Material selection of the injection molding automotive parts

Posted on : July 18 , 2022 By GREFEE
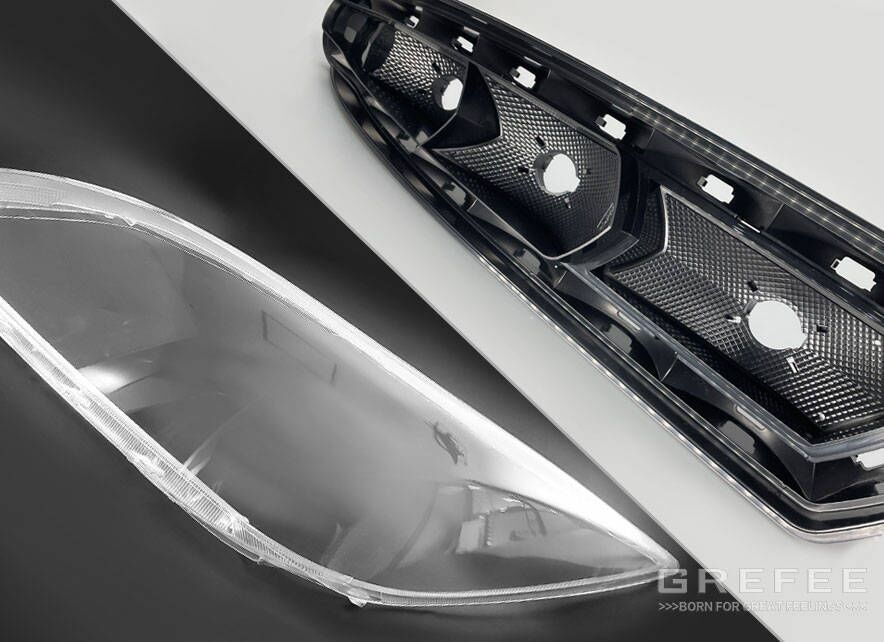
The raw material has a broad range, which is divided into the interior, exterior and functional parts in terms of the automotive plastic injection molding parts.
The plastic is classified into three types, general plastics, engineering plastics and special plastics according to the various properties.
General plastic
It generally refers to plastics with large production volume, good formability, low price and broad range of applications. General plastics include five categories, polypropylene (PP), polyethylene (PE), polyvinyl chloride (PVC), polystyrene (PS) and acrylonitrile butadiene styrene copolymer (ABS), all of which are thermoplastics.
1. PP
PP is the abbreviation of the polypropylene, which is similar to white wax. It is transparent, light weight, and has good flowability during injection molding. Besides, its water absorption rate is less than 0.02%. The shrinkage of PP is 1.0-3.5%, and the suitable thickness is 1.5-2.5mm.
Two common issues exist in the application of PP in the automotive field, flammable (include dripping combustibles) and being brittle under low temperature. In terms of these two issues, adding proper additives in the actual use to change its property, and the flame retardant will be added. It is brittle under low temperature, which is solved mainly by adding other rigid materials, rigid particles or elastic substance to increase the rigidity, such as rubber (EPDM), talc powder (TD), glass fiber (GF), etc. There are many automotive products made of PP resin, including various instrument panels, door guards, column guards, bumpers, water tanks, and decorative panels. The application of PP in automobiles is still increasing.
2.PE
Polyethylene, one of the lightest plastics, which is translucent and white waxy with good water resistance, acid and alkali resistance, organic solvent resistance, and excellent electrical insulation. Its shrinkage rate is 1.5 ~ 4.0%, and the thickness is 1.0-2.5mm. The biggest disadvantage of PE as an automotive material is that it is easy to burn. The simplest method is to add appropriate flame retardants to enhance its combustion performance. The automotive products made of PE mainly include fuel tank, air duct, front seat decorative cover, air duct assembly (HDPE), left and right vent pipe assembly, up and down wind blade connecting rod, left and right foot vent assembly, etc.
3.PVC
PVC, commonly used PVC, is a multi-component plastic. Due to the difference in content of each component, its particles has different hardness and mechanical properties, which are divided into soft PVC and hard PVC. Shrinkage: hard PVC is 1-1.5%, soft PVC is 2-2.3%, and the appropriate thickness is 2-3.5mm.
PVC is the most common used plastic raw material in the car plastic products without any doubts. Not only because its low price, but also the great processing performance and comprehensive mechanical properties , all make it become the first choice in making the car injection molded parts. The automotive made by PVC is common in out daily lives, such as the PVC dashboard skin, PVC plastic steering wheel, PVC plastic lining, PVC plastic automobile flooring material, etc.
4.PS
Polystyrene is a transparent glass material with good fluidity and no water absorption. Since PS is brittle, it is often grafted and copolymerized with other substances. For example, it is grafted and copolymerized with butadiene to form hips. The impact strength and surface hardness are greatly improved after adding rubber. The shrinkage rate is 0.4-0.7%, and the appropriate thickness is 2-3mm.
The applications of PS in the automotive mainly include the instrument shell, lampshade and lighting products. PS is also the material used to produce the packaging material, insulation and temperature maintaining material, and shells by the means of foaming. There is also graft copolymerization and modification with other materials, resulting in many fixed matching PS family alloy plastic varieties, such as SMA used in the manufacture of automobile dashboard framework.
5.ABS
Acrylonitrile butadiene styrene copolymer, commonly known as super unbreakable rubber, its body is white. The shrinkage is 0.4-0.7%, and the appropriate wall thickness is 1.8-3MM.
Due to the large varieties of ABS, good surface treatment, and low price, it is widely used in the filed of automotive. Since its poor weather resistance, the commercial used cars has been using materials like AES or ASA to enhance its performance of ABS, which is of high weather resistance. When the products need surface treatments (such as water transfer film, spraying), ABS can be adopted, whereas when it is not, ASA or ASE is the correct choice. The most typical automotive products are decorative bright strips, shift handle heads, interior pull handles, license plate trim panels, rear spoiler assemblies, rear-view mirror bodies, radiator grille bodies, handrails, etc.
Engineering plastics
Engineering plastics, anther commonly used material in automotive field, are known for their good comprehensive mechanical properties. In this paper, we will introduce the polyamide (PA), polymethacrylate (PMMA), Polyoxymethylene (POM), polyamide (PU), polycarbonate (PC).
1.PA
Polyamide, commonly known as nylon, with a large varieties in industrial use, like the PA6, PA66 and PA610. Due to the thermal expansion and water absorption, the dimensional stability of the workpiece is poor. Its shrinkage rate is 1 ~ 2%. The dimensional change of moisture absorption after molding should be paid attention to. The water absorption rate is 100%, and it can absorb 8% when the relative moisture absorption is saturated. The appropriate wall thickness is 2 ~ 3.5mm
PA is mainly used to manufacture hoses (brake hoses, fuel pipes), combustion oil filters, air filters, oil filters, water pump housings, water pump impellers, fans, brake fluid tanks, power steering fluid tanks, white leaf windows, headlight housings, and safety belts in the automotive field.
2. PMMA
Polymethacrylate, commonly known as plexiglass, is resistant to outdoor aging, which is known for its excellent light transmittance. Products: transparent structural parts with certain strength requirements.
PMMA is widely used in automobile lighting signs, door glasses and lamp glass covers due to its good light transmission performance.
3. POM
Polyoxymethylene, commonly known as plastic steel, with a shrinkage of 2-3.5% and its appropriate wall thickness is 1.5-2.5mm.
POM is used to manufacture car parts, like the instrument panel glove box accessories, various valves (drainage valve, air conditioner valve, etc.), various impellers (water pump impeller, heater impeller, oil pump wheel, etc.), various electrical switches and pinions on electrical instruments, various handles and door pins, etc
4.PC
Polycarbonate has excellent impact toughness and creep resistance, good heat resistance and cold resistance. Its shrinkage is 0.5-0.7%, and the appropriate wall thickness is 2-3.5mm. The shrinkage, mechanical strength and temperature resistance of PC can be improved by adding glass fiber. The long-term use under the condition of 100 ℃ can increase its rigidity , and its internal stress can be improved by annealing.
Introduction to the main composite PC-ABS:
Pc-abs is a blend material of PC and ABS, which is usually supplied in the shape of pellets after blending. Simply mixed and injected directly of the two materials will lead to poor effect, and delamination will occur. The advantages of PC are rigid and tough, whereas the disadvantages are stress cracking and high viscosity. While, ABS has good flowability but low surface hardness. In this way, the blended material PC-ABS keeps the advantages of both. Moreover, it has a high surface hardness, high rigidity and toughness, and high stress cracking resistance; Its mechanical properties are between them two.
PC is mainly used to manufacture lampshades, left and right wheel guards, instrument baffle body (PC + ABS), left and right wind frame covers, middle wind frame covers (PC + ABS), and rear bumper cushion.
5.PU
Polyurethane, according to the different products of polymerization reaction, it is divided into rigid polyurethane and soft polyurethane. Polyurethane foams are widely used in automotive interiors and vibration absorbing parts, such as coating materials, polyurethane rigid plastic plates, polyurethane elastomers, soft foam materials for seats, decorative parts, sofa leather, and roof accessories. The most widely used are various soft and hard polyurethane foam materials, including vibration isolation, sound insulation, noise reduction, thermal insulation. In terms of the automotive parts, PU can also be made into polyurethane coatings, adhesives, sealants, etc. PU representative products on the car include instrument panel, rearview mirror, bumper, seat cushion, headrest, steering wheel, instrument panel anti vibration pad, pillar trim, front roof lining, window frame frame, ceiling and side roof frame decoration, door lining, sunshade, rear roof frame decoration, etc.
Special plastics
Glass fiber reinforced plastic
Glass fiber reinforced plastic includes extent of glass fiber and other additives, in addition to the pure plastic material to increase its range of use. Generally, most of the glass fiber reinforced materials used to produce the structural parts of products, also can be said as structural engineering materials, such as PP, ABS, PA66, PA6, PC, POM
Advantages:
(1). The reinforced glass fiber has a higher thermal resistance than having the glass fiber as a content, especially the nylon.
(2). the shrinkage rate of reinforced plastic also decreases significantly due to the limited mutual movement of the polymer of plastics, but the rigidity is enhanced.
(3). the reinforced plastic will not crack due to the stress, but its impact resistance will increase largely.
(4). fiber glass is high strength material which can increase strength of plastic (The tensile strength, compressive strength and yielding strength have been improved a lot)
(5). after adding the glass fiber and other additives, the flammability of it decreases drastically. Most of the plastics are non-flammable.
Disadvantages:
(1). it is transparent before adding glass fiber and turns into in transparent after a long term.
(2). the rigidity of plastic decreases, but the brittleness increases.
(3). the molten viscosity of all of materials increases, but the flowability is poor. The injection pressure is larger than that priors to the add of glass fiber.
(4). the fluidity is poor. For normal injection molding, the injection temperature of all reinforced plastics should be increased by 10 ℃ -30 ℃ compared with that without glass fiber.
(5). the water absorption of reinforced plastic increases and the pure plastic will absorb water as well. Thus, it should be dried during the injection molding.
(6). during injection molding, the glass fiber can increase the surface roughness
(7). glass fiber has high strength, so it releases a large amount of gas under temperature, which can cause erosion and wear on the screw bar and injection mold. Thus, the surface treatment and surface strength treatment should be paid attention to when producing mold or injection molding machines made of this kind of plastic.
Shrinkage of commonly used glass fiber:
PP+ glass fiber:0.2-0.8% ABS+ glass fiber:0.1-0.2%
PA66+ glass fiber:0.5% PA6+ glass fiber:0.4%
PC+ glass fiber:0.1-0.3% POM+ glass fiber:0.9-1.2%
The representative material of glass fiber reinforcement, the application of glass fiber reinforced plastics / Composites in the automotive industry:
Body parts: including body shell, hood hardtop, sunroof, door, radiator grille, headlamp reflector, front and rear bumpers, and interior trim. Due to a substantial needs in the automotive market, this is the main direction for the application of FRP / composite materials in automobiles. In China or even the worldwide, the automotive injection molding parts It is mainly aimed at meeting the needs of streamlined body design and high-quality appearance. So far, there is great potential for development and application. The material of this part is mainly glass fiber reinforced thermosetting plastic. Typical molding processes include SMC / BMC, RTM and hand paste / spray.
Structure parts: Including front-end bracket, bumper frame, seat frame, floor, etc., which aims to improve the design freedom, versatility and integrity of parts. It mainly uses high-strength SMC, GMT, LFT, etc.
Function parts: the main characteristics include the high temperature resistance, oil resistance, and the automotive injection molded parts mainly include engine and the surrounding components. Such as: engine valve cover, intake manifold, oil pan, air filter cover, gear chamber cover, air guide cover, air inlet pipe guard plate, fan blade, fan air guide ring, heater cover plate, water tank components, water outlet housing, water pump turbine, engine sound insulation plate, etc. The main process materials are SMC / BMC, RTM, GMT and glass fiber reinforced nylon.
MORE BOLG
Categories
Latest blog
Try GREFEE now,for free
We keep your uploaded files confidential and secure.