to repair. The horizontal die casting machines are simple and easy to repair. Technologically, the air in the vertical die casting machines will not get into the mold cavity with the liquid metal. It is easy to make a center gate. However, due to a long gate, the amount of metal consumption raises, the energy loss in the filling process raises, too. Due to a short flow distance, the pressure loss is less. This helps with the final pressure transmission and the specific pressure increases. So it is widely used. The cold chamber die casting machine is driven by hydraulic pressure. The high pressure suits alloys with a high melting point. Currently, cold chamber die casting machines are more common in production.
4. Die casting theories
Die casting uses high pressure and high speed to fill the casting mold with molten or semi-molten metal in the die casting chamber.
There are three major phenomenons during the process: first is inject, second is the molten metal flow inside, third is cooling and solidification.
There are three aspects of a successful die casting process: first is molten or semi-molten metal; second is die casting molds; third is a die casting machine. The primary process coefficient is die casting pressure and die casting spe
Die casting pressure:
The die casting pressure is represented by injection pressure and specific pressure. The injection pressure is decided by the specs of the die casting machines, which is the force when the injection mechanism of the die casting machine pushes the piston: Pr=PG•πD2/4
injection specifc pressure: Pb = Pr / F = 4 P r/ πd2
Four stages: slowly sealing the holes; filling; increasing pressure; holding pressure
5. Die casting speed
Die casting speed has two different concepts: injection speed and filling speed
Injection speed: the speed that when the hydraulic pressure inside the injection cylinder pushing the piston to move forward during the die casting process.
Filling speed: the linear velocity of the molten alloy to fill into the cavity through the inlet under the pressure.
The major function of filling speed is: filling the molten metal into the cavity immediately before it solidified, which is an important factor to obtain castings with clean outline and surface; it is also for obtaining high hydrodynamic pressure.
The selection of the filling speed should follow several aspects, including the characteristics of the property of alloys and casting structure, filing speed, injection specific pressure, injection speed, and the inlet section area, etc.CONTACT US
Due to the high speed, even with low specific pressure, we can still obtain the castings with clean surface finish.
Too high filling speed will lead to many defects. Unfavorable conditions for die casting process:
- warp the air, and air bubbles form. The high speed liquid alloys might block the venting system, causing air trapping inside the cavity. Meanwhile, the quick cooling liquid is unable to precipitate the air which dissolved in the melt effectively.
- liquid alloy gets into the cavity and sticks onto the walls due to the spray form, which cannot fuse with the liquid alloy injected afterward, causing the surface defects and lowering the surface quality.
- causing the vortex and the vortex wraps the air and the cold alloy which is injected into the cavity, which leads to the air holes and oxidization mingled defects.
- flushing the cavity walls of die casting mold will deteriorate the wear condition and shortens the service life.
- The filling and injection speed, the injection specific pressure on molten alloy and density of liquid alloy, and the bore size of the chamber are all related to the section area of the inlet. The high the injection speed, the high the filling speed is. The high the injection specific pressure of alloy, the high the filling speed is. The change of the filling speed can also be achieved by changing the injection speed, injection specific pressure, and bore size of the chamber or by increasing the section area of the inlet (thickness).
6. Die casting design
The design of castings is an essential part of the die casting technology. The feasibility of design and the technology adaptability directly affect the selection of parting surface, the set of the gate, the outlay of the ejection, the contraction rules, the guarantee of the accuracy, the location of defects, production rates, etc. The specific structure requirements of castings are:
- Fixes the internal side groove to help with the core pulling.
- Improves the wall thickness, fix the contract holes, air holes;
- Improves the structure, fixes the side grooves which are not easy to press out
- To prevent the deformation by ribs
- Improves the structures, fixes the closed angle and corners
- Improves the structures, easy to pull the core, simplify the die casting manufacturing process
- Fixes the grooves to make the castings easy to release.
- Improves the structures to prevent the core from being crossed, etc.
7.Die casting alloys and the choice
The requirements for die casting alloys:
- Enough stiffness and formability under high temperature, without thermal brittleness (or low thermal brittleness)
- Contracts as small as possible
- Small crystallization temperature range
- Sufficient fluidity under low superheating temperature
Factors need to consider to select the die casting alloys:
- the stress state of the castings is the main reference for selecting alloys
- the working environments of castings
- Working temperature: high temperature and low temperature requirements
- Contact medium: moisture air, seawater;
- Airtightness requirements: air pressure, tightness of the hydraulic pressure
- the working conditions of the castings in the overall unit or parts
- the requirements of the size and weight for castings
- production conditions: melting devices, die casting machine, process unit, materials, etc.
- economical
8. Die casting mode
In the die casting production, the die casting molds (molding)are the important process units.
From the aspect of structure, the complete die casting molds are composed of several parts:
- Fixed part:the access through which the liquid alloy flow into the casting mold is fixed on a fixed mount plate of one side on the chamber, which is also a composed part of the casted cavity. The sprue on the plate is directly connected with the nozzles or chambers of the die casting machines.
- Moveable part: moveable part is fixed on the movable mount plate of the die casting machine and moves left and right with the dynamic mount plate, separating and clamping with the static part. Ordinary core pulling mechanism and casting ejection mechanism are in this part, which is the composed part of the die casting cavity.
- Forming part: forming part is the part of the geometrical shapes of castings. The exterior of casting is called the cavity. The part formed in the internal shape is called the core.
- Pouring system: connects the forming part and chamber. It guides the liquid metal to flow into the molding part of the casting mold in a specific direction, including sprue, runner, and inlet.
- Core pulling mechanism: formed the side groove and holes of complex castings. It utilizes the movable core by finishing the action before ejecting the casting with the core pulling mechanism.
- Ejection mechanism: after the casting molding process, take the castings out of the casting mold till the dynamic and static parts are separated. This mechanism is usually set in the movable part.
- Venting part
- Heating and cooling parts: balances the temperature of the casting mold to ensure the quality of casting due to the sudden temperature change. In many cases, the casting mold should install heating and cooling devices.
- Others: inside the casting mold, there is also parts, like positioning, guiding, fastening, etc.
9.Defects
The defects of castings are diverse, which include surface defects, internal defects, cracks, incorrect geometries, material property, impurities, etc.
Surface defects include flow marks, textures, dicta-burrs, cold-shuts, sinks, compressions, cold shots, etc. The surface damages include mechanical strain, die sticking strain and collision;
Internal defects include air holes, air bubbles, shrinkage, porosity.
The geometrical shape is not in line with the drawing is due to factors like undercasting, unclear outlines, deformation, burrs, overfeeding, containing other materials, malposition, thread alternating, and core deviation;
The material property is not in line with the requirements, which means the chemical composition and mechanical properties. The impurity defects refer to slag inclusion and hard spots.
Although die casting defects are various, however, after analysis, we can know they are all related to the selection of the coefficient of die casting technology, die casting design, and operation. For example, flow marks and textures might result from the low mold temperature, low specific pressure, the small section area of the inlet, etc. Of course, the solution is to adjust the mold temperature, the section area of the inlet, injection speed, or pressure.
With many years of experience, GREFEE has grown into a company with a competitive production capability of die casting molds, especially the automotive parts and telecommunicating parts. GREFEE has won customers from over 20 countries. Try GREFEE to turn your ideas into actual products.
Try GREFEE now,for free
We keep your uploaded files confidential and secure.