Protection design of electronic products

Posted on : Dec 30 , 2022 By GREFEE
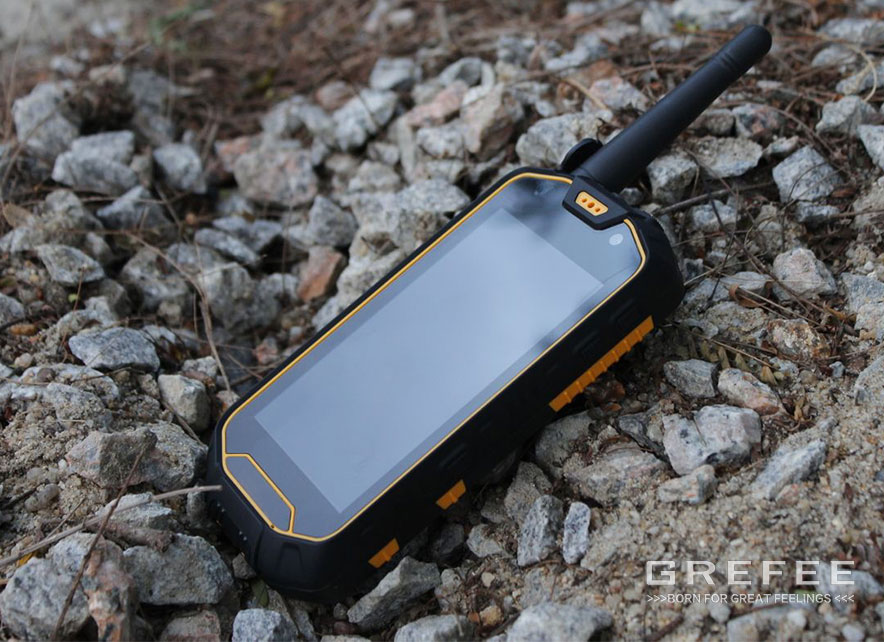
Environmental factors impact the military electronic products in use, transportation and storage significantly, while it also affects the stability and reliability of military electronics. The loss is astonishing if they are not properly protected. The American military have made statistics about the failure of electronic equipment, finding that above 50% failure is related to the environmental factors and thus tolerating harsh environment is a required lesson to achieve higher economic and military benefits.
From the theoretical research to engineering applications of three-proofing technology during the recent years, the field of application has been expanding, from the development of the early single process protection to the current overall design, circuit design, structural design and standardized system engineering,great changes have taken place. Now, the three-proofing technology is aimed to improve the environmental adaptability of products, including waterproof, moisture-proof, anti condensation, anti salt fog, anti-corrosion, anti-aging, anti vibration, anti-static, etc. At present, most mobile phones also have partial protection function, like waterproof and dust proof, etc.
Technical measures for three proofings of electronic structure
“Three proofing” technology is a comprehensive concept, which has been involved into many applications. To enhance the capacity of three-proof of electronics, the three-proof design concept must be introduced when it starts the product designing. Introducing three-proof technology can ensure the products are equipped with environmental adoptability from complete machine to extension and then to parts. Three-proof technology can compensate the deficiencies of three prevention in guarantee and supplementary design. At the same time, it also increases the ability of products to resist environmental changes, which further largely improving the reliability of electronic products. The following is a description of the material, structure and process.
1. Material protection
Material protection refers to properly and reasonably selecting material, and processing the material with specific processing treatments to further improving the ability of material to resist the environmental changes. According to the classification of actual use environment and requirements for three prevention levels of electronics, selecting the proper material to manufacture components. Material selection is the first step of three-proof, but also the key step.
Electronics working in the poor conditions will be affected by various environmental problems like salt spray, rust, mold and aging. To help the electronics to better adopting into server environmental conditions, metals with great corrosion resistance is highly recommended, as well as non metallic materials that do not grow mold and are resistant to aging. Metals with great corrosion resistance mainly include aluminum alloy, austenitic stainless steel, titanium alloy, gold, nickel, etc. Re-coated metal layer or non-metal layer of aluminum alloy, stainless steel, titanium alloy are often used due to a economical consideration,
When selecting materials, one should know the compatibility of materials, the corrosion mechanism and damage mode of materials well to prevent some corrosion that are risky and issues, like corrosion and aging caused by the interaction of different materials. It is essential to select the coating and type of metal approximately according to the capability of material. The larger the potential difference, the server the corrosion. When designing, in the same structure, try to choose the same metal material, or choose the material with similar electrode potential. What’s more, the potential difference of two kinds of material should be less than 0.25v, or the related protection measures should be adopted.
At present, the military electronics is developing towards light and small mobility. Many components and parts of products are made of engineering plastics, then pay attention to the mold and aging of materials. Selecting the engineering plastics with great environmental adoptability, like polycarbonate, ABS, plexiglass, etc.
2. Structural protection
The structural protection is as important as the material protection. In the real environment, most problems can be avoided with the appropriate structural design (structural protection). When designing, the sealing or semi sealing measures should be taken for local parts or the whole machine, then separating the equipment with the external environment. All kinds of boxes are welded into a whole with aluminum alloy. Sealing rings made of conductive rubber are added at the connection between the chassis side plate and the box, and the external surface of the chassis is coated. To avoid the corrosion caused by the mechanical stress, thermal stress, water accumulation or impurities, the following measures should be taken during the structural design:
(1). Avoid ponding structure. The appearance of products should be slightly inclined and reduce the number of holes and grooves. There should be drain and vent holes at the areas where would possibly be ponding or moist, and avoid the embosses.
(2). Under the humid environment, spot welding, riveting, thread fastening and other structural forms should be avoided. Sheet metals or the structure of integral casting box are the first choice to prevent the corrosion at clearance. At the same time, sealing treatment or sealing gasket should be added at the place where crevice corrosion can be formed.
(3). For the same structure, if different types of metal are used, one of the metals should be applied with a metal coating allowed to contact with the second metal, or two types of metal should both have the same type of metal coating, or place the gasket, or apply the insulation protection layer between the two types of metal. Now, electromagnetic compatibility requirements of equipment shall be considered.
(4). When stress corrosion cracking is likely to occur, avoid using structural forms that cause stress concentration, and take appropriate measures to eliminate the internal stress.
(5). The size of the thickened member at the most vulnerable and the most corrosive part is commonly referred to as “corrosion allowance”. Generally, taking twice the amount required for the expected life. For the parts that are prone to corrosion and damages, easy maintenance and replacement shall be ensured from the structure.
3 .Process protection
In addition to take measures from the material protection and structural protection, process protection is also essential as it can further improve the three-proof ability of products. The process protection method that is often used is the surface chemical coating and metal and non-metal coating. According to the working environment, we divided the structures into type I structure and type II structure. The surface of type I is often exposed to the natural environment or directly affected by natural environmental factors when the products are working. The surface of type II is not directly being exposed to the natural environment or directly affected by natural environmental factors when products are working. The process measures depends on the different types of component surfaces.
(1). Chemical coating
Using the method of electrochemical or chemical methods to stimulate the surface to produce a kind of compound to form a covering layer to resist the environmental factors. Common methods include oxidation, passivation, phosphating, anodizing, etc. The chemical coating is applicable to both type I and type II surfaces.
For non ferrous metals and their alloys, chemical oxidation or anodic oxidation treatment are often used to protect the parts. The oxidation film is characterized by porous and insulating, with strong adsorption capacity, can be used as the bottom layer of paint. After painting, the corrosion resistance can be greatly enhanced. In addition to the robust corrosion resistance and adhesion ability, the chemical oxidation layer also got electric conductivity, so it is often used for surface treatment of electrostatic devices. Ferrous metals are usually treated by oxidation and phosphating.
(2). Metallic and non-metallic coatings
The metallic coating is often obtained thought electroplating, chemical plating, hot dip plating, thermal spraying and other methods, which is to apply one layer of metal coating with great environmental resistance on the surface of structural parts but has low environmental resistance to improve the three-proof ability of the whole parts. Metallic coating is suitable for type I and type II surface. Common metal coatings have zinc, nickel, copper, chromium, gold, etc. According to the environmental requirements, both the characteristics of the matrix material and the compatibility requirements of the material shall be taken into account.
The non-metallic coating has two types, paint coating and plastic coating. Paint coating is the most common one in the non-metallic coating, which has a certain degree of flowability and is able to form a consecutive thin film on the surface of subjects, thus the surface can be protected. Plastic coating that is coated on the surface of the protected object with epoxy and polyethylene resins with excellent environmental resistance. Non-metallic coatings are usually applied to Type I surfaces.
Three-proof painting is a special coating that is used for preventing the circuit board and the related equipment from environmental corrosion. It has great high and low temperature resistance. After curing, it forms a transparent protective film, which has superior insulation, moisture-proof, anti leakage, shockproof, dust-proof, anti-corrosion, anti-aging, corona resistance and other properties.
There is a variety of three-proof paintings with different functions, so it is based on the properties, application range, and appearance requirements, actual using environment of paintings. For the surface of products that are acrylic paint and polyurethane paint, which the paint color is preferred, with good light retention, color retention, water resistance, abrasion resistance, outstanding atmospheric corrosion resistance and three proofing performance, high heat resistance and strong adhesion.
Conclusion
The environmental protection technology of electronic structure involves the professional information on many aspects. In align with the overall requirement and the actual use environment, adopting the advanced design concept, reliable material, modified structure, surface treatment, and measures such as sealing and drying to carry out environmental protection design to the whole components and parts to improve the environmental adoptability and reliability of products.
MORE BOLG
Insert mold in injection mold service
What are advantages and disadvantages of Zinc alloy and Aluminum alloy?
Inspection standards for injection molded partappearance
How to judge the quality of your plastic products?
Inspection standards for CNC machining
To ensure that your products are 100% qualified
Categories
Try GREFEE now,for free
We keep your uploaded files confidential and secure.