Requirements of Electroplated Plastic Parts

Posted on : Dec 13 , 2022 By GREFEE
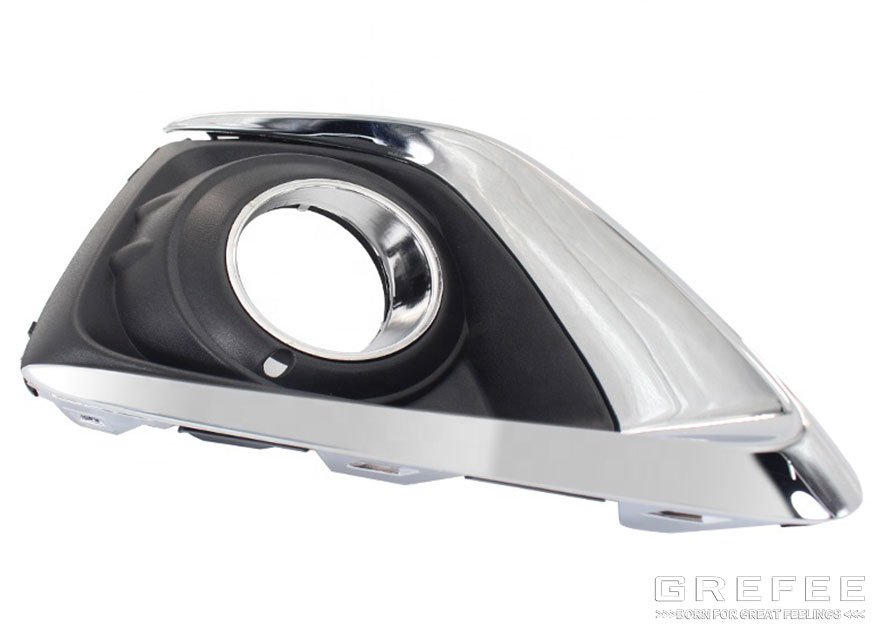
Electroplate parts designs
1.The ideal selection of base materials is electroplated ABS. Normally, Chi Mei ABS727 is often used. ABS 757 is not recommended as the ABS757 screw post is easily to crack.
2.The surface quality must be qualified. Electroplating cannot cover up some defects of injection but will make it more obvious.
3.The screw holes of electroplating parts is made by resistance plating process to avoid the screw cracking, and the inner diameter of screw holes should be 10dmm larger than ordinary single line (or can add material)
4.Cost of electroplating parts. As electroplating parts are classified as appearance decoration parts, which mainly functioned for decorating, but is not suitable for large area electroplating design. In addition, the undecorated area should be underfed, so it can reduce weight and electroplating area.
5. Some points that should be aware of when designing structure to make the appearance suitable for electroplating process.
1) surface projection should be controlled within 0.1~0.15mm/cm without sharp edges as much as possible.
2) if there are blind holes, the depth of it should not exceed half of the hole diameter, and no requirements for the color and luster of bottom of holes.
3) appropriate wall thickness can prevent deformation, which had better be within 1.5mm~4mm. If the thin wall is required, the strengthening structure at the corresponding sites is required to ensure the electroplating deformation is within the controllable range.
3) appropriate wall thickness can prevent deformation, which had better be within 1.5mm~4mm. If the thin wall is required, the strengthening structure at the corresponding sites is required to ensure the electroplating deformation is within the controllable range.
6. How thickness of plating of electroplated parts affects the fit dimension.
The ideal electroplating parts thickness should be controlled approximately 0.02mm. However, in the actual production, it may only be 0.08mm as much as possible. Thus, to achieve a satisfied result, the unilateral clearance should be over 0.3mm at the position of sliding fit, which we should pay attention to when matching electroplated parts.
7. Deformation control of electroplated parts
The temperature of several steps are all within 60℃~70℃ during the electroplated process. Under this working condition, the hung parts are easily to deform. So how to control the deformation is another question that we should know. After communicating with the engineers in electroplated factories, we know that the key is to fully consider the design of coupling mode and supporting structure in the structure of parts, which can improve the strength of whole structure. Generally, various structures are designed on the injection runner structure, which not only ensures the filling of plastic flow but also strengthens the overall structure. In electroplating, electroplating is carried out together. After electroplating, the runner is cut off to get the final product.
8. Realization of local electroplating requirements
We often asked for different effects at different areas on the parts surface. It is the same for electroplated parts, we often use the following three to achieve it.
(1) If parts can be divided, it is recommended to make different parts and finally assemble them into one part. If the shape is not complex and the components are in batches, producing a small set of molds for injection will have a significant advantage in price.
(2) If electroplating is not required for parts that do not affect the appearance, it can usually be processed by electroplating after adding insulating ink. By doing so, there will be no metal coating at the area that has sprayed the insulating ink. To meet up the requirement, this is the only one part of it. As the electroplated part will become brittle and hard, so on the parts, such as keys, its crank arm is the part that we do not want to be plated because we want them to be elastic. Now, local electroplating is necessary. Meanwhile, it is also applied into the lightweight products, such as PDA. Normally, the circuit board is directly fixed on the plastic shell. Generally, the parts in contact with the circuit are insulated to avoid affecting the circuit board. The method of printing ink is used for local treatment before electroplating. During the electroplating, in the case of the above figure, it is impossible to achieve the effect shown in the figure should be obtained (blue purple indicates the electroplating part) because the electroplated area should form a connected circuit so a solid electroplated coating can be generated. In the figure, each electroplating surface is divided into many parts, which cannot achieve uniform electroplating effect.
The parts above can be made in the way that is shown in the figure above. Only by doing so, a good circuit can be formed that allows the current react well with the electric ions in the liquid, achieving great electroplating effect.
9. Another method is similar to the double injection. Normally, we can divide it into ABS, and PC to carry out the injection if there is double injection machine. Start electroplating after plastic parts are made. Under this condition, due to the different adhering force of two types of plastic to the plating solution, it will cause ABS has electroplating effect while PC has no electroplating effect. Another way to get a good effect is by dividing the parts into two phases. First, one part will be electroplated after injection, and the processed products will be put into another set of molds for secondary injection to obtain the final sample.
10. Requirements of mixed electroplating effect on design
To obtain special designing effect, we often adopt high gloss electroplating and etching electroplating together on one product when designing. Usually, small etches are recommended for better effect. However, in order to not make the effect of etching is covered by electroplating, only two layers of electroplating will be carried out, so the nickel of the second electroplating layer will be easier to be oxidized and discolored, which affecting the design effect.
11. Effect of electroplating effect on design
Here, it mainly refers to if if is colored electroplating effect, the color difference table should be submitted as the color canon be uniform and same after electroplating. Different parts will have a big difference, so the acceptable color difference values need to be provided.
12. Make sure practicing under safety distance and following the safety instructions as the electroplated parts are conductive.
MORE BOLG
Insert mold in injection mold service
What are advantages and disadvantages of Zinc alloy and Aluminum alloy?
Inspection standards for injection molded partappearance
How to judge the quality of your plastic products?
Inspection standards for CNC machining
To ensure that your products are 100% qualified
Categories
Try GREFEE now,for free
We keep your uploaded files confidential and secure.