Things you need to consider about overmolding design

Posted on : May 13, 2022 By GREFEE
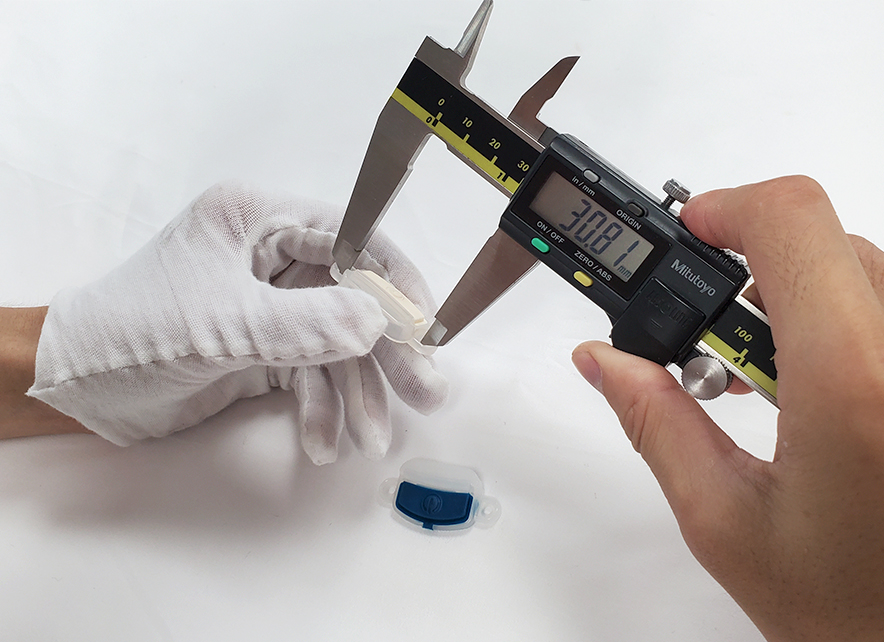
Overmolding is an injection molding process that allows the available molding parts to have an additional layer of resin to provide a property combination that can not be obtained through a single material. One of the common applications is to add a layer of soft, functional, and skin rubber-like material, TPE (thermoplastic elasticity). Another one is to alter or strengthen surface property through materials in different colors or surface treatment materials of overloading. Overmolding material can be found in any items, from medical equipment and manual tools to a toothbrush, the washer of the components, and the seals. GREFEE owns many years of experience in this. You can contact our engineer directly to get more details.
As a manufacturing technique, overmolding provides great adhesive force between different materials without manual assembling. Since it can achieve automation to different extents, its cost-effectiveness is significant. By simplifying the assembling process, the cost decreases, which helps with the speed of bringing the products and equipment to the market. While the most important thing is that it can significantly increase the available material property range for the products developer.
Overmolding has two primary methods, overmolding, overmold injection molding, and Pick-n-place molding. The former relies on a single production mold, and the latter relies on double molds.
Material selection of overmolding can be intricate. Substrate and the overmold resin are complementary to each other but have to be effective and compatible. The material selection depends on the application of overmolding components and the methods of producing overmolding parts. However, the process and outcome of the two-stage molding are more intricate than single injection molding. Thus, when selecting materials, we can seek advice from resin professionals
Two-shot & pick-n-place overmolding
Let’s first look at the overmolding-injection molding. It uses one base material for molding and then covers the base material with another type of material quickly, which is a high-level automation process. The second is the “pick-n-place” molding in which the whole batch of substrate parts is formed, then places the substrate part manually into a second mold and injects the overmolding resin into this mold to obtain a complete part.
Three primary methods of overmolding
Transfer overmolding is a robotic procedure in which the substrate is taken out mechanically from one mold and put into another bigger one. The overmolding material is injected to fill the empty space of the second mold during the next substrate being made in the first mold.
Rotational overmolding is another robotic procedure in which the mold is transferred from one injection station to another injection station to allow the injection of substrate material and overmolding materials.
Core-back overmolding only can be adopted for specific linear geometrical shapes. Mold is composed of a sliding section that is pulled back after finishing the injection of the first material and set to make room for the second injection material.
All these three types overmolding layer the overmolding material on the warm substrate, which is helpful with chemical adhesion. All three products will need specific equipment and expensive molds. Due to high-level automation, they have great cost-effectiveness in mass production, over 10000 pcs usually.
Pick-n-place molding uses two independent molds. One batch of substrate components is produced and cooled in one mold. Then, places it manually into a second larger mold. This mold can contain the substrate components and make room for the overmolding for injecting the overmolding material onto the substrate plate. Compared to the second injection, this technique does not need complex equipment. It can be operated with simple molds and simplifies and accelerates the installation procedure.
Overmolding methods comparison
Although the speed of manually placing the substrate plate into the second mold is slower than robots, it can finish the small volume production at a lower cost quickly and effectively. The difficulty of the Pick-n-place molding is the reduction of chemical adhesive between the overmolding material and the substrate plate. To raise the adhesive force to the highest degree, one must process the substrate material to prevent the adhesive force from being affected due to surface pollution. Besides, appropriate material selection is also helpful to make sure a good bonding.
Bonding
The bonding between resin layers facilitates the prevention of the layers being separated. According to various geometrical images, the bond site might be affected by the action of multi-force that will separate the bonding layers.
Measures including:
1. Straight pulling force leads to the butt joints separated.
2.shears due to the pulling force which is parallel with the adhesion interface will lead to the separation at the junction point.
3. Peeling that starts from the edges and penetrates from the interfaces between the materials.
When one of the materials is an elastomer, the bond strength is essential. The elastomer can be bent, too. This is not only suitable for thermoplastic elastomer (soften when heating) but also is suitable for thermosetting materials (do not soften).
There are two primary layer bonding methods. One is the actual chemical bonding of the two resin layers interface; another is mechanical bonding, which depends on the physical geometry structure of the interface. Through the combination of the part design, material selection, mold design, and molding technique, acceptable bonding is achieved.
Chemical bonding compatibility
Overmold material
The substrate material and overmold material have thousands of possible combinations. Except for some common bond materials, it is better to consult the engineer if you got any specific requirements.
Besides the compatibility and adhesive force, many factors affect the selection of the overmolding resin. If it only aims to cushion, the thickness and the softness of the overmolding material are equally essential. No matter the material selection, thin layers lower than 0.40 inches (10mm) will feel hard. Due to this, many consumer goods will have ribs inside to increase their sensing thickness, reduce the number of overmolding materials, and enhance their flexibility at the same time. The actual softness of the materials has no direct relation to its stiffness or stiffness design. A better measuring method is the flexural modulus which measures the bending resistance of materials. Materials whose flexural modulus is low will feel softer. Although many types of resin suit for over-molding, some elastomers, like Versaflex, can be applied to overmolding applications specifically.
If the purpose of the overmolding is to raise the track adhesion, the friction coefficient of materials means the touch feeling. For example, the thermal elastomer (TPE) usually has high friction coefficient. Under the cushion, the hardometer is not reliable enough to test the track adhesion of materials. Since many resins, including thermal plastic and thermal setting plastic, all have a series of properties. Thus, when selecting appropriate resin grades for specific applications, we can seek advice from related experts.
Like over-molding, the insert molding injects the resin into another material, whereas another material is metal and the injection plastic material is steel plastic rather than the plastic substrate material. Metal electrical components or custom metal components are being inserted into the plastic in this way typically. Similarly, the threaded inserts can make plastic parts assemble the plastic parts more durably and firmly, such as the device shell. Insert molding is the alternative to inserting metal parts through heat staking or ultrasonic welding through which a molded plastic part is melted partially for the allowance of the insert of metal components. Compared with other methods, insert molding is more controllable, allowing for better sealing. The molded inserts also eliminate the need for a secondary insert installation, saving time and money.
As the inserts are metal, they must be put into the molds and sealed with plastic. Mass production can be done by robots. However, for low and medium-volume insert molds production, pick-n-place is a manual process. There is no chemical bond between the metal inserts and plastic. Thus, the inserts and resin parts must be designed into the mechanical bond.
Try GREFEE now,for free
We keep your uploaded files confidential and secure.