Zinc alloy die casting mold machining

Posted on : April 7, 2022 By GREFEE
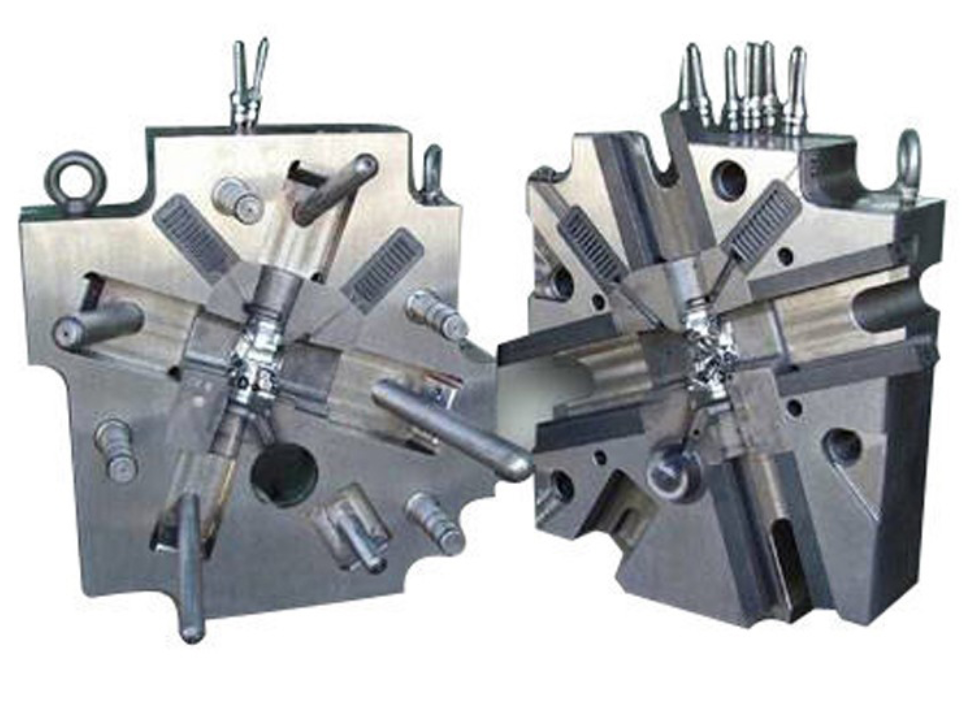
1. Zinc alloy die casting mold machining
Zinc alloy die casting mold making refers to the forming and blank making. It also includes shear mold and die-cutting mold. In most cases, the mold has an upper mold, and a lower mold with a steel plate is in between to realize the material formed by the press machine. When the machine opens, a part will be obtained as the shape of the mold or remove the residues. From electronic connectors to automotive panels all can be obtained by the molding process.
Progressive die wizard refers to parts moving automatically from one position to another to obtain a whole set of formed parts. The mold machining technologies include mold cutting, blanking mold, compound mold, extrusion mold, four-slide mold, progressive die wizard, stamping die, die-cutting mold, etc.
2. Types of mold
(1) metal stamping mold: progressive mold, single punch mold, compound mold, pull mold
(2) plastic forming mold: injection molding die, extrusion mold, blister mold
(3) die casting mold: zinc alloy die casting mold, aluminum alloy die casting mold, magnesium alloy die casting mold
(4) mold forging
(5) powder metallurgy molds
(6) rubber mold
3.Machining process of zinc alloy die casting mold
- Cutting: cavity,core,insert, slide,lifter
- Open the box: cavity frame,core frame
- Roughening: cavity roughening, core roughening, parting line roughening
- Cooper Electrode : cavity Cooper electrode, core Cooper electrode, parting line undercut Cooper electrode
- Linear cutting: insert parting lines, Cooper electrode, lifter shut-off
- Computer gong: fine gong parting line, fine gong core
- Electrospark: thick cavity, copper electrode, core line undercut, ribs of core, shut-off
- Drill holes, pin holes, ejector pin; ejector pin waterway holes machining slide
- lifter.
4. Others
(1) Sprue nozzles, clamping slot, stop pin
(2) Deck form
(3)Sprue, support pillar, spring, water line
(4)Lapping,polishing, ribs of cavity and core
(5) Pin-point structure, pull bar screw hook, spring
(6) Heat treatment, quenching, slide surface nitride for key parts
5. Softwares for making zinc alloy die casting mold
- UGNX、Pro/NC、CATIA、MasterCAM、SurfCAM、TopSolid CAM、SPACE-E、CAMWORKS、WorkNC、TEBIS、HyperMILL、Powermill、GibbsCAM、FEATURECAM
- UGNX、Pro/NC、CATIA、MasterCAM、SurfCAM、TopSolid CAM、SPACE-E、CAMWORKS、WorkNC、TEBIS、HyperMILL、Powermill、GibbsCAM、FEATURECAM, etc.
6. Basic features
(1) high machining accuracy requirements – a set of zinc alloy die casting mold is usually composed of the former block, force plug, and mold frame. Sometimes, some of them might be the die segments in multiple pieces. So it has high machining accuracy requirements for the combination of upper and lower mold, inserts and cavity, die segments. The accuracy of the size of precise molds is μm level.
(2) products have complex geometries, such as automotive panels, airplane components, toys, house appliances, which the surface of them is multi-curved surfaces combined. Thus, the cavity of the zinc-alloy die casting mold is sophisticated with some curved surfaces that must be processed by a mathematical calculation method.
(3) the volume production of small molds is not bulk order or large volume production. It is usually produced in only one piece.
(4) multiple procedures: steps included in the mold machining are milling, boring, drilling, reaming, tapping, and other processes.
(5) the work-life for mold in reproduction is limited. When the mold using period has exceeded its service life, we should replace it with a new mold, so the mold production is repeatable.
(6) contour machining usually does not include the design and data. It needs to work by copying the real product, so it has higher requirements for contour machining without deformation.
(7) the quality of mold material, molds with high stiffness are made of high-quality steel alloy, especially molds with a long service life using Crl2, CrWMn, and other ledeburite steels. This type of steel has rigorous requirements from bank forging to processing to heat treatment. Thus, the arrangement of the machining process is essential, as well as the heat treatment deformation.
Based on the characteristics above, it should select lathes that could meet all machining needs, such as advanced numerical control, high accuracy, good rigidity, stable heat endurance, contour mach
7. Arrangement of machining process
(1) Bottom side machining and promise machining volume
(2) Correctly positioning casting blank benchmark and allowance inspection of 2D, 3D surfaces
(3) Rough machining to 2D, 3D surfaces. Non-installment and non-working surface machining (security plane, mounting plane of buffer, pressing plate, profile datum plane)
(4) Before semi finishing, profile datum plane should be correctly marked with accuracy guaranteed.
(5) Semi finishing 2D, 3D surfaces and fine machining all types of working surfaces ( mounting surface of stopper and contact surface, the mounting surface of the insert, backside, punch mounting surface, the mounting surface of waste cutter, various stroke limiting surface, the mounting surface of wedge)
(6) Test the machining accuracy
(7) Fitter inlay process
(8) Before fine machining, the benchmark hole and surface should be marked correctly, and check the insert allowance.
(9) The fine machining 2D, 3D surface, side punching surface and hole positions, fine machining standards, altitude datum, fine machining guide surface, and guide holes.
(10) Test the machining accuracy
8. Dos and Don’ts
(1) Process planning should be concise, detailed, and numerical
(2) Key points and difficulties should be specified
(3) Areas need combined process should be clarified
(4) Inserts need separate machining ought to be careful of the machining requirements for accuracy.
(5) After combined machining, the inserts need to be machined separately, and the combined machining follows the separate machining standards.
(6)Spring is most likely to be damaged in the zinc alloy die casting mold machining process, so the spring should be with long fatigue life.
MORE BOLG
Categories
Try GREFEE now,for free
We keep your uploaded files confidential and secure.