Four things you need to know about ultrasonic welding

Posted on : Dec 1 , 2022 By GREFEE
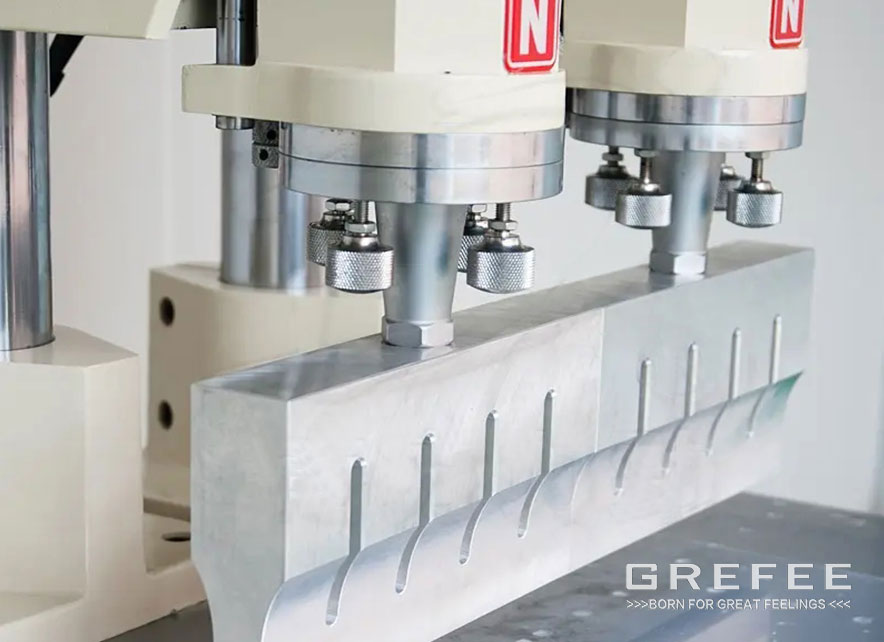
Metal welding
Welding: welding makes the two separated objects produce the binding force between atoms together by heating or compressing or both, rather than filling materials.There are a variety of them, which traditionally means the welding of metals. It has more than 40 types, which includes fusion welding, pressure welding and brazing according to the process of welding.
2. Pressure welding
Under the pressure, the two workpieces can achieve inter atomic bonding under the soil status, also known as solid state welding. Common welding techniques include resistance butt welding. When the electric current passes through the connecting sides of two workpieces, the temperature rises due to high resistance. When it is heated to plastic state, it is connected together.
3. Brazing
Using metals of which the melting point is lower than that of workpieces and heat them to the point which is higher than that of filler metal but lower than that of workpieces. The method of welding is realized by wetting the workpiece with liquid solder, filling the interface gap and realizing the mutual diffusion between atoms and the workpiece.
Plastic welding
Not only metals can be welded, but also plastics. The key of plastic welding is to heat and soften the plastic material at first. According to the difference of softening method, the welding method can be divided into external heat source softening, mechanical motion softening and electromagnetic action softening.
1. external heat source softening
Welding technique with external heat source softening method: Hot plate welding, hot air welding, hot rod and pulse welding.
2. Mechanical movement
Welding technique with mechanical movement: friction welding, ultrasonic welding
3. electromagnetic action
Welding technique with the electromagnetic action softening: high frequency welding, infrared welding, laser welding
The three softening methods are same in essence, but differently in forms, which works by accelerating the irregular movement of molecules inside the plastic generates heat and softens the plastic.
In the plastic welding methods above, the most commonly used ones are ultrasonic wave welding due to its high welding efficiency. The whole process is finished in only few seconds. Compared to other welding methods, it does not require to pre-heat the tools and long time waiting period to wait for the joint is cured or dried.
Principle of ultrasonic welding
ultrasonic: refers to the sound waves that exceed the upper limit of human auditory range (20000Hz). Due to the high frequency, it has many features. First is large power and the energy is much larger than the general sound wave, so it can be used for cutting, welding, drilling, etc.
The equipment used for ultrasonic welding is ultrasonic welding machine
Plastic ultrasonic welding process:
First, the ultrasonic generator converts 50 Hz or 60 Hz electrical energy into 20~40 kHz electrical energy. The transferred high frequent electrical energy can be transferred into mechanical vibration of the same frequency by the transducer. Since there is insufficient vibration energy being produced during the mechanical vibration to heat and melt the welding sites between plastic rubber parts, the mechanical vibration can be through a set of amplitude transformers that can change the amplitude. The amplitude of mechanical vibration can be enlarged and transferred to the welding heads.
After that, the weld head will transfer the received high frequency vibration to the interface of plastic parts to be welded. At this area, the joint of two welding interfaces will have friction caused by vibration and the temperature of this area will go up. Due to the poor thermal conductivity of plastics, the heat cannot be evaporated immediately, so it concentrates on the welding areas. When the temperature reaches the melting points of the plastic parts, the contact interface of two plastics will melt immediately. With the pressure, the melt plastic rubber will fill out the clearance of connectors and makes it melt together. When the ultrasonic stops working and maintain the pressure for few seconds, the plastic will be cursed and formed. A solid molecular chain is obtained, forming a strong bond
Advantages and disadvantages of ultrasonic welding
There are a few benefits of ultrasonic welding in the applications. However, we need to know the advantages and disadvantages of this technology before the ultrasonic welding technology.
1. Advantages:
high welding speed and efficiency — Most of the ultrasonic welding can be finished in a few seconds
Low cost — due to high efficiency, the cost is low and it also saves a number of jigs, adhesives or mechanical fasteners, etc. Thus, it is a very economical assembly method of plastic parts.
High strength It reaches more than 80% of the body strength of plastic parts, and can even be comparable to injection molding in some applications;
Without changing the plastic status. The ultrasonic welding is a solid state process, and can be controlled accurately, which is beneficial to maintain the original material properties of the plastic before joining.
Appropriate structural design can make the ultrasonic to a certain degree of water tight or air tight effect.
Good surface quality and the welding points are beautiful and can realize seamless welding.
Simple procedures and operations, which can make automatic welding available.
Stable quality. Low welding failure rate, suitable for mass production.
The whole process is clean without using adhesives, high energy and material efficiency.
2. Disadvantages
High cost at the early stage of ultrasonic welding machine
The ultrasonic plastic welding machine requires customized welding heads and tooling, poor adaptability.
Limitations of size and shapes of parts. Medium and small sized plastic parts are suitable for the ultrasonic welding. Common ultrasonic welding machines have limitation (usually <250mm). The shapes are too complex (mainly means to the height direction of welding area). The welding quality is hard to ensure.
Ultrasonic welding is a non-detachable connection, which cannot be disassembled repeatedly, like screw buckle and other connection methods.
Ultrasonic welding cause vibration that may have some negative influence to some ares which the stress of plastic is not concentred (cracking). Meanwhile, vibration will also affect the internally assembled electronic components.
Ultrasonic welding has some limitations to the plastic rubber materials as some materials have good plastic welding performance, while some do not. Moreover, the ultrasonic welding normally is suitable for welding between one or similar plastics.
Which materials are suitable for ultrasonic welding?
Thermoplastic materials: Thermoplastic molecules are linear or branched chain. After being heated, softened, and melt, it can be made into plastic parts that is being shaped and maintained after cooling. It enables the plastic with weldability.
elastomer: elastomer is made of , once the heat is reduced, it will recover to the original status. Meanwhile, the elastomer is soft material, which is easy to absorb and vibrate. Thus, it is hard to pass through the ultrasonic welding.
Thermosetting plastic: the crosslinking reaction occurs when the thermosetting plastic is being heated. The main chain of molecular combines with the chemical bond and becomes a kind of incombustible substance, which means unable to weld.
Thermoplastic is the idea material for the ultrasonic welding as it will not generate unrecoverable molecular bonds, and it can be reshaped after being re-heated. The thermoplastic also includes the other two types: amorphous and semi crystalline plastics. The molecular arrangement of the amorphous plastic is random and has no certain melting point. It has high efficient energy transfer. Thus, it only needs a little amount of energy to melt. Conversely, the molecular arrangement of the semi-crystalline plastics is regular and has duplicate structural characteristics and a stable melting point. Melting of semi crystalline polymer requires high temperature and absorbs a lot of heat, which is more difficult than welding of amorphous polymer.
To measure the weldability of different thermoplastic materials, Tg, chemical compatibility and melt flow index (MFI) should be considered.
a) usually, there are two different plastics. Tags should be within 6℃ as there is no big difference in the time for them to melt under the ultrasonic vibration and the weldability is high.
b) the chemical compatibility is a complex topic, which comes down to the proportion of free radicals in polymers. When the data of these two kind of materials are similar, it will have compatibility, which can be simply understood as that the performance and compatibility of different plastics during mixed processing are good, but when different plastics are mixed together, the analysis key will be produced. Otherwise, they will separate. For example, although polyethylene and polypropylene look very similar, but they are not compatible chemically and cannot be welded together. ABS to ABS parts are compatible. ABS and acrylic parts are usually compatible.
C) the melt flow index indicates how difficult it is to turn the plastic from solid to liquid status to obtain the best effect. The plastics to be welded should have similar MFI.
Combined the above three factors, the weldability of ultrasonic between different plastic is as follows:
Orange indicates good weldability
White indicates poor weldability
04 Influencing factors of ultrasonic welding effect
2、 Design of ultrasonic structure of plastic parts
2. Location structure
Before the R&D and designing of a product, we need to consider the appearance of the final products, whether the joint position of two plastic parts is dislocated after ultrasonic welding. The design of positioning structure can effectively avoid or reduce the defects of dislocated scraping hands.
Common positioning structures:
spigot location
The spigot welding (single seam and double seam) has been mentioned in the last ultrasonic welding structures, which plays a guiding and positioning role to ultrasonic welding. Combined with design of art line, it has already met the requirements for most of the products.
2) use guide pin and guide holes to locate
Using guide pin and guide holes to achieve localization with higher accuracy, which is suitable for products requiring high precision. What needs to pay attention to is that the strength of guide pin should not be too low, in case it became invalid during the welding process.
3) Edge and boss location
Locating with the edges and bosses of plastic parts. Due to the large characteristics, the precision is poor, suiting for products with low precision requirements.
3) base mold location
In addition to special products, base mold location is not recommended normally as there is also clearance between the base mold and plastic welding parts. When the clearance is too narrow, it is difficult to put in or take out of the parts as it is too tight, or even scratch the appearance manually. If the clearance is too large, the dislocation gap is large after welding. Although it is also possible to use pneumatic or manual jigs to fix the products to avoid the dislocations, however the production speed and cost of jig manufacturing will cause extra cost.
3. Other structures of plastic parts
Sharp corner: The stress is concentrated at sharp corners. If there are many stress concentrate points on the plastic parts, after ultrasonic mechanical vibration, cracks or other scratches may occur at the area with high stress concentration of the corners, edges or junction of parts. Thus, these areas should have fillets as much as possible (R≥0.5).
2) Hole site or loophole on plastic part
The hole sites or loopholes on plastic parts contacted with the welding head will block the ultrasonic power transferred by the welding head. The effect of it to welding depends on how many types of plastic part materials (especially the semi crystalline plastics) and the size of openings. At the lower end of opening, a small amount of welding or complete lack of fusion will occur, and thus loopholes and holes should be avoided at the ultrasonic transmission area.
3) The shape structure of the plastic part bending
The transmission of the ultrasonic is rectilinear propagation. Hence, bending structure should be avoided In the propagation path of ultrasonic wave, or the vibration of ultrasonic cannot be transmitted to the welding sides, especially for the semi crystalline
4) Splits, handles, or other small features of plastic parts
The vibration will affect the protrusions on the inner or outer surface of plastic parts, causing fractures. The following are the measures that can reduce or eliminate the effect:
The joint between the protrusion and the main body is designed to be the largest circular arc;
Reducing the kink at the joint by external means;
Add up the thickness of material
Evaluate the ultrasound at other frequencies.
5)contact area between welding head and plastic parts
Generally speaking, the size of welding head should be large enough to make the linear projection cover the entire welding area, which is beneficial to the transmission of the mechanical vibration energy and reduce the possibilities to reduce the contacting marks. Note: the contact surface between welding head and workpiece should be larger than the whole area of the welding areas, otherwise may lead to surface marks.
6)near and far field welding
Near field welding refers to the welding area located 6.35mm or less from the welding area to the welding head. The distance over than 6.35mm is called the far-field welding. Based on above: it is difficult to carry out far-filed welding to the semi crystalline molecular structure plastics as it will hinder the transmission of vibration energy. In terms of the non-semi crystalline plastics, as the rondo arrangement of molecular, it is easy for the transmission of the vibration energy and even reduced. Attenuation of vibration energy will also occur in the low hardness plastic wrapping head, and thus it is required to consider whether there is sufficient energy to be transmitted to the welding side when designing the plastic products
7) Thin wall products (when the thin wall is less than 1mm)
Thin wall is like spring, which is unable to transmits the vibration effectively to the joint area, so it is more likely to generate lateral vibration and cause loss of welding energy. Thus, for thin walled products, near-field welding is more suitable.
8) tightness:When welding non-fusible resin or irregular shapes, the elastic oil seal and winding track are required to hinder the melt flow to achieve good tightness effect. The Fig under below is a kind of welding interface design with O-ring.
3、 Application of ultrasonic welding:
The applications of ultrasonic welding are based on the requirements of products. The ultrasonic welding also have advantages and disadvantages. When it requires to connect two separate plastic parts, there are many methods, which has been concluded. Click the link to check: How can two plastic parts be connected?
First, simplify the design of parts without designing the screw columns, bucks, and connection structure that takes up large space, while maintaining certain integrity of appearance.
Second, good tightness, which is more efficient and clean than the adhesive without mixing or waiting for cursing, etc.
1. Household appliance: water tanks for drinking fountains, humidifiers, beauty instruments and other appliances.
2. Electronics industry: electronic switch, charging head, power adapter, U disk, battery, waterproof and breathable film, etc.
3. Toy industry: dolls, building blocks, small toys, etc.
4. Applications in the automotive industry: spoiler, dashboard, glove box, storage box, hood, servo fuel tank, filter, trim and bumper strips, and intake manifold.
MORE BOLG
Insert mold in injection mold service
What are advantages and disadvantages of Zinc alloy and Aluminum alloy?
Inspection standards for injection molded partappearance
How to judge the quality of your plastic products?
Inspection standards for CNC machining
To ensure that your products are 100% qualified
Categories
Try GREFEE now,for free
We keep your uploaded files confidential and secure.