High precision machining mold,GREFEE is always moving forward.

Posted on : April 7, 2022 By GREFEE
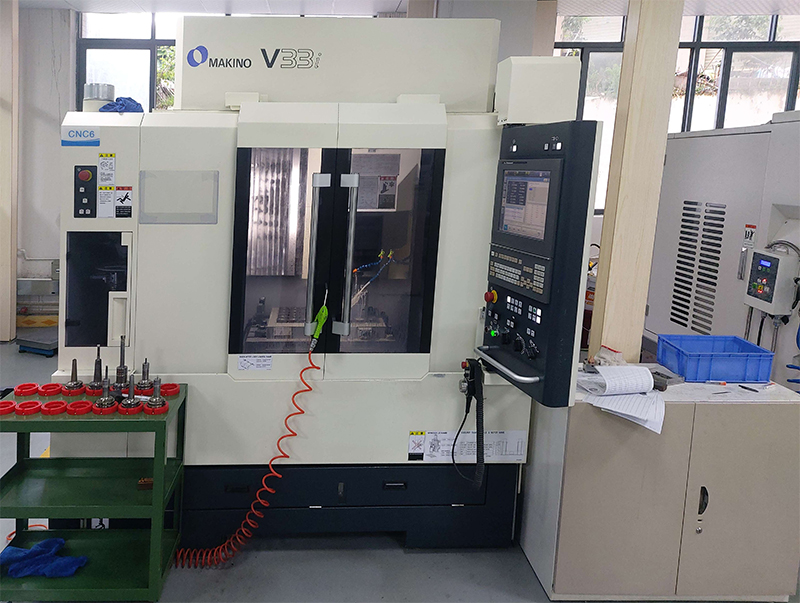
Molds play an indispensable role in many industries, like electronic consumers, automobiles, airplane making, etc. In recent years, mold technology has achieved remarkable progress. With more and more enterprises begin to purchase high-precision mold.
The mold technology development and quality are essential factors for domestic mold manufacturing development. Utilizing high-speed machining can efficiently improve the production rate, accuracy, and service life. Thus, it replaces the EDM finishing mold and has become the major trend, which has been accepted by domestic and international manufacturing enterprises. High speed machining has a short application time and higher requirements for technology.
High speed machining technology
High speed machining technology has properties of low temperature rises (only 3 degrees increasing in machining parts), small thermal deformation, and more advantages. The metal cut rate of the unit power raises by 30%-40%, the cutting force decreases by 30%, and the working durability increase by 70%.
As the cutting heat of zinc alloy die casting parts have minimized largely, the low order cutting vibration almost disappeared. With the cutting velocity increasing, the removal rate of banking per unit time increases, cutting time shrinkages, and the efficiency improves, which shortens the cycle time and increases the competitiveness in the market.
Meanwhile, the small cutting depth and high feed rate of high speed machining minimize the cutting force on the parts. It reduces the cutting heat by avoiding the chips at a high velocity, the same as the thermal deformation. Therefore, the rigidity of the zinc alloy die casting parts makes the thin wall parts machining available.
The high speed machining can replace electrical discharge machining (EDM) for the machining of material whose stiffness exceeds the HRC60. This shortens the cycle time effectively and saves 80% of the manual grinding time. Besides, it also cuts 30% cost, makes the surface roughness reaches Ra0.1 and the cutting efficiency doubles.
Advantage of high speed machining in the mold machining
The characteristics of mold machining are single pieces, small volumes, and complex geometry. Therefore, the cycle time is long, and production rates are low. In the conventional mold machining processes, the fine machining hardened mold usually uses EDM and Manual polishing technology. The main target for mold technology development is to shorten the cycle time and decrease the production cost. Recently, mold machining has been innovated, such as high speed machining, CAD / CAE design simulation, rapid prototyping, EDM milling, compound machining, etc. The most remarkable one is the high speed machining with the optimal effect.
High speed machining mold utilizes the high speed rotating and high feed rate of lathes to complete the multiple production procedures. The high speed machining mold has several advantages, which are:
① high speed machining rough machining and semi-fine finishing, which largely increase the metal cutting rates.
②uses the high speed cutting machining lathes, tools, and technology to work with hardened material. For small-scale die-casting molds, after heat treatment, the rough and fine machining can be completed in one clamping. For large-scale die casting mold, starts the rough machining and semi-fine finishing before the heat treatment, then starts the fine machining after the heat treatment.
③ high speed & high accuracy machining replaces the finishing increases the efficiency of manual grinding, which is 50% more efficient than EDM.
④the final forming surface after the hard machining, increase the surface quality and surface accuracy ( low surface roughness, high surface brightness), which suits molds with complex curved surfaces.
⑤avoid the decarburization, burns, and microcracks caused by the electro spark and machining, which effectively reduces the surface damages and extends the service life by 20%.
⑥ less thermal decomposition, cutting force, and thermal deformation. Combined CAD/CAM technology suits the rapid machining electrodes, especially electrodes with complex shapes, and thin walls, that are easy to deform.
High speed machining lathe for mold manufacturing
Things should notice for selecting the high speed lathe of high speed machining lathe:
(1) the power of the principal axis of the lathe should be large and high speed. It must meet the needs of both rough and fine machining. The fine machining mold uses tools that have small diameters, and the principal axis rotating velocity reaches over 15000~20000rmp. Lathes whose axis rotating speed is lower than 10000rpm can do rough and fine machining. Lathes have the principal axis with two rotating velocities or motorized spindles of two specifications that meet the needs of rough and fine machining.
(2) fast feeding has low requirements for noncutting stroke but needs high machining feed rates (30~60m/min)and high acceleration and deceleration.
(3) it has a robust control system with high speed and accuracy. Besides, it also has functions like high precision interpolation, contour forward-looking control, high acceleration, high-precision position control, and more.
(4) selects the CAD/CAM software which matches the high speed machining lathes, especially for the software for high speed machining mold.
The applicant of the five-axis lathe has been increasing in mold production. Cooperating with a high-speed cutting die has the following advantages:
① can change the machining angle of tools. Good cutting conditions can minimize the grinding influence to protect them and prolong their service life.
② flexible machining routes to reduce the interference of tools, which can manufacture the molds with complex geometries and deep cavities.
③big machining range, suits different types of mold machining(Five axis high speed linkage milling machining center)
Five-axis lathes have two types, worktable and milling head five-axis machine tools. The milling head five-axis machine tools can change the milling head and the electric spindle head for rough and fine machining.
Cutting tool technology for high speed machining mold
High speed machining needs proper tools. The application of hard metal-coated tools and the polycrystalline reinforced ceramic tool make a high stiffness blade and high rigidity base, which accelerates the development of high speed machining. The stiffness of the polycrystalline cubic boron nitride (PCBN) blades is 3500~4500HV and the stiffness of Polycrystalline diamond (PCD) is 6000~10000HV. The overseas famous tools company, like SCS of Germany, Mitsubishi (KOBELCO”) and Sumitomo of Japan, Sandvik of Switzerland, and Kenner Feishuo of the United States have developed their high-speed machining tools. These companies not only produce tools for machining the steel with ordinary structure but also ceramic tools for machining hardened steel. Especially the coated tools play an essential role in the rough and fine machining of hardened steel.
Generally, when the acceleration speed of the tools and cutter holder reaches over 3g, the radial runout is less than 0.015mm, and the length is 4 times less than the diameter of the tools. The high speed machining tools manufacturing experience shows that the ball nose cutter with a small diameter for fine machining, the linear velocity exceeds 400m/min.
This has high requirements for the material(stiffness, rigidity, red hardness), the shape of tools (chip removal performance, surface accuracy, dynamic balance, etc), and the service life. Hence, the utilization of high speed machining needs high speed lathes, suitable tools, and machining technology. In high speed machining, there are several aspect need to be aware of:
①selecting harden metal coated tools, CBN, and Diamond sintered layer tool. according to different machining items.
②uses small diameter type of ball nose cutter to do the fine machining. Usually, the fine machining tools’ diameter is <10mm. The diameter varies according to the machined material and stiffness. For the selection of material, the TiAIN ultra-fine grain hard metal-coated tools have a good lubricate function. When machining the mold steel, it has better wear resistance than the TiCN hard metal-coated tools.
③ selects proper tool parameters, like a negative rake, etc. high-speed machine tools should have better rigidity for anti-impact and anti-thermal impact.
④ uses multiple methods to extend the life of tools and save the cost, such as the appropriate feeding, feeding modes, lubricate modes, etc.
⑤uses high-speed hilt. Currently, the most used one is HSK hilt and hot pressing stamp tools. When using, it should be aware of the overall dynamic balance of the rear spindle system.
GREFEE has been updating and self-developing itself with cutting-edge technology. With more than 20 years of experience, we can quickly produce molds with high quality, long service life, and competitive price. Our products have been exported to many overseas countries and have been high affirmed by the customers. Try GREFEE now to initiate your project.
MORE BOLG
Categories
Try GREFEE now,for free
We keep your uploaded files confidential and secure.