Causes analysis and improvement methods of mold sticking problems in die casting products

Posted on : March 23, 2022 By GREFEE
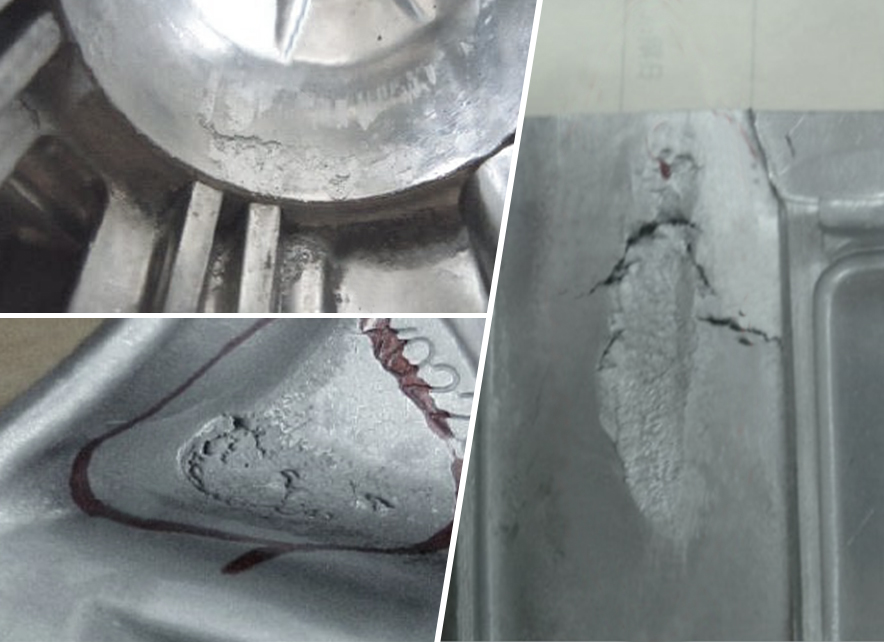
To learn more problems and preventions of die casting, click to check it out.
The sticking problem in the aluminum alloy die casting process has plagued die casting operators for a long time. Sticking will generate other casting defects, such as strains on the product surface, lack of material, internal porosity and shrinkage, surface dense layer damage caused leaking problems, etc.
Hence, the die casting operators should be prepared sufficiently on several aspects, such as die-casting mold design, mold surface treatment, maintenance, and control in the production process to reduce the possibilities of sticking problems maximumly.
When liquid metal and mold welding, it is easy to cause strains, so the material sticks on the surface or lacks material on some surface areas.
Causes:
1.The die casting mold cavity surface is damaged or has sinks after die casting mold machining.
2.The mold release angle is too small or the draft angle is reversed.
3.Products inclined in ejection.
4.Too high or too low pouring temp, too high mold temp lead to liquid aluminum sticking on the surface.
5.Poor effect of mold release agent and poor painting.
6.Iron content in aluminum alloys is lower than 0.6%.
7.Too long or too short cooling time.
How to improve sticking problems in die casting parts?
1.Fixes the damages on mold surface, adjust the angle, improves the finish by 0.4 with 600 fine oilstone down grinding the surface.
2. Adjusts or change ejector rod to balance the ejecting force or check whether the ejector plate of die casting mold is balanced or not
3. Changes or adds mold release agent with higher density, adjusts painting angle, especially the gate direct injection position.
4. Increases the iron content in aluminum alloy appropriately
5. Controls a proper pouring temp and mold temp.
6.the gate should avoid impacting the wall of die core directly or do specific treatment on the surface of die core.
7. Adjusts the parameters of the die casting process, reduces fast pressure flow volume and injection force. With the promise of ensuring good die casting, the lower the pressure and temperature, the better.
Key inspection areas to die casting parts
Generally, sticking is likely to appear on the areas of deep holes, sidewalls, corners of the products.
How does sticking affect the die casting products?
1.Affects the surface quality of product
2.Affects airtightness or water resistance of products.
3.Test Methods: visual, measure by eyes after deburring, painting .
How to evaluate whether the die casting parts with sticking problems or not?
Generally, by visual, but sometimes it needs to to after demurring or painting because measuring by eyes will be effective.
1. No drawing die allowed on the outer surface or surface that needs post-treatment.
2. No screw holes allowed inside the die casting machine as it will affect the shape of tooth after tapping.
3. The strains caused by sticking inside the sealing groover of die casting machine is not allowed as it will affect the smoothness of sealing groove to sealing effects.
4. Non-appearance surface and cavity depth ≤0.1mm,can try to grind the brush position to see if it works.
Improves the sticking problems
Sticking problems cause strains, which is a common issue in die casting. In addition to the draft angle, it results from the die casting parameters, unprofessional coating treatment, or the hardness of the die core is not enough.
A company like GREFEE owns 20 years of experience in the die-casting industry, is aware of avoiding the sticking problems during mold manufacturing, so a professional supplier is essential.
GREFEE not only has expertise but also a deep understanding of the products of your industry, such as automotive, 5G telecommunication, health care products, electronic kitchen appliances, LED lamps, LED outdoor displays, etc.
GREFEE will bring you high-quality die casting service with a professional team and outstanding work ethics. Contact us now!
MORE BOLG
Insert mold in injection mold service
What are advantages and disadvantages of Zinc alloy and Aluminum alloy?
Inspection standards for injection molded partappearance
How to judge the quality of your plastic products?
Inspection standards for CNC machining
To ensure that your products are 100% qualified
Categories
Try GREFEE now,for free
We keep your uploaded files confidential and secure.