How much should you pay for your 3D printing components?

Posted on : April 29, 2022 By GREFEE
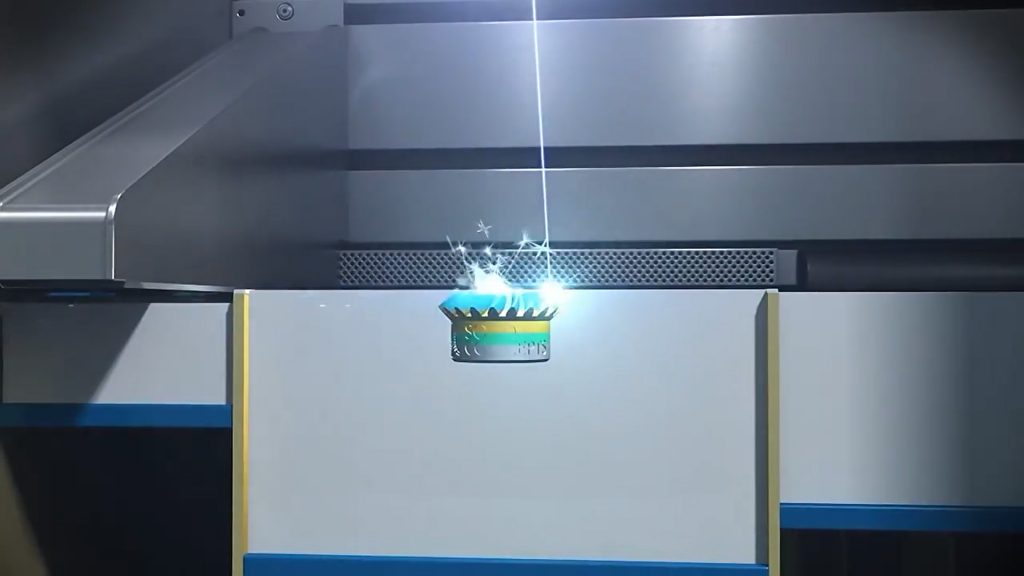
The cost of 3D printing is mainly decided by materials, quantities, and types of printers. Plastic is cheaper than metal. Small components use a fewer amount of materials. Simpler and less tough parts can use cheap printers.
When it comes to various 3D printing processing and materials, many factors affect the final decision —— like the required dimension accuracy, surface finish, and post-treatment requirements —— all these will affect the end cost.
When designing and manufacturing single parts, many combinations of these factors are possible, including continual fluctuated material price, making the price hard to forecast. One rapid and correct cost estimating method is to upload the CAD to GREFEE to obtain free real-time pricing.
Major factors affecting 3D printing cost
It is assumed that the designs of parts are the same, 3D printing cost has two major types: material cost and equipment cost.
Material cost: base material, material loss, supposing structure
Equipment cost (outsource or internal): installation and setting time, operation cost, regular repairing, post-treatment, maintenance, and the shut down time of machines.
3D printing will affect the material and equipment material. In this article, you will see the difference in the cost of the most common 3D printing material, processing, and which aspects of parts design affect the cost?
Cost of 3D printing material
Selecting the 3D printing material suiting your application will decide which type of 3D printing processing because different processing is compatible with different materials.
Usually, the price of 3D printing metal is higher than that of plastics. 3D printing compound material usually is more expensive than metals. In this section, we will conclude some common costs of the 3D printing material.
Plastic
3D printing plastics have two types —— thermosetting plastic and thermoplastic. Thermoplastic literally is the heat ruction to plastic and could be melted and make them the most common extrusion materials. Thermosetting polymer resin solidifies through the UV lines, suits for prototyping manufacturing.
Metals
Stainless steel and aluminum are the most common 3D printing metals, but titanium and copper alloy suit special applications. Laser welding, laser sintering, and cohesive injection suit for 3D printing metal material.
Compound material
Carbon fiber, kevlar synthetic fiber, glass fiber, and other compound materials are at the cutting edge of 3D printing innovation. They have the same strength characteristics as aluminum, which increases the strength-to-weight ratio. The cost of the compound material might be 8 to 12 times that of plastic materials and 2 to 5 times that of metal material.
In some applications, if each component uses fewer materials to achieve the same structural strength with a simpler design, the cost of the compound materials will be offset by the overall saving. Besides, the parts made of metal and plastic can utilize the mixing method. Compound 3D printing material is popular in specific industries which focus on costs, like aerospace, medical, alternative energy, and high-performance cars.
Cost of 3D printing
1. Material extrusion
Including: Melt deposition modeling (FDM, as shown)
Low cost of the simple geometric shapes and low volumes.
Material cost: lowest base material cost; the cost supporting structure increases as the complexity of the components.
Equipment cost: parts’ assemble time is short, low cost; due to the increase the post -treatment time/labor force, the complexity of the parts increases, the cost increases.
2. Reductive photopolymerization
including:Stereolithography (SLA,as shown), Digital optical processing (DLP), progressive (CDLP)
Produce complex geometric shapes and mass production. High material cost, but the post treatment cost is low.
Material cost: for plastic, compared to the extrusion martial and the powder bed melting, the whole material cost is the highest.
Equipment cost: shortest parts production time; Due to the surface quality is high, the post treatment cost is low.
3. Powder bed melting
Including: selective laser sintering (SLS, as shown), selective laser melting (SLM), direct metal laser sintering (DMLS), multi-jet melting (MJF)
Suits for parts with intricate geometric features, mass production and high quality parts of which the cost is the lowest.
Material cost: cost of the base material is mainly higher than that of the material extrusion but lower than the reductive photopolymerization; a non-support structure might lower the overall material cost; the base material can use again, which effectively reduces the waste and lowers the material cost.
Equipment cost: Longer part setup time and maintenance time between batches of powder materials; Due to the lack of support structure, the post-treatment cost is the lowest
4. material injection
compared to the extrusion material, the whole cost is high. However, compared to the laser melting/sintering, the cost is lower.
Material cost: similar to the reductive photopolymerization; compared to the extrusion material and the powder bed melting, its overall material cost is the highest.
Equipment cost: shortest parts setting up time; most parts need a support structure, which will lead to the increase in the spending of the components with intricate geometric details; The post-treatment is lower due to the surface treatment of the high-quality parts.
5. Adhesive injection
With the reduction in the material volume and printing time, the cost is lower than material injection. When the high-quality surface treatment, parts geometrical details, or material properties are not the priorities, this might be an economical solution.
Material cost: higher base material cost — — similar to laser melting/sintering; non-support structure lowers the whole material cost.
Equipment cost: set the high-quality surface treatment, parts geometrical details or the material properties as the priorities, which will increase the cost of post-treatment; compared to material injection, the setup time between batches for processing powder materials and maintenance time is longer.
6. Directional energy deposition
Including: Laser engineering net forming (LENS), direct metal deposition (DMD), electron beam additive manufacturing (EBAM)
Almost equal to the cost of the laser melting/sintering and powder injection melting.
Material cost: higher base material cost — — similar to the powder bed melting and laser melting/sintering; due to the waste material of complex geometric details, the cost is relatively high.
Equipment cost: parts with complex geometric details will cost high; the setup time between batches for processing powder materials and maintenance time is longer.
How does design affect the cost of 3D printing
Before printing the part, the design decisions will directly affect the overall cost, including the whole material, support structure, and the required post-treatment. Factors affecting the costs are:
Part volume: the whole part volume is essential. The size of the models reducing at a small extent will largely lower the cost of the 3D printing parts.
Support structure: with a support structure, the material cost varies according to the 3D printing. Using different printing methods will lower the printing cost.
With the increase in the complexity of parts, the extrusion material and material injection usually need more support structures. The powder bed melting does not require a support structure by which the whole material reduces.
Part geometry: Part geometry can reduce the material needed for diminishing the support structure. To lower the cost, it is considered to disassemble the part model into several parts to shorten the length or angle of extension or re-position the model in the printing base.
Filler: filling usually needs to maintain the shape of parts but will increase the cost of materials. If the strength of material intensity is the priority, modify the filling design to lower the material cost.
Post-treatment: thick layers do not affect the overall material cost of 3D printing parts. However, the spending on post-treatment might be affected if one wants a high-quality surface treatment.
Try GREFEE now,for free
We keep your uploaded files confidential and secure.