Energy Consumption Saving in the Heat Treatment in Die Casting Industry

Posted on : Apr 7, 2022 By GREFEE
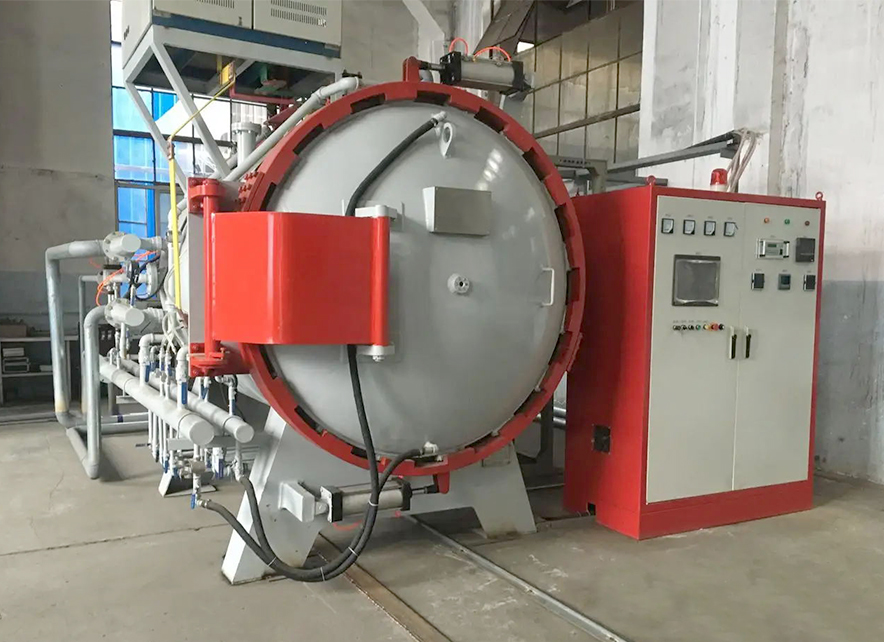
Energy Consumption Saving in the Heat Treatment in Die Casting Industry
Some new techniques are being widely used for manufacturing molds, such as EDM, forming grinding, linear cutting, etc. These technologies can effectively solve the deformation issue due to the heat treatment or the machining of complex mold. Heat treatment is generally the last step of mold machining. The mold accessories that are already heated will be hard to re-process. Thus, the heat treatment must be dealt with appropriately. Not only do we need to meet the needs for maintaining the microstructure and properties of the mold also need to avoid problems, like out of tolerance and deformation.
- The chemical composition and the original set-up of mold steel will be affected by heat treatment.
- For mold steel, the primary concerns are carbide segregation and the shape and distribution of carbides.
- The carbide segregation in high carbon and high alloy steel (like Cr12 steel) has a significant impact on the quenching deformation.
- The distribution of different carbides (granular or fibrous displayed) impacts matrix expansion and contraction from many aspects, too. Thus, it also affects the heat treatment deformation. In most cases, it is clear that it inflates following the direction of the carbide fiber cavity. However, the area perpendicular to the fiber direction shrinks but is not evident.
2. Mold deformation prevention
- The impact of the geometry of mold on heat treatment is through the action of thermal stress and structural stress. Due to the shapes of mold being diverse, it is hard to conclude an accurate deformation law so far.
- To minimize the occurrence of deformation, the heat treatment department should negotiate things related to design with the design department. Things like how to avoid the structure with too much section difference, the shape of mold shall be symmetrical as much as possible, piece parts together for complex molds, etc.
As a high energy-consuming machining process but an indispensable part of the die casting industry, the innovation of heat treatment technology is critical to saving energy. This principle should be in line with the development theory of GREFEE.
1. Decrease the temperature of heat treatment
- Generally, the temperature for quenching of hypereutectoid carbon steel is 30-50℃ above the AC3. The heating temperature of segregation and the hypereutectoid carbon steel is 30-50℃ above the AC1. Recent studies show that quenching the hypoeutectoid carbon steel in the α+γ two areas that are a bit lower than AC3 enhances the rigidity of steel and decreases the temperature of brittle transition to eliminate the quenching brittleness. The quenching temperature drops by 40℃.
- High-carbon steel quenching very quickly in a short time under a low temperature. This can reduce the austenite carbon content and helps obtain good lath martensite with greater fitting rigidity. It not only increases the rigidity but also shortens the heat time. For some transmission gears, replacing the carburization with carbonitriding enhances the wear resistance by 40-60% and fatigue strength by 50%~80%. The time for both processes is the same. The carbonitriding temperature is 70℃ lower than the carburizing temperature, which is 850℃ and 920℃. This property minimizes the deformation due to heat treatment in the meantime.
2. Heat time shortening
- The practice results indicate that the heating time depends on the valid thickness of the zinc alloy die casting parts are still can be improved. Thus, the heating coefficient α in the τ=α·K·D should be modified. According to the traditional coefficient, the value α is recommended at 1.0~1.8min/mm when the temperature in an air furnace is 800~900℃. Value α improves by decreasing the value of α to shorten the heating time. The heating time should depend on the experiments data, like the size of the parts and the furnace charging number. The optimized machining coefficient should be operated strictly for the promise of profit.
3. Omit tempering or reduce the tempering times
- Cancel the tempering process of carburizing steel, like the fatigue limit of 20Cr steel loader with double-sided carburized piston pin without tempering increases by 16% than the data of being tempered. Omitting the low carbon martensitic steel tempering process and simplifying the bulldozer axle sleeve into a quenched state of 20 steel (low carbon martensite) to stabilize the stiffness to be at around 45HRC. The strength and wear resistance are improved significantly, and the quality is stable, too. Reducing the tempering times of high-speed steel. Such as the W18Cr4V Steel Machine used a saw blade replaces the conventional three-time tempering (560℃×1h) with one-time tempering (560℃×1h) to make the service life increase by 40%.
4. high temperature tempering can be substituted by low or medium temperature tempering
- Medium carbon or medium carbon alloy structural steel replaces the low or medium temperature tempering with high-temperature tempering to get a more intense resistance force. W6Mo5Cr4V2 steel Φ8mm drill bit processes 350℃×1h+560℃×1h two times tempering after quenching. Compared to the 560℃×1h three-time tempering drill bit, the machining life increases by 40%.
5. Properly reducing the depth of nitrided layer
- The chemical heat treatment has a long cycle and high electricity consumption. It would be an effective method to shorten the cycle time and save energy by reducing the depth of the nitrided layer. Getting the necessary depth of the hardened layer through stress determination. The depth of the hardened layer now is high and should be 70% of the traditional depth of the hardened layer. Carbonitriding can reduce the layer depth by 30% ~ 40% compared with carburizing. If The depth in the production is controlled under the limits of the technical requirement can save 20% energy, shorten the cycle, and minimize the deformation.
6. Utilize the high temperature and vacuum chemical heat treatment
- High-temperature chemical treatment refers to increasing the carburizing speed effectively by the increased temperature of high-temperature chemical treatment if the temperature allows, and whether the austenite grain of steel grade enlarges or not. Raising the carburizing temperature from 930℃ to 1000℃ doubles the carburizing speed. Due to some other problems, future development is limited.
- The vacuum chemical heat treatment works in the negative pressure gaseous medium. The surface of the zinc alloy die casting parts in a vacuum state is clean. Under a high temperature, the penetrating rate improves significantly. Like vacuum carburizing enhances the production rate by 1-2 times; The penetration rate of aluminum and chromium can be ten times as before under the 133.3×(10-1~10-2)Pa.
7. Ion chemical heat treatment
- It is a type of chemical heat treatment that works in a gas phase medium lower than the atmospheric pressure with seeping elements. It utilizes the glow discharge generated between the workpiece (cathode) and anode. It then penetrates the seeping elements in the meantime. Ion nitriding, ion carburizing, ion sulfurizing, and other similar procedures have advantages of rapid penetration rates, good quality, energy-saving, etc.
8. Induction self tempering
- The induction self-tempering works by the heat penetrating to the outside of the quenching layer by the effect of the induction, so the short time tempering can be achieved by the residual heat in the quench cooling step. It replaces the furnace tempering due to its high efficiency and energy consumption. Moreover, in many cases, it eliminates the cracking caused by the quenching (like high carbon steel and high carbon high alloy steel). Meanwhile, it supports volume production with complete machining coefficients. It also brings huge economic benefits.
9. Pre-heated quenching after forging
- Pre-heated quenching after forging saves energy in the heat treatment, simplifies the production process, and improves the production property. Applying residual heat to quench after forging plus high-temperature tempering as the pre-treatment can eliminate the large grains and impact toughness after the quenching. The time of spheroidizing annealing is shorter than that of ordinary annealing, and its production rate is higher, too. Besides, the temperature of high-temperature quenching is lower than normalizing and annealing, so the energy consumption amount decreases. Moreover, the equipment is simple and easy to operate.
- Compared to the normalizing, the residual heat after forging enhances the stiffness of steel and plasticity. Decreases the cold brittle transition temperature and notch sensitivity, such as 20i steel achieve a better cooling effect after cooling in 730~630℃ by 20℃/h.
10. Replaces carburization quenching by the surface quenching
- The property for high carbon steel with 0.6%~0.8% carbon content after frequent quenching (like static strength, fatigue strength, multiple impact resistance, residual internal stress) from the system shows that replacing the carburizing quenching with induction quenching is feasible. We used 40Cr steel for high-frequency quenching to manufacture gearbox gears, which replaced the original carburized and quenched gears of 20i steel and achieved success.
11. Replace integral heating by local heating
- Some local components with technical requirements (like wear-resistant gear shaft diameter, roll diameter, etc) can utilize bath furnace heating, induction heating, pulse heating, and flame heating to replace the role of integral heating of the batch-type furnace to achieve perfect matchable performance between the friction grip positions of each zinc alloy die casting parts, and extends the service life. As it is local heating, it can remarkably minimize the deformation due to quenching and decrease energy consumption.
Whether the energy resources solution helps maximize the profits in a die casting process with limited resources depends on many factors, like the efficiency of equipment, machining technical routes, management mode, etc. It needs to consider comprehensively in alignment with the cooperative philosophy and each section. Meanwhile, global views are necessary when planning technology. If you have a new project to initiate, Try GREFEE!
MORE BOLG
Categories
Try GREFEE now,for free
We keep your uploaded files confidential and secure.