Introduction to reliability test
Posted on : Dec 5 , 2022 By GREFEE
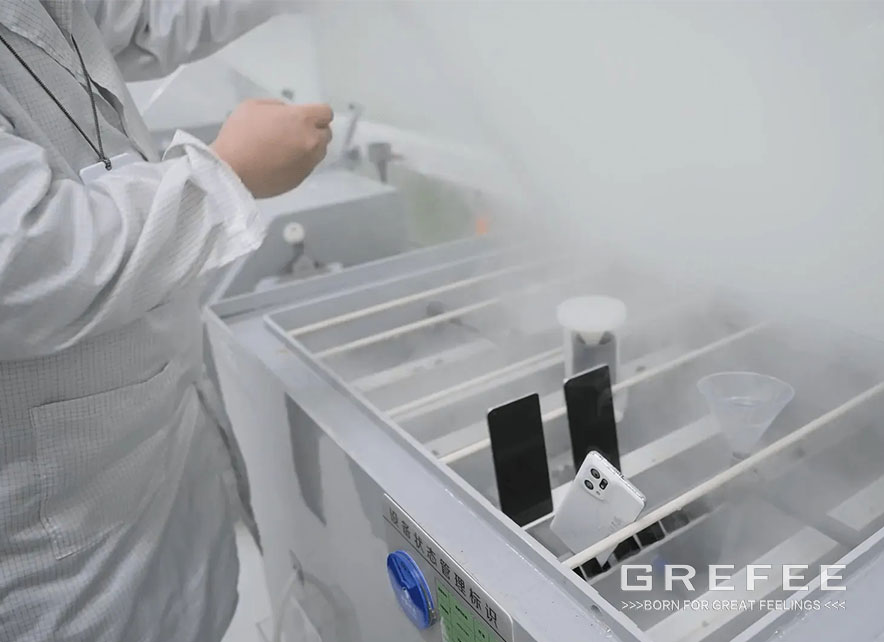
Reliability test is an activity for evaluating the the functional reliability of the product in all environments, such as expected use, transportation or storage during the specified service life. The products are exposed to the natural environment or under artificial environmental conditions to evaluate the performance of products in actual use, transportation and storage environments, and analyze the influence degrees of environmental factors, as well as the mechanism of action.
Aim of reliability test
By using different kinds of environmental test equipment to simulate the high temperature, low temperature, high temperature high moist and change of temperature in the environment. Accelerating the reaction of the product in the use environment to testify whether the products reach the expected quality objectives in R&D, design and manufacturing. Then, carrying out an evaluation for the whole products to obtain the reliability service life of products.
Necessity of reliability test
The advantages and disadvantages of reliability test can be detected through the reliability test so that defects during the products manufacturing can be found and improved immediately. This largely increases the manufacture level of industry and the service life and quality raised in the meantime. It provides the technical support for the research and development of industry and the business competitiveness is enhanced by creating high quality products
Bathtub curve is also called “Life characteristic curve “
Bathtub curve is used to describe the failure characteristics of mechanical parts during service life or to describe the life characteristics of parts. The bathtub curve varies from different parts.
The reliability project can be divided into three categories: electrical performance test, environmental reliability of parts, mechanical reliability of parts.
1.Electrical performance test
Breakdown voltage | Insulation resistance | Surface resistance |
Volume resistance | Dielectric strength | Dielectric constant |
Surface resistivity | Volume resistivity | Resistivity |
Electric conductivity | Withstand voltage | Temperature rise |
Tangent of dielectric loss angle |
2.Environmental reliability of parts
High temperature test | Low temperature test | Alternating damp heat test |
Constant temperature and humidity test | Cold and hot shock test | Low pressure test |
Ozone test | Salt spray test | Rapid change temperature test |
HAST | Gas lamp aging/Solar radiation | Gas corrosion test |
IPXY/IP level | UV Aging Test |
3.Mechanical reliability of parts.
Vibration test | Crash test | HALT/HASS test |
Drop test | Three combined test | Insertion and pullout force test |
Introduction to testing programs
1. Electrical performance test
Headings | Introduction of programs | Standards and equipment |
Breakdown voltage | The voltage when the sample breaks down under the specified test conditions, in KV | Reference Standards: ASTM D149-09(2013) GB/T 1408.1-2006 IEC 60243-1-2013 ASTM D1000-10 GB/T 4677-2002 |
Dielectric strength | KV/mmThe quotient of distance between the breakdown voltage and two electrodes of applied voltage (thickness of samples), in KV/mm. |
Dielectric constant | The ratio of its capacitance Cx to the vacuum capacitance C0 formed by the same electrode ε r=Cx/C0 when the area between electrodes of capacitor and space around electrode are all filled with insulated materials. | Reference Standards: GB/T 1409-2006 GB/T 1693-2007 ASTM D150-11 |
Dielectric loss | The residual angle of the phase difference between the voltage applied by locking the capacitor with insulating material as the dielectric and the resulting current is the dielectric loss angle, and its tangent value is the dielectric loss factor. |
Volume resistivity | The quotient of the mainstream electric field strength and the steady-state current density in the insulating material, which is the volume resistance per unit volume; Unit: Ω· cm or Ω· m | Reference Standards: GB/T 3048.3-2007 GB/T 1410-2006 GB/T 15662-1995 ASTM D257-14 |
Surface resistivity | The quotient of the DC electric field strength and the linear current density in the surface layer of the insulating material, which is the surface resistance per unit area; Unit: Ω/sq. |
Withstand voltage | Withstand voltage is an experiment to detect the ability of insulation to withstand working voltage or over voltage and to check the insulation manufacturing or maintenance quality of electrical equipment, requiring to use withstand voltage tester. Withstand voltage test is an equipment to test the strength of withstand voltage, which can directly, accurately, rapidly and reliably test the electrical safety performance indexes such as withstand voltage, breakdown voltage and leakage current of various tested objects. The main aim of it includes: a. Detect the ability of insulation withstand working voltage or over-voltage . b. Detect the insulation manufacturing or quality of electric accessory. c.Eliminate the risks of damages due to raw material, manufacturing and transportation, reducing the early product failure rate. d. Detect the insulation clearance and creepage distance. | Reference Standards: EIA-364-20C Equipment parameters: Agilent/34420A |
Ccontact resistance | Contact resistance is the resistance present between conductors. Normally, the contact resistance is under 10-20 mohm. some openings require to be under 100-500uohm. some circuits are sensitive to the change of contact resistance. What should be noticing is that the contact resistance of switch is the maximum allowable value of the switch over serval contacts. On the circuit board, contact resistance is the contact point between the gold finger and the connector, and resistance present when the electric current passes through. To reduce the formation of metal surface oxides, the male gold finger part, and the female card clip of the connector will all be coated with metals to suppress the occurrence of its “load resistance”. When the inserts of other electrics inserted into the socket, or there is also a contact resistance between the guide pin and its socket. | Reference Standards: EIA-364-06C Equipment parameters: Agilent/34420A |
Insulation resistance | With the rapid development of life, people cannot live without electricity. There are many risks when using electricity. In the electrical equipments, like motors, cables, household appliances, etc. DC resistance of insulation under specified conditions. Insulation resistance is the basic insulation index for the electrical equipment and electrical circuit. For the handover test of low-voltage electrical equipment, the insulation resistance of motors, power distribution equipment and power distribution lines should not be lower than 0.5MΩ (for equipment and lines in operation, it should not be less than 1M Ω/kV). The insulation resistance of low pressure electrics, connectors and secondary circuits should not be less than 1MΩ; In humid environment, the insulation resistance should not be less than 0.5MΩ. The insulation resistance of the secondary circuit small busbar should not be lower than 10MΩ. The insulation resistance of Class I hand-held power tools should not be lower than 2MΩ. Insulation resistance: When a DC voltage is applied to the dielectric, after a certain period of time the polarization process is over, the resistance corresponding to the leakage current flowing through the dielectric is called insulation resistance. | Reference Standards: EIA-364-21C Equipment parameters: GWINSTEK/GPT-9803 |
Temperature rise | Temperature rise refers to the temperature of each components of electric equipment devices is higher than that of the environment. After the conductor is passed through, the current heating effect is generated. As the time goes, the temperature will increasingly rise till it turns stable, of which the condition for that is the temperature difference between the front and back does not exceed 2°C within 3 hours. The temperature of the conductor surface is the ultimate temperature in ℃. The temperature of this part of the rising temperature that exceeds the temperature of the surrounding air (ambient temperature) is called temperature rise, and the unit of temperature rise is Kelvin (K). Some articles and reports of temperature rise often write the unit of it in ℃, which is inappropriate. It should be (K/W). Temperature rise is often used to test the service life, stability and other properties of products. The temperature rise of its important components (IC chips, etc.) is usually tested, and the device under test is placed at a specific temperature (T=70°C) higher than its rated operating temperature (T=25°C). After it is stable, record the temperature rise that higher than the environmental temperature to verify the reasonability of design. In electrical products: the rated temperature rise of the motor winding refers to the maximum allowable temperature rise of motors under the ambient temperature specified by the design (+40°C), which depends on the insulation level of winding. The temperature rise depends on the heat and heat dissipation during the operation of motor. The temperature is the actual heating temperature of each part of motors. High temperature will make the insulation aging and shorten the service life, or even damage the insulation. To protect the insulation, the temperature of each part of the motor winding and other parts is subject to an irregular limit, which is the allowable temperature limit of motors. | Reference Standards: EIA-364-70B Equipment parameters: Agilent/34970 |
2. Environmental reliability of components
Heading | Introduction to programs | Testing requirements |
Salt spray test | The salt spray test simulates the environments with marine or humid climates to testify the products, materials and the ability of the protective layer to resist salt spray corrosion. There are two tests, salt spray test and alternating salt spray, used for the quality evaluation and invalid verification under specific conditions. | test range:NSS,AASS,CASS tst parameters:900*600mm test parameters:1 m3 test range:NSS test parameters:2400*1500mm |
Dustproof and waterproof test/IP rating | The dustproof and waterproof test/IP rating is mainly for the electronic products and equipment used outdoors or in harsh environments, notation is IPXX. The first characteristic number represents the protection class that prevents the foreign matters from getting into and prevent the access to hazardous parts. The second characteristic number represents the the protection class that prevents the water from getting into. | test range:IP XX Test parameters:dust proof: 1~4X dust proof : 5~6X waterproof: X1~7 |
High temperature test | The high temperature affects the products in many aspects, like aging, oxidation, chemical change, thermal diffusion, electromigration, metal migration, melting, vaporization deformation, etc. Normally, when the ambient environment rises by 10°C, the product life will be reduced to a quarter. When the temperature rises to 20℃, the life of products will be reduced by half. The life of products obeys the “10℃ principle”. Thus, as the most common test, the high temperature test is used for the screening of components and machines, aging test, life test and accelerated life test. In the meantime, it is also of great importance to the validation of Failure Analysis. | testing range:<200℃ testing parameter:1m3 16m3 |
UV light aging test | Used to simulate the damaging action of sunlight, moisturized environment and temperature to the material. The aging of material includes fading, loss of gloss, strength reduction, cracking, peeling, chalking and oxidation, etc. | testing range:UVA340/UVB313/ UVA351 testing parameter:6*9cm |
Low temperature test | Low temperature affects the products in many aspects, like embrittlement, icing, viscosity increase, curing, decrease in mechanical strength and physical shrinkage, etc. It is used to test the adaptability of products storage and usage under low temperature environment when the products are in the development stage, screening test of components, etc. | testing range:0℃~ -70℃ Testing parameters:1m3 1m3 18.9m3 testing range:-40℃~ -70℃ Testing parameters:nil |
Thermal shock test | The aim of the temperature shock test is to confirm the change of product characteristics in a short period of time, and the breakdowns caused by the various materials that make up components have different thermal expansion coefficients. These variations can be observed by exposing the components to the ultra-high and ultra-low temperature environment intermittently. Thermal shock test is different from environment simulation test, which is to find the potential risks by cold and hot temperature shocks that are difficult to find under normal temperature conditions. | testing range:temperature: -75~220℃ Conversion time,<10 second testing parameters:770*650*610mm |
Rapid temperature change test | Rapid temperature change test specifies the rate of temperature change, often simulating regional environments with large temperature differences between day and night, also the life test to assess the appearance, mechanical properties and electrical properties of components or products. | testing range:temperature:-70℃~150℃ :testing parameters:rate of temperature change≤10℃/min rate of temperature change10~25℃/ min |
Alternating Damp Heat Test | Alternating humidity and heat is to simulate the environment of tropical rainforest to confirm the temperature changes of the products and material, and the adaptability to use and storage when product surface is dewy, which is normally used for the service life test, evaluation test and comprehensive test. | testing range:temperature-70℃~180℃ humidity:5%~98% testing parameters:1m3 1m3 18.9m3 humidity<20%(Only use C340 boxes, low temperature ≥ – 40 ℃) |
Constant temperature and humidity test | Humidity accounts for more than 40% for the failure of products, so humidity test is necessary in the environmental test. It is normally used for life test, evaluation test and comprehensive test. In the meantime, it is also of great importance for the analysis of failure, especially necessary for the research and development of products with resin. Double 85 refers to the temperature of 85 ℃ and humidity of 85% RH. | Temperature/humidity environment, temperature residence time testing range:temperature:-70℃~180℃ humidity:5%~98% testing parameters:less than 1m3 1m3 18.9m3 humidity<20% |
Gas Corrosion Test | Gas corrosion is mainly applied into the contact points and fitting parts. The evaluation standards after experiment is the change of contact resistance, then is the appearance change. Gas corrosion mainly include sulfur dioxide, hydrogen sulfide, nitrogen dioxide, chlorine. One or more gases can be selected for test according to the service environment | testing range:SO2/ H2S/ NO2/Cl2 density:0.01~100ppm;temperature:0℃~90℃ ;humidity:10%~98% testing parameters:870*735*520mm |
Low pressure test | Low pressure test is mainly used in aviation, aerospace, information, electronics and other fields to determine the instruments, electrical products, materials, parts and equipment are under single or simultaneous action of low pressure, high temperature and low temperature or the environmental adaptability and reliability tests at the same time. | testing range:pressure:Atmospheric pressure~10KPa temperature:Normal temperature~200℃ Test parameters: 1 m3 |
Ozone test | Ozone test is used to test the ozone aging resistance and aging cracking test of non-metallic materials and organic materials (such as coatings, paints, rubber, plastics, and their products) of rubber products. | testing range:density: 0~500pphm temperature: room temperature~50℃ testing parameters:550*500*700mm |
(HAST)HAST | HAST is used to to assess the comprehensive impact of plastic encapsulated semiconductor integrated circuits and other electronic devices under high pressure and high humidity conditions, which is a highly accelerated test method to evaluate the ability of electronic products to withstand humidity and heat. It is commonly used in product development, quality evaluation, and failure verification. | testing range:temperature:105~142.9℃ humidity:75%~100% pressure:0.02~0.186Mpa testing parameters:400*280*270mm |
Xenon lamp aging/solar radiation | By using the xenon arc lamp to simulate the full sunlight spectrum to reproduce destructive light waves in different environments. This provides the corresponding environmental simulation and accelerated test for scientific research, product development and quality control. | testing range:The temperature range of the blackboard is 25℃~90℃ testing parameters:XE-3-HSC |
3. Mechanical reliability of parts
Heading | introduction to programs | testing requirements |
Drop test | Drop test is used to simulate the possible drops when using or handling of products, including (1) non packaged products may fall freely during handling and the samples often drop onto the specified surface from the specified height. (2) simulating the allowable and repeatable free falls of connectors and small remote control device of load cable. (3) packaging falls | testing range:<100 kg testing parameters:drop height:30-150cm |
Vibration test | Vibration test simulates the influence of different kinds of vibration environments to the products in transportation, installation and use. It simulates all the vibration environment influence encountered in transportation, installation and use to assess the ability to against all kinds of environmental vibration. The vibration test assesses the resistance of components, parts, and whole machine in the expected transportation and use environment. | testing range:Sine vibration, random vibration Vibrating table of less than 2 tons Vibrating table of 10 tons |
Impact and impact test | Many products will be impacted in use, loading and unloading, and transportation process. The value of impact changes greatly and has complex properties. Thus, impact and collision tests are suitable for assessing the weak parts of machinery and checking the integrity of product structure. | testing range:Half sine wave, acceleration<500gn Half sine wave, acceleration:500-5000gn testing parameters :Platform size:450*450mm testing range:square wave Max:85gn testing parameters:platform size:450*450mm |
Insertion and pull-out force test | Insertion and pull-out force test is used for many tests, including insertion force, pull-out force, plastic retention force, service life, etc. Through the analysis of computer, the load, stroke and corresponding change curve of the measured object can be obtained accurately. Also, it can accurately control the test travel, speed, target measurement times and pause time of the insertion force of the connectors, especially for different kinds of clamps and jigs, which can help the connectors to automatically centered and aligned when testing, rather than unilaterally inserted. | plugging times plugging strength standard male and female plugs |
HALT/HASSAccelerated life test HALT/HASS test | HALT (Highly Accelerated Life Test) is a method which is used to detect the weaknesses or defects through the improvement of designing and reliable experiment tips. The key of it is to gradually increase the test stress, gradually find and eliminate defects to quickly improve the reliability. | testing range:temperature:-100℃~200℃ vibration:5-50Grms testing parameters:1360*1370*1400mm |
Crash test | Crash test is used to evaluate the protection ability of packaging to the contents and the impact strength of multiple times repeated mechanical collisions when transporting the packages. | testing range:load:0~100kg,acceleration:5-100gn testing parameters:platform size:500*700mm |
Temperature/Humdiity/Vibration test | There are many environmental factors affecting the products usage, which lead to the breakdowns caused by all weak parts have faults under the action of natural and induced environmental factors. The temperature/humidity/vibration test can carry out environmental tests of products such as high temperature, low temperature, temperature cycle, temperature shock, constant temperature and humidity, alternating damp heat, sinusoidal constant frequency, sinusoidal sweep frequency, random vibration, shock, high temperature mechanical shock, low temperature mechanical shock, temperature shock response, temperature vibration, temperature vibration humidity, etc. Applying the separate environmental stress onto the products can lead to the breakdowns. Similarly, applying three different environmental stress on the products can easily obtain 3~5times acceleration effect. By combining the different environmental stresses, it can also simulate faults that cannot occur when individual stress is applied. Therefore, it is often used in early detection of product defects to improve the reliability of the products. | Temperature:-70℃~150℃ humidity:25%-98% testing parameters:temperature+humidity+vibration |
MORE BOLG
Insert mold in injection mold service
What are advantages and disadvantages of Zinc alloy and Aluminum alloy?
Inspection standards for injection molded partappearance
How to judge the quality of your plastic products?
Inspection standards for CNC machining
To ensure that your products are 100% qualified
Categories
Try GREFEE now,for free
We keep your uploaded files confidential and secure.