What are the differences and applications between low-pressure injection molding and traditional injection molding?

Posted on : Oct 20 , 2022 By GREFEE
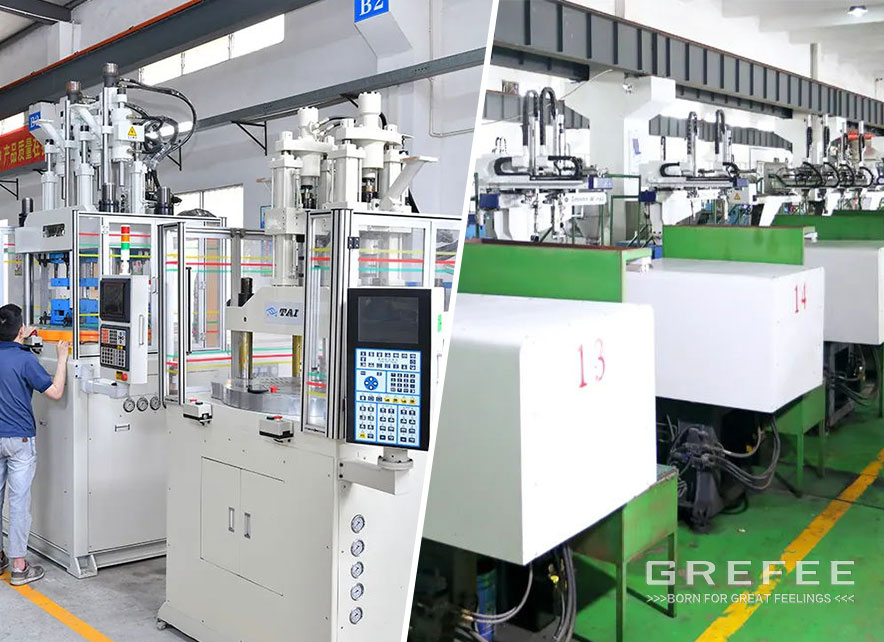
Low pressure injection is a kind of method that utilizes low injection pressure (0.15-4MPa) to inject the material into the mold and quickly solidified and formed in an extremely short period of time (5-50 sec).
Low pressure injection generally is not just merely refers to the injection products, but to use the other parts as inserts to inject. Finally, the inserts wrapped by the plastic will be bonded and form an integrated assembly parts.
The main difference between the low pressure injection and traditional injection is the low injection pressure because it does not damage the parts that are wrapped or bonded. The two major applications are following:
1. The electronic and electrical field mainly focuses on the molding of connectors containing PCBA, extremely fine conductor welding, low strength, and the packaging and protection of precision and sensitive electronic components, including printed circuit boards (PCBs), automotive electronic products, mobile phone batteries, wire harnesses, waterproof connectors, sensors, microswitches, inductors, antennas, and cables.
2. Automobile industry, including auto parts like door guard, column guard and wrapping frame guard need to be covered with skin (cloth, PVC fabric, etc.).
Electronic and electrical field
Most of the electronic and electrical field parts are fragile because of the influence of external factors (stress, humidity, temperature, dust, chemical solvent) and cause components damaged. In some products or use scenarios, we need to pack the electrical components closely and seal them for moisture proof, waterproof, dust proof and chemical corrosion resistant. In addition, some internal properties can be also involved like high and low temperature resistance, impact resistance, insulation and flame retardancy.
1、 Comparison between low-pressure injection molding process and traditional high-pressure injection molding process:
Low pressure injection molding is a kind of new technology between the potting and traditional high pressure injection molding, which is quite similar to the traditional high pressure injection molding technique. However, electronic components have the following advantages in packaging: great properties and low defective rate :
(1) in terms of injection molding materials, the low-pressure injection molding process uses a special hot-melt adhesive (polyurethane resin), which has low viscosity and good fluidity in the molten state and can fill the mold cavity only with a low pressure. In the meantime, the hot melt adhesive are mainly used for injection molding shells due to its excellent flexibility, good adhesion to polar materials, functional protection, waterproof, environmental resistance, electrical insulation, and can protect and seal electronic components. Engineering plastics, with excellent mechanical strength and low adhesion.
Low pressure injection | Engineering injection |
Material | Polyamide resin | Engineering plastic |
viscosity | quite low | High |
Injection pressure | low | High |
Adhersion | Good adherence effect with water proof | Nil |
(2). In terms of the injection pressure, low pressure inject hot melt plastic: low viscosity requiring low injection pressure: 1.5~40bar. It does not damage sensitive electrical components. The injection pressure of the engineering injection is low, which not exceed 400bar, but may damage electrical components.
(3). Regarding to the injection temperature, the injection temperature of low pressure injection molding process (190 ~230℃), which is also lower than the high pressure injection temperature (230~300℃). Therefore, it reduces the possibility of damaging sensitive and precise components due to the high temperature.
Low pressure injection molding process | Traditional engineering plastic injection molding |
Material | Low pressure hot melt adhesive | ABS, PBT, PP, etc. |
Injection pressure | 1.5~40bar | 350~1300bar |
Injection temperature | 190~230 | 230~300 |
Mold clamping force | 1 ton | Over 50 tons |
Mold material | Aluminum | Steel |
2.cost saving
Low equipment cost. General, the cost for the traditional injection molding equipment system is high, including the purchase of the high pressure injection molding machine. Besides, there should be water cooling system and expensive steel film. While, low pressure injection molding technique is simple with short cycle. Due to the low injection molding pressure, the mold can adopt casted aluminum mold as it is suitable for the research and develop, as well as manufacturing. Also, it reduces the cost and shortens the R&D cycle.
2.Comparison between low-pressure injection molding process and traditional potting process:
Not low-pressure injection molding process and traditional potting process can be used to seal the electrical components. Compared to the traditional potting process, low pressure injection molding is not only environmentally-friendly, but also improves the production rate significantly, as well as saving the cost for production.
Traditional potting process:
Basic principle of automatic glue filling machine
Low pressure injection molding process flow:
1. Add low-pressure injection molding materials and insert components into the mold.
2. Set up a hot melt adhesive machine and inject hot melt adhesive into the mold.
3. After about 1 minute, the mold can be opened and the parts can be taken.
Low pressure injection molding
Advantages of low-pressure injection molding process, compared with the traditional potting process:
1. The curing mechanism of the traditional potting s chemical reaction, and the curling mechanism of the low pressure injection molding process is physical reaction. Extra material and wastes can be recycled.
2. The processing cycle of traditional potting is about 24 hrs, while that for low pressure injection molding is shortened for just few or dozens seconds, which accelerates the production rate effectively.
3. The engineering plastics made shell is needed for traditional injection molding technique, while low pressure injection molding technique does not,. It is integrally formed, with small volume and low cost in the injection molding process.
4. The traditional potting process requires accurate control the promotion of 2k, which is complicated. While low pressure injection molding technique only adopts one type of rubber material with simple processing flow and great volume production.
5. The traditional potting process has a long curing time so it requires more shelf to store samples, occupying more production space. While low pressure injection molding does not require extra time to wait for curing to process the packaging, and it is not used for curing the frames, so it occupies less space.
6. Traditional potting technique requires a high amount of sealing material, while low pressure injection molding technique can reduce the using amount of sealing material or can achieve local sealing by designing the mold cavity.
3. Typical applications of low pressure injection molding in the electronic and electrical field
1. Packaging of electronic components
During injection molding process, electronic products with PCB, PCB with connectors, PCB with harness, using low pressure can avoid damages on sensitive electronic components. This kind of material can protect the electronic components from being affected by external environment (such as mist, mechanical stress etc) and can be used as shell.
2. Connector waterproof seal
The plug and cable clip are sealed with low-pressure injection hot melt adhesive. The flexibility of low-pressure injection molding material enables the encapsulated connector to eliminate stress, and its adhesive performance is helpful in water tightness, even reaching the waterproof requirements of IP67 level.
3. Field injection molding of grommet
Low pressure injection molding technique can be adopted into on site production. It can be formed quickly and buffer the tension to protect harness. In addition, it overcomes the time consumption in the threading the grommet and the production process is formed.
4. Function of structural member after forming
Low pressure injection molding has integrated shell, which works through flexible structural design to achieve diversified assembly requirements, and the next assembly can be directly carried out.
5. Others
4. summary:
1. The aim for designing low pressure injection molding is not to replace traditional engineering plastic. For instance: a component (like connector) can successfully use PVC to cast without considering low pressure injection molding. The higher the pressure is, the higher the scrapping rate of PVC is higher during injection molding. So, low pressure injection molding is more economical because it produces less wastes.
2. Low pressure injection molding is generally used to replace multi-step production operations, such as epoxy sealing after plastic shell molding. Also, it can achieve a single step. When a component is press molded using low-pressure injection molding without additional plastic housing is required.
3. Limitations of low-pressure injection molding process: due to the high cost of hot melt adhesive used in low-pressure injection molding, it is mainly used for the packaging and protection of precision components with a low volume.
Components with large volume is not recommended since the economy cannot be reflected.
Automotive industrial field
The application of low-pressure injection molding in the automotive field is not limited to the packaging protection of electronic devices, PCB boards, wire harness connectors, and electric vehicle batteries, but also used in automobile interior trim.
As the rapid development of the automobile industry and the continuous improvement of the material needs of drivers and passengers, users have higher requirements for the aesthetics and comfort of the automobile interior. At present, an increase number of automobile products relies on fabric to cover the column trim panel, which increases the aesthetics and comfort of the automobile interior and improves the sensory quality of the interior.
Two ways to cover the column trim panel with fabric mainly include traditional manual covering and low-pressure injection molding. Compared with traditional manual coating, low-pressure injection molding has the advantages of high production efficiency, environmental protection and good consistency, as well as a good application prospect.
Low pressure injection molding process: placing the PVC skin or knitted fabric into the mold before injecting the plasticized molten plastic (generally modified PP and PC / ABS with good fluidity) into the closed mold cavity with the thrust of the screw. Taking the product out after curing and shaping. The whole process completes the composite injection molding between the surface material and the skeleton material.
At present, low pressure injection molding has been widely used in the production of automobile door guard, column guard and parcel shelf guard.
Low pressure injection molding of automotive interior parts
1. Advantages of low-pressure injection molding process compared with traditional coating process:
(1). Low pressure injection molding is the integration of skin material and plastic substrate with high bonding strength and low falling off risk.
(2). As there is a lack of coating process necessary for coating process, so low pressure injection molding is more environmentally friendly, and it can effectively improve the VOC volatilization and odor of parts, which enhances the air quality inside the cars.
(3). There is no limitation for design of the internal structure of low pressure double layer injection molding parts. The freedom of surface modeling is higher than that of coating process, and the modeling features are clearer and stronger, with good hand feel and appearance.
(4). The low pressure injection molding does not require second coating and less procedures, so its production rate and pass rate are higher.
2. Meanwhile, low pressure injection molding technique also has disadvantages
(1). Complicate processes
Easy to be affected by the mold and fabric / PVC skin ductility. The scrapping rate is relatively high.
(2). Pattern retention
The stereoscopy of the pattern is poor at the high stretch point.
(3). High mold tooling cost and expensive technique material
(4). Not suitable for products with complicated structures due to low injection pressure.
injection molding near me?please pay your attention to GREFEE
MORE BOLG
Insert mold in injection mold service
What are advantages and disadvantages of Zinc alloy and Aluminum alloy?
Inspection standards for injection molded partappearance
How to judge the quality of your plastic products?
Inspection standards for CNC machining
To ensure that your products are 100% qualified
Categories
Try GREFEE now,for free
We keep your uploaded files confidential and secure.