Application of 3D printing – conformal waterway technology in hot runners

Posted on : April 9, 2022 By GREFEE
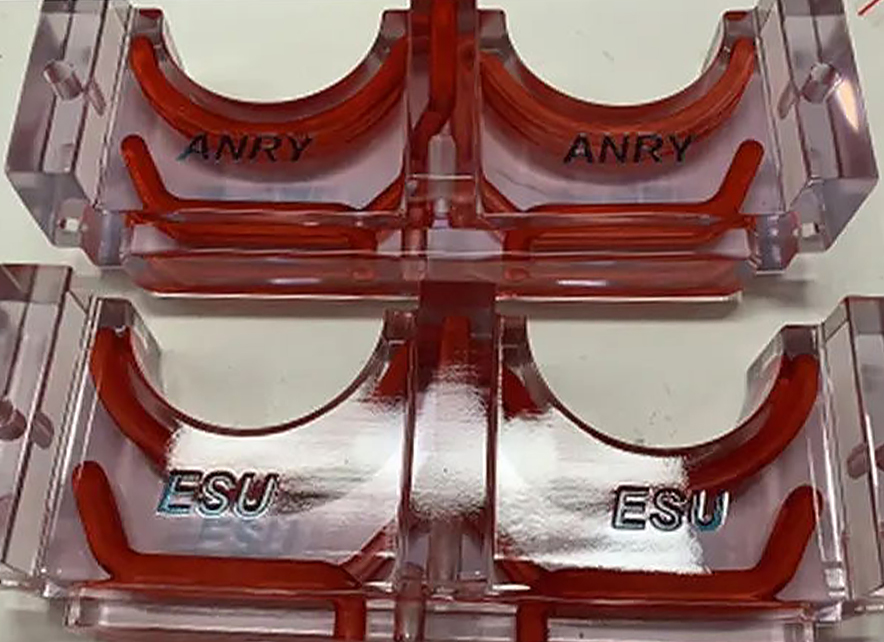
Application of 3D printing – conformal waterway technology in hot runners.
It is well-known that mold is fundamental to the manufacturing industry. The improvement of mold technology can effectively enhance the core competitiveness of enterprises and the nation’s critical businesses. To better meet the needs of consumers, the enterprises have been re-invented themselves and strictly controlled the quality.
As the products update rapidly, production efficiency and quality are crucial. This trend leads to higher requirements for the mold. So far, the mold industry has come to its technological bottleneck in the deformation, injection mold cycle, and other aspects.
The existing technologies still can not meet the product development needs, so it ultimately changes the intentions of designs to achieve the goals, which lead to a long development cycle of new products and also fail to make the appearance and structure adapt to market needs.
Metal 3D printing – conformal waterway technology is the Industrial application of 3D printing technology in the mold field. It can solve many quality issues by reducing 40% cycle time by reducing uneven cooling, scald caused by too high mold temperature, defamation, etc.
The basic principles of metal 3D printing technology.
3D printing, also known as additive manufacturing (AM), is a new molding method works by digital driven and consistent material accumulating. currently, the three main types of manufacturing method are subtractive manufacturing, equivalent manufacturing, and additive manufacturing.
The subtractive manufacturing is the process of material consistently reducing. The part forming process is to consistently cutting the material of blank, such as turning, milling, planing, grinding and drilling. This leads to material wasted.
The amount of material remains unchanged before and after in equivalent manufacturing, such as casting, forging, welding, etc. Additive manufacturing starts from scratch. It is an additive process, typically layer by layer, so the material usage rate is almost 100%, which is a newly environmentally friendly manufacturing technology.
The principle of 3D printing is from discrete, stacked to formed: first is to discrete the part to be manufactured and then cut the 3D Stereoscopic data into 2D plane data. After that, discrete the 2D plane data into a load of linear data. The material will be extruded, sintered, or melted from linear solid material into plane concrete material, then formed into a 3D concrete object. The whole manufacturing process is driven digitally. Thus, the 3D model decides the shapes and structures of the final products.
The basic procedure of 3D printing is to create the 3D model and cut it layer by layer. The slice data will be input into the 3D printer to print layer by layer till obtaining an actual product consistent with the 3D model. Currently, 3D printing materials utilized include metal, nylon, resin, ceramic, etc. It has been widely used in different fields, such as mold, medical, automotive, aerospace, war industry, etc.
3D printing technology is the revolution of mold cooling system
The metal 3D printing technology can make conformal waterways that cannot obtain from conventional mold manufacturing methods. This technology can manage multiple issues, like the cooling time saving for injection molding, minimizes the deformation volume, reducing the scald due to poor cooling efficiency, and other defects like black blobs and yellow blobs. It increases the production capacity and quality to a great extent, which is of significant strategy sense for long-term development.
(1) Factors that affect the product cycle are a long pressure holding time, mold locking, cooling, mold opening, etc. Among these factors, the cooling time accounts for 60%-70% whole product injection molding cycle, which is the longest. Thus, the cooling time shrinkage is an effective method for shortening the injection molding cycle.
(2) factors that lead to product deformation are numerous. The uneven cooling is the primary factor because the shrinkage rate of other areas is inconsistent as poor cooling. The changeable cooling velocities in the cavity and core will cause different shrinkage rates, warpage, depression, and other defects which affect the appearance and assembly line.
(3) factors that lead to scald, black blobs, yellow blobs, and other defects are the poor cooling effect which causes the temperature exceeds the temperature tolerance of the material.
Conformal waterway:
From the above analysis, we can know that a sound cooling effect promises a shorter injection molding cycle and fine product quality. It mainly relies on the cooling circuit. Thus, the waterway modification is the core. Conventional waterways can only do liner types.
However, as there is a long and unequal distance between the mold and product, it is hard to achieve the ideal cooling effect. 3D printing conformal waterways can print waterways in any shape, structure, and sectional shape. It can obtain the optimal cooling effect and achieve the narrowest gap between mold water circuit and product plus uniform distribution.
GREFEE has made the 3D metal printing conformal waterway inserts into the large-scale application. Since 2016, we have tried to use it to print mold parts to obtain a complex internal conformal waterway that conventional methods cannot. This technology increased the cooling uniformity and efficiency of high-precision mold. Nowadays, more customers asked us to involve 3D metal printing conformal waterway technology in high-precision mold manufacturing to save the material and improve the quality.Try GREFEE
A case of the combination of 3D printing technology and hot runners
Hot runners are a sound method to shorten the injection molding cycle and save material. After each injection, the material will not solidify in the hot runners due to the heating system, so it does not need to be off the runner nozzle for mold release. The injection runner is still open since the next injection cycle.
To protect the cooling function of the pouring system, the cooling time only depends on the cooling of the product. Therefore the injection molding cycle is shortened. 3D printing technology can significantly reduce the cooling time, so it can further shorten the injection molding cycle if combined with hot runner technology.
3D printing conformal technology distributes cooling water around the product surface. Besides, it can further minimize the production cycle to increase production efficiency. Figure 3 shows the design comparison between 3D printing conformal waterway and traditional. The waterways in conventional mold (a) cannot adhere to the around places of product.
Moreover, the internal range of this inverted buckle structure is narrow so that the waterways cannot distribute. The waterways in 3D printing conformal waterways can be designed into a spiral shape, which can be placed in a narrow space and fit the peripheries of products to achieve a uniform and rapid cooling. It can be seen intuitively that the design of 3D printing conformal waterways is more rational.
Comparison between the waterway designs
3D printing conformal waterway shortens the forming cycle. Pic 4 shows the comparison of forming-cycle: the time that the part needs to eject is 58s for conventional waterway molds. However, the time for 3D printing conformal waterway decreases to 28s. 5s needs to open the mold. The forming-cycle drops by 48%, from 63s to 35s, which indicates the cooling efficiency of the latter has improved significantly.
Comparison of ejection time
Another advantage of 3D printing conformal waterway printing is that it significantly decreases the highest temperature of mold and product. Meanwhile, it makes sure that the temperature of different areas is uniform. Pic 5 shows the difference in mold temperature between the conventional mold and 3D printing conformal waterway technology.Try GREFEE
We can learn that the temperature difference of the core insert of the traditional mold is 38 degrees, whereas the temperature difference for 3D printing conformal waterway mold decreased by 37 degrees, which is merely 1 degree. Pic 6 is the comparison of products temperature.
It shows that the temperature difference is 47 degrees for the core insert of conventional mold, while the number for that of 3D printing conformal waterway mold at the same position is 13 degrees, with a decrease by 34 degrees. It concludes that 3D printing conformal waterway technology is of fine cooling uniformness compared to the temperatures of mold and products.
Mold comparison:
Product temperature comparison
The uniform cooling effect significantly reduces the shear heat effect so that the production rate increases without deformation issues. However, the transparent cover of cosmetic products made from conventional mold can only assure the quality of one mold four-cav. Try GREFEE
If the cavity numbers increase, it might lead to poor cooling or even cause product deformation. The same thing won’t happen in 3D printing conformal waterway technology. It allows the cavity numbers to increase from 4 to 16 plus a 48% reduction of the injection molding cycle so that the overall production capacity can increase by about five times. Pic 7 (a) is one mold 16 cav., (b) is the product.
Case of one mold, sixteen cav.
3D metal printing is an additive manufacturing technology for a digital-driven of environmentally friendly. It has great practical significance in the mold field and technology. The application examples of 3D printing technology in hot runner molds demonstrate that 3D printing technology makes mold inserts with conformal waterways with the uniform and rapid cooling effect, which shortens the forming cycle by about 48%.
This technology has numerous advantages, like minimizing the risks of deformation of parts, enhancing the quality of parts, and increasing the production rate by more cavity numbers.If you need services for high-precision mold and injection molding products, contact us right now for customized and professional programs。
Try GREFEE now,for free
We keep your uploaded files confidential and secure.