Metal injection Molding –MIM

Posted on : Jan 6 , 2022 By GREFEE
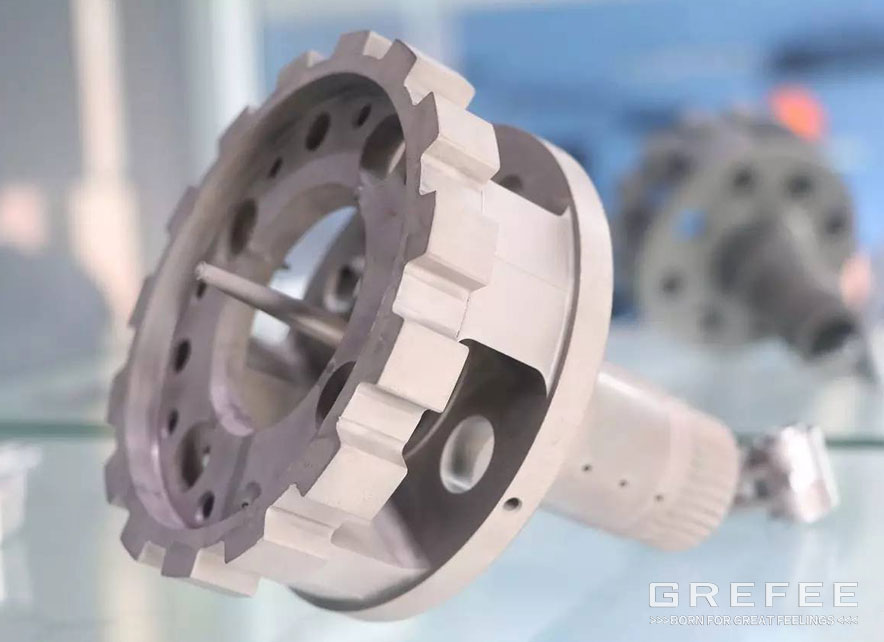
The metal injection molding, MIM, is a kind of forming method of injecting the plasticized mixture of metal powder and binder into the model. Modern plastic injection method is introduced into the powder metallurgy to form a brand new net shape processing technolgy for metal parts, which is a high technology developing fast in the powder metallurgy discipline and industrial field. First step of MIM is that selecting the metal powder to mix with the organic binder that in align with the requirements of MIM. Adopting the appropriate method to mix them evenly under a certain temperature, then injecting into the mold cavity with the injection molding machine under the heating and plasticizing state after granulation to obtain the parison. With the degreasing treatment by chemical or solvent extraction, the final product is obtained through sintering and densification.
Features of MIM products
Complexity
MIM is similar as the injection molding. There is no limitation to the designing of shape. Since MIM is a forming process, so the additive products features won’t raise the cost, which makes MIM an ideal way to assemble independent parts into multi-functional products. The designing principles of MIM is close to that of injection molding so that it can be applicable to all kinds of products.
Precision
The reference design of MIM net forming precision is normally ±0.5% of size. The net forming of some features can reach to ±0.3%. Similar to other technologies, the higher the precision requirements, the higher the cost. Thus, if the quality is good enough, the tolerance requirement can be softened. Surface treatment can help if the MIM inaccessible tolerances for one shot molding.
Weigth and size
MIM is extermely suitable for the parts that is less than 100 gram. It is the most economical when it is less than 50 gram. Parts over 250gram can be also processed. The major cost of MIM processing is its raw material, so MIM can reduce the weight of parts by new technologies. Same as the plastic products, the weight can be reduced by core and bracket without affecting the integrity of products. MIM is extremely outstanding in terms of tiny and micro components. It is also applicable to the ones that are less than 0.1 gram. Weight is not the limit factor. Products longer than 250mm can be also processed.
Thinness
Less than 6mm thickness is the bes for MIM, as well as thick external wall. However, the cost may be increased due to the time increase and extran material. In addition, ultra-thin wall (<0.5mm) is also avaliable but has a much higher requirement.
Yield
MIM is quite flexible with a annual demand of serveral thousand to serveral million. Like the castings and injection molded parts, MIM requires customers to invest in mold and tool, so the cost for low volume products is affected,
Raw mateiral
MIM can process a variety of materials, including iron alloy, superalloys, titanium alloys, copper alloys, refractory metals, hard alloys, ceramics and metal matrix composites. Although the colored aluminum alloy and copper are applicable technically, other ways are more economical, like die casting or machining.
MIM process flow:
MIM process flow combines the flexibility of injection molding design and the high strength and integrity of precise metal together to achieve the possibilty of low cost made extremely complex geometric parts. MIM process is divided into four steps (mixing, forming, degreasing and sintering) to achieve the production of parts, then to decide if surface treatment is requried according to teh product features.
Mixing
Mixing the thermoplastic, paraffin binder and fine metal powder of which the particles is lower than 20µ according to precise scale. The volume of metal powder and binder is approximately 60:40. The mixing process is done with a specific mixing equipment. Heating and melting the binder. In most cases, mechanically mixing is used until the large particles of metal powder is evenly mixed with binder and form granular (called raw material), which can be injected into the mold cavity.
Formation
The injection molding equipment and technology is similiare to The granular raw materials is heated by the heater and then being injected into the mold cavity. During this section (green part), the binder can only be melted with the temperature at about 200°c after cooling and demolding (fully mixing with the metal powder) to ensure the above process can be processed. The multi-cavity mold is highly recommeded for increasing production rates. The size of cavity should be 20% of metal parts to compensate for shrinkage during sintering. The shrinkage of each kind of material accurate and known.
Degreasing
Degreasing is to remove the binder from the formed parts, which is usually completed withint serveral steps. Most of the binder is removed before sintering. The residual part can support the part in the sintering apparatus. There are many methods to degrease, of which the most common one is the solvent extraction. The parts after degreaseing have semipermeability. It is easy for the resiudal binder to volatilize during sintering.
Sintering
The part after degreasing will be put into the high temperature and high pressure furnace. The parts are being heated slowly under the protection of gas to remove the resiudal binder. After the binder is completely removed, then the part will be heated to a very high temperature. The clreance between praticels will disappear due to the melt of particles. The component is directionally shrunk to its design size and transformed into a dense solid. For most materials, The typical sintering density is greater than 97%. The high sintering density makes the product performance similar to that of forging materials.
Surface treatment
According to the spcific requirement, some parts after sintering will require surface treatment. Thermal treatment can improve the phsical performance of metals. Electroplating and coating can be applied into high denstiy material to provide welding and cooling technologies.
Advantages of MIM
(1). Similar to the plastic products producing process. it can produce small metal parts with complex shapes (usually 0.02~200G in size) in one forming process.
(2). All parts of the workpiece are uniformly organized with a relative density at 95%~99%, allowing carburization, quenching, tempering and other heat treatment. Some dimensions with high precision requirements can do pos-treatment with mechanical processing.
(3). Product accuracy can be +0.3%~+0.5%. Smooth surface finish, reaching 1.6Ra at one time.
(4). The strength, rigidity, elongation rate and other mechanical performance of products are great. High wear resistance, resist fatigue, uniformly organized.
(5). High raw material utilization rate. High degree of production automation. simple to process, and support continuous mass production.
(6). No pollution,the production process is all clean technology.
Comparsion of MIM and other forming process | |||||
data | MIM | powder metallurgy | precision casting | machining | stamping |
density of part | 98% | 86% | 98% | 100% | 100% |
Tensile strength of parts | high | low | high | high | high |
Part surface finish | high | medium | medium | high | high |
microminiaturization capability of parts | high | medium | low | medium | high |
Thin wall capacity of parts | high | medium | medium | low | high |
Part complexity | high | low | medium | high | low |
Tolerance of part design | high | medium | medium | medium | low |
Batch production capacity | high | high | medium | medium-high | high |
Applicable material range | high | high | medium-high | high | medium |
Supply capacity | high | high | medium | low | high |
MIM materials and applications:
Performances of Typical MIN Materials
Application fields of several typical MIN materials
Material system | Alloy grade, composition | application area |
low alloy steel | Fe-2ni,fe-8ni | Various structural parts in automobile, machinery and other industries |
stainless steel | 316l,17-4ph | Medical devices, clock parts |
Hard alloy | Wc-co | Various knives, clocks and watches |
tungsten alloy | W-ni-fe,w-ni-cu,w-cu | Military industry, communication, daily necessities |
titanium alloy | Ti,ti-6al-4v | Medical and military structural parts |
magnetic material | Fe,f14nd2 b,smco5 | Various magnetic components |
Common MIN products in the market
Mobile phone SIM card holder
Metal gear
MORE BOLG
Insert mold in injection mold service
What are advantages and disadvantages of Zinc alloy and Aluminum alloy?
Inspection standards for injection molded partappearance
How to judge the quality of your plastic products?
Inspection standards for CNC machining
To ensure that your products are 100% qualified
Categories
Try GREFEE now,for free
We keep your uploaded files confidential and secure.