Causes analysis and improvement methods of burrs in die casting products

Posted on : March 23, 2022 By GREFEE
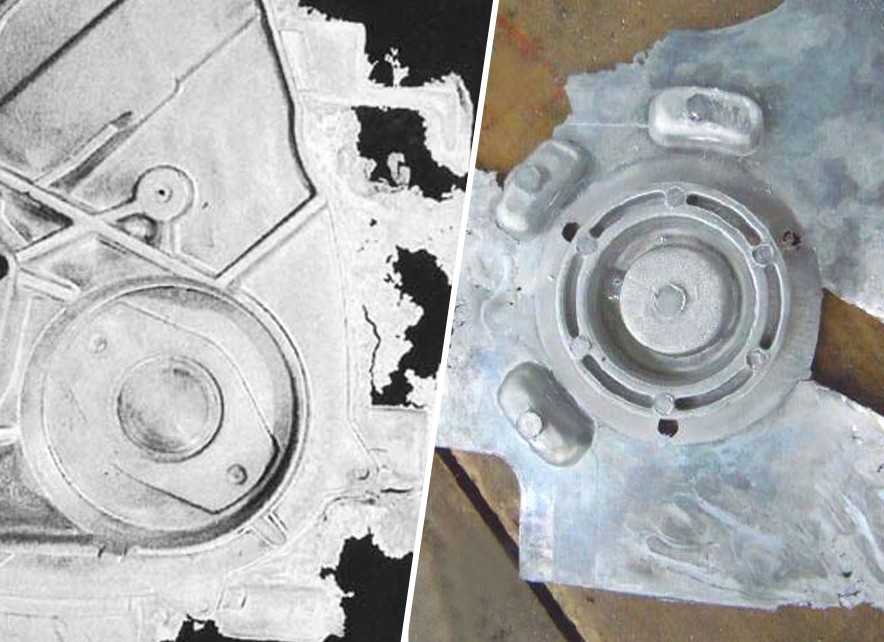
To learn more problems and preventions of die casting, click to check it out.
What is burrs of die casting parts?
Thin metal layers appeared above the casting edge or PL surface, thickness < 0.2MM.
Causes:
1. The clamping tonnage of machine is adjusted properly before ejecting.
2. Unqualified deck form, mold, and slides damage, blocking component is ineffective.
3.the insert block and slide of mold are wear.
4. The overall mold, especially the mold frame strength is not enough for elastic deformation.
5. The impurities on the parting surface is not cleaned completely.
6. Projected area calculations is incorrect, which exceeds the clamping tonnage.
7. Injection speed is too high, which forms high pressure shock peak.
How to improve the problem of burrs of die casting products?
1. Inspects clamping tonnage or pressure increasing state, adjusts the injection pressure increasing structure to lower the injection pressure increasing peak.
2. Inspects the damages of slide and repairs by coloring the mold to ensure the blocking component is effective.
3. Inspects the wear condition of mold and repair, or replace the insert blocks.
4. Calculating the mold strength properly. Uses the way of adding pillars at the rear of moving die frame to solve the problem.
5. Can measure by the straight state of the crank bar when clamping the mold. Cleans the impurities on the parting surface and continue producing after polishing.
6.To check the clamping tonnage is enough or not by calculation. If the interior quality requirements are not strict, we can use low-pressure high-speed machining parameters to solve it. If the requirements are high, we need to start a pressure test and use a die casting machine with a larger tonnage.
7. Check the set of parameter to see if it exceed the standard a lot. Lowering the injection speed properly.
Key inspection areas to burrs:
Mainly check the PL surface of products, kiss off holes and shut off holes position, ejector pin or moving core pulling structure position.
How does burr affect the quality of products?
It needs be aware of the related dimension of clamping surface, which indicates that these dimensions will change.
Another thing is the change of dimension will affect the post-treatment (thick burrs, machining chamfer, or size) and assembly. Moreover, burrs need to be dealt with a lot of labor force or die casting trimming mold, which increases the workload and costs.
How to make sure whether a die casting products with burrs is qualified or not?
Burrs usually can be measured by visual. The problem of burrs is unavoidable in die casting production. Generally, we will clean the parts after the process, or it will affect the appearance and dimension, so the products with burrs will be seen as unqualified. We must trim them completely.
Improves the problem of burrs of your die casting parts.
Generally, die casting products have burrs. A stable quality means that the burrs occur at the same position each time, which is what we need. We can use fixed die casting trimming tools to clean them out. If the burrs are not stable, we can use CNC machining to remove them.
GREFEE is a one-stop industrial company from mold machining, die casting production, die casting surface treatment to CNC machining of die casting parts, all we can do. Contact us for a competitive price and free product evaluation.
MORE BOLG
Insert mold in injection mold service
What are advantages and disadvantages of Zinc alloy and Aluminum alloy?
Inspection standards for injection molded partappearance
How to judge the quality of your plastic products?
Inspection standards for CNC machining
To ensure that your products are 100% qualified
Categories
Try GREFEE now,for free
We keep your uploaded files confidential and secure.