Working principles of CNC precise machining parts

Posted on : April 12 , 2022 By GREFEE
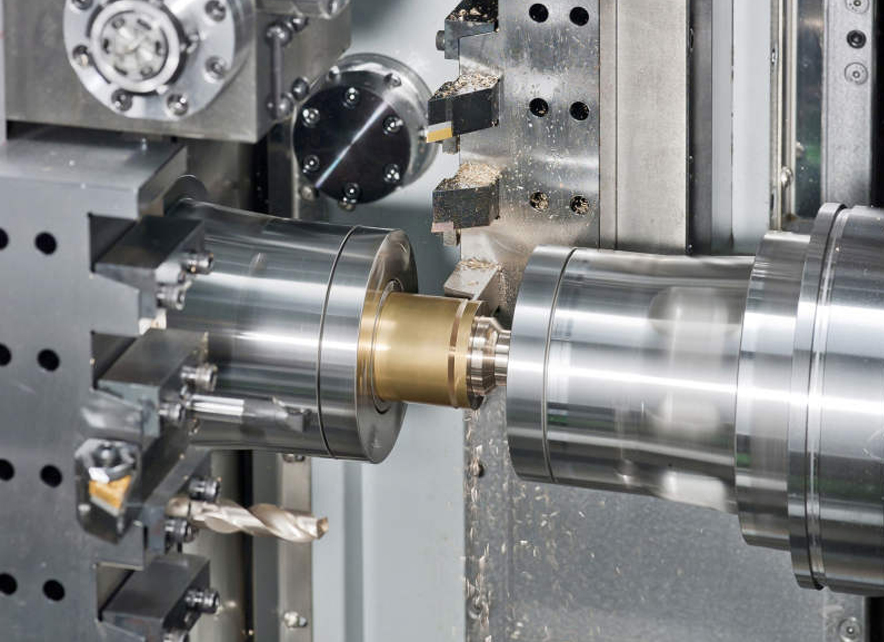
Control system for CNC precise machining parts
Generally, the machine tool works by following the orders which are programmed by numbers to make it automatically start and stop, turn and change speed.
It can automatically change the feeding speed, direction, and machining route.
Can select tools and can adjust the engagement according to the size of the tools and can complete all auxiliary actions that are needed in work.CONTACT US
The structural CNC lathe of CNC precision machined parts contains a principal axis box, tool carrier, feeding transmission system, lathe, hydraulic system, cooling system, lubricating system, etc. However, the feeding system for the numerical controlling lathe and the horizontal lathe are fundamentally different.
Summaries of the advantages of CNC machining
So far, the manufacturing of many parts relies on CNC machining. The reason why for this is that CNC machining owns many advantages, such as convenient operation and fine machining effect.
So, that is why CNC precision machined parts is so remarkable.
Four advantages of CNC machining:
1. Uses industrial plastic which is cheap and has a wide selection range.
2. Reliable machine properties with simple operations
3. Breakdowns the parts appropriately
4. Suits components with simple structure and large size
How to choose right equipments for CNC precision machined parts?
The choice you made matters significantly and brings better products without quality issues and accidents during operation. So, in this article, GREFEE will show you how to select the correct machines for CNC machining?
1. Selects the devices of CNC machining properly
2. The rough machining is by cutting a big part of machining allowance without high requirements for machining accuracy, so it should be processed in the lathes with high power, not too high accuracy. The procedures of fine machining do require working in the lathe with high accuracy.
3. To assure the machining accuracy, it is better to separate the rough and fine machining.
4. There is heat treatment process involved in the CNC machining routes.
5. The organization of the heat treatment process: to improve the machinability property of metal, such as annealing, normalizing, conditioning, are before the mechanical procedures.
Sequence of precision machined parts
For the machining industry, the sequence is critical because it is related to quality. One procedure mis-arranged will lead to a great loss. If it worsens, then the products are scrapped. So, the precision-machined part is one of them, so what is its sequence? CONTACT US
1. The arrangement of the processing sequence is according to the condition of the structure, blank, and fixture. The key is to protect the rigidity of the parts.
(1) The processing of each procedure should not affect the location and fixture of the next. With processes of universal precise machined parts involved should also consider comprehensively.
(2) Processes the interior and internal cavity and then processes the exterior
(3) The processes which have one location and the same fixture methods or procedures which use the same tool had better be processed before and after to reduce the times of locating, tool replacement, and pressing plate movements.
(4) For the situation of including many procedures within one installation, should start with the step which has minimal affection for the rigidity of parts.
2. Centralized sequential method is to arrange the procedures according to the tools used. Finish the locations which one tool can and then replace the second and third tools till the remaining areas have been done.
Doing so can reduce the times of tools replacement and unnecessary location tolerance.
3. Machining areas sequential method: parts with complex machining procedures can be divided into several parts according to the structural features, such as interior, exterior, hook surface, flat surface, etc.
a. Generally, it starts from the flat surface to the location surface then to machining holes.
b. For the machining procedures, the simple geometrical shapes are before the complex geometrical shapes.
c. The locations with lower machining accuracy are before the ones with higher machining accuracy.
Above are the procedures of the precision machined parts. It will effectively reduce the risks if following the steps.
The extend of the precise hard metal mold knowledge
1. Common brands of mold accessories
DME、DME-EOC、RAYMOND、HASCO、CUMSA、SPEC、ASSOCIATEDSPRING、STRACK、RABOURDIN、PCS、MISUMI、PUNCH、PROGRESSIVE、DANLY、LEMPCO、SUPERIOR、TOHATSU、FIBRO、FUTABA、AGAGHON、STAUBLI、NITTO KOHKI
2. Common material for mold accessories
a. The material used for mold accessories is tungsten steel, high-speed steel, bearing steel, stainless steel, brass, metal alloy, spring steel, carbonized steel, etc.
b. The plastic mold accessories mainly include single section ejector pin, double-section ejector pin, flat pin, guide pin, plastic guide bushing, straight bushing, middle column bushing, Square auxiliary device, stereo positioning blocks guide auxiliary device, A, B, C type sprue bushing, fixing ring A, B type, standard mechanical switch, small nozzle standardized sprue bushing, big nozzle standardized sprue bushing, mold date indicating device, resin switch, stopcock, finished tip for plastic mold, Pen Center, pen tube, small pull rod type C, bracing pin, material pulling pin, plastic mold guide pin, pull bar and return pin.CONTACT US
3. Hardware ramming mold accessories
H-type straight body punch, A-type secondary punch, edge forming punch, K-type budding punch, B-type guide punch, A-type sub female punch, former block, force plug, bushing, high-speed steel round bar, ultra-fine particle tungsten steel round bar, powder high-speed steel round bar, floating pin, lifter guide pin, stop screw, dowel pin, spool, guide pin, guide bushing, high-precision chromium plated guide pin, high-precision copper-titanium alloy guide pin, self-lubricating guide bushing, inner guide post assembly, sliding guide pin assembly for die base, ball guide pillar assembly for die base, detachable ball guide pillar assembly, outer guide pillar assembly, steel ball sleeve (cage), independent guide pin, hex-head screw, he* socket head shoulder screw, etc.
4. Basic requirements of mold accessories
a. Wear resistance
- When the blank plasticity denaturalizes in the mold cavity, it will flow and slip along the surface of the mold cavity to make an intense fraction between the mold cavity and blank and then lead to the mold-breaking due to the fractions.
- So, the material is one of the fundamental properties of wear resistance.
- Hardness is the main factor which affects the wear resistance.
- Generally, the higher the hardness, the less the frictio
- Besides, wear resistance is also related to the types, numbers, shapes, sizes, and distribution of the carbide in the material.
b. Fatigue fracture property
- When the mold is in the working process, it might be fatigue fractured due to the long-term effect of the cyclic stress.
- It has types of low energy multiple impact fatigue fracture, tensile fatigue fracture, contact fatigue fracture, and bending fatigue fracture.
- The fatigue fracture property of molds is mainly depends on the hardness, rightly, strength, and impurities content in the material.
c. Rigidity
- The working conditions for mold are awful, so the parts that often bear heavy impact will be fractured. To avoid fatigue fracture from happening, the mold must be of high strength and rigidity.
- The rigidity mainly depends on the carton content, grin size, and microstructure.
d. High temperature property
- When the temperature is high, the hardness and strength of molds will decrease, which will lead to wear in the early stage or generate plasticity denaturalized. Thus, the mold material should have high tempering resistance to promise the mold’s hardness and rigidity at high temperatures.
e. Cold and hot fatigue resistance
- Some molds are in the circumstance with repeated heating and cooling so that the mold cavity surface appears surface crazing and peeling due to the pulling force or the pressure turning stress. So, the mold is broken by increasing the friction in-between, interfere-ring with the plasticity denaturalization, and decreasing the dimension accuracy.
f. Corrosion resistance
- When some molds work inside the plastic molds, it will exhaust highly corrosive gas, like HCI and HF. These gases penetrate the mold cavity surface and increase the roughness and wear.
5. Mold inspection technology
- The measuring requirements are getting higher and higher for the development of precise molds.
- Precise CMM is used rarely on-site due to environmental limitations.
New CMM has temperature compensation and uses anti-seismic material to improve the dust, environment adaptability, and reliability to assure safe operations in the workshop to achieve the on-site measurement.
MORE BOLG
Categories
Try GREFEE now,for free
We keep your uploaded files confidential and secure.